
What is a make or buy analysis in project management?
1 Answer. In project management, make-or-buy analysis (often wrongfully called make-or-buy decision), is a process that companies follow in order to know whether it's better for them to do a project in-house or pay for a third party company to execute the project for them.
What is a make or buy decision?
Reviewed by Dheeraj Vaidya, CFA, FRM Make or Buy Decision Meaning A Make or Buy Decision is a decision made to either manufacture a product/ service in house or buy it from outside suppliers (outsourcing) based on cost-benefit analysis.
What factors should be considered in a make or buy analysis?
Your make or buy analysis should consider cost, time, quality, skill sets, necessary resources, and much more. Here are some factors that may help you decide if it’s better to make or buy. Cost Concerns: Does making the good or service in-house fit within your budget?
What is an example of make-or-buy analysis?
A rigorous make-or-buy analysis can also act as a source of competitive advantage. For example, a company can increase the value it delivers to customers and shareholders from its core service and skills. It can also stay flexible by adopting a make-or-buy decision approach.
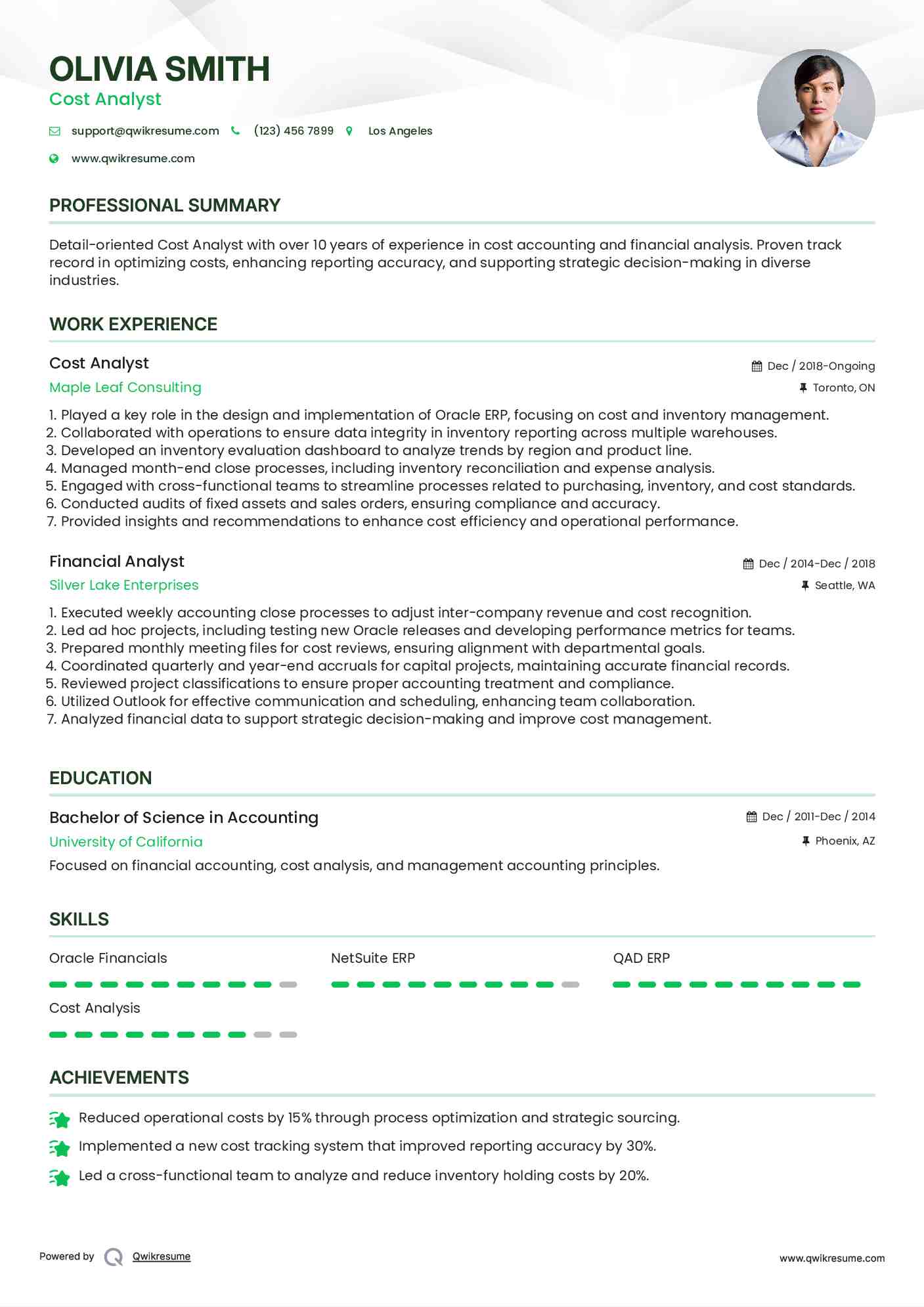
What is the importance of a make-or-buy analysis?
One of the most notable advantages that a company enjoys when embracing a make-or-buy decision approach is that it can lower costs and increase capital investments, regardless of whether it decides to make materials in-house or subcontract from an external vendor.
What is a make-or-buy strategy?
A make-or-buy decision is an act of choosing between manufacturing a product in-house or purchasing it from an external supplier. Make-or-buy decisions, like outsourcing decisions, speak to a comparison of the costs and advantages of producing in-house versus buying it elsewhere.
What is an example of a make-or-buy decision?
Examples of a Make-or-Buy Decision ABC Manufacturing Company is contracted to supply 6,000 units of its MVP. This would also require 6,000 units of a component essential for the MVP. The estimated cost of manufacturing these 6,000 units of the necessary component is roughly 234,000 USD.
What are the 4 primary factors to evaluate in make-or-buy decisions?
The following are the major factors considered while deciding to buy the good or service from the outside supplier.Lack of expertise.Research and specialized know-how of the supplier better than the buyer.Cost considerations (cheaper to buy the item)Insufficient or no manufacturing capacity at the buyer's end.More items...
What are the three pillars of the Make vs Buy decision?
This report explores the dynamics of make-or-buy decisions and presents a framework to help companies make the right decisions. The framework is built on three key pillars — business strategy, risks, and economic factors.
What are the risks in make vs buy strategy?
Risks. The second pillar under the Make Vs Buy strategy is risks involved with any decision. The major risk factors involved in making a product in the home country or purchasing it from foreign countries are quality, reliability, and predictability of outsourced solutions or services.
What are the factors affecting make-or-buy decision?
Factors Influencing Make or Buy Decision:Volume of Production: ... Cost Analysis: ... Utilization of Production Capacity: ... Integration of Production System: ... Availability of Manpower: ... Secrecy or Protection of Patent Right: ... Fixed Cost: ... Availability of competent suppliers or vendors.More items...
What step does the make-or-buy decision occur?
They proposed a make-or-buy decision process methodology through the following stages: planning, evaluation, internal costs, and performance analysis. ... Companies can perform their freight distribution in three different ways.
When should the make-or-buy decision be made?
Make-or-buy decisions usually arise when a firm that has developed a product or part—or significantly modified a product or part—is having trouble with current suppliers, or has diminishing capacity or changing demand. Make-or-buy analysis is conducted at the strategic and operational level.
What is make-or-buy analysis in project management?
A make-or-buy analysis is a general project management technique that is used to identify if a particular work can be accomplished by the project team or should just be purchased from external sources.
What are the 5 elements of decision-making?
Step 1: Identify the decision. You realize that you need to make a decision. ... Step 2: Gather relevant information. ... Step 3: Identify the alternatives. ... Step 4: Weigh the evidence. ... Step 5: Choose among alternatives. ... Step 6: Take action. ... Step 7: Review your decision & its consequences.
What costs are usually relevant in a make-or-buy decision?
In relevant costing, the decision to make or buy a product component involves proper analysis of costs. Generally, managers choose the option that will allow them to save on costs. The variable cost of manufacturing the product is compared with the purchase price of the product when bought from an outside supplier.
What is a make strategy?
It is a management concept for the creation of a structured, systematic plan or direction intended to achieve an objective. Strategy making usually consists of three tasks: vision or mission setting, objective determination or definition, and strategic choice.
Which is better make to order or make to stock?
Make to order is a viable strategy when the products you're manufacturing are complex, with many customizable features for your customers. Make to stock is a viable strategy when there isn't much variation between the products you manufacture and little customization on orders.
What are the four types of buy?
The 4 Types of Buying BehaviourExtended Decision-Making.Limited Decision-Making.Habitual Buying Behavior.Variety-Seeking Buying Behavior.
What does buy in mean in construction?
The definition of a buy-in is an agreement to do something, even though the person agreeing didn't have anything to do with the project beforehand. An example of a buy-in is a person agreeing to the design of a controversial product after all the details have been finalized.
What is a make or buy analysis?
It might initially appear that a make or buy analysis is a quantitative one that involves a simple comparison of internal production costs to a supplier's quoted price. However, the preceding points should make it clear that the make or buy decision actually encompasses a large number of qualitative issues that may completely override a numerical analysis of production costs.
What is the make or buy decision?
The make or buy decision involves whether to manufacture a product in-house or to purchase it from a third party . The outcome of this analysis should be a decision that maximizes the long- term financial outcome for a company . There are a number of factors to consider when making this decision, including the following items.
How important is the product to the corporate strategy?
How important is the product to the corporate strategy? If it is very important, then it could make more sense to manufacture the product, in order to maintain complete control over it. This option is most likely to be taken if the company has proprietary production technology that it does not want to share with a supplier. Conversely, something having little importance can more easily be shifted to a supplier.
Do businesses include fixed costs when adding up internal costs?
Businesses tend to include fixed costs when adding up their internal costs, which is incorrect. Only direct costs should be included in the compilation of the internal cost to manufacture a product in-house. This amount should be compared to the quoted price of a supplier.
Will shifting production to a supplier ease the burden on the company's bottleneck operation?
Will shifting production to a supplier ease the burden on the company's bottleneck operation? If so, this can be an excellent reason to buy the goods . If the bottleneck is elsewhere (such as in the sales department), then this is not a consideration.
Step1: Review the existing skills
In the first step, you need to take a look at what skills and resources your company currently has. This will help you determine whether it is feasible for your company to produce the product or service in-house.
Step2: Consider the costs
In this step, you need to consider all of the associated costs of both making and buying the product or service. This includes both up-front costs and ongoing costs.
Step3: Consider your capacity for production
In this step, you need to consider whether your company can produce enough of the product or service in order to meet demand and prevent lost sales due to stock-outs.
Step4: Consider the risks and opportunities
Next, you need to consider both the benefits as well as potential drawbacks of either making or buying a product. This includes intangible costs such as time, resources used for training employees, etc.
Step5: Consider the long-term outlook
Finally, you need to consider your company’s long-term outlook. And whether it is feasible to produce the product in-house for an extended period of time.
Factors that influence the decision
Make or buy analysis is an important factor in deciding whether to make or buy a product. However, there are other factors that also need to be considered such as:
Conclusion
Now that you understand the five easy steps to making a decision about whether to make or buy a product, it’s important to remember that there is no one-size-fits-all answer. The best way to determine which process is right for your company is by doing a thorough analysis of the situation and considering all the factors involved.
What is the meaning of "make or buy"?
A make-or-buy decision is an act of choosing between manufacturing a product in-house or purchasing it from an external supplier.
What is a make or buy decision?
A make-or-buy decision is an act of choosing between manufacturing a product in-house or purchasing it from an external supplier. Make-or-buy decisions, like outsourcing decisions, speak to a comparison of the costs and advantages of producing in-house versus buying it elsewhere. There are many factors at play that may tilt a company ...
Why Choose?
If a company is already in business there may be a point when certain situations arise that will cause a company to pause and consider which direction it should proceed in; whether it should buy or make the parts or products it needs.
Why do companies use quantitative analysis?
Companies use quantitative analysis to determine whether making or buying is the most cost-efficient method.
How to compare costs accurately?
To compare costs accurately, a company must consider all aspects regarding the acquisition and storage of the items versus creating the items in-house, which may require the purchase of new equipment, as well as storage costs.
What factors can a firm use to make an item in-house?
Similarly, factors that may tilt a firm toward making an item in-house include existing idle production capacity, better quality control, or proprietary technology that needs to be protected.
What factors influence a firm's decision to buy a part rather than produce it internally?
Factors that may influence a firm's decision to buy a part rather than produce it internally include a lack of in-house expertise, small volume requirements, a desire for multiple sourcing, and the fact that the item may not be critical to the firm's strategy.
What is a make or buy decision?
A Make or Buy Decision is a decision made to either manufacture a product/ service in house or buy it from outside suppliers (outsourcing) based on cost-benefit analysis. A complete or accept decision can be made using quantitative or qualitative research and most of the time, the results of quantitative analysis (cost-benefit analysis) ...
What are the advantages of making a buy decision?
Some of the advantages of making or buy decisions are as follows: The finding helps choose the most efficient option to go about in-house production of outsourcing. The decision helps in the strategic maneuver of the business. The decision helps save the cost for many businesses.
What are the factors considered when deciding to buy the good or service from the outside supplier?
Environmental reasons. Political reasons. The following are the major factors considered while deciding to buy the good or service from the outside supplier. Lack of expertise. Research and specialized know-how of the supplier better than the buyer.
Why does Apple outsource its manufacturing to China?
The smartphone giant Apple Inc. outsources the manufacturing of all its devices to China because manufacturing is not its core competency. It is also significantly cheaper to assemble the tools in China due to substantially lower costs.
Can a company choose to manufacture in the house?
Considering the company has the idle capacity, and it is already incurring a large part of fixed expenses, it can choose to manufacture in the house if the marginal cost of manufacturing is less than what it will cost to buy from outside suppliers.
Should you make or buy?
The make or buy decision should be taken with utmost care keeping the long-term and short-term benefits into consideration. There are pros and cons to both make and purchase; however, generally, businesses tend to outsource function where they do not have a core competency or when the cost of procuring the components or services from outside suppliers is significantly cheaper.
What is the meaning of "make or buy"?
A make-or-buy decision refers to an act of using cost-benefit to make a strategic choice between manufacturing a product in-house or purchasing from an external supplier. It arises when a producing company faces a diminishing capacity, experiences problems with the current suppliers, or sees changing demand.
What is the make or buy decision?
The make-or-buy decision compares the costs and benefits that accrue by producing a good or service internally against the costs and benefits that result from subcontracting. For an accurate comparison of costs and benefits, managers need to evaluate the benefits of purchasing expertise against the benefits of developing and nurturing the same expertise within the company.
Why is it important to make or buy decisions?
One of the most notable advantages that a company enjoys when embracing a make-or-buy decision approach is that it can lower costs and increase capital investments, regardless of whether it decides to make materials in-house or subcontract from an external vendor. 2.
What is the decision to make or buy?
A company’s decision on whether to make or buy is based on its core competence. The production cost and quality problems are the major triggers of a make-or-buy decision. Other factors are managerial decisions and a company’s long-term business strategy that dictate the current operations pattern.
What are the factors that determine outsourcing?
While cost remains the hallmark of any business decision, other factors such as strategic, technological, core competency, risks, and relationships , also constitute outsourcing decisions, not to mention factors involved in developing and introducing a new product.
Why is it important to set up a make or buy process?
It is partly due to companies’ distinct behavior patterns and the fact that businesses operate in different business environments that are unique to each business. However, cost accounting remains the primary dimension of the make-or-buy decision.
How do companies realize the benefits of their policies?
To realize the benefits, companies must consider the internal and external environment in which they operate. In particular, the culture in which such decisions are reached, and the agenda of the parties involved can influence the decisions and their implementation, as well as the sustainability of the policy.
What is a make or buy cost analysis?
A make or buy cost analysis involves a determination and comparison of the cost to make the part and the cost to buy it. The final make or buy decision must be based on a careful weighing of the cost considerations and various quantitative considerations.
What to learn after reading Make or Buy Decision?
After reading this article you will learn about:- 1. Introduction to Make or Buy Decision 2. Factors Considered for Make or Buy Decision 3. Criteria 4. Analysis 5. Procedure and Personnel Involved 6. Checklist.
What do companies prefer to own?
Companies prefer own manufacturing and buying only raw material or semi-finished parts.
What is buy permits?
Buy permits specialisation, allows manufacture by most efficient equipment, lowers inventories, change of design without loss of investment in equipment or inventory, obtaining best price of product, and supplying more varied experience and encourages growth of ancillaries.
How to calculate total cost?
and Total cost = A × I + A × S/Q 1 + C (R – A) Q 1 /2R
How to calculate total cost of procurement?
and also we know total cost = Procurement cost/year + Inventory cost per year
Is it clear that the decision must be in favour of buying the part?
On the basis of above cost analysis it is quite clear that the decision must be in favour of buying the part.
What is a make or buy program?
Make-or-buy programs. (a) General. The prime contractor is responsible for managing contract performance, including planning, placing, and administering subcontracts as necessary to ensure the lowest overall cost and technical risk to the Government. When make-or-buy programs are required, the Government may reserve the right to review ...
When prospective contractors are required to submit proposed make or buy programs, the solicitation shall include?
When prospective contractors are required to submit proposed make-or-buy programs, the solicitation shall include-. (1) A statement that the program and required supporting information must accompany the offer; and. (2) A description of factors to be used in evaluating the proposed program, such as capability, capacity, availability of small, ...

What Is A Make-Or-Buy Decision?
Understanding A Make-Or-Buy Decision
- Regarding in-house production, a business must include expenses related to the purchase and maintenance of any production equipment and the cost of production materials. Costs to make the product can include the additional labor required to produce the items, which takes the form of wages and benefits, storage requirements within the facility, holding costsoverall, and the pro…
Choosing Make Or Buy
- The results of the quantitative analysis may be sufficient to make a determination based on the approach that is more cost-effective. At times, the qualitative analysis addresses any concerns a company cannot measure specifically. Factors that may influence a firm's decision to buy a part rather than produce it internally include a lack of in-house expertise, small volume requirements, …
Why Choose?
- If a company is already in business there may be a point when certain situations arise that will cause a company to pause and consider which direction it should proceed in; whether it should buy or make the parts or products it needs. Some of these events could be a trusted supplier shutting down, an increase or decrease in demand for the product, or a possible path for new op…