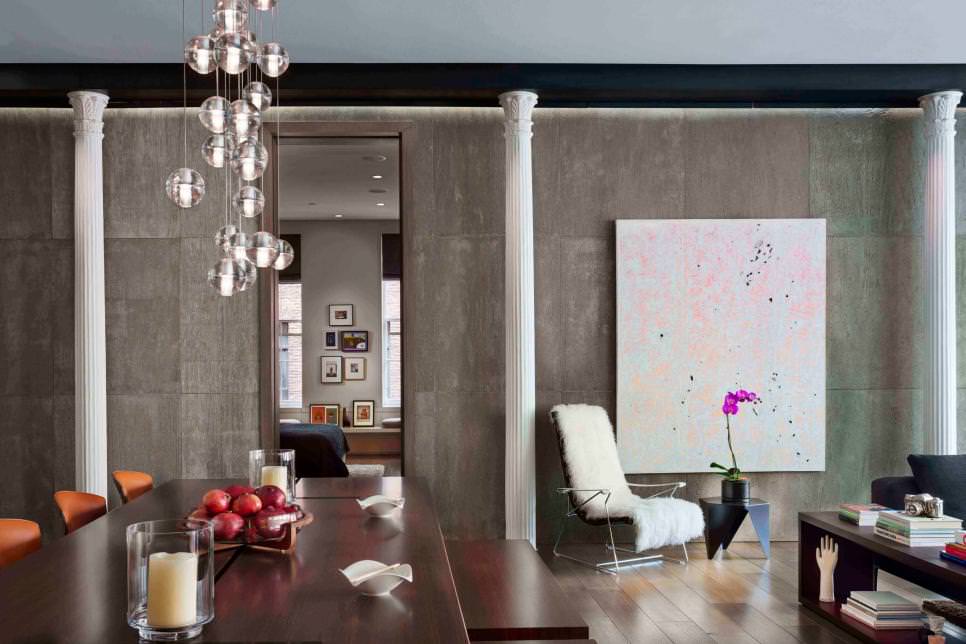
Is precast concrete better than modular building?
Precast is perfect for buildings which are typical in layout and plan. If the loads coming onto the floor is non moving and lighter. Both are fast paced. Logistic is an issue. We also have issues fixing the Precast concrete panels. Modular is better if buildings are divided into various functional units.
How to form a homemade concrete wall?
Part 4 Part 4 of 4: Pouring and Curing Concrete
- Mix enough concrete to complete the wall all at once. Purchase some concrete mix and pour it all into a mixer with a ramp or hose.
- Pour the concrete in layers, starting at the end of the wall. Pour the concrete directly into the wood form using a chute or hose attached to the mixer.
- Pull the spacers out as you pour the concrete. ...
Are superior walls better than poured concrete?
Superior Walls foundations are better than poured or block foundation because they are made with steel re-enforced, high-density concrete (5,000 psi) that's poured into permanent forms in a controlled environment. (According to the American Concrete Institute, 4,000 psi mix is watertight.) What are superior basement walls?
What is the meaning of precast concrete?
What is Precast Concrete? The form of construction where concrete is casted in a re-usable mould and then cured in a controlled environment (precast plant) is called precast concrete. The casted structural member is then transported to the construction site and then erected.
What is precast concrete used for?
Precast concrete is widely used in low- and mid-rise apartment buildings, hotels, motels, and nursing homes. The concrete provides superior fire resistance and sound control for the individual units and reduces fire insurance rates. Precast concrete is also a popular material for constructing office buildings.
What is precast concrete in simple words?
Precast concrete is a construction product produced by casting concrete in a reusable mold or "form" which is then cured in a controlled environment, transported to the construction site and maneuvered into place; examples include precast beams, and wall panels for tilt up construction.
What is the difference between concrete and precast concrete?
Precast concrete components are ready for immediate use upon delivery while cast-in-place concrete are not. This eliminates unnecessary time needed to set up cardboard forms, bend and position rebar, pour and vibrate concrete and then wait for the concrete to cure.
What are the advantages of using precast concrete walls?
Precast concrete wall panels provide numerous long term cost advantages with exceptional durability, lower energy costs and lower maintenance costs when compared with insulated metal panel systems. and ability to be produced and erected year-round shortens project schedules.
What are the disadvantages of precast concrete?
Disadvantages of Precast ConcreteHigh Initial Investment: For installing a precast concrete plant, heavy and sophisticated machines are necessary which requires a high initial investment. ... Transportation Issue: The construction site can be at a distant location from the precast concrete plant.More items...
Does precast concrete crack?
These cracks occur when the surface dries quickly due to heat or wind and no controls are used to cure the surface at a slower rate maintaining moisture while the cement hydrates. These types of cracks may also present themselves if there is a high water to cement ratio in concrete mix design.
How long does a precast concrete wall last?
50 to 100 yearsPrecast concrete structures have a lot to live up to; they must endure all manner of environmental conditions. Ideally, such products should last 50 to 100 years or more. Curing the concrete in a controlled environment is key to its longevity.
Are precast concrete walls cheaper?
A recent research project directly compared the costs of precast concrete to on-site pouring and found precast concrete slabs save 23 percent over cast-in-place concrete. Columns yielded a similar result, with savings at 21 percent less cost than on-site pouring.
Is it cheaper to build with precast concrete?
Are concrete homes expensive to build? Homes made from poured concrete or concrete blocks are already cheaper than brick homes, but precast concrete homes are cheaper still, costing around 23 percent less and taking a much shorter time to complete.
Are precast walls strong?
Structural precast concrete panels are comprised of high-strength concrete and prestressed steel strand. It's relatively routine for precast concrete wall panels have a compressive strength of approximately 7,000 PSI. You can apply loads in excess of 100,000 pounds to the panels, Miks says.
Are precast concrete walls suitable for houses?
The precast concrete wall is used as an interior surface which saves time and money by eliminating the need for separate stud framing and drywall costs. The precast concrete wall can be used as load-bearing structures and will save costs by eliminating the need for an additional structural framing system.
Are precast concrete walls expensive?
Precast concrete is estimated to be 23% less expensive than poured concrete. Installing a precast concrete wall costs $4,800 on average. While precast materials cost from $20 to $30 per square foot, precast installation is much less labor-intensive than pouring concrete.
What is the definition precast?
Definition of precast : being concrete that is cast in the form of a structural element (such as a panel or beam) before being placed in final position.
What is concrete in simple words?
concrete • \kahn-KREET\ • adjective. 1 : naming a real thing or class of things 2 : formed by coalition of particles into one solid mass 3 : relating to or involving specific people, things, or actions rather than general ideas or qualities 4 : relating to or made of concrete.
Why is precast important?
The main advantages of precast technology are quality, speed and value for money. It can help in time savings of up to 64 percent compared to similar projects using normal construction methods. If a brick-and-mortar method takes one year to complete, the precast method can take about four months.
What is the ACI code for precast concrete?
The concrete panels are designed in accordance with PCI Design Handbook-Precast and Prestressed Concrete (MNL-120), Design Responsibility for Architectural Precast Concrete Projects (ACI 533.1R-02), and ACI 318 Structural Concrete Building Code. Steel elements of a wall system are designed in accordance with AISC specifications for steel construction. Precast concrete elements are designed in accordance with ACI and PCI specifications.
What are the different types of precast panels?
There are generally four types of precast panels used as part of building envelopes: Cladding or curtain walls. Load-bearing wall units. Shear walls. Formwork for cast-in-place concrete. Precast cladding or curtain walls are the most common use of precast concrete for building envelopes.
Why are joints important in a precast concrete envelope?
The joints between precast units or between precast and other building components must be maintained to prevent leakage through the precast wall system.
What is precast shear wall?
Precast concrete shear wall panels are used to provide lateral load resisting system when combined with diaphragm action of the floor construction. The effectiveness of precast shear walls is largely dependent upon the panel-to-panel connections.
Why is my precast concrete wall cracking?
Most distress and deterioration encountered with precast concrete wall systems can be attributed to problems during erection, an chors used to attach panels to the structure, or corrosion of the embedded reinforcing steel. Panel cracking, displacements, or other distress conditions can occur at locations where anchors are inadequately or improperly connected. Poor construction is often the result of poor quality control and out of tolerance fabrication or erection of the panels. Also, damage from handling during construction can result in panel cracking, some of which may not become evident for several years.
How are precast panels supported?
Typically, each precast panel is independently supported to the building structure using an assemblage of metal components and anchors. Joints around each of the precast panels are usually filled with sealant.
What is the exterior surface of precast concrete?
The exterior surface of precast concrete can vary from an exposed aggregate finish that is highly ornamental to a form face finish that is similar to cast-in-place. Some precast panels act as column covers while others extend over several floors in height and incorporate window openings.
How is it Made?
Previously, cast-in concrete was built using forms, then having to pour the concrete, waiting for the concrete to cure, all while being done on-site. All of the raw materials have to be shipped to the project site.
How does precast concrete differ from cast in place?
Like we mentioned earlier, cast-in-place is done all on-site. Once the concrete is poured and cured, the wall is assembled. With precast concrete, the shipped components have to be put together. This is relatively easy and doesn’t require highly skilled workers.
What is precast concrete used for?
Precast concrete has been popular for parking structures, bridges, foundations, curb inlets, culverts and catch basins, sound walls, retaining walls, and other walls and fences. Generally, architects like to use precast concrete for multi-housing units, office buildings, hospitals, medical centers, schools, and retail shopping centers.
What happens if you don't pass a concrete inspection?
Anything that doesn’t pass inspection is crushed to be recycled as aggregate . Once the pieces pass inspection, they are shipped to the project site to be assembled.
What was the Roman monument made of?
Many of the ancient Roman monuments were made, in part, using an older form of concrete . Now that you know a bit more about precast concrete, it’s time to consider it for your next fencing or wall project. If you would like to learn more about precast concrete for your project, contact American Precast Inc. today for a free consultation!
Is precast concrete made on site?
Precast concrete is not made on-site. It’s typically made in a climate-controlled environment by a skilled worker like cast-in-place concrete; precast concrete is poured into a wooden or steel mold with wire mesh or rebar included to add strength.
Can you use precast concrete again?
The great thing is, unlike cast-in-place concrete, these molds can be used again and again. Precast concrete can have pigments and/or aggregates added to the concrete prior to pouring it into the molds. The molds are extremely versatile and can have interesting motifs or decorations added to them. This allows precast concrete to be more varied ...
Is There a Downside to Precast Concrete?
Truly, the only real downside to choosing precast concrete is that the pieces must be transported from the plant to the construction site for installation. However, we find that the ease and efficiency of the precasting process, along with the reliability and predictability of the finished products are benefits that far outweigh any nuisance created by delivering pre-made concrete pieces to the construction site. Beyond this one and only hangup, we realize that change can be a difficult thing to face.
Why is precast concrete cured?
Control: Since precast concrete is cast and cured in a controlled environment like a plant, the chances of error are greatly reduced. Environmental factors like weather are no longer pertinent to the production of pieces. The most ideal conditions are used each time, building confidence that each piece will be poured and cured precisely as required. This minimizes wasted excess materials, since the process is so predictable, and allows for construction timelines and schedules to be met more readily each time.
What is the difference between precast and site cast concrete?
The main difference between precast concrete and site-cast concrete is that pre cast concrete is poured off-site, usually at a plant, using a mold. Site cast concrete, in comparison, is poured on the construction site itself, subjecting it to environmental factors, weather, unstable schedules, and much wasted excess material. When concrete is precast in a plant, on the other hand, the entire process in controlled before bringing the cured concrete to the construction site. Weather is no longer a factor, nor are other environmental factors that can be huge obstacles with on-site concrete pours. In precast concrete, the mold often includes a pre-stressed cable. While this is not always necessary or included, the process of curing the concrete releases a tension that transfers strength to the concrete itself, making it even more durable.
What are curb inlets and catch basins?
Curb Inlets and Catch Basins: Aiding in storm-water and wastewater drainage, retention of rainwater, and stormwater runoff are all possible despite the different specifications that vary from state to state, and even in different municipalities. You can be sure your pieces reflect the exact manufacturing specifications when you choose precast concrete since these are customized to each specific project.
What are the natural materials used in precast concrete?
With precast concrete, natural materials like sand, gravel, rock, and water are used as aggregates, and the water used is often recycled. These natural materials are typically harvested locally, cutting down on hauling trips that are expensive and environmentally unfriendly.
What are the types of buildings that use precast concrete?
Here are some common types of buildings regularly using precast concrete: Schools: Schools can be built in a timely and efficient manner, keeping the project schedule on track. Permacast Walls provide sound-proof security walls along the perimeters of schools, creating a safer environment for students and staff.
How does casting concrete affect the environment?
Casting concrete in a plant greatly reduces the amount of waste from packaging, excessive concrete, bracing and form work, and other debris that builds up on a construction site. Also, less raw material is used leaving the environment in and around the construction site untouched and less polluted.
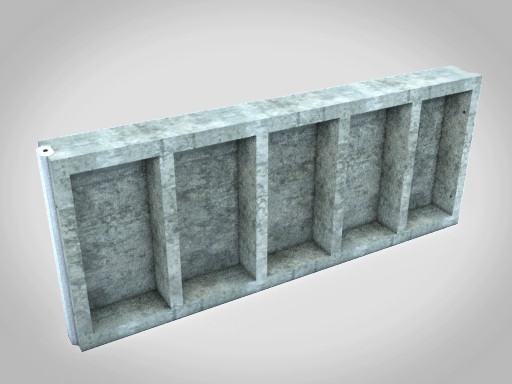
Introduction
- Architectural precast concrete has been used since the early twentieth century and came into wide use in the 1960s. The exterior surface of precast concrete can vary from an exposed aggregate finish that is highly ornamental to a form face finish that is similar to cast-in-place. Some precast panels act as column covers while others extend over several floors in height and …
Description
- Precast Panel Types for Building Envelopes
There are generally four types of precast panels used as part of building envelopes: 1. Cladding or curtain walls 2. Load-bearing wall units 3. Shear walls 4. Formwork for cast-in-place concrete Precast cladding or curtain walls are the most common use of precast concrete for building env… - Support and Anchorage Systems
The connections for precast concrete panels are an important component of the envelope system. Precast manufacturers utilize numerous different types of anchors but they are often characterized as gravity and lateral types of connections. The primary purposes of the connecti…
Fundamentals
- Structural Aspects of Design
Precast concrete wall systems are most often constructed as a curtain wall or veneer, in which no building loads are transferred to the concrete panels. Most typically the precast concrete wall system must resist lateral loads directly imparted on it, such as from wind and earthquake; as w…
Applications
- Precast concrete wall systems allow a wide variety of colors, finishes and architectural shapes. Precast concrete can be used in environments that allow the use of conventional cast-in-place concrete. In addition, precast concrete may be made in a controlled environment and erected in an environment that would not allow site casting of concrete. The concrete used in precast pane…
Details
- The following details can be downloaded in DWG format or viewed online in DWF™ (Design Web Format™) or Adobe Acrobat PDF by clicking on the appropriate format to the right of the drawing title. Architectural Precast Window Jamb and Sill DWG | DWF | PDF Architectural Precast Round Penetration DWG | DWF | PDF Architectural Precast Square Penetration DWG | DWF | PDF Archit…
Emerging Issues
- The necessity to make building envelopes blast-resistantforces reconsideration of precast concrete joint and connection designs.
Relevant Codes and Standards
- American Concrete Institute ACI 318—Building Code Requirements for Structural Concrete
- American Concrete Institute ACI 301—Specifications for Structural Concrete
- Precast/Prestressed Concrete Institute PCI Design Handbook-Precast and Prestressed Concrete(MNL 120)
Additional Resources
- American Concrete Institute
1. ACI 318—Building Code Requirements for Structural Concrete 2. ACI 301—Specifications for Structural Concrete 3. ACI 201.2—Guide to Durable Concrete 4. ACI 533.1R—Design Responsibility for Architectural Precast Concrete Projects - ASTM International
1. ASTM C 33—Aggregates in Concrete 2. ASTM C 457—Air Void 3. AGGREGATE REACTIVITY 4. ASTM C 856—Petrographic Analysis of Hardened Concrete