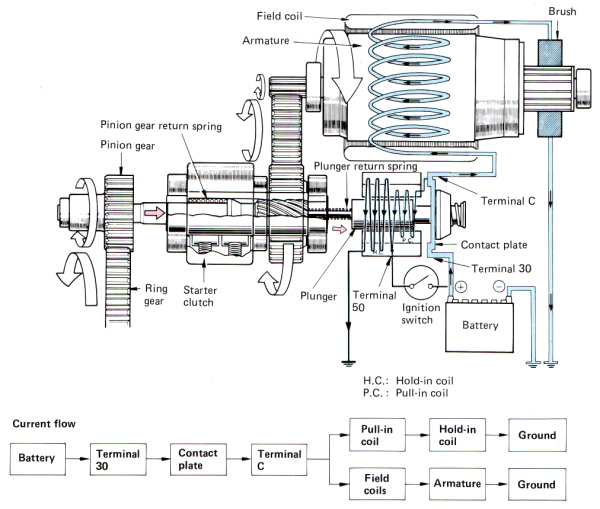
What is the advantage of using a reduction type starter motor?
The main benefit of gear reduction is that it allows for significantly smaller starters that produce an equal or greater amount of torque in comparison to much larger direct drive starters.
Why do manufacturers use reduction type starters?
By design, a gear-reduction starter is more efficient, so it requires less current draw, which causes less heat and you get more cranking power.
What are the main differences between a direct drive and a reduction drive starter motor?
The gear reduction starter allows the DC motor to spin much faster allowing it to develop more torque and run more efficiently than the direct drive starter that runs at half to 1/3 the speed of the more efficient gear reduction starter. Gear reduction starters are more expensive.
What are the two types of starter?
Types of Motor StartersManual Starters.Magnetic Motor Starters.Direct-On-Line Starter.Rotor Resistance Starter.Stator Resistance Starter.Auto Transformer Starter.Star Delta Starter.NEMA Rating.More items...
What does A reduction starter do?
Gear reduction starters use gears to reduce the speed of a higher-speed electric motor in order to extract more torque at the flywheel end of the starter.
Is A gear reduction starter worth it?
Take-home message to all of this: In most cases, a gear-reduction starter is lighter, more reliable and more efficient than the one originally fitted to your classic.
What are the 3 types of starter motor?
At PSI Power & Controls, we handle three major product types when it comes to motor starters: wye-delta open transmission, soft-start solid state, and wye-delta starter OEM. How do these differ, and which suits your needs?
How many types of starter motors are there?
two typesThe starter motors have many types, but they are mainly classified into two types: manual and magnetic.
Are direct drive and gear reduction starters interchangeable?
A gear reduction starter may appear different by design. For example, the Delco Remy 29MT™, 35MT™, 38MT™and 39MT™ all incorporate a nose-less design and don't include a cone around the starter drive. Despite this design difference, these starters are completely interchangeable with straight drive nose style starters.
What is the most common type of starter motor?
Magnetic Starter Magnetic starters are the most common type of starter & they are mostly used for high power AC motors. These starters operate electromagnetically like a relay that breaks or makes the contacts using magnetism.
How does a reduced voltage motor starter work?
A simple and common method of starting a motor at reduced voltage is used in primary resistor-type starters. In this method, a resistor is connected in series in the lines to the motor. As current flows through the resistors, a voltage drop occurs, and the voltage at the motor terminals is reduced by that amount.
What are the types of starters of 3 phase induction motor?
Methods of Starting Three Phase Induction Motors. ... Direct-on-Line Starter (DOL) ... Star Delta starter. ... Auto-Transformer Starting. ... Rotor Resistance Starter. ... Review.
Why we use different types of starters?
Such starters directly connect the motor with the power line providing the full voltage. The motors connected through such starters have low power ratings so that they do not create a huge voltage drop in the power line. They are used in an application where motors have low ratings & need to run in one direction.
What is the purpose of the main reduction gear?
A reduction gearboxes, or speed reducer, is used to reduce the speed of the input, from the motor, while also multiplying the torque the input creates.
What is the most commonly used reduced voltage starting method?
Primary resistor starting is a simple method for reducing the voltage at the motor terminals during starting, although it is not a very energy-efficient method. The power circuit is shown in figure 3.
What is the main reason a starter is required?
A starter motor is required to run the internal combustion engine up to a speed sufficient to produce satisfactory carburation. The starter motor is mounted on the engine casing and a pinion on the end of the starter motor shaft engages with the flywheel teeth. The gear ratio between pinion and flywheel is about 10:1.
What are the two types of starter motors?
The starter motors have many types, but they are mainly classified into two types: manual and magnetic.
What is a starter motor?
A starter motor is an electrical device that is utilized to start & stop a motor reliably. Same as a relay, the motor starter switches the power OFF/ON, and unlike a relay, it also presents low voltage and overcurrent protection.
How does a Motor Starter operate?
A starter is a switching device that has electrical contacts (both for incoming and outgoing). Based on the operation, starters are fundamentally divided into electrically operated and hand-operated devices.
What is a stator resistance starter?
Stator resistance starter employs the reduced voltage starter technique to start motors. External resistance is attached in series with all phases of a 3 phase induction motor’s stator. The resistor’s function is to lessen the line voltage (subsequently decreasing the initial current) connected to the stator.
Why do you need to decrease the voltage at the start of a motor?
The most typical starting procedure is to decrease the voltage at the starting of the motor to diminish the inrush current that could damage the motor’s windings and cause a considerable dip in voltage. These starters are common in high-rated motors.
What is a direct online starter?
Direct Online Starter, aka DOL, is the simplest motor starter that directly connects the motor to the power supply. It has a magnetic contactor that combines the motor to a supply line and an overload relay for protection toward overcurrent. There is not a voltage reduction for reliable starting a motor. So, the motor working with such starters has a rating below five hp. It has two manageable push buttons that start and stop the motor.
Why is the voltage in a motor at the safe level?
The voltage in the motor is minimum (at the safe level) because of the voltage drop over the resistor. The low stator voltage narrows the starting inrush current that may damage the windings. As the speed increases, the resistance is decreased, and the stator phase is connected to the power lines directly.
What is the difference between direct drive and gear reduction starters?
When direct drive and gear reduction starters are compared, direct drive units are typically cheaper , and gear reduction units tend to be smaller, lighter, ...
What is the ratio of a starter shaft to a drive mechanism?
Although “gear reduction” technically takes place between the starter’s pinion gear and the ring gear on the flywheel or flex plate, the pinion gear itself rotates in a 1:1 ratio with the armature shaft.
Why Replace Direct Drive With Gear Reduction?
Since the late 1980s, the OEMs have steadily moved away from direct drive starters toward gear reduction starters. Although gear reduction starters are more complex, which makes them more expensive, they are also smaller, lighter, and more efficient.
What is the benefit of gear reduction?
The main benefit of gear reduction is that it allows for significantly smaller starters that produce an equal or greater amount of torque in comparison to much larger direct drive starters. The main drawback is that they are typically more expensive.
Is gear reduction more expensive than direct drive?
These starters have also come down in price over years. So while gear reduction starters are still more expensive than direct drive starters, they are more affordable than they used to be.
Is Elreg a gear reduction starter?
Gear reduction starters are also available from the aftermarket, which is one way to offset the higher price that is typically associated with these units. For instance, an Elreg brand 39mt starter is functionally identical to a Delco 39mt, but the aftermarket unit represents a significant savings versus the original equipment. In cases where a high quality aftermarket unit is available, it will often cost about half as much as an OEM unit.
What is the difference between a gear reduction starter and a direct drive starter?
Weight – Gear reduction starters are smaller and lighter than direct drive models. When replacing a direct drive starter with a gear reduction model, there is more space around it, which makes installation easier and may improve heat-resistance of the solenoid.
Why are gear reduction starters faster?
However, because their torque is higher, they have a faster speed when pistons are at TDC on the compression stroke where it is needed most. This is why they are ideal for diesel or other high-compression engines.
Why is my direct drive starter slow cranking?
Maintenance – Gear reduction starters have a higher part count, but internal wear is often less compared to direct drive starters since they use bearings versus the bushings common in direct drive starters. Misaligned or worn bushings are the most common cause of slow cranking of hot engines that use direct drive starters.
What is a Bendix drive?
The motor armature and the Bendix drive, which engages the flywheel’s ring gear, are directly connected and positioned in-line with one another. There may be construction differences such as the use of field coils or permanent magnets within the motor. Gear reduction starters use gears to reduce the speed of a higher-speed electric motor in order ...
What is gear reduction?
Gear reduction starters use gears to reduce the speed of a higher-speed electric motor in order to extract more torque at the flywheel end of the starter. Two typical designs are Offset Gear Reduction and Planetary Gear Reduction.
How much power does a direct drive starter need?
Power – Direct drive starters require up to 50 percent more electrical power to turn over the car’s engine than do gear reduction starters. This means direct drive requires more current from the car’s battery, larger battery cables are needed and other components are designed to handle higher current. Weight – Gear reduction starters are smaller ...
What happens when a starter motor fails?
When a vehicle’s starter motor begins to fail, a heavy strain is placed on your vehicle’s battery and other components in the starter circuit. Repairing or replacing your starter motor at the first signs of failure saves you the added cost of replacing supporting components.
Why We Need a Starter with a Motor?
When current is given to the induction motor, the current of the magnetic field moving in the rotor winding and the AMF behind the current produced increases the motor torque, which leads to a higher rotor current.
What is step down transformer?
A step-down or autotransformer is used to reduce the voltage applied to the stator at the beginning of the motor. This type of transformer can be connected to both star and delta type motors.
How does a soft starter work?
The Soft Starter works on the same voltage reduction system as other starters. This motor uses a semiconductor switch like the TRIAC to control the voltage as well as the current supplied to the induction motor.
How to turn on a motor?
The most common way to turn on a motor is to drastically reduce the voltage at the start of the motor to reduce the current flow so that the windings of the motor can be damaged as a result of a drastic reduction in voltage. This type of starter is used for high-rated motors.
How to change AC motor speed?
To change the speed of an ac motor it is necessary to vary the frequency of the given power supply or to vary the number of poles of the motor (by reconnecting the windings in some). This type of starter drives the motor at a slightly pre-selected speed to complete its applications.
What type of starter works on full voltage?
This type of starter operates on full voltage. It is also known as a slip ring motor starter as it only works for one slip ring induction motor.
What is a fuse control tricac?
Fuse control TRIAC is used to provide variable voltage. In voltage, TRIAC’s carrier angle or firing angle can be separated. The minimum carrying angle is kept to give this reduced voltage to the motor. The carrying angle is increased and the voltage is gradually increased. At the maximum carrying angle, the full line voltage is applied to the induction motor and it runs at the prescribed speed.
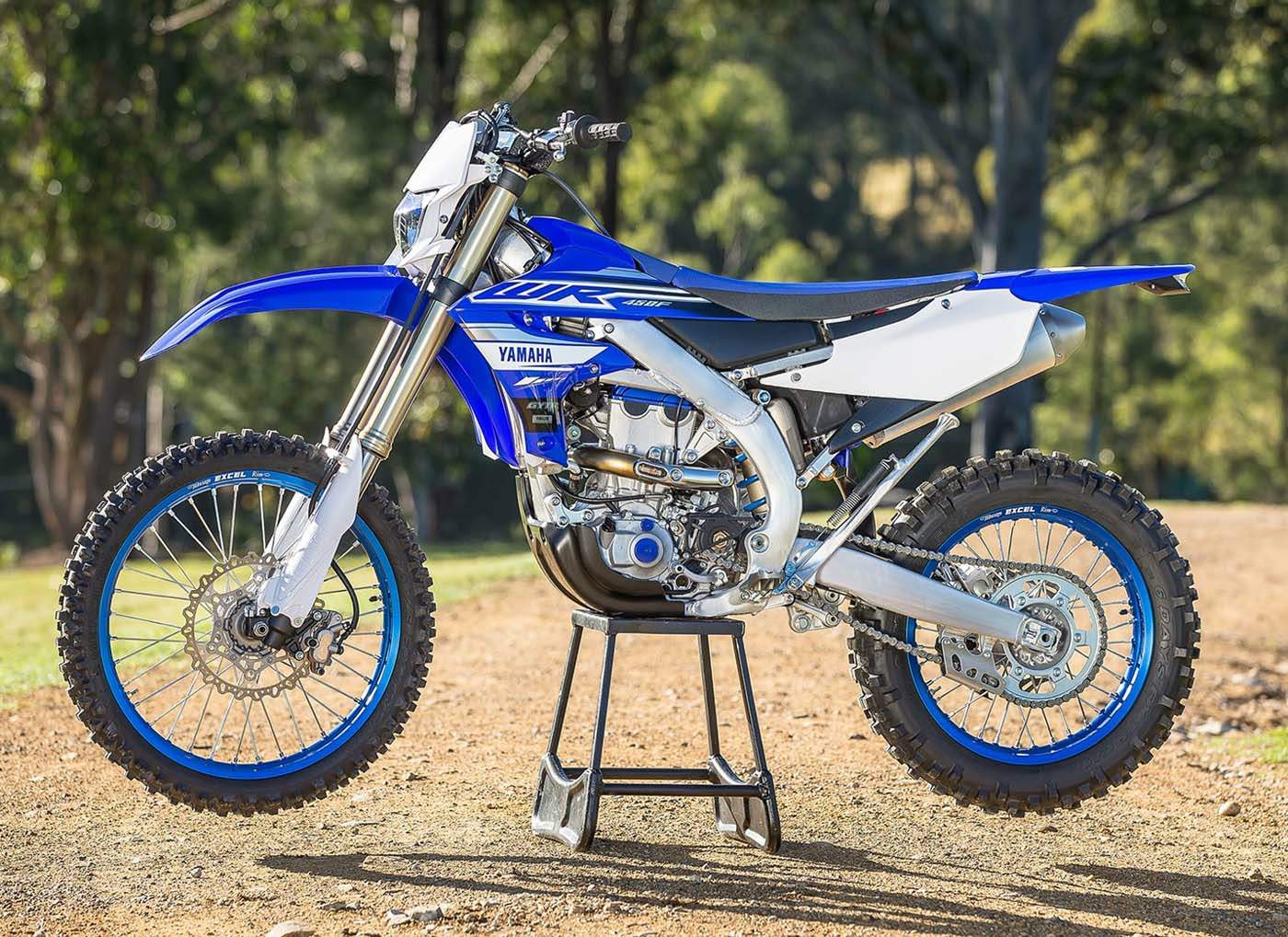