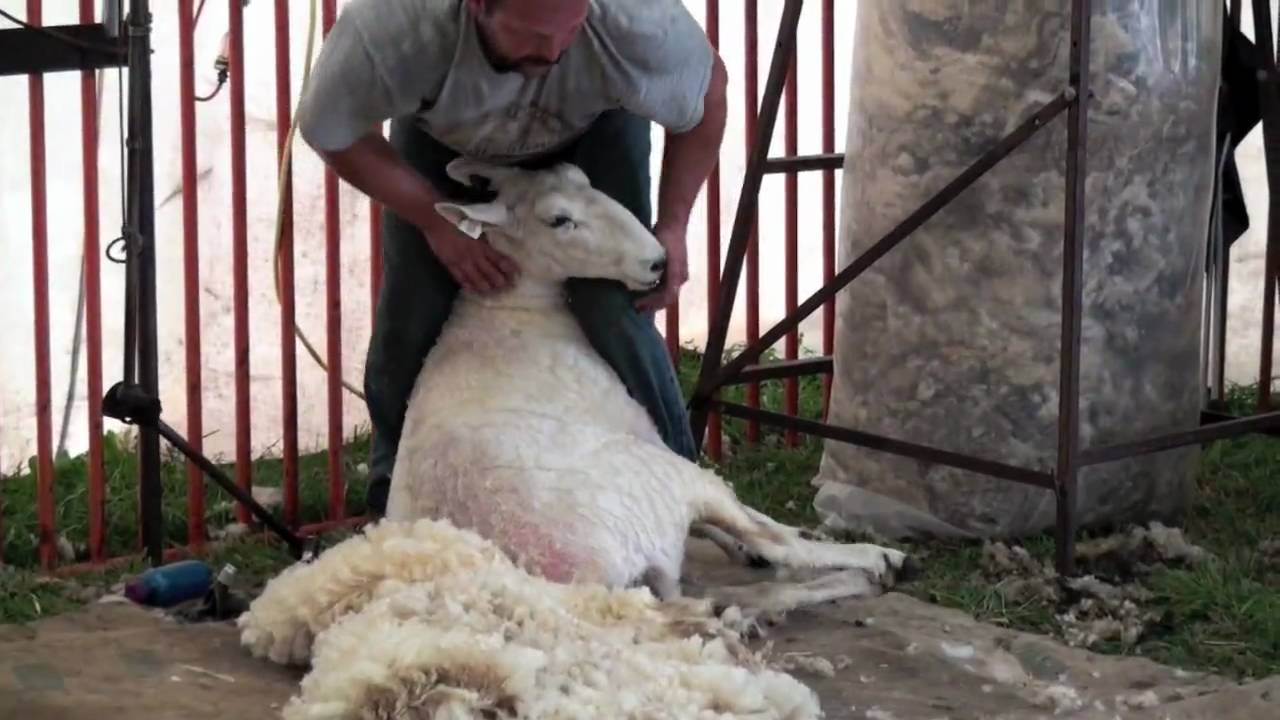
What is shear cutting?
What is a top knife?
Can crush cutting be performed by a web path?

What is the difference between shearing and cutting?
In fact, they're both cutting or finishing processes that involve the use of a blade to remove excess material or create a desired shape for sheet metal. The main difference is that shearing uses straight-edge blades whereas the blades used in die cutting are curved.
What is a cutting shear used for?
Metal cutting shears are used for cutting scrap metal to a suitable size for handling and transport to a metal recovery operation. Sometimes they are constructed as an alligator shear or a shearing and baling press.
What can a metal shear cut?
Shearing performs straight-line cuts without forming chips or burning or melting the material. This allows the process to work well with most softer metals, such as aluminum, brass, bronze, and mild (low carbon) steel.
How thick of metal can a shear cut?
1/4"Manual metal shear can cut sheet metal, rebar, and round stock as well. Its blade length is 8" / 203.2 mm, and cutting thickness can reach 1/4" maximum, 3/16" thickness at full size.
What are the three types of shearing?
TypesAir/pneumatic shears use a pneumatic cylinder to power the crosshead and upper blade.Hydraulic shears are driven or powered by a hydraulic cylinder. ... Hydromechanical shears are driven by a hydraulic cylinder or hydraulic motor.More items...
What are the three types of shears?
Upright snips, which are ideal for use in tight spaces; Long cuts snips, which are ideal for making longer straight cuts; and. Hard snips with head treated blades that can be used to cut through tougher metals.
What is a disadvantage of shearing?
Shearing Disadvantages Not ideal for low-volume manufacturing applications. Exceptionally hard metals like tungsten cannot be sheared. May cause deformity in sheet metal.
What are the two most common shearing operations?
The most common shearing operations are punching-where the sheared slug is scrap or may be used for some other purpose-and blanking-where the slug is the part to be used and the rest is scrap.
What are the different types of shearing?
Shearing-type operations include blanking, piercing, roll slitting, and trimming. It is used for metal, fabric, paper and plastics.
Can stainless steel be sheared?
Shearing stainless steel plate or sheet is an efficient, cost effective way to cut common squares or rectangles from larger stainless steel plates that do not require internal part geometry to be cut.
How does a metal shear work?
Metal is sheared between two offset blades, rather like scissors. The material is held down flat and the top blade lowered onto the surface. As the blade touches the metal it starts to push it down over the lower blade. A gap between upper and lower blades provides room for the metal to flow.
What are the safety precautions when using a shear?
6 Shearing Machine Safety Precautions to Prevent AccidentsShear Safety Tip #1: Keep Your Metal Shear Well-Maintained. ... Shear Safety Tip #2: Keep the Shop Well-Lit. ... Shear Safety Tip #3: Do Not Increase the Opening Height of the Finger Protector. ... Shear Safety Tip #4: Familiarize Employees with the Shear.More items...•
What are the advantages of shearing?
The benefits of shearing before lambingDrier environment. ... Cleaner environment. ... Increased lamb birth weight. ... Improved fleece quality. ... Ewes have better access to feeders. ... Barn is warmer for winter lambing. ... Lambs access the teat easier. ... Ewes seek protection in bad weather.More items...
What are the two most common shearing operations?
The most common shearing operations are punching-where the sheared slug is scrap or may be used for some other purpose-and blanking-where the slug is the part to be used and the rest is scrap.
How does a metal shear work?
Metal is sheared between two offset blades, rather like scissors. The material is held down flat and the top blade lowered onto the surface. As the blade touches the metal it starts to push it down over the lower blade. A gap between upper and lower blades provides room for the metal to flow.
Can shears cut metal?
Nibblers and shears are two of the most common power tools available for cutting sheet metal, providing a faster and less fatiguing alternative to hand tools.
What is shearing in metal cutting?
However, the term "shearing" by itself refers to a specific cutting process that produces straight line cuts to separate a piece of sheet metal. Most commonly, shearing is used to cut a sheet parallel to an existing edge which is held square, but angled cuts can be made as well. For this reason, shearing is primarily used to cut sheet stock into smaller sizes in preparation for other processes. Shearing has the following capabilities:
How does shearing work?
As mentioned above, several cutting processes exist that utilize shearing force to cut sheet metal. However, the term "shearing" by itself refers to a specific cutting process that produces straight line cuts to separate a piece of sheet metal. Most commonly, shearing is used to cut a sheet parallel to an existing edge which is held square, but angled cuts can be made as well. For this reason, shearing is primarily used to cut sheet stock into smaller sizes in preparation for other processes. Shearing has the following capabilities: 1 Sheet thickness: 0.005-0.25 inches 2 Tolerance: ±0.1 inches (±0.005 inches feasible) 3 Surface finish: 250-1000 μin (125-2000 μin feasible)
What is punching metal?
Punching is a cutting process in which material is removed from a piece of sheet metal by applying a great enough shearing force. Punching is very similar to blanking except that the removed material, called the slug, is scrap and leaves behind the desired internal feature in the sheet, such as a hole or slot.
What is a blank cut?
Blanking. Blanking is a cutting process in which a piece of sheet metal is removed from a larger piece of stock by applying a great enough shearing force. In this process, the piece removed, called the blank, is not scrap but rather the desired part. Blanking can be used to cutout parts in almost any 2D shape, but is most commonly used ...
What is a piercing?
Piercing - The typical punching operation, in which a cylindrical punch pierces a hole into the sheet.
What is the clearance between a punch and die?
The hydraulic press drives the punch downward at high speed into the sheet. A small clearance, typically 10-20% of the material thickness, exists between the punch and die. When the punch impacts the sheet, the metal in this clearance quickly bends and then fractures.
What is notch punching?
Notching - Punching the edge of a sheet, forming a notch in the shape of a portion of the punch.
As adjectives the difference between cut and shear
is that cut is (participial adjective) having been cut while shear is ( sheer ).
As nouns the difference between cut and shear
is that cut is an opening resulting from cutting while shear is a cutting tool similar to scissors, but often larger.
As verbs the difference between cut and shear
is that cut is to perform an incision on, for example with a knife while shear is to cut, originally with a sword or other bladed weapon, now usually with shears, or as if using shears.
English
To cut, originally with a sword or other bladed weapon, now usually with shears, or as if using shears.
What is a mechanical cutting operation?
Any mechanical cutting operation such as blanking , piercing, shearing, slitting, or trimming reduces edge ductility. Each of these processes generate a zone of high work hardening and a reduced n-value. This work hardened zone can extend one-half metal thickness from the cut edge.
How many zones are there in a sheared steel edge?
A typical mechanically sheared steel edge has 4 main zones – rollover, burnish, fracture, and burr, as shown in Figure 1.
Why are AHSS grades less rollover?
Due to their progressively higher yield and tensile strengths, AHSS grades experience less rollover and smaller burrs. They tend to fracture with little rollover or burr. As such, detailed examination of the actual edge condition under various cutting conditions becomes more significant with AHSS as opposed characterizing edge quality by burr height alone. Examination of sheared edges produced under various trimming conditions, including microhardness testing to evaluate work hardening after cold working the sheared edge, provides insight on methods to improve cut edge formability. The ideal condition to combat local formability edge fractures for AHSS was to have a clearly defined burnish zone with a uniform transition to the fracture zone. The fracture zone should also be smooth with no voids, secondary shear or edge damage ( Figure 3).
What is AHSS steel?
Advanced High-Strength Steels (AHSS) exhibit high degrees of work hardening, resulting in improved forming capabilities compared to conventional HSLA steels. However, the same high work hardening creates higher strength and hardness in sheared or punched edges, leading to reduced edge ductility. Microstructural features in some AHSS grades contribute to their sheared edge performance. While laser cutting results in less edge damage than mechanical cutting methods, the heat from laser cutting produces a localized hear treatment, changing the strength and hardness at the edge. Achieving the best formability for chosen processing path requires generating a consistent good quality edge from the cutting operation.
How to increase sheared edge ductility?
Researchers have also found that it is possible to increase sheared edge ductility with optimized rake angles. Citation S-53 used 2-D Edge Tension Testing and the Half-Specimen Dome Test to qualify the effects of these rake angles, and determine the optimum settings. After preparing the trimmed edge with the targeted conditions, the samples were pulled in a tensile test or deformed using a hemispherical punch. The effect of the trimming conditions was seen in the measured elongation values and the strain at failure, respectively. The results are summarized in Figures 23-25. Some of the tes ts also evaluated milled, laser trimmed, and water jet cut samples. Shear Trim 1, 2, and 3 refer to the shear trim angle in degrees. The optimized shear condition also includes a 6-degree rake angle on both the upper and lower blades, as defined in Figure 22 .
What causes a steel burr to split?
These splits, however, are global formability related failures where the steel thins significantly at and around the split, independent of the local formability edge fractures associated with AHSS. A real-world example is shown in Figure 2, which presents a conventional BH210 steel grade liftgate with an excessive burr in the blank that led to global formability edge splitting in the draw die. The left image in Figure 2 highlights the burr on the underside of the top blank, with the remainder of the lift below it. The areas next to the split in the right image of Figure 2 shows the characteristic thinning associated with global formability failures.
How to reduce cutting force?
Putting shear angles into cutting tools is a well-known approach to reduce cutting forces. Modifying the cutting tool leads to other benefits in terms of edge ductility. Researchers studied the effects of a beveled punch instead of the traditional flat bottom punch. S-9, S-50, S-52 In these studies, the optimized bevel angle was between 3 and 6 degrees, the shear direction was parallel the rolling direction of the coil with a die clearance of 17%. With the optimal cutting parameters, the hole expansion ratio increased by 60% when compared to conventional flat punching process. As expected, a reduction in the maximum shearing force occurred – by more than 50% in certain conditions. Dropping the shearing force helps reduce the snap through reverse tonnage, leading to longer tool and press life.
What is shear cutting?
Shear cutting (also known as shear slitting) is the type of slitting that uses a combination of top and bottom knives. With the defined geometries introduced later in this article, it creates a force on the material separating it as it goes through the cut point. The main idea behind shear cutting is to replicate a pair ...
What is a top knife?
The top knives of a shafted set-up are mounted using a collar assembly. This contains a spring that maintains contact between the blades and bottom knives as much as possible, allowing for narrower slit widths.
Can crush cutting be performed by a web path?
Shear slitting as well as crush cutting can be performed either by a tangential or wrapped web path. Although it is more common and preferable to find tangential shear slitting, it is important to mention both web paths do exist.
