
Automatic Control Valve Products
- Automatic Flow Control Valve. A flow control valve regulates the flow or pressure of a fluid. ...
- Flow Control Valves. Control valves regulate the flow or pressure of a fluid. ...
- Pressure Control. Water Control valves can also work with hydraulic actuators (also known as hydraulic pilots). ...
What is the function of a flow control valve?
control valve: A valve which controls the flow rate or flow direction in a fluid system. The final control element, through which a fluid passes, that adjusts the flow passage as directed by a signal from a cont-
What is an automated control valve?
Automatic control valves are specialty valves fitted with actuators that can be controlled by temperature or flow sensors. The valves are controlled by electrical, hydraulic, or pneumatic signals from sensors. The valves can be set to open, closed, or anywhere in between to accurately control flow.
What are the types of control valve?
What are the Types of control Valves?
- Introduction. We have learned that valves are used to either shut-off flow, change the flow path or throttle flow, and that valves are characterized by how their flow coefficient varies ...
- Linear Motion. Linear motion valves have a closure member that moves with a linear motion to modify the rate of flow through the valve.
- Rotary Motion. ...
How to replace a gas control valve?
Gas control valve replacement is fairly simple on most water heater models. With the gas turned off, disconnect the lines connected to the gas control valve using an open faced or adjustable wrench. It is important to hold the water heater in place while applying torque to the connectors or you could cause additional damages.
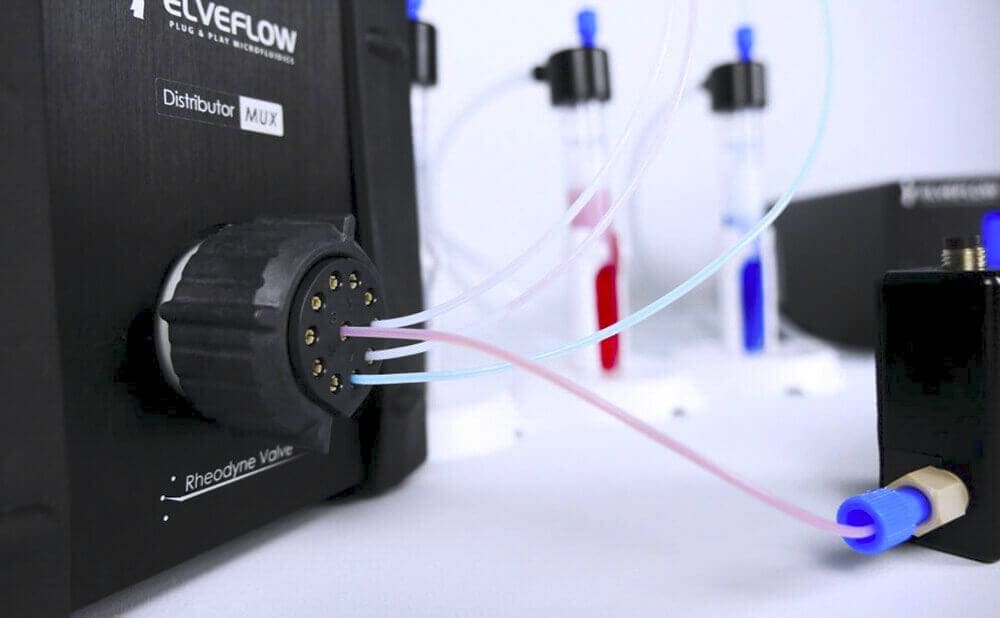
What is the difference between the manual control valve and the automatic control valve?
Manual actuation of a valve involves direct, physical contact with its hand wheel, lever or gear operator, while power automated actuation utilizes air pressure, electricity, or hydraulic pressure controlled by flow conditions, monitoring systems, or other means that does not involve physical contact with the valve.
How does a flow control valve work?
How do flow control valves work? Whilst there are different types of flow controller, they all work on a simple basic principle. The smaller a hole, or orifice, in a pipe, the lower the rate of flow of air at a given pressure (or more correctly differential pressure either side of the orifice).
When would you use a flow control valve?
Flow control valves are used to regulate the flow rate and pressure of liquids or gases through a pipeline. Flow control valves are essential for optimizing system performance, relying on a flow passage or port with a variable flow area.
What are the 3 types of automatic gas valves?
All of the most common types of automated valves fall into one of three main categories. They are linear, rotary, and self-actuated. There are a variety of valve types within each of these categories each having its own benefits. This training course is focused on rotary and linear actuated valves.
What is another name for a flow control valve?
These types of valves are also known as automatic control valves. The hydraulic actuators respond to changes of pressure or flow and will open/close the valve.
How do you adjust a flow control valve?
0:321:00Rain Bird Valves: Adjusting the Flow Control - YouTubeYouTubeStart of suggested clipEnd of suggested clipTo increase the flow turn the stem counterclockwise. In an emergency you can turn off the sprinklersMoreTo increase the flow turn the stem counterclockwise. In an emergency you can turn off the sprinklers from any particular valve by turning the valves flow control stem clockwise. Until it's hand tight.
How many types of flow control valves are there?
Ball valves feature a hollow ball that pivots 90 degrees around its axis to open or close the flow. Our ball valves range includes miniature ball valves, ball check valves, cryogenic ball valves, high pressure ball valves, rotary plug valves and swing out ball valves.
Which valve is best for flow control?
Globe valves are considered the industry standard for control valves because they are good at regulating flow, whereas ball valves are better for on/off control without pressure drop.
Does flow control valve affect pressure?
Flow Control Valves react to an increase of the parameters they control by throttling closed. This is a "progressive" process = increase in demand results in the valve reducing the flow progressively. The more the valve closes, the more the downstream pressure is reduced.
What are the two main types of valves?
Common functional designations and their common design types include: Isolation Valves: Ball, butterfly, diaphragm, gate, pinch, piston, and plug valves. Regulation Valves: Ball, butterfly, diaphragm, globe, needle, pinch, and plug valves.
What are the three types of control valves used in hydraulic systems?
The three most common types of hydraulic valves are: directional control valves, pressure control valves and flow control valves.
Which valve is used for gas flow?
Ball Valves Ball valves are designed to control the flow of high pressure liquids and gases with minimal pressure drop. They are quick to open and close, and have a tight seal with low torque.
Is a flow control valve a check valve?
A true flow control valve by most definitions is a needle valve with a reverse flow check valve. The check valve supplies free flow in one direction while restricting flow in the returning direction.
Where does mass flow controllers are useful?
Gas mass flow controllers used in customer applications Liquefied gas dosing using gas mass flow controllers with pump. Compact MEMS based instruments for gas dosing in bioreactor application. Mass flow controllers with evaporator system for graphene production. Aeration of beverages using gas flow controllers.
What is flow control in chemical engineering?
Flow control is a mechanism that regulates the flow or pressure of liquid. To be able to effectively manage flow control, flow control valves are used. The flow control of liquids is regulated as these respond to signals that are produced by independent devices like temperature gauges as well as flow meters.
What is the purpose of a load valve in a flowmeter?
To provide a lower pressure circuit in a hydraulic system. They are normally open valves that close to reduce pressure.
What is a Griswold flow limiting valve?
The Griswold Controls Automatic Flow Limiting Valve is used in many different applications, mostly in the HVAC industry to maintain balance in a HVAC System. The stainless steel flow limiting cartridge has a spring loaded cup that dynamically absorbs pressure fluctuations resulting from changing system conditions due to varying heating/cooling loads. These fluctuations in pressure, within a given pressure differential control range, do not change the flow through the valve, therefore the flow is controlled to within +/- 5% of the designed flow.
Do automatic flow limiters require balancing?
Automatic Flow Limiting Valves do not require any additional balancing as do Manual Balancing Valves, therefore they reduce labor costs from not having to balance and rebalance the valves.
Automatic control valves are used in commercial and industrial applications to control water flow or pressure. We offer automatic control valves that are used to ensure uninterrupted water service during emergencies, maintain a constant liquid level in tanks, automatically reduce a higher upstream water pressure to a constant downstream pressure, and for other purposes
Automatic control valves are used in commercial and industrial applications to control water flow or pressure.
Customer Support
Looking for more specific information? Need to contact us? Please visit our Customer Support page.
Why does flow rate vary?
As the flow rates tend to vary because of changing line pressures or downstream demand, the differential pressure across the orifice plate also tends to vary. When this occurs, the pilot valve repositions to compensate, and changes the throttled position of the main valve piston which controls and maintains the desired flow rate. ...
What is an altitude valve?
An altitude valve controls the level of a tank. The altitude valve will remain open while the tank is not full and it will close when the tanks reaches its maximum level. The opening and closing of the valve requires no external power source (electric, pneumatic, or man power), it is done automatically, hence its name.
Do hydraulic valves need external power?
The hydraulic actuators will respond to changes of pressure or flow and will open/close the valve. Automatic Control Valves do not require an external power source, meaning that the fluid pressure is enough to open and close the valve.
How does an Automatic Flow Limiting Valve Maintain Design Flow?
Griswold Controls designed the first balance valve in the market in 1960, years before the first manual balance valve was designed and manufactured. The all stainless steel flow limiting cartridge is a standard in the industry because of its simply elegant design.
Why do engineers still use manual balance valves?
While the industry accepts that pressure changes cause flow changes which then causes heat transfer changes, many engineers still accept manual balance valves because the INITIAL unit cost is less than automatic or pressure independent valves.
What is the elimination of the manual partner balancing valves on the mains, risers and branches?
The elimination of the manual partner balancing valves on the mains, risers and branches in turn eliminates the head loss through them. Hence, the system head loss is reduced which lowers the pump head requirements.
How to measure pressure drop on PI valve?
The only labor required is for flow verification. The pressure drop across each valve is measured by using the ports provided on the valve body. As long as the PSID is within the control range listed on the valve tag, the flow, which is also listed on the tag, will be within plus/minus 5%.
How many valves are needed for a manual balancing system?
The manual system, shown above, requires a total of 27 valves whereas the automatic system, on the right, requires only 18 because it does not require the “partner balancing valves” (shown in red) on the risers and the branches.
How far does the head loss go through the manual balancing valve?
Please note, for design flow at design head, the head loss through the manual balancing valve is the same as that through an automatic flow control valve (86 feet).
How many balances per valve?
Each time a valve in the system is adjusted, the flow through the other valves will change including those previously set because of the pressure change. Hence, the previously set valves must be reset, which in turn affects the flow through the other valves… and so on. In a large system, a minimum of three balances per valve is generally recommended by ASHRAE and NEBB.
Why do we need needle valves?
Needle valves can provide positive shutoff in order to allow gauges and other measurement instruments to be installed or removed safely. That’s also why needle valves may be used in a range of industries, from petrochemicals to biofuels. It is the needle valve’s finely-threaded valve stem that gives it a significant mechanical advantage by allowing operators to seal it using only minimal force. One disadvantage of needle valves, however, is that the visual inspection alone is not enough to determine whether a needle valve is open or closed.
What is gate valve?
Gate valves are general service valves primarily used for on/off, non-throttling service. Specifically, gate valves are used in applications requiring a straight-line flow of fluid with minimum restriction is desired. Gate valves operate when the user rotates the stem in a clockwise to close (CTC) motion or a clockwise to open (CTO) motion. The gate moves up or down on the threaded step when an operator moves the stem, which is why it is a multi-turn valve; the valve must turn several times for it to go from open to closed, and it is the slow operation that prevents water hammer effects. Engineers also utilize gate valves when minimum pressure loss and a free bore are required. Typical gate valves have no obstruction in the flow path, which results in a minimal loss of pressure.
What is a diaphragm valve?
Diaphragm Valves. Diaphragm valves are characterized by a flexible disc that contacts a seat at the top of the valve body and forms a seal. The diaphragm is flexible and pressure-responsive; it transmits force to open, close, or control a valve.
Why use flow control valve?
System operators can use a flow control valve to rapidly depressurize a serviceable hose and change fittings quickly. They are also used in many consumer applications such as showers, faucets, and lawn watering systems to easily reduce the amount of water consumed without impacting the overall system performance. Flow control valves are also known for their reliability and typically have a long operating lifetime as they are not prone to clogging due to their design.
How many types of flow control valves are there?
While the five types of flow control valves described above are some of the most commonly used valve types, there are other types of flow control valves with features that make them suitable for different applications. Here’s a look at a few other types of flow control valves.
What is butterfly valve?
Butterfly valve. A butterfly valve is operated by rotating a disk within the flow area and, due to this design, it does not have linear flow characteristics. This makes these valves less precise than the more common flow control valve types above.
What are the advantages and disadvantages of using a diaphragm valve?
There are many advantages to using diaphragm valves: they are extremely clean, feature a leak-proof seal, have a tight shut-off, are easy to maintain, and reduce leakage to the environment. Diaphragm valves also may be repaired without interrupting a pipeline. On the other hand, the disadvantages of using diaphragm valves include only being able to use them in moderate temperatures of -60 to 450 degrees Fahrenheit and in moderate pressures of approximately 300psi. Diaphragm valves cannot be used in multi-turn operations and do not have industry standard face-to-face dimensions. Also, the body of a diaphragm valve must be made of corrosive-resistant materials.
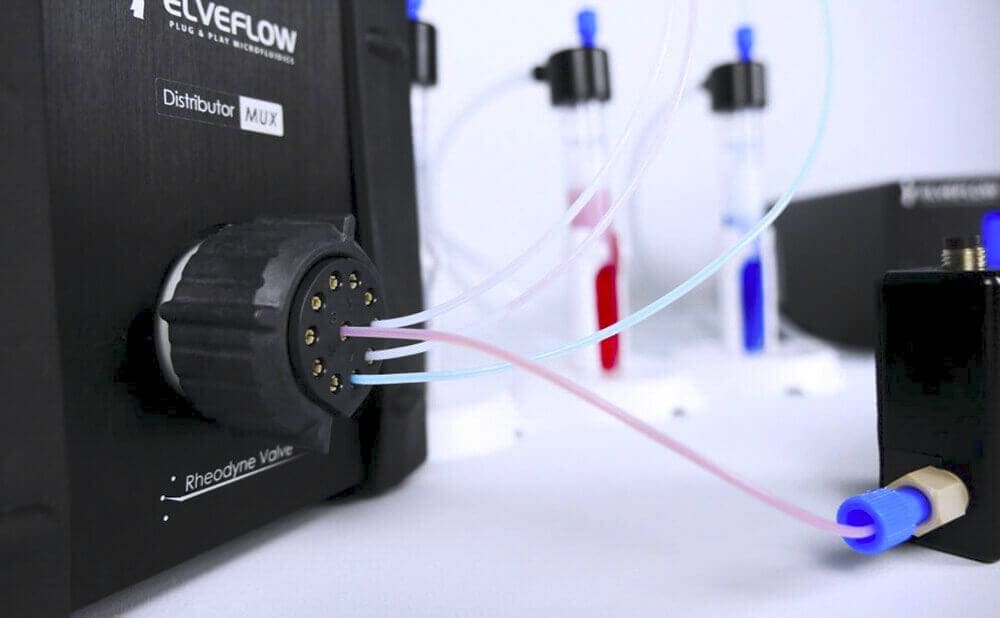