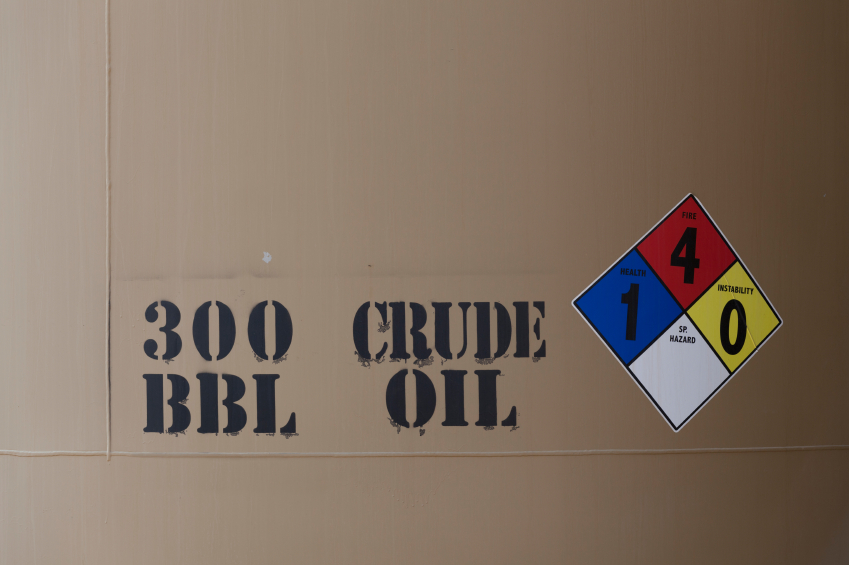
What are the key components of an EHS management system?
These Standards provide the framework for EHS risk management, incorporating many key elements to successful EHS management such as regulatory compliance, risk assessment, communication, self audit, and senior leadership engagement.
What is the meaning of EHS?
Environment, Health, and SafetyEHS stands for Environment, Health, and Safety. It's a general term used to refer to laws, rules, regulations, professions, programs, and workplace efforts to protect the health and safety of employees and the public as well as the environment from hazards associated with the workplace.
What is EHS and QMS?
Nowadays, it's rare to find an organization that hasn't implemented any software solution to provide some sort of support. And the most common software solutions in many organizations are Quality Management Systems (QMS) and Environmental Health and Safety (EHS) systems.
What are the benefits of EHS?
Below are a few benefits of applying EHS systems in your manufacturing company: Reduce compliance costs & risks. ... Reduce Waste and Improve Efficiency. ... Improve Environmental Performance. ... Streamline audits & inspections. ... Improve Safety Performance.
What are examples of environmental safety?
The following are some examples of general environmental controls for facilities:Safety color codes for pipes and cans.Marking hazards.Provision of safety signs (Danger,Caution, and Instruction signs) Lockout/Tag-out (LO/TO)Provision of sanitation facilities.
What is the ISO 14001 standard?
ISO 14001 is an internationally agreed standard that sets out the requirements for an environmental management system. It helps organizations improve their environmental performance through more efficient use of resources and reduction of waste, gaining a competitive advantage and the trust of stakeholders.
What is EHS database?
Environmental, health, and safety (EHS) software is a technology companies use to manage all their regulatory compliance, enterprise risk, and corporate sustainability data and activities. An EHS software system helps companies save time, reduce risk, and prevent unwanted events.
What is ESG and EHS?
One trend on the rise is environmental, social, and governance (ESG) reporting, and it is increasingly a business requirement. Your environment, health, and safety (EHS) teams are in the perfect position to support organizational ESG efforts.
What does EHS stand for in business?
Environment, Health, and SafetyEHS is an acronym for Environment, Health, and Safety. You also might also see it spelled as “SHE” or “HSE.” Ultimately, EHS is a system of processes, plans, standards, laws, and regulations that aim to protect the safety of the environment, workers, and the general public.
Is EHS a good career?
CareerBuilder has identified the “safety and health engineer” position as one of the seven fastest-growing jobs that pays about $75,000 a year – more evidence that EHS jobs are an in-demand and wise career choice.
How does EHS management software help?
Using EHS management software can help you keep track of changes and make fully informed decisions. Using information management software has benefits that can empower you to track EHS challenges and improve your performance. The main EHS management system benefits include:
Why Is EHS Management Important?
EHS management system protocols are important because they prevent a significant number of illnesses, injuries, and environmental hazards. Workplaces have come a long way since the horrific tragedies that used to occur fairly regularly, like the Triangle Shirtwaist Fire, which killed 146 workers and prompted greater attention to and regulation of workplace safety.
What Does an EHS Manager Do?
Overall, the EHS manager is there to identify, reduce, and control risks and hazards. Some of the tasks they may be responsible for include:
What are the areas of EHS?
These are some of the areas EHS processes strive to protect and make safer. Environment: This refers to the world around you and concerns preventing things like chemical spills and air pollution. Health: This usually refers to things that can make people ill, like pathogens, radiation, and exposure to noise or bad smells.
What is the future of EHS?
The Future of EHS Management. EHS constantly evolves as the world becomes more aware of environmental concerns, new technology develops, and new protection measures are needed. The focus of EHS professionals is to keep up with the changing times and adapt to use technology to the best of their abilities.
How has EHS saved lives?
Put simply, EHS management has saved lives. As consumer goods production has expanded exponentially, so has consumption of energy and dangers to the environment and human residences. EHS has helped protect the planet from these threats while still allowing businesses to thrive.
What does EHS stand for?
EHS stands for “environment, health, and safety,” and for many companies, a crucial part of their processes is EHS management, meaning the codification and practice of procedures aimed at ensuring the safety of workers and their surroundings. Technology has transformed the way EHS is managed: It’s allowed management systems to become more finely ...
What is EHS management?
EHS management refers to the implementation of procedures focused on ensuring and improving the safety of workers and their surroundings. These processes play a significant role in achieving and maintaining ...
How can CQ EHS Management Software help companies?
It is flexible and modular, enabling businesses to deploy only the features that needed. It integrates with existing enterprise systems for seamless integration of EHS with operations. ComplianceQuest’s EHS management solution enables seamless management of an organization’s entire environment and safety program with a range of intuitively integrated tools and applications. CQ’s EHS management software allows companies to prioritize health and safety programs based on risk analysis and providing relevant and timely data.
What are the key features of ComplianceQuest EHS system?
The key features of the ComplianceQuest EHS System include: Safety Event Reporting: EHS systems promote a safety culture to control risks and hazards at the workplace by ensuring workers have easy access to report injuries, accidents or near misses that could affect safety on the worksite.
What are the benefits of automating EHS?
The benefits of automating the EHS processes include: Employee well-being and safety as a culture. Sustainability and brand loyalty. Productivity and transparency gains.
What is worksite inspection?
Worksite Inspections: Define schedules, checklists, and assess the type and level of safe activity for all or specific locations. Keep the health and safety inspections seamless, consistent, timely, and mobile on any device. CQ’s EHS management system allows managers to assign actions to unwanted findings – all within one record for easy tracking and trend analysis.
What is Compliancequest EHS?
ComplianceQuest EHS System is a part of its enterprise-wide quality management system, thereby integrating all the processes seamlessly. ComplianceQuest EHS System enables automation of workflows and establishing a culture of safety and sustainability while meeting organizational goals. The key features of the ComplianceQuest EHS System include:
Does OSHA mandate EHS?
To overcome these challenges, OSHA mandated EHS management programs. Over the years, OSHA has conducted many studies that show the many needs of EHS management programs. EHS has
What is EHS management system?
A highly collaborative effort that draws on the leadership and expertise of faculty, researchers, students, administrators, and staff, the EHS Management System shapes how all members of the MIT community view their environmental, health, and safety responsibilities; carry out MIT’s comprehensive and integrated environmental commitment in their day-to-day activities; and assess MIT’s performance against our goals.
What is EHS policy?
The EHS Policy is provided to students, faculty, researchers, and staff during many orientation and training opportunities. The EHS Policy is reviewed and modifications to the policy are considered as needed or as part of the overall EHS-MS management review process as described in Section 6.1, Inspections.
What is EHS training?
The EHS Training Needs (certificate login required) is a web-based tool used by MIT to identify individuals engaged in regulated activities, to assess the types and levels of EHS risks they may encounter and regulations that apply to their activities, and to create and track a customized training program for each individual. The assessment creates and tracks individual training programs based on different criteria such as departmental or EHS activity or job title. Twice a year, EHS Representatives in laboratories or other work areas are notified to review the list of trainees affiliated with the lab or work area and to update the list using the online Training Reconciliation. If a trainee is added, the system sends that person an email and a link to update their activity selection.
What is EHO in EHS?
EHO represents the administration of the EHS Management System, including the EHS Office, to Institute leadership for matters of policy, budget, organization, and major process and technology programs.
Why is communication important in EHS?
MIT has developed comprehensive communication mechanisms within the EHS-MS to ensure that the information needed to implement MIT’s EHS Policy reaches the MIT community. The ultimate objective of these communication mechanisms is to promote the full integration of the MIT EHS Policy and EHS Management System into research and work processes to ensure compliance and promote achievement of MIT’s high EHS standards. Clear and effective channels for communication are essential to ensure awareness and understanding of EHS regulatory requirements , the components and operation of the EHS-MS, and of the supplemental programs, plans, and procedures established at MIT to address EHS issues.
Why are EHS records kept?
Appropriate records are maintained to ensure compliance with EHS regulatory requirements, MIT’s high EHS standards, and good recordkeeping practices. Records may be maintained as either paper files or electronic files. The EHS Office recognizes that it is good business practice to retain records in a consistent, systematic and reliable manner so that they can be retrieved promptly when required for legal, regulatory or operational reasons. The EHS Office has determined the types of records that must be maintained, and the time period over which the records must be available. The EHS Records Management Program has been developed to provide management direction and support throughout the records’ lifecycles. The objectives and details of this program are covered in the EHS Records Retention Standard Operating Procedure, and Records Retention Schedule.
Why is EHS training archived?
Trainee data generated by the EHS training program is routinely archived to ensure a robust and accurate data set. The periodicity of archiving is determined by the EHS Office to foster accurate information and, to the extent feasible, takes into consideration the annual academic year cycles for students and staff appointments and the need for regular archiving of inactive students, staff, and employees from the system. EHS training records are archived according to regulatory requirements or MIT determined best practice.
What Is EHS Software?
There are a large number of software applications that can be used as part of a company's EHS management program. These can include software applications that:
What Does an EHS Manager Do?
An EHS manager works at a company to identify, remove, reduce, and otherwise control hazards and risks.
Why Is EHS Important?
The primary benefit of EHS, and workplace EHS programs, is the obvious one: preventing incidents such as injuries, illnesses, and harmful environmental releases.
What Is an Occupational EHS Program?
Organizations try to manage risks related to EHS hazards through EHS programs at the workplace. These programs attempt to identify, assess, and control hazards at work as well as train workers about the hazards and how to work in a safe and health manner, protecting their safety and health, the safety and health of others in the workplace, and the safety, health, and environmental conditions in their larger community.
Why are EHS programs important?
Because these hazards are real, EHS programs are necessary and provide real benefits. For example, this OSHA website on safety and health management programs provides a lot of case studies demonstrating these benefits. In addition, EHS programs at work also show employees that companies care about their well-being.
What is occupational safety?
It's a general term used to refer to laws, rules, regulations, professions, programs, and workplace efforts to protect the health and safety of employees and the public as well as the environment from hazards associated with the workplace. You can also think of it as what makes up the profession of occupational safety and health professionals ...
What are the responsibilities of an EHS manager?
The responsibilities of an EHS manager are many, and may include: Running the safety and health management program. Performing industrial hygiene activities or working with industrial hygienists. Performing job hazard analyses. Performing incident investigations.
What is EHS strategy?
We develop and review EHS strategic plans to address resource requirements to meet regulatory requirements, capital plans and sustainability goals. Global EHS & Sustainability and business management provide the financial and human resources to maintain compliance, support programs, drive innovative leadership initiatives, review capital investments, and maintain and improve staff competencies to carry out their environment, health and safety responsibilities.
What is EHS training?
EHS training and awareness programs are provided to address the policy, goals, technical and professional subject matter, and the importance of complying with EHS regulatory and company requirements.
What is the role of EHS audit?
The EHS audit function, within the Global Environmental, Health, Safety and Sustainability Department, has the responsibility to plan and conduct the audits, train and select team auditors, report audit results to management and monitor action plans through closure.
How to maintain quality assurance of EHS audit process?
One method of maintaining a system for quality assurance of our EHS Audit process is to periodically secure the services of an independent third party EHS audit firm to conduct an audit of the BMS Audit Program. The objective of this review is to determine if internal BMS EHS audit systems are functioning effectively to maintain and continually improve EHS performance, and verify that the EHS Audit Program is operating in conformance with established procedures and selected external consensus standards. A copy of the most recent audit attestation letter can be found on our Verification Statements page.
How often are EHS audits conducted?
The frequency of audits range from 18 to 24 months for manufacturing facilities, 24 to 36 months for Research and Development and finishing and packaging facilities, and 36 to 48 months for offices, warehouses and distribution facilities. Corrective and Preventive Action (CAPA) plans are developed and implemented to close open EHS Audit Findings. The CAPAs are tracked by an internal automated system and the Lead Evaluator of the audit until closure.
What is the Bristol Myers Squibb EHS management system?
Our Environment, Health and Safety management system builds on the foundation of Our Commitment and our Principles of Integrity: Standards of Business Conduct & Ethics. It provides the structure for implementing proactive sustainable business practices associated with our products and operations. Its threefold purpose is to ensure compliance with internal and external requirements, drive continuous improvement, and support the company's strategy to be a global biopharmaceutical company helping patients prevail in their fight against serious disease. The Bristol Myers Squibb EHS Management System encompasses the following elements:
How does webinar technology help with EHS?
By using webinar technology, staff can actively participate in the training sessions, ask questions and discuss topics. The webinars eliminate the need to travel while providing staff worldwide with access to EHS training on a regular basis. Through a formal survey, 100 percent of responders indicated the sessions met or exceeded their expectations and were applicable or useful to their jobs.
1. Develop a Meaningful EHS Policy
Top management should craft a succinct list of objectives that outline the organization’s commitment to EHS. It should be aligned with the core principles of the company. A meaningful EHS policy only zooms in on an organization’s core values through the EHS lens, it doesn’t create new ones.
2. Plan and Integrate EHS into Daily Operations
Once an EHS policy is laid out, the next important step is to identify EHS risks and assess your current control capability. A good way to start would be to identify the legal requirements that need to be complied with and craft a review process for such documents.
3. Measure EHS Management System Performance
During implementation, there should be a mechanism to gather data on how the system operates in actual practice. This gives the most straightforward opportunities to identify and respond to areas needing corrective action.
4. Facilitate Continuous EHS Education and Training
It is important to promote a growth mindset throughout the entire organization. Employees must feel free to lodge suggestions and complaints with regards to existing protocols. Remember that you are building a management system, and you cannot build one without engaged employees.
5. Review EHS Outcomes
The management should review EHS policy regularly to ensure two things: compliance and relevance. This should not be a problem if steps 1 to 4 have been carefully executed. With clear goals, an implementation strategy, reliable measurement tools, and engaged employees, the management can easily have a bird’s-eye view of the EHS situation.
Conclusion
A good strategy in building an EHS management system that works is to seek a balance between rigidity and adaptability. Build standard protocols that prevent harm and build on the lessons once these protocols do not work out as planned.
