
7 Best Welders for Aluminum – Exceptional Speed and Precision! (Summer 2022)
- Editor’s Choice: Hobart Handler 210MVP. "A popular MIG welder that features 25-210A output, 30% duty cycle and can cut aluminum up to 3/8” thick.
- Premium Pick: Forney 220 ST PRO Welder.
- PrimeWeld TIG225X. "An excellent TIG/Stick welder that features 10 –225A output, 40% duty cycle and can cut aluminum up to 1/4” thick. 110/220 V. 10 ...
- Best for Beginners: AHP Alpha-TIG200X-2018. "A full-function AC/DC TIG welder that features 10 –200A output, 60% duty cycle and can cut aluminum up to ...
What is the best method to use for welding aluminum?
Weld the Aluminum
- Use the push technique when welding aluminum. ...
- Use hotter settings in terms of amperage and voltage. ...
- Pick welding wire that has a melting point similar to the base material that you’re working with. ...
- Choose a welding tip about 0.020 inches larger than the diameter of the filler metal that you’re going to use.
How to "weld" aluminum for beginners?
Learning to TIG aluminum
- Watch hand and torch placement. Beginning TIG welders often unintentionally produce a lot of scrap because they don’t practice basic hand placement and control before striking an arc ...
- Coordinate movement and filler deposition. Next, you should work on the flow of your hand and torch movement without striking an arc. ...
- Practice puddle control. ...
How to MIG weld aluminum for the first time?
Tips for MIG welding aluminum without a spool gun
- Try a long stick-out of ¾” to save contact tips. ...
- Keep your electrode trimmed. ...
- Preventing the wire from jabbing into the workpiece before the arc starts will avoid one cause of birdnesting. ...
- You’ll get better cleaning action and shielding gas coverage if you push the weld puddle.
Which welder is best for TIG welding aluminum?
Which Welder Is Best for TIG Welding Aluminum?
- AHP AlphaTIG 200X -All Rounder. New and Improvised AlphaTIG 203XI features Fully control LCD screen. ...
- Hobart EZ-TIG 165i -Best for Stainless Steel. Unlike the AHP AlphaTIG welder, this one isn’t versatile. ...
- Lotos TIG200 -Best Value. ...
- Everlast PowerTIG 250EX-Best for Thin Aluminum. ...
- Weldpro 200 GD. ...
- Lincoln Electric Square Wave TIG 200. ...
What can I use to weld aluminum?
Gas tungsten arc welding (GTAW), also known as tungsten inert gas (TIG) welding, is one of the most popular welding processes chosen for aluminum.
Is MIG or TIG better for welding aluminum?
You can use aluminum, stainless steel and mild steel. TIG welding is also compatible with these metals but works better with thinner gauge materials. Speed: TIG is a slower method but provides a higher level of detail. MIG is the faster method of welding, making it ideal for projects requiring higher production rates.
What is the strongest weld for aluminum?
Of the filler metals for aluminum, the 5356 produces the strongest welds. The 5356 welding rod has a longitudinal shear strength of 17 Ksi versus the 11.5 Ksi of the 4043.
Do you need a special welder to weld aluminum?
The right Welder is essential if you're going to work with aluminum. For aluminum, a TIG – tungsten inert gas – welding machine is a better choice than a MIG machine. While MIG machines can be used, TIG machines are preferred by most professionals taking on complex aluminum welding tasks. Welding torch.
How many amps does it take to weld aluminum?
A common rule of thumb is that you will need 1 amp for every 0.001 inches of metal you are going to weld when other variables are constant. That means if you want to weld 1/8-inch aluminum, you will need around 125 amps when other factors are constant.
Can you mig weld aluminum without gas?
Yes, aluminum can be welded without gas in a vacuum chamber. However, welding aluminum gasless will expose the metal to the oxygen air circulating around your workspace and will make for a less secure weld.
Do you need AC or DC to weld aluminum?
AC Welding Whenever aluminium is welded using the tungsten inert gas welding process, alternating current is used.
Why do aluminum welds crack?
Stress cracking can occur when an aluminum weld cools and excessive shrinkage stresses are present during solidification. This could be due to a concave bead profile, a too slow travel speed, a highly restrained joint, or depression in the end of the weld (crater crack).
Is MIG or stick welding stronger?
When done correctly, stick welding produces stronger joins than MIG welding.
Can you weld aluminum with a regular MIG gun?
The answer is yes and no, depending on the user's preference, you do not necessarily need a spool gun to weld aluminum. Depending on the application, some have found success in taking a ten- or twelve-foot MIG gun and running a Teflon liner through it, then calling it a day.
How do you weld aluminum for beginners?
0:497:52How to Tig Weld Aluminum for Beginners - YouTubeYouTubeStart of suggested clipEnd of suggested clipBut today we're going to weld AC in order to weld AC. And aluminum we need to put a ball on the endMoreBut today we're going to weld AC in order to weld AC. And aluminum we need to put a ball on the end of this tungsten. It's already pre ground to a point.
Can you weld aluminum with a regular stick welder?
Can I weld aluminum with a stick welder? Yes, it is possible to weld aluminum with a stick welder. Since it can be messy, the best methods are: AC TIG.
Can you use a MIG welder on aluminum?
Aluminum is a tricky metal to weld with a MIG welder because it takes more heat than mild steel (Usually in the range of 21 to 24 volts). The minimum aluminum thickness you should attempt is roughly 14 ga. To 18 ga. Any thinner than that and you'll need a TIG welder.
Is TIG stronger than MIG?
Precision. TIG welding can achieve this level of precision because the operator has more control over the gun vs. MIG welding. Unlike the MIG gun, which contains both the electrode and filler metal in one system, TIG welding uses a non-consumable tungsten electrode to form the arc.
Can you weld aluminum with MIG and TIG?
6:089:19Welding Aluminum TIG vs MIG Spool Gun - YouTubeYouTubeStart of suggested clipEnd of suggested clipEverything is more sensitive gun angle you want to push. And not pull whereas with steel. You canMoreEverything is more sensitive gun angle you want to push. And not pull whereas with steel. You can push you can pull straight in there are subtle differences. But with with MIG welding aluminum.
Can you MIG weld aluminum without a spool gun?
The answer is yes and no, depending on the user's preference, you do not necessarily need a spool gun to weld aluminum. Depending on the application, some have found success in taking a ten- or twelve-foot MIG gun and running a Teflon liner through it, then calling it a day.
What is the best aluminum for welding?
5XXX and 6XXX series aluminum alloys are the best for welding overall. Remember that your project and application will ultimately determine which grade will work best.
Which series holds up best to welding?
The series that hold up best to welding are 5XXX and 6XXX. "Is 6061 aluminum weldable?" is one of the most frequent questions we get. We most often use 5050 or 6061 aluminum, so the answer is "Definitely." Those two metals are very common, so availability and price shouldn’t be an issue.
What is 3xxx aluminum?
3XXX series aluminums include manganese. They're malleable and easy to weld, and they often feature in heat-related applications (cookware; heat exchangers in vehicles and power plants). Their so-so strength precludes them from structural use.
What does it mean when you buy aluminum?
The grades are separated into series, beginning with 1XXX and ending with 7XXX. Generally, higher numbers mean a higher percentage of magnesium.
Why does aluminum crack when welding?
It behaves much differently -- usually fussier. Here are the problems that aluminum typically presents when welding: If the part has to be squared after welding, it can crack (due to heat distortion). It’s less malleable than steel. It’s easily affected by heat.
Is 4xxx alloy weldable?
4XXX alloys are highly weldable, but they're more often used as filler materials for other grades.
Is 2024 aluminum crack resistant?
While the 2024 alloy is very common and immensely strong, it’s extremely crack-sensitive.
What Welding is Best for Aluminum?
TIG (Tungsten Inert Gas) welding is the best method for welding aluminum. A TIG welder can provide more precise welds and is better suited for welding aluminum than other welders.
How Does Welding Aluminum Differ from Welding Steel?
Steel and aluminum have different chemical and physical properties such as melting point, coefficient of thermal expansion, elastic modulus, etc. In aluminum welding, the definition of the consumable to be used differs from how it is done for the steel and is even simpler.
Can All Welders Weld Aluminum H3?
For aluminum to be versatile and have a wide range of applications and characteristics, it needs different compositions. Several aluminum alloys meet various needs, such as greater hardness or flexibility. Here are some different configurations:
What is the best alloy for welding?
The Best Aluminum Alloys For Welding. When it comes to welding, choosing the right material is one of the most important considerations for a manufacturer. This is especially true when you are working with aluminum. With so many alloys to chose from, and with so much versatility and adaptability, it’s critical that you do your research and find ...
What is the closest alloy to aluminum?
This class of alloy is the closest to pure aluminum. They are commonly employed to conduct electrical currents and for corrosion resistance. 1XXX alloys are easily weldable and are generally used with 1100 filler metal. 2XXX alloys. The 2XXX alloys are very strong. They are commonly used in the aerospace industry and come in sheets or plates.
Why use aluminum alloys?
Because of their lower cost and greater versatility , aluminum alloys offers many advantages over other materials when used in the production process. However, choosing the right alloy is of critical importance. Whether you are specifically looking for weldable materials, or desire the ability to quickly and easily repair materials down the line, knowing which aluminum alloys work best in welding applications will make your job easier.
What is the 5000 series of alloys used for?
The 6000 series of alloys are the easiest to extrude, so in addition to welding applications, they will regularly be used in extruded shapes.
When welding aluminum, each alloy must be used with the proper welding wire.?
When welding aluminum, each alloy must be used with the proper welding wire. The properties of the wire must align with those of the particular alloy it is to be welded to. The welding wire must also possess a similar melting temperature to that of the base material in order to be effective. Considerations must be made, for instance, to match the magnesium concentration of the alloy with that of the filler alloy. The dynamic chemical makeup of the welding wire needs to be similar to the parent alloy to yield the most efficient and reduce welding deformation.
What temperature is treated aluminum?
On the other hand, heat treatable aluminum has been treated at 400° F. Naturally, during the welding process, the metal is heated to much higher temperatures than 400° F, meaning the alloy will lose some of its mechanical properties. If there is no post-welding treatment done after the weld, then the welded area will become as much as 40% weaker. ...
What is the difference between 7000 and 2000 alloys?
Because the 5000-series alloys are more easily welded, they are regularly used in structural applications, including bridges, ships, buildings, and vehicle bodies. The 6000 series of alloys are the easiest to extrude , so in addition to welding applications, they will regularly be used in extruded shapes.
What type of welding is used for aluminum?
Gas metal arc welding (GMAW), or metal inert gas (MIG) welding is another great choice for welding aluminum. Gas metal arc welding generally has higher deposition rates and faster travel speeds than GTAW. However, GMAW uses a mechanical wire feeding system. Because of this, a push-pull gun or spool gun may be needed so that aluminum wire feeding is possible. Also, it is important to not use 100% CO2 or 75% Argon/25% C02 shielding gas. Such gas is a viable choice for steel, but aluminum cannot handle the reactive C02 gas. Follow the filler metal manufacturer recommendations for shielding gas type.
Why Is Welding Aluminum Difficult?
One area of difficulty is filler metal . First, some aluminum alloys cannot be welded without filler materials. Alloys such as 6061 will undergo solidification cracking if welded without filler metal. Furthermore, the correct filler material must be selected. For instance, welding a 6061 alloy with a 6061 filler metal will result in weld failure. Instead, a 5356 or 4043 aluminum filler metal should be used when welding a 6061 base material. Another challenge with aluminum filler metal is feeding. If a mechanical wire feeding process is being used, special drive systems will most likely be needed. This is because aluminum has less column strength than steel, and will more than likely buckle and tangle if special wire drive systems, such as a push-pull gun, are not used. This is especially true for thinner aluminum filler metals (i.e. 0.8 mm or 1 mm diameter).
What is a tungsten arc welding process?
GTAW/TIG. One of the most popular welding processes for aluminum is gas tungsten arc welding (GTAW), otherwise known as tungsten inert gas (TIG) welding. GTAW is a great process for aluminum because it does not require mechanical wire feeding, which can create feedability issues.
Why is aluminum more thermally conductive than steel?
Aluminum also has a greater thermal conductivity than steel. The heat created when the welding process is initiated on aluminum is dispersed more rapidly than when welding an iron-based alloy. Therefore, full penetration may not occur until the weld has progressed quite far from the start. This is known as a cold start. Care must be taken so that cold starts do not occur when welding aluminum. Another result of the increased thermal conductivity is larger craters. By the time the end of the weld is reached, more heat is present than at the start. This heat disperses well in aluminum and can create a large crater. Aluminum is very susceptible to crater cracking, therefore, craters should be filled in so that failure does not occur at the end of a weld.
What is a cold start welding?
This is known as a cold start. Care must be taken so that cold starts do not occur when welding aluminum. Another result of the increased thermal conductivity is larger craters. By the time the end of the weld is reached, more heat is present than at the start.
Why is laser welding not good?
Electron beam welding generally does not have these problems because it does not use light as an energy medium and it is performed in a vacuum.
What is the process of removing aluminum oxide from a weld?
In order to avoid un-melted aluminum oxide particles in the weld, an oxide removal process, such as wire brushing or chemical cleaning, should be used prior to welding.
What is the best welding tool for aluminum?
You should always turn to the best when the weld has got to be right. The Lotos MIG175 is one of the best in the industry with all the features you would want for welding almost everything from aluminum to stainless steel and steel.
What is the best MIG welder for aluminum?
Hobart is a respectable brand with a fantastic line of MIG welders and this 210MVP is downright the best MIG welder for Aluminum you can buy with your money. It is popular among professional welders because of its easy-to-use design and versatility. It will allow you to achieve your most desired high-quality and neat welds.
Why is a tig welder AC?
AC capability is essential for aluminum welding because it works well on thinner materials. The DC (Direct Current) capability is highly suitable for welding thicker materials. Many high-power welding machines run on DC but it does not work well with aluminum because of its lower melting point and other special properties. Nearly all the TIG welders on our list have the AC/DC capability.
Why do welders use tig welding?
TIG welding is the most popular process because TIG welders do an excellent job of preventing burn through. Aluminum needs a lot of heat to be welded and can hold the heat for a long time leading to a burn-through. Also, TIG welding can be applied to both thick and thin aluminum plates/sheets.
What can you weld with a welder?
In fact, it comes fully stocked and ready to use. With it, you can weld various items including farm equipment, trailer frames, body panels, and gun/bow racks.
How much does a welder weigh?
The welder is a bit on the heavier side in its build coming in at 79 pounds. Moving it around might be tedious especially if you want to use it in different locations in your working area. You can solve this by getting a wheel cart that you can also use to store your gas cylinder and cables.
How much does a DV reverse rod welder weigh?
With this welder, you can weld pretty much anything including DV reverse rods. It is ultra-lightweight, coming in at 33 pounds but doesn’t feel flimsy at all. Plus, it has a secure carrying handle at the top of its case that adds to its easy portability.
What type of welder is used for aluminum?
1. Get a TIG (tungsten inert gas) welder with AC capability, not only DC. This is a type of welder that uses a tungsten electrode and an inert gas to shield the welding area. The precision achieved with this type of welder is crucial when working with aluminum, especially thin pieces.
What is welding aluminum?
Welding is the process of joining 2 metal components by melting them together. Welding any material is a challenging process, but welding lightweight metals like aluminum requires the utmost precision to ensure a strong bond. Knowing how to weld aluminum is a matter of assembling the right tools, exercising caution and patience, ...
How to weld aluminum with a torch?
Move the torch along the welding path. With the torch in proper position, practice moving your hand along the part of the aluminum that you will be welding. Practice with gloves on to simulate the amount of effort required. Make sure to move your entire hand, as getting in the habit of using just your fingers is very limiting.
How hot should aluminum be to weld?
Aim for a temperature between 300°F and 400°F (149-204°C).
What to wear when welding a tig?
Wear protective clothing. Wear a shirt with long sleeves made from a thick fabric. TIG welding produces a large amount of ultraviolet radiation. Because of this, you will get burns along your arms if you weld in short sleeves.
What angle should a weld be held at?
You will lead the weld with the filler rod, which should be held at about a 90° angle to the torch tip. The torch should always be pushed and not dragged. If the filler and the tip come into contact, your weld will be contaminated and lose structural integrity.
How to make a puddle in welding?
Create the puddle. Melt the workpiece until you create an adequately-sized puddle that’s no wider than double the diameter of your filler. Add just enough of the filler rod to fill in the joint, and then move to the next portion of the weld. Continue until the entire joint is welded properly.
What is the Best Method to use for Welding Aluminium?
The best method to weld aluminium and its alloys is dependent on the joining application of interest. The following points should be included for consideration before deciding on a welding process:
How can Aluminium be Welded?
There are numerous processes that can be used for welding aluminium and its alloys, which are detailed below:
What is a tig welding?
TIG welding can also be used for joining aluminium alloys. Owing to the high thermal conductivity of bulk aluminium, the TIG process enables sufficient generation of heat to keep the weld region hot enough to create a weld pool. TIG welding can be used to join thick and thin sections.
Why is aluminium weld so porosity?
Porosity in aluminium welds is caused by gas that becomes trapped in the weld pool when the metal freezes before all of the gas in the weld pool has a chance to escape.
How does linear friction welding work?
Linear friction welding (LFW). LFW works by oscillating one workpiece relative to another while under a large compressive force. The friction between the oscillating surfaces produces heat, causing the interface material to plasticise. The plasticised material is then expelled from the interface, causing the workpieces to shorten (burn-off) in the direction of the compressive force. During the burn-off the interface contaminants, such as oxides and foreign particles, which can affect the properties and possibly the service life of a weld, are expelled into the flash. Once free from contaminants, pure metal to metal contact occurs, resulting in a weld. The process is used for joining bulk aluminium components to produce near-net-shapes
Why are aluminium alloys used in transport?
Aluminium alloys are ubiquitous in transport applications because they provide engineering materials with good strength-to-weight ratios at reasonable cost. Further applications make use of the corrosion resistance and conductivity (both thermal and electrical) of some alloys. Although normally low strength, some of the more complex alloys can have mechanical properties equivalent to steels. Owing to the many benefits of aluminium alloys offered to industry, there is a need to identify best practices for joining them.
What is the melting point of aluminum?
Aluminiums have an oxide layer (aluminium oxide), which has a much higher melting point (2060 C°) than the parent aluminium alloy (660 C°). When welding, this can result in the oxide layer being included in the weld region, potentially causing lack of fusion defects and reducing the strength of the weld. Consequently, the workpieces should be ...
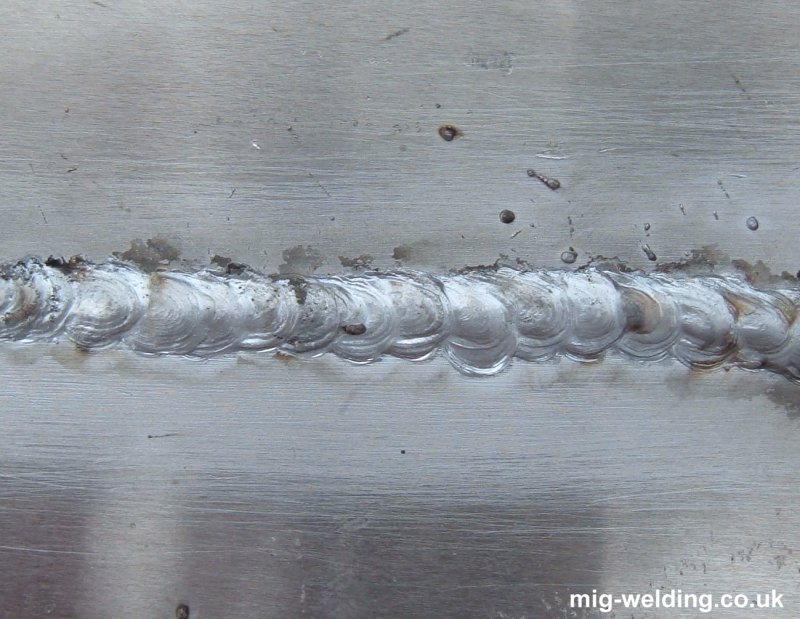