
What is a bond coat on concrete?
If the new concrete layer will be thicker than 1 or 2 inches, and both the overlay and the existing concrete surfaces are unmodified, a bond coat typically ensures adhesion between them. A bond coat is essentially a layer of “glue” for joining unmodified concrete to unmodified concrete.
What are the different applications of bond coat?
Vertical and horizontal applications for bond coats in residential construction range from self-leveling floors for patios and basements to walkways, stairways, and a variety of decorative concrete surfaces. Commercial applications include cementitious mortar applied to block walls, bridge deck overlays, and repair patches on bridge pilings.
How long do bond coatings last?
When bond coats are properly selected and applied, and surfaces are properly cleaned and prepared, there is no reason they should not provide decades of reliable service. Acrylic- and other polymer-based bond coats make concrete to concrete adhesion much stronger and more durable when done correctly.
How does bond coating affect overlay concrete?
Whenever the new overlay concrete is placed over the bond coat, the moisture in the concrete causes the bond coat to redisperse, or become active, and create a strong bond between the two concrete surfaces.
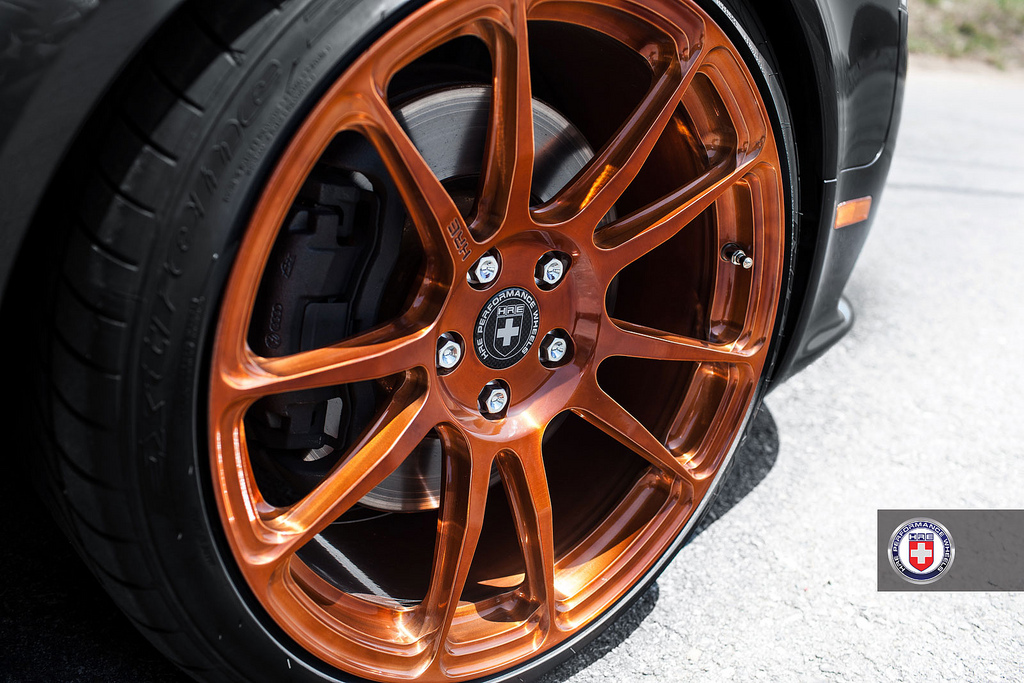
What is a bonding paint?
BEHR Bonding Primer is a modified-acrylic primer specifically designed to adhere to various challenging surfaces. This primer reduces the need to sand dense, glossy surfaces such as Kynar, PVC, vinyl, Formica, glass, tile, glazed brick, chalky paints, glossy finishes, fiberglass, and metals.
How do you use bonding paint?
3:064:24How to use the Bonding Agent with Milk Paint - YouTubeYouTubeStart of suggested clipEnd of suggested clipI'm just going to start brushing it on. And it just goes on like any normal paint there's no realMoreI'm just going to start brushing it on. And it just goes on like any normal paint there's no real dramatic difference here.
What is bond coat primer?
It is specially formulated to bond to a variety of challenging substrates and reduces the need for sanding dense and glossy surfaces – making it an ideal primer choice for painting tile, glass, Kynar®, and vinyl. This water-based formula has a quick dry time and can be used under Alkyd, Oil, and Water-based topcoats.
When should I use bonding primer?
When you have a difficult surface such as knotty or tannin-releasing wood, slick glass or metal, or even weathered paint on wood, you need a bonding primer. This primer bonds especially well to highly porous and otherwise poor surfaces because, physically, it lays on and stays on like a thick plastic blanket.
Can I paint on bonding coat?
If you have some multifinish at hand, I'd put a skim coat of that on top of the bonding first, but if you don't then go right ahead and paint the bond coat directly. It'll soak up your paint, so you should probably put on a couple of layers of diluted paint first mainly to seal it.
Do I need to scratch bonding coat?
Bonding does not need the wall underneath to be scratched or have a mechanical “key” and bonding agents, such as latex SBR adhesive are usually applied to the wall before the bonding plaster itself.
Do I need to PVA before bonding coat?
If the bonding cost has been gone over with a scarifier before it dried (like a hand held rake) to put little troughs in it for the finishing coat to adhere to then PVA is not required.
What is the difference between primer and bond?
Both primers and bonders chemically prepare the surface of the nail for better adhesion for the enhancement product. Primers will work to modify the pH of the nail bed, bonding with the keratin in the nail bed, while also leaving part of itself exposed above the nail bed to bond with the acrylic.
Do you put primer or bond first?
Bond Enhancer application should be applied as an extra step after natural nail prep and before application of primers, to dehydrate and balance the ph of the natural nail. This will help to maximize product adhesion.
How many coats of bonding primer should I use?
one coatThis stuff is THICK and can appear chunky in the can, so stir it thoroughly. It only takes one coat and can be painted over in one hour. Primer isn't meant to cover, but coat so you will see the surface below it.
How long should bonding primer dry before painting?
Primer takes between one and four hours to dry on average. However, the exact drying time depends on the primer type, room temperature, humidity, and the surface you're painting. Most manufacturers advise waiting at least 60 minutes before painting over the coat of primer.
Does bonding primer need two coats?
You will want to use 2-3 coats of primer to ensure there is a good bond between the new paint and the wall, and also to cover up any previous colors, especially if they are red, orange, or a strange outdated color. In short, you will typically need 2 coats of primer for most painting projects.
How long does bonding paint take to dry?
However, if you use a bonding primer, it will seal the surface, and bond to the paint when it is applied. Bonding primer will dry in 1-24 hours, depending on the environment.
How do you apply bonding liquid?
Application methods Brush, roller or spray application. Brush or roller preferred to ensure the product is worked well into the surface. Thinner Thinning not recommended. Ready for use after thorough stirring for brush and roller applications.
Does bonding primer need two coats?
You will want to use 2-3 coats of primer to ensure there is a good bond between the new paint and the wall, and also to cover up any previous colors, especially if they are red, orange, or a strange outdated color. In short, you will typically need 2 coats of primer for most painting projects.
How long does bonding take to set?
How Long Does Plaster Take To Dry: UK Guide (Answered)Plaster TypeDry (Setting) Time (25°C)Cure Time (25°C)Bonding plaster1.5 - 3 hours4 - 7 daysBrowning plaster1.5 - 2 hours4 - 7 daysHardwall plaster2 - 5 hours7 - 14 daysTough coat plaster2 hours4 - 7 days7 more rows
What is bond coat?
Bond coat is the most effective way to prevent delamination. Bond Coat material is an acrylic modified cement and sand mixture. It is made of one-part resin and one-part bonding cement is mixed and then rolled or sprayed onto the pool wall and floor. Bond coat is used to mechanically bond new pool coatings over existing plaster finishes.
Does Tile Concepts use bond coat?
To ensure that the plaster manufacturers’ warranty is not voided, Tile Concepts does not mix their own bond coat. Our team uses SGM Bond Kote™ which is a specially formulated two-part cementitious coating, designed to be used as an ideal substrate to mechanically bond pool plaster over existing plaster finishes. It minimizes delamination problems by offering superior bonding capability.
What is the interface between topcoat and bond-coat?
In plasma-sprayed TBCs a rough interface between bond-coat and topcoat is essential for the performance as the bonding mechanism of plasma-sprayed coatings is mechanical interlocking. On the other side, this wavy structure of the interface leads to off-plane stresses which can promote crack growth in this region (see Fig. 19.14 left).
What is MCrAlY bond coat?
MCrAlY (M states Ni, Co or Ni and Co) has been widely used as a bond coat below a ceramic top coat in TBC systems. A bond coat can increase adherence between the ceramic top coat and substrate. It can also protect superalloy substrates from chemical attacks such as oxidation. Also, bond coats provide a reservoir from which Al can diffuse to form a protective α-Al2 O 3 TGO while protecting cohesion with the TBC without reacting with it. At the operating temperature, a bond coat should work to optimize cooling air from the substrate without reacting and melting. It should be advised that the bond coat temperature cannot exceed 1150°C. Bond coats are generally produced from metal alloys that can support TGOs. To achieve good adherence and minimize interdiffusion with the underlying superalloy, rare earth elements such Y and Hf (<1 wt%) can be added to the bond coat. The rare earth elements prominently increase the creep resistance of alumina ceramics [2,17,25,26].
What is the stress level of a bond coat?
Subjected to high temperature coupled with fatigue load cycling , substrate and bond coat are under tension, σy, with the highest stress level being 150 MPa. At the edge of the heated area, the substrate and bond coat underwent shear stress over 10 MPa caused by non-uniform thermal loading. Therefore, slip bands formed in the bond coat at an angle of 45° from the interface. Cracks induced at these defects tend to propagate in the bond coat, since the slip bands will be blocked at the interface. Hence, the bond coat is internal oxidized.
What is the TGO layer on a ceramic top coat?
A TGO layer is formed on the bond coat. The TGO is a thin oxide layer (the thickness varies from 1 and 10 μ) that includes mainly Al 2 O 3 and other oxides such as minor Cr 2 O 3, NiO, and Ni (Al, Cr) 2 O 4. The high ratio of mixed oxides on the interface can cause early spalling of the TBC [17,25,27]. Although this layer protects the substrate against further oxidation, the growth of TGO throughout thermal cycling and long-term exposure cause cracking and spallation of the ceramic top coat because of the thermal expansion mismatch between the oxide and metallic substrate. TGO scales on bond coatings can be affected by the thickness rate, bond coat surface roughness, hold time, and top coating composition. Increasing the TGO scale on the bond coat leads to stress at the interface. If this existing stress passes the strain tolerance of the TBC, destructive delamination can occur at the interface of the ceramic top coat. There are two main stresses in the TGO: one is related to growth strain as new oxide occurs at the grain boundaries of the TGO; the other is mismatch stress with the substrate formed by differences in thermal expansion upon cooling [28,29].
What is flint coat?from zerocor.com
Flint-Coat is a high-temperature resin embedded with flint shards to create an extremely rough and hard surface for the OD of casing. It significantly enhances cement bond to casing as well as acting as a corrosion barrier. Flint-Coat is resistant to CO2, brine, and H2S, prevents gas migration, and provides cathodic protection.
Is Flint Coat durable?from zerocor.com
Communication and loss as a result of faulty tubing is preventable. By using Flint-Coat, you get reinforced, tough tubing that is durable enough to prevent and mitigate these problems.
What is the interface between topcoat and bond-coat?from sciencedirect.com
In plasma-sprayed TBCs a rough interface between bond-coat and topcoat is essential for the performance as the bonding mechanism of plasma-sprayed coatings is mechanical interlocking. On the other side, this wavy structure of the interface leads to off-plane stresses which can promote crack growth in this region (see Fig. 19.14 left).
What is MCrAlY bond coat?from sciencedirect.com
MCrAlY (M states Ni, Co or Ni and Co) has been widely used as a bond coat below a ceramic top coat in TBC systems. A bond coat can increase adherence between the ceramic top coat and substrate. It can also protect superalloy substrates from chemical attacks such as oxidation. Also, bond coats provide a reservoir from which Al can diffuse to form a protective α-Al2 O 3 TGO while protecting cohesion with the TBC without reacting with it. At the operating temperature, a bond coat should work to optimize cooling air from the substrate without reacting and melting. It should be advised that the bond coat temperature cannot exceed 1150°C. Bond coats are generally produced from metal alloys that can support TGOs. To achieve good adherence and minimize interdiffusion with the underlying superalloy, rare earth elements such Y and Hf (<1 wt%) can be added to the bond coat. The rare earth elements prominently increase the creep resistance of alumina ceramics [2,17,25,26].
What is the stress level of a bond coat?from sciencedirect.com
Subjected to high temperature coupled with fatigue load cycling , substrate and bond coat are under tension, σy, with the highest stress level being 150 MPa. At the edge of the heated area, the substrate and bond coat underwent shear stress over 10 MPa caused by non-uniform thermal loading. Therefore, slip bands formed in the bond coat at an angle of 45° from the interface. Cracks induced at these defects tend to propagate in the bond coat, since the slip bands will be blocked at the interface. Hence, the bond coat is internal oxidized.
What is the TGO layer on a ceramic top coat?from sciencedirect.com
A TGO layer is formed on the bond coat. The TGO is a thin oxide layer (the thickness varies from 1 and 10 μ) that includes mainly Al 2 O 3 and other oxides such as minor Cr 2 O 3, NiO, and Ni (Al, Cr) 2 O 4. The high ratio of mixed oxides on the interface can cause early spalling of the TBC [17,25,27]. Although this layer protects the substrate against further oxidation, the growth of TGO throughout thermal cycling and long-term exposure cause cracking and spallation of the ceramic top coat because of the thermal expansion mismatch between the oxide and metallic substrate. TGO scales on bond coatings can be affected by the thickness rate, bond coat surface roughness, hold time, and top coating composition. Increasing the TGO scale on the bond coat leads to stress at the interface. If this existing stress passes the strain tolerance of the TBC, destructive delamination can occur at the interface of the ceramic top coat. There are two main stresses in the TGO: one is related to growth strain as new oxide occurs at the grain boundaries of the TGO; the other is mismatch stress with the substrate formed by differences in thermal expansion upon cooling [28,29].
What is bond coat?
A bond coat is essentially a layer of “glue” for joining unmodified concrete to unmodified concrete.
What type of bond coat is used for portland cement?
Sometimes, Type II bond coats can be designed as an admixture with portland cement, water and sand to create a bonding slurry. In effect, these slurries are a form of modified mortar because the Type II bond coat adds polymer content to the mortar, giving it strong adhesion properties.
What is a C1059 type bond coat?
All bond coat products should be labeled clearly as ASTM C1059 Type I or Type II. ASTM C1059 Type I bond coats are redispersible, or sometimes called re-emulsifiable. Redispersible bond coats usually are based on PVA homopolymers, and can be applied by spray, brush, or roller. They create a film over the concrete surface ...
Why do contractors use redispersible bond coats?
Some contractors on large jobs prefer redispersible bond coats because they allow them the flexibility of applying the new unmodified concrete at any time. But if too much time elapses between applying the redispersible bond coat and placing the overlay, loose dirt or other contaminants may accumulate on the bond coat surface and compromise the adhesion. In this case, a second cleaning may be necessary.
What happens when you put a new overlay over a concrete bond?
Whenever the new overlay concrete is placed over the bond coat, the moisture in the concrete causes the bond coat to redisperse, or become active, and create a strong bond between the two concrete surfaces.
Why is my bond coat failing?
A: There are several possible reasons for failure when joining two concrete surfaces using a bond coat. The most common are inadequate surface preparation and using the wrong type of bond coat. Bond coats can be very versatile, but no single product is right for every job. So let’s start with a quick review of bond coats.
Can you short cut bond coat?
Never take a short cut or try a method the bond coat manufacturer does not recommend. When bond coats are properly selected and applied, and surfaces are properly cleaned and prepared, there is no reason they should not provide decades of reliable service. Acrylic- and other polymer-based bond coats make concrete to concrete adhesion much stronger ...
Why use bonding primer?
One of the major advantages of using a bonding primer is they save time and money, and if you can get the job done quicker, that’s a benefit. Especially for pros taking on a big job, who may not have the time to take down the gloss or sand the substrate. When it comes to best practices, though, bonding primer doesn’t take the place ...
How long after peanut butter can you topcoat?
“Although the topcoat may be applied anytime after the bonding primer coat is applied, we recommend you topcoat within a week after priming for best adhesion results,” ...
What is a highly engineered primer?
Highly engineered, it’s a coating that promotes adhesion to the surface or existing coating as well as the new coat that you want to apply. You’re going to pay more, nearly double in many cases, but that’s because they’re designed to do two things very well: stick, and be stuck to. “Most primers have adhesion characteristics,” says Frank Glowacki, ...
How to test if primer is holding?
If you want to confirm the primer is holding, Englis recommends conducting a test in an inconspicuous area: Do a small brushout, and then perform a tape test to make sure it’s adhering.
Can you use primer on hot coatings?
Depending on the product, bonding primers can also offer the advantage of accommodating lots of different coatings, including hot coatings with a high solvent content. Whereas an exothermic reaction may cause a major problem with a regular primer, the premium products can accept just about anything.
Can bonding primer be used over drywall?
Conversely, just because a bonding primer is highly engineered, it doesn’t mean it’s the right coating for every job. Using it over drywall, as an extreme example, would just be a waste of money. If you need a specific hide, odor blocking, or stain blocking, choose a primer with those characteristics.
Can you use primer as bonding primer?
When considering bonding primers, you need to be aware of two common misconceptions: 1. Many products with ‘primer’ in the name aren’t purpose-built or suitable for use as bonding primers. Really, they’re sealers— designed to seal a porous surface and make it even for paint—so don’t try to force them beyond their specs.
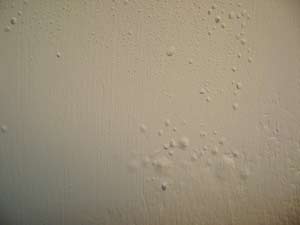