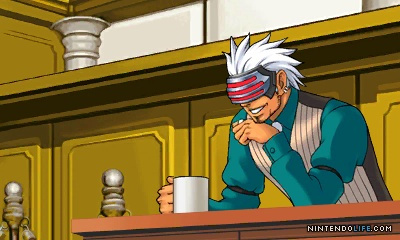
Process capability is defined as a statistical measure of the inherent process variability of a given characteristic. You can use a process-capability study to assess the ability of a process to meet specifications.
Full Answer
How do you determine process capability?
Steps for a Capability Analysis
- Generate I and mR charts. Start with the range chart and determine stability. ...
- Look at individuals chart. ...
- Generate a normal probability chart and test for normality If a distribution is close to normal, the normal probability plot will be close to a straight line. ...
- Assess process capability.
How do you calculate process capability?
- Compute the process average μ
- Subtract the process average from each measured data value (the X i values)
- Square each of the deviations computed in step 2.
- Add up all of the squared deviations computed in step 3.
- Divide the result of step 4 by the sample size.
How to calculate the process capability?
Process capability index (cpk) is used for calculating the ability of the process. The cpk formula is given as, Cpk = min [ (USL−mean)/3σ, (mean−LSL )/3σ] where, Cpk = Process capability index. mean = mean value. σ is a standard deviation.
How to explain and understand process capability?
Process capability is a measurement used to reflect how well a process functions within the normal limits of variability. These limits of variability are the upper and lower control limits. The goal is to have the process occur within the range of variability. When the process occurs outside the range, the process is ...
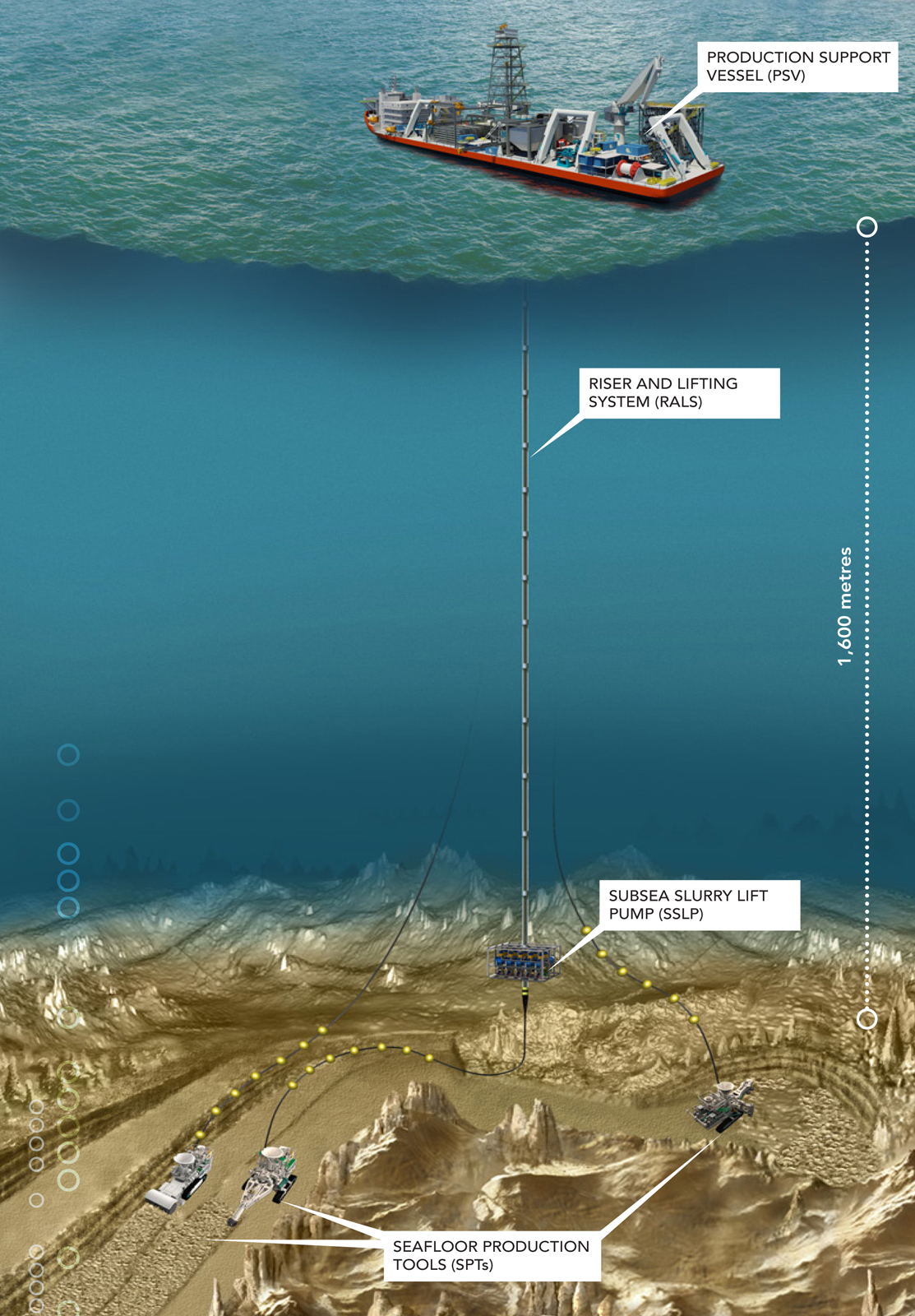
What means process capability?
Process capability is defined as a statistical measure of the inherent process variability of a given characteristic. You can use a process-capability study to assess the ability of a process to meet specifications.
What is process capability with example?
Process Capability Example 1: The ice cream that must be served in an ice cream parlor has to be between -15 degrees Celsius and -35 degrees Celsius. The process of refrigeration that keeps the temperature has a standard deviation (SD) of 2 degrees Celsius. And the mean value of this temperature is -25 degrees Celsius.
How do you measure capability of a process?
Measures of Process Capability (Indices) K= (Process Centre-Process Mean)/50%of USL-LSL and if we talk about process center; Process center = (USL+LSL)/2, and the process mean is the average or mean of the process data points.
Why is process capability important?
Why is process capability important? When the capability of a process is understood and documented, it can be used for measuring continual improvement using trends over time, prioritizing the order of process improvements to be made, and determining whether or not a process is capable of meeting customer requirements.
What is CP Cpk process capability?
Cp and Cpk, commonly referred to as process capability indices, are used to define the ability of a process to produce a product that meets requirements.
What is Cp and Cpk value?
The Cp and Cpk indices are the primary capability indices. Cp shows whether the distribution can potentially fit inside the specification, while Cpk shows whether the overall average is centrally located. If the overall average is in the center of the specification, the Cp and Cpk values will be the same.
What is process capability analysis?
An important technique used to determine how well a process meets a set of specification limits is called a process capability analysis. A capability analysis is based on a sample of data taken from a process and usually produces: 1. An estimate of the DPMO (defects per million opportunities).
What are two types of capability data?
The two main types of data for capability analysis are continuous data and attribute data. Minitab offers normal and nonnormal analyses for continuous data and binomial and Poisson analyses for attribute data.
How can process capability be improved?
How to Improve Process CapabilityExamine the process flowchart. Look for areas of duplicate work, extended cycle times or rework. ... Examine the control charts for outliers and variability. ... Prioritize improvements and create new control charts to examine the effects of the changes.
What is a good process capability?
A Cpk value less than 1.0 is considered poor and the process is not capable. A value between 1.0 and 1.33 is considered barely capable, and a value greater than 1.33 is considered capable. But, you should aim for a Cpk value of 2.00 or higher where possible.
What is a process capability chart?
Process Capability Chart – cp Chart The process capability chart contains a normal curve superimposed over a histogram of the data, followed by several statistics. A process is said to be capable if its output falls within the specifications virtually 100% of the time.
When we say process is capable?
What is a capable process? Some quality assurance experts define a capable process as one having and maintaining a CpK index of at least 1.33. This equates to a maximum defect rate of 63 ppm while others say a maximum of 3.4 ppm is the true capability process meaning of Six Sigma control.
What are the three major types of process capability studies?
To determine how our process is operating, we can calculate Cp (Process Capability), Cpk (Process Capability Index), or Pp (Preliminary Process Capability) and Ppk (Preliminary Process Capability Index), depending on the state of the process and the method of determining the standard deviation or sigma value.
What is process capability analysis used for?
Process capability analysis is a set of tools used to find out how well a given process meets a set of specification limits. In other words, it measures how well a process performs.
What is process capability chart?
The chart shows how consistent and predictable a process is at achieving the mean. X-bar charts measure variation between subgroups. They are often paired with either Standard Deviation (S) or Range (R) charts, which measure variation within subgroups.
What are two types of capability data?
The two main types of data for capability analysis are continuous data and attribute data. Minitab offers normal and nonnormal analyses for continuous data and binomial and Poisson analyses for attribute data.
What Is The Difference Between Cp, Cpk and Pp, PPK?
Cp and Cpk are called Process Capability. Pp and Ppk are called Process Performance. In both cases we want to try to verify if the process can meet...
Notes on Relating CP and Cpk
1. If Cp == Cpk, then the process is perfectly centered. If perfectly centered, Cp == Cpk. 2. Because Cpk accounts for centering (where Cp does not...
ASQ Six Sigma Black Belt Certification Process Capability Questions
Question: Data being used in the initial set-up of a process are assumed to have a normal distribution. If the nominal (target) is set at the cente...
ASQ Six Sigma Green Belt Certification Process Capability Questions
Question: When calculating the Cp index, what does the standard deviation represent in the formula Cp = (USL – LSL) / 6σ?(A) The tolerance interval...
What is process capability?
Process Capability (Cp) is a statistical measurement of a process’s ability to produce parts within specified limits on a consistent basis. To determine how our process is operating, we can calculate Cp (Process Capability), Cpk (Process Capability Index), or Pp (Preliminary Process Capability) and Ppk (Preliminary Process Capability Index), depending on the state of the process and the method of determining the standard deviation or sigma value. The Cp and Cpk calculations use sample deviation or deviation mean within rational subgroups. The Pp and Ppk calculations use standard deviation based on studied data (whole population). The Cp and Cpk indices are used to evaluate existing, established processes in statistical control. The Pp and Ppk indices are used to evaluate a new process or one that is not in statistical control.
How does process capability help manufacturing?
When we look at the bigger picture, process capability is more than just measuring Cp and Cpk values. Process capability is just one tool in the Statistical Process Control (SPC) toolbox. Implementing SPC involves collecting and analyzing data to understand the statistical performance of the process and identifying the causes of variation within. Important knowledge is obtained through focusing on the capability of process. Monitoring process capability allows the manufacturing process performance to be evaluated and adjusted as needed to assure products meet the design or customer’s requirements. When used effectively this information can reduce scrap, improve product quality and consistency and lower the cost to manufacture and the cost of poor quality.
What does CPK mean in engineering?
Cp tells you if your process is capable of making parts within specifications and Cpk tells you if your process is centered between the specification limits. When engineers are designing parts, they must consider the capability of the machine or process selected to produce the part.
What is Quality One?
Quality-One provides Knowledge, Guidance and Direction in Quality and Reliability activities, tailored to your unique wants, needs and desires. Let us help you Discover the Value of Process Capability Consulting, Process Capability Training or Process Capability Project Support.
Why is information gained important?
As previously mentioned the information gained is generally used to reduce waste and improve product quality. In addition, by knowing your process capabilities, the design team can work with manufacturing to improve product quality, and processes that are “not in control” may be targeted for improvement.
Can capability indices be calculated manually?
The capability indices can be calculated manually, although there are several software packages available that can complete the calculations and provide graphical data illustrating process capability. For the example in this section, we will utilize a popular statistical software package. For our example, we will utilize data from randomly collected measurements of a key characteristic of a machined part. To better represent the population values, the sample data must be randomly collected, preferably over time from a large production run. A few things to keep in mind:
What is process capability study?
Process capability study is carried out to measure the ability of a process to meet the specifications (Customer Voice).
What is stable process?
If product characteristics/specifications conform to engineering/customer requirements, then the process is considered as stable/capable and performing well as per set standards. A process is considered stable if there are only Common Causes of Variation present in the process.
What is process in engineering?
Process. The process is a set of interrelated activities that convert the inputs such as equipment, materials, people, methods, and environment into desirable output. The quality of the process is measured by the output of product quality characteristics.
What does Cp mean in a process?
Cp indicates the spread of variation present in a process.
What is a CPK in a process?
Cpk measures how close a process is performing compared to its specification limits and accounting for the natural variability of the process. Larger is better. The larger Cpk is, the less likely it is that any item will be outside the specification limits.
What is the CPK of a 3-2/3s function?
Now you end up with a Cpk of (3-2)/3s = 1/3s , but your Cp is still the same 1s as before. It is important to note that because Cpk uses the minimum function, it will always be equal to or smaller than the Cp for the same set of data.
Why do CPK and PPK converge?
The values for Cpk and Ppk will converge to almost the same value because sigma and the sample standard deviation will be identical ( use an F test to determine ).
What does CPK mean in a garage?
Cpk tells you the relationship between the size of the car, the size of the garage and how far away from the middle of the garage you parked the car.”.
Why do we take large samples from the process to account for variation?
Because there is not a lot of historical data we take large samples from the process to account for variation. Process Performance generally uses sample sigma in its calculation. In theory Cpk will always be greater than or equal to Ppk.
Is capability ration the inverse of Cp?
The capability ration is the inverse of Cp
What is process capability?
Process capability = Voice of the customer / Voice of the process. It is an expression of how well your process performs relative to the VOC. And it is a prediction of how well your process will meet customer requirements in the future.
How to determine if a process is stable?
Start with the range chart and determine stability. Are all points inside of the control limits? If yes, the process is stable and the analysis can move forward. If no, the process is unstable and this must be addressed before moving on.
What is CE in a process?
Consider CE as customer expectation. The customer expects the car to fit inside the garage and that the car will be reasonably centered in the garage. The customer of your process has similar expectations. For a process:
What does the car size mean in a process?
The car size represents the process limits . Figure 1: Cp. If the car is smaller than the garage, it means Cp > 1; the car will fit inside the garage. When you find that your data (car) is smaller than the specification limits (garage), your process is capable.
How many independent data values are needed for a capability index?
Most capability index estimates are valid only if the sample size used is “large enough,” which is generally thought to be about 30 or more independent data values.
What is process capability study?
A process capability study uses data from an initial run of parts to predict whether a manufacturing process can repeatably produce parts that meet specifications. Think of it as being similar to a forecast.
Why do customers need a process capability study?
They will do this to ensure that your manufacturing processes are capable of consistently producing good parts.
What does Cp mean in a process?
Cp measures whether the process spread is narrower than the specification width
What is process behavior?
Process behavior - both short-term and long-term - is characterized by the average and the standard deviation. A process will be considered stable when it's average and standard deviation are constant over time.
What is ensure traceability?
Ensure Traceability: Make sure all measurements are traceable back to Man (Operator), Machine (Operation), Method, Material, Measurement System, and Environmental Conditions (5Ms, 1E) to enable process improvement. Record Unit Number or Serial Number for each part.
How to calculate process capability?
One way to calculate Process Capability is through number of defects per opportunity. This is usually used for discrete data and in manufacturing is usually acceptable number of 3.4 Defects Per Million Opportunities (DPMO)
What is process capability analysis?
Process capability analysis is the determining if a process can meet specification.
What Can Process Capability and Process Performance Tell Us?
Process Capability Analysis tells us how well a process meets a set of specification limits, based on a sample of data taken from a process. It can be used to establish baseline for the process and measure the future state performance of the process for comparison.
What does "process capable" mean?
A process that is capable indicates the car (process) is skinnier than the garage you’re trying to park it in (the specification width). If the car is simply much bigger than the garage, it is not enough to be capable of fitting within the specification limits and thus is not capable. See how to calculate Cp. See how to calculate Pp.
What is Cp in statistics?
Cp for processes that are under statistical control and Pp for new processes. A good analogy is parking a car in a garage. If the car is bigger than the garage, it will not fit within the specification limits and thus is not capable – this case is clear. What about a case when our car is skinnier than the garage you’re trying to park it in (the specification width)? Can we consider our parking process as a capable one? It depends on our specification and the width of the car. Are we satisfied with the probability of 99% that we will park our car, without hitting the wall? This mean that one in a hundred attempts to park our car will hit the wall of the garage!
When to use Cp and Pp?
Both Cp and Pp are a monitoring indices for the spread of your process compared to the specification spread. Cp is used when a process is under statistical control. Pp is used when a process is initially starting out.
Is it good to keep a process in control limits?
Keeping a process in control limits is not sufficient to achieve good quality. Quality is always dictated by the user. For that we use specification limits when assessing process capability. The process specifications used in process capability are the voice of the customer and control limits of Statistical Process Control are the voice of the process.
What is a Capability Procedure?
A capability procedure relates to the process of improving an employee’s performance.
Capability Vs Conduct
Capability relates to the willingness of the employee but may lack the skills to do the job. However, conduct shows unwillingness and a lack of motivation towards the job.
How to Manage a Capability Procedure
To manage capability at work, you should follow a process to help your employees improve.
Get Advice on Capability Procedures at Work with BrightHR
Dealing with poor performers can be difficult. But setting objectives can encourage your employees to improve their performance.

Process
Process Capability Meaning and Definition
- Minimum spread of process variation present in a manufacturing process. Process capability means how likely a product is going to meet the design specification. It is the 6 Sigma range of process Inherent variation. In SPC, Control limits are one of the most basic requirements of a process capabilitystudy, So it is very important to ensure the cond...
Need For Process Capability
- For meeting customer requirements/specifications.
- To measure and control the spread of process.
- To provide more realistic tolerances for product dimensions.
- Improve the process performance capability
Factors Influencing PC
- Condition of machine and equipment.
- Operation type and operational conditions.
- Type of Raw materials.
- The Skill of Operators and Inspectors.
Tools For PC Estimation
- Histogram.
- Control charts.
- Analysis of Variances.
- Run chart.
Process Capability Indices: CP and Cpk
- Process capability – Cp:This is defined as the tolerance width divided by the total spread of process. Cp indicates the spread of variation present in a process. Process Capability Index – Cpk: This is the capability index which accounts for centering of process and is defined as the minimum of Cpk upper and Cpk lower Cpk is a measure of the process performance capability. …