
Capacity analysis is the process of determining the capacity of an operation. In this regard, “capacity” can have a number of meanings, and a truly comprehensive capacity analysis will evaluate the physical capacity of your infrastructure and facilities, your production capacity, and your mechanical capacity.
What are some examples of capacity?
Definition Of Capacity. Capacity is the amount of liquid a container can hold. In other words, capacity is the volume of a container given in terms of liquid measurement. Examples of Capacity. The figure shows the tub in which Susan usually stores water for the cows. The capacity of the tub could be about 5 liters.
What is the measurement of capacity?
“We need to act now to protect residents across the state from unnecessary harm, and limiting the capacity of mass shooters to inflict more damage on innocent lives is an important ...
What is analytic capacity?
Capacity analysis seeks to determine the maximum output given current conditions at an industrial facility. Capacity analysis is an evaluation of the production capabilities at a plant or similar facility. This can be performed as part of a comprehensive review, or as a stand alone research project.
What is capacity based model?
capability mapping ), capability-based planning will enable an organization to:
- Identify its capabilities
- Assess the level of change required to each capability
- Prioritize the changes required
- Develop a plan for making the changes
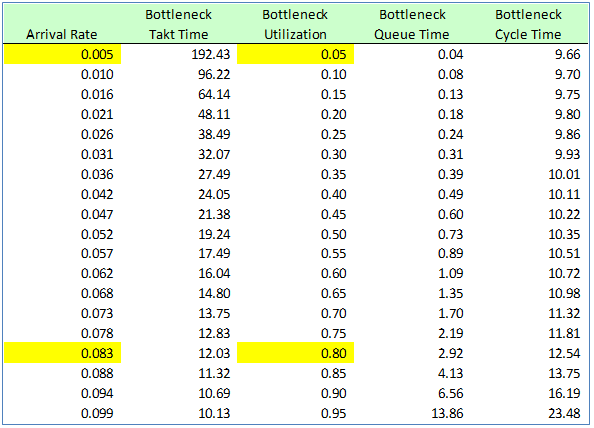
What are the 3 types of capacity?
Capacity is defined under 3 categories; design capacity, effective capacity and actual capacity.
What is capacity management and analysis?
Capacity management refers to the act of ensuring a business maximizes its potential activities and production output—at all times, under all conditions. The capacity of a business measures how much companies can achieve, produce, or sell within a given time period.
What are the 4 types of capacity?
There are three ways to categorize capacity, as noted next.Productive Capacity. This is the amount of work center capacity required to process all production work that is currently stated in the production schedule.Protective Capacity. ... Idle Capacity.
What is capacity in operation management?
What is Capacity Planning in Operations Management? Capacity planning in operations management is the process of balancing demand for a good or service with the ability of a manufacturer or organization to produce enough to meet demand.
How do you do a capacity analysis?
Capacity AnalysisPerform regular maintenance on machines to increase their efficiency.Purchase another machines (best for inexpensive resources, if possible).Hire another employee.Invest in employee training.Re-allocate existing capacity to increase the capacity of the bottleneck operation.More items...•
Why is capacity analysis important?
A capacity analysis coupled with advanced data capture and analytics can help companies find their path to full capacity quicker than most would think, and lead to a leveled production.
How is capacity measured?
Capacity is the amount a container can hold. The oil, juice drink and gasoline containers are just a few examples of objects that illustrate capacity. Capacity is measured in the SI base unit called litres (L). The most common units for capacity are litre (L) and millilitre (mL).
What is capacity Example?
The definition of capacity is the ability of someone or something to hold something. An example of capacity is how many people can fit in a room. An example of capacity is the amount of water a cup can hold. The power of receiving and holding knowledge, impressions, etc.; mental ability.
What are the 8 steps in capacity planning process?
Question: explain 8 steps of the capacity planning process and Give example for each 1- Estimate future capacity requirements 2-Evaluate existing capacity and identify gaps 3- Identify alternatives 4- Conduct financial analysis 5- Assess key qualitative issues 6- Select one alternative 7- Implement alternative chosen 8 ...
What are the 3 components of capacity management?
This is reflected by the three subprocesses of capacity management: business capacity management, service capacity management, and component capacity management.
What is the concept of capacity?
There are numerous definitions of capacity, and several bases upon which to define it. The most widely used concept of capacity is the maximum potential production of an output or group of outputs by a producing unit, firm, or industry, given technology, capital stock and other factors of production.
What is capacity strategy?
Capacity strategy is an approach to increasing and decreasing business capacity to meet demand. Capacity includes things like labor and equipment that can be scaled to increase business output.
What is capacity analysis?
Capacity analysis is the process of modeling the capacity of infrastructure, facilities, processes, services and machines. Capacity is the maximum output of an item based on its design or constraints such as available resources. The following are illustrative examples.
How is capacity modeled in information technology?
The capacity of information technology may be modeled with performance testing. For a software platform, this may be based on the maximum concurrent users that can be supported while achieving service level objectives such as a response time target.
What is throughput modeling?
This may involve modeling the entire process with estimates for the throughput of each workstation, machine and operation to identify capacity limits .
What is Capacity Analysis?
Capacity analysis is the process of determining the capacity of an operation. In this regard, “capacity” can have a number of meanings, and a truly comprehensive capacity analysis will evaluate the physical capacity of your infrastructure and facilities, your production capacity, and your mechanical capacity.
What is physical capacity?
Physical capacity refers to how much physical space an operation has to house inventory, systems, and processes. It is often completed using modeling software, with the goal of identifying ways that space can be used more efficiently.
What happens if you use lag capacity?
The downside to this is that an operation following a lag capacity strategy is likely to experience stockouts and lower service levels as it ramps up capacity to meet the new, increased demand. This can cause issues with business retention as customers turn to competitors to fulfill their needs.
What is production capacity?
Production capacity refers to the peak throughput of all of the processes in an operation. It takes into account important KPIs like total order cycle time, orders/lines picked per hour, order accuracy rates, and others.
How can an operation increase the physical capacity of their facilities?
There are a number of ways that an operation can increase the physical capacity of their facilities, from reclaiming vertical space through the use of automated storage and retrieval systems (AS/RS) or goods-to-person technologies, to drop-shipping larger items to keep them out of inventory, to conducting an SKU analysis to prevent SKU proliferation and reduce inventory needs, and more.
What are the three strategies for increasing the capacity of an operation?
When it comes to increasing the capacity of an operation, most businesses will pursue one of three common strategies: Lead Capacity, Lag Capacity, and Match Capacity. Each of these has their own unique advantages and disadvantages, and which one a specific operation decides to go with will depend on the specifics of their business.
What is lead capacity?
By increasing capacity before the demand is present, this strategy allows an operation to immediately ramp up production when the demand materializes, preventing an inability to fulfill orders that could cause customers to turn to the competition.
What is capacity analysis?
Capacity Analysis is the process of identifying the available capacity for your organization which includes the available inventory holding capacity, machine capacity, labor capacity, etc.
What is a capacity plan?
The capacity plan ensures that the production facility knows which orders they can commit to based on the available capacity of their facility.
How to model capacity?
The key frameworks to model capacity are rooted in real world thresholds (constraints) of practicality and profitability. Most commonly, these include: 1 Price - The cost of equipment, machines, softwares, and other maintenance fees can create thresholds to the total available capacity on resources. 2 Performance - The performance of your resources can affect the total amount of capacity you have. If older machines are running at a slower rate than they should, you are not able to produce as many items on it. 3 Capabilities - The resource capacity you posses must be capable to perform the work that is required. If your capacity bottleneck involves a process requiring a highly specific skill set, your capacity will be limited.
Why are bottlenecks so costly?
Bottlenecks cause delays in production, too much work-in-process items, and can be costly to the company . Identifying capacity bottlenecks can help identify the real cause of the problem and develop a plan to resolve it. There are many ways to increase resource capacity within your facility:
What is performance in computing?
Performance - The performance of your resources can affect the total amount of capacity you have. If older machines are running at a slower rate than they should, you are not able to produce as many items on it. Capabilities - The resource capacity you posses must be capable to perform the work that is required.
Why is it important to understand your capacity limitations?
It is important to understand your capacity limitations so that you can identify areas of improvement and develop a capacity plan that is just right for your organization.
What is the first step to take when you are constantly operating under constrained capacity?
The first step to take when you are constantly operating under constrained capacity is to identify the bottleneck. A capacity bottleneck is a process or operation that has limited capacity and reduces the capacity of the entire production plant.
Why do companies perform capacity analysis?
Companies that perform a manufacturing capacity analysis are able to reduce downtime and waste. They can also mine the data to optimize processes and streamline workflows. Doing so can help them understand what the existing constraints are and make real-time decisions to solve problems as they happen. As data support these solutions, managers can drive improvement throughout the operation and increase capacity without additional investment in equipment or labor. For companies looking to improve their manufacturing capacity, here are the steps required to unlock existing capacity:
What is the role of managers in capacity analysis?
These changes can be used to tackle the most significant capacity constraints, unlock the hidden capacity to eliminate overtime, reduce the need for capital expenditure, and hone a maintenance program that works in sync with changeovers and other operating conditions instead of contention with them.
What is Manufacturing Capacity?
But what is manufacturing capacity? The short answer is that manufacturing capacity represents the state in which all equipment and resources within a company are utilized at the highest operation rate for the product mix and volume their industry requires. This means that all processes from operations to maintenance are optimized with a set amount of resources and that no unnecessary downtime is incurred. When this condition is reached, the equipment has reached full capacity.
Why do factories lose production capacity?
Or they could lose valuable production capacity due to changeovers, setups, and adjustments.
What is benchmark data?
Benchmark Data. If you don’t know where you’re at, you’re not going to see where you’re headed. It’s common to overestimate current equipment utilization as many companies may not even realize that utilization is as low as it is. Benchmarking includes determining existing capacity.
Capacity Analysis in Transport
Transport capacity is the maximum transport capacity of a means of transport in a given period of time, in specific conditions defined by current technical and organisational factors. Technical factors determine the payload or load capacity of the means of transport, the speed of the vehicle or the type of vehicle transported .
Capacity meters
The main measure characterising passenger transport of each type is capacity, defined as the product of the number of passengers (train, bus) and the distance travelled by them. The unit of transport work is the passenger-kilometre .
Assumptions for capacity analysis
The concept of capacity in passenger traffic (e.g. rail) can be defined as the number of passengers that is movable in a given period of time, taking into account the convenience of travel . Determination of seating capacity passenger coaches may concern the whole railway network, or only the line or section to be analysed .
Capacity analysis in determining congestion and bandwidth
Capacity analysis is also used to traffic measurements, determine congestion and bandwidth. In a stochastic concept of highway bandwidth analysis, the capacity of an object on a highway is treated as a random variable, not a constant value.
Capacity Analysis in IT
Each computer is equipped with memory, i.e. electronic systems for storing data and programs. Memory is an ordered (numbered from 0) set of elementary memory cells of a specified length. RAM (Random Access Memory) is a memory with free access (access to any RAM cell is possible at any time).
Capacity Analysis in Management
Capacity in management is understood as efficiency, effectiveness and potential . It is a result of undertaken actions, described by the relation of the achieved effects to the incurred outlays.
What is capacity
Capacity means ability to do something. In case of manufacturing industry, ability to manufacture a particular quantity of products in a particular time duration.
What is capacity analysis
Capacity analysis is basically an analysis done to check whether a manufacturing plant can produce a particular no of products in a given period, with available no of resources.
Business Analysis
This is the complete list of articles we have written about business analysis.
Office Politics
A list of social processes, absurdities and strategies related to office politics.
What is a Capacity Analysis?
The initial step to take when you are continuously operating under distant capacity is to recognize the obstruction. A capacity bottleneck is a process or operation that has restricted capacity and minimizes the capacity of the whole production plant.
Manufacturing Capacity
Every manufacturer always aims to perform its operations at full capacity. So what is the manufacturing capacity? Manufacturing capacity describes the state in which all equipment and resources within a company are used at the highest operation rate for the required product volume.
Types of Capacity Planning
There are 3 key types of capacity planning that you require to be up to date with before you get started. Make a plan that will assure that you have the precise amount of everything you require to develop your products and grow your business.
How to Execute a Manufacturing Capacity Analysis
Industries that execute a manufacturing capacity analysis are capable to minimize downtime and waste. They can also store the data to optimize processes as well as streamline workflows. It will help them to interpret what the existing obstructions are and take real-time decisions to resolve issues as they occur.
Measure Data
Benchmarking contains determining existing capacity. Machine quality losses, speed, downtime by categories – likewise breakdowns, performance losses – must all be calculated to decide the current capacity. Below are few practices that can be utilized to build a solid and practical framework for benchmarking:
Monitor Downtime
Manufacturers must be conducted a downtime analysis. This process includes managers, technicians, manufacturing engineers, operators, as well as others who can help to recognize all the reasons for downtime and plan how to minimize or eliminate it.
What is product capacity plan?
A product capacity plan ensures you have enough products or ingredients for your deliverables. For a florist, this would be flowers, vases, and cards. For a pool maintenance company, this would be things like chlorine that are required to do the job.
Why is capacity planning important?
Capacity planning helps you deliver on the things that are important to your customers. Incorporating this type of strategic planning into your process will help you meet due dates, effectively scale your business, and increase your bottom line.
How Is Capacity Planning Different From Resource Planning?
Resource and capacity planning sometimes get confused with one another, but they are different things – and you need both. Capacity planning is more high level and helps you determine what and how many resources you need to meet demand. Resource planning is more about analyzing resource utilization: you use it to takes the number of resources available (as determined by your capacity planning) and allocate them to individual projects.
Why is delivery capacity important?
As online sales grow ever more popular, delivery capacity is becoming an essential component for many businesses. In another global consumer study conducted by Oracle Retail, 92% of retail shoppers said they would like or love “free one-day delivery by whatever means is most expedient.” Capacity planning ensures you have the workers available to deliver products whenever needed, keeping your business competitive.
What are the three types of capacity planning?
You’ll want to plan weeks, months, or even a year in advance. 1. Product capacity planning. Product capacity planning ensures you have enough products or ingredients for your deliverables.
How many steps are there in capacity planning?
There are three basic steps to capacity planning.
What is lag strategy?
Lag strategy is a conservative method of capacity planning that ensures your costs are as low as possible. The potential downside to this strategy is that it can create a lag in the delivery of products or services to customers, which is where the name comes from. If you get a sudden surge in orders or land a large new client who wants fast turnaround times, lag strategy may prevent you from meeting due dates.
