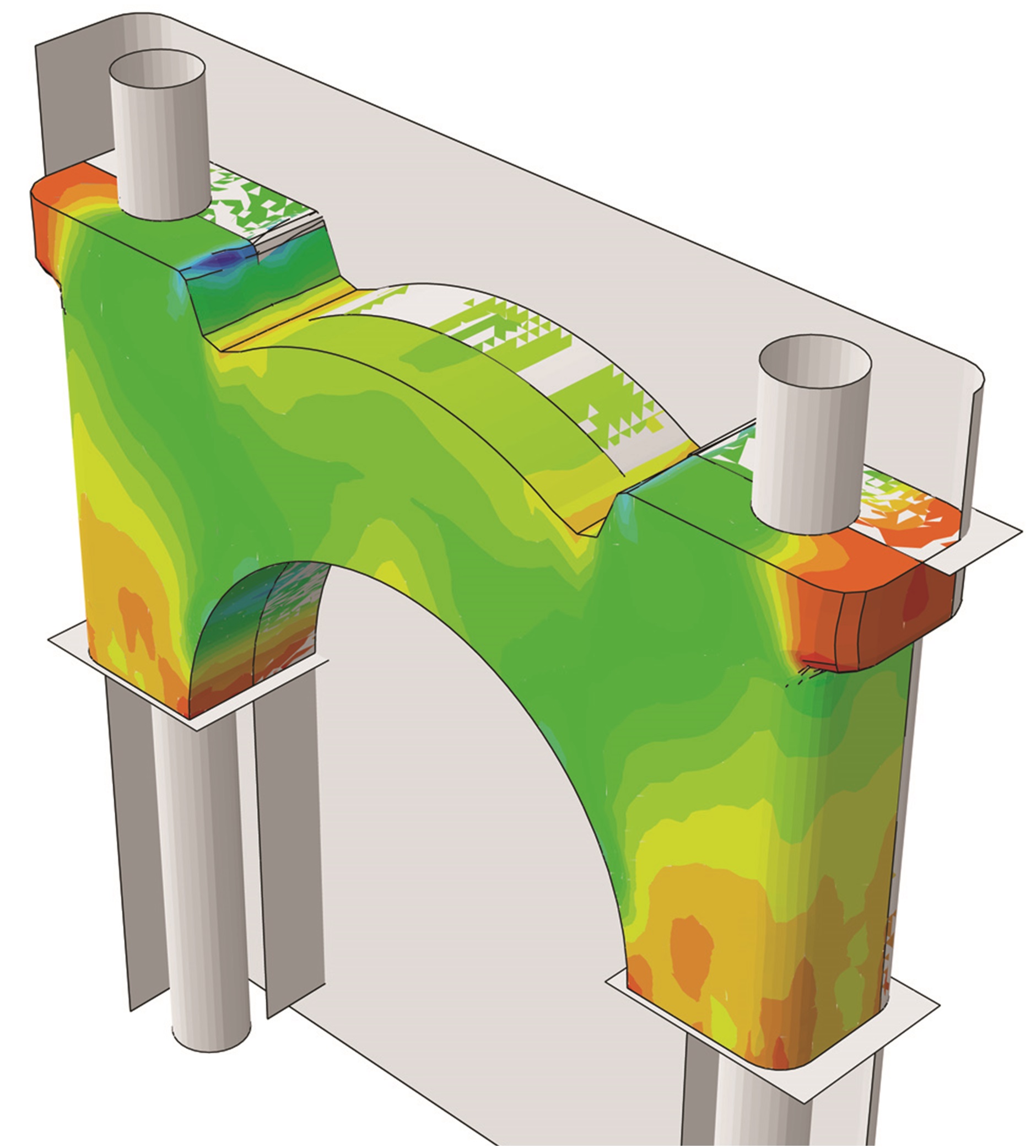
What is a powder compaction die?
May 11, 2020 · What is compaction in powder metallurgy? Powder compaction is the process of compacting metal powder in a die through the application of high pressures. Typically the tools are held in the vertical orientation with the punch tool forming the bottom of the cavity. The powder is then compacted into a shape and then ejected from the die cavity.
What is compacting in powder moulding?
Mar 11, 2020 · What is compacting in powder metallurgy? Powder compaction is the process of compacting metal powder in a die through the application of high pressures. Typically the tools are held in the vertical orientation with the punch tool forming the bottom of the cavity. The powder is then compacted into a shape and then ejected from the die cavity.
What is the meaning of compact compacting?
May 19, 2020 · Compaction is crucial in powder metallurgy processing because it allows free metal powders to be formed into desired forms with sufficient strength to survive until sintering is done. Compaction is often performed without the use of heat.
What is powder compaction of rhodium?
Apr 17, 2014 · This phase of powdered metallurgy is referred to as compacting or pressing. Compacting or pressing of metal powders is divided into the following two areas: Hot Pressing Cold Pressing Hot pressing is the compaction of powder at elevated temperatures. It is usually a dual technique where the metal powders are compacted and sintered at the same time.

What is compaction and sintering?
The desired characteristics to be achieved by compacting are high product density and uniformity of that density throughout the compact. Sintering: Sintering is the process of heating the green compact at a high temperature below the melting point in a controlled atmosphere.
What is the process of powder metallurgy?
Powder metallurgy is a fabrication technique that involves three major processing stages: (i) production of metal powder, (ii) compaction and shaping of the powder, and (iii) consolidation and fusing of the powder into a solid metal component under high temperature and pressure.
What is the significant role of compaction and sintering in powder metallurgy?
After compaction, neighbouring powder particles are held together by cold welds, which give the compact sufficient “green strength” to be handled. At sintering temperature, diffusion processes cause necks to form and grow at these contact points. Reduction of the surface oxides from the powder particles in the compact.
What is meant by green compaction in powder metallurgy?
Powder Metallurgy (PM) deals with products and processes which use raw material in the form of powders that are compacted into the required shape and size using suitable moulds. These compacted powders are called „Green Compacts‟.
What is metallurgy powder?
Powder metallurgy (PM) is a process for forming metal parts by heating compacted metal powders to just below their melting points. In other words, PM is a metal shaping process that creates near-net parts from powdered metal.Aug 15, 2017
What are the four main steps in powder metallurgy?
There are four main processes used in powder production: solid-state reduction, atomization, electrolysis, and chemical.
What is powder compaction?
Powder compaction is the process of compacting metal powder in a die through the application of high pressures. Typically the tools are held in the vertical orientation with the punch tool forming the bottom of the cavity. The powder is then compacted into a shape and then ejected from the die cavity.
Why is sintering used?
Why is Sintering done and Why is it Important? Sintering is done to impart strength and integrity to a material as well as reducing porosity and enhancing electrical conductivity, translucency and thermal conductivity.
What is the basic purpose of powder pressing?
Powder pressing is the compaction of powders into a geometric form. Pressing is usually performed at room temperature. This creates a solid part called a green compact. The strength of this pressed, unsintered part, (green strength), is dependent on compactability, binders may be used to increase compactability.
What is effect of compaction of powder on thermal conductivity k value?
Moreover, the higher the compaction forces, the higher the thermal conductivity. Since, pressure is directly proportional to compaction force, increased in thermal conductivity will results to increase in temperature.
What is green strength in metallurgy?
Green strength, or handling strength, can be defined as the strength of a material as it is processed to form its final ultimate tensile strength. This strength is usually considerably lower than the final ultimate strength of a material.
What does the word compacting mean?
Compaction is what happens when something is crushed or compressed. In many places, garbage undergoes compaction after it's collected, so that it takes up less space. The process of making something more compact, or dense and very tightly packed together, is compaction.
What is hot pressing?
Hot pressing is the compaction of powder at elevated temperatures. It is usually a dual technique where the metal powders are compacted and sintered at the same time. The hot pressing technique is used mostly in the manufacturing of carbide cutting tools and in a few specialized applications.
Why did stamping presses require a lot of set up time?
They also required quite a bit of set up time to change dies and punches because of the lack of adjustability and controls.
What is the first phase of P/M?
This first fabrication or configuration of a P/M bearing begins with the pressing process. In most cases the first serious problems to be encountered in the powdered metallurgy process are usually found when pressing powder into shapes. This phase of powdered metallurgy is referred to as compacting or pressing.
What is a P/M compacting press?
The majority of P/M parts are compacted by mechanical means. Mechanical presses, in general, are used for making parts in the lower pressure range because their speed exceeds those of hydraulic presses in most cases. The two basic categories of P/M compacting presses are mechanical and hydraulic. The main difference between the two are ...
Why do P/M parts need to be repressed?
When extremely accurate dimensions are required the P/M part or parts must be repressed because of dimensional changes during the sintering operation. This is a rapid operation usually performed on high speed presses.
What are the physical properties of metal powders?
Pressing of metal powders depend upon their physical characteristics and properties. These include particle size, shape, composition, and size distribution. The type of powder and its method of manufacture also influences its behavior under pressure in a cold die.
What are the problems with excessive pressure?
Excessive pressures can present some complex problems such as punch and die fractures, slip cracks and cleavage fractures in the green part. Although high pressures are required for pressing high density shapes they should not be excessive.
What is PM in metal?
In other words, PM is a metal shaping process that creates near-net parts from powdered metal.
Is powder metallurgy a high volume process?
It is suitable for high-volume production with very little wastage of material. Secondary machining is virtually eliminated. Powder metallurgy is a continually and rapidly evolving technology embracing most metallic and alloy materials, and a wide variety of shapes.
Chapter One - What is Powder Metallurgy?
Powder metallurgy is a manufacturing process that produces precision and highly accurate parts by pressing powdered metals and alloys into a rigid die under extreme pressure.
Chapter Two - The Powder Metallurgy Process
The process of powder metallurgy is an ancient, unique method for forming shapes and designs from ferrous and non-ferrous metals. Powder metallurgy has been used for thousands of years as a way to produce household items and tools. It began as a method for mass producing products and parts in the middle of the first industrial revolution.
Chapter Three - Parts and Products Made Using Powder Metallurgy
After its return in the middle of the first industrial revolution, the use of powder metallurgy has steadily grown to become an essential part of the production of a wide variety of parts and products.
Chapter Four - Types of Metals Used in Powder Metallurgy
There are few limitations to the types of metals that can be used in the powder metallurgy process. Though there is a wide selection available, certain metals are used repeatedly due to their properties and characteristics. There are certain factors producers consider when making their metal selection.
Chapter Five - Equipment Used for Powder Metallurgy
Each step of the powder metallurgy process requires special equipment that varies according to the process being used. Powder metallurgy is a method for producing structural parts and bearings using a variety of techniques and equipment.
Chapter Six - Benefits of Using the Powder Metallurgy Process
To many, the steps of the powder metallurgy process may seem like a waste of time considering there are other methods less time consuming. Though there are negative factors regarding powder metallurgy, its many benefits have made it one of the most popular production methods.
Conclusion
Powder metallurgy is a manufacturing process that produces precision and highly accurate parts by pressing powdered metals and alloys into a rigid die under extreme pressure.
What is electro sintering?
Spark plasma sintering and electro sinter forging are two modern, industrial commercial ECAS technologies. Additive manufacturing (AM) is a relatively novel family of techniques which use metal powders (among other materials, such as plastics) to make parts by laser sintering or melting.
What is isostatic powder compacting?
Isostatic powder compacting is a mass-conserving shaping process. Fine metal particles are placed into a flexible mould and then high fluid pressure is applied to the mold, in contrast to the direct pressure applied by the die faces of a die pressing process. The resulting article is then sintered in a furnace which increases the strength of the part by bonding the metal particles. This manufacturing process produces very little scrap metal and can be used to make many different shapes. The tolerances that this process can achieve are very precise, ranging from +/- 0.008 inches (0.2 mm) for axial dimensions and +/- 0.020 inches (0.5 mm) for radial dimensions. This is the most efficient type of powder compacting (the following subcategories are also from this reference). This operation is generally only applicable on small production quantities, although the cost of a mold much lower than that of pressing dies it is generally not reusable and the production time is much longer.
What is hot isostatic pressing?
In some pressing operations, such as hot isostatic pressing (HIP ) compact formation and sintering occur simultaneously. This procedure, together with explosion-driven compressive techniques is used extensively in the production of high-temperature and high-strength parts such as turbine disks for jet engines. In most applications of powder metallurgy the compact is hot-pressed, heated to a temperature above which the materials cannot remain work-hardened. Hot pressing lowers the pressures required to reduce porosity and speeds welding and grain deformation processes. It also permits better dimensional control of the product, lessens sensitivity to physical characteristics of starting materials, and allows powder to be compressed to higher densities than with cold pressing, resulting in higher strength. Negative aspects of hot pressing include shorter die life, slower throughput because of powder heating, and the frequent necessity for protective atmospheres during forming and cooling stages.
What are the steps of powder metallurgy press?
The powder metallurgy press and sinter process generally consists of three basic steps: powder blending (pulverisation), die compaction, and sintering. Compaction is generally performed at room temperature, and the elevated-temperature process of sintering is usually conducted at atmospheric pressure and under carefully controlled atmosphere composition. Optional secondary processing such as coining or heat treatment often follows to obtain special properties or enhanced precision.
What is sintering metal?
Sintering involves the production of a hard solid metal or ceramic piece from a starting powder. The ancient Incas made jewelry and other artifacts from precious metal powders, though mass manufacturing of PM products did not begin until the mid or late 19th century. In these early manufacturing operations, iron was extracted by hand from metal sponge following reduction and was then reintroduced as a powder for final melting or sintering.
How are air and powder streams segregated?
Air and powder streams are segregated using gravity or cyclonic separation. Most atomized powders are annealed, which helps reduce the oxide and carbon content. The water atomized particles are smaller, cleaner, and nonporous and have a greater breadth of size, which allows better compacting.
What are the hazards of powder metallurgy?
The special materials and processes used in powder metallurgy can pose hazards to life and property. The high surface-area-to-volume ratio of the powders can increase their chemical reactivity in biological exposures (for example, inhalation or ingestion), and increases the risk of dust explosions.
1. Powder production
Almost all iron powders for the production of PM components are produced either using the sponge iron process or by water atomization. Non-ferrous metal powders used for other PM applications can be made by a number of processes.
2. Mixing of powders
This can often include the incorporation of alloy additives in the form of an elemental powder or the incorporation of a press lubricant.
3. Forming of the mixed powder into a compact
The dominant consolidation process involves the press-fitting of a rigid tool set that includes a die, punches, and possibly mandrels or core rods. However, there are several other consolidation processes that are used in niche applications.
4. Sintering of the compact to enhance integrity and strength
This process step involves heating the material, usually in a protective atmosphere, to a temperature that is below the melting point of the major constituent.
5. Secondary operations
The application of finishing processes to the sintered part. In powder metallurgy, such processes are often referred to as “secondary operations”.
What is compacting powder?
Compacting: Compacting means compressed the prepared powder mixture into pre-defined dies. This step ensures to reduce voids and increase the density of the product. The powder is compacted into the mold by the application of pressure to form a product which is called green compact (the product gets by compacting).
What is powder metallurgy?
Powder Metallurgy is can be defined as the process of preparation and process the powdered iron and nonferrous metals are called as powder metallurgy.
What is the first step in the process of making powder?
1. Powder Preparation: This is a first and basic step for producing an object by powder metallurgy process. Any material can convert into powder. There are various processes of producing powder such as atomization, grinding, chemical reaction, electrolysis process, etc. 2.
What is a secondary operation?
Where a sintered product cannot be used as a finished product. That’s why a secondary operation required to obtain high density and high dimensional accuracy. The most common secondary operation used is sizing, hot forging, coining, infiltration, impregnation, etc.
What is Babbitt bearing?
Babbitt bearing for automobiles. To produce oil pump gears for automobiles. Used for production of cutting tools, wire drawing dies and deep drawing dies. To produce refractory metal composites, eg: tungsten, molybdenum, tantalum For manufacturing the tungsten wires for filaments in the lamp industry.
Is powder metallurgy heat resistant?
Powder metallurgy should be heat resistant. The size of the powder particles is to pass the powder through the screen (sieves) having a definite number of meshes. The powder should have good plasticity. It should have the ability to be cold-pressed. The powder should have an excellent parking factor.
Is sintered material porous?
The sintered object is more porous compared to fully dense material. The density of the product depends upon press capacity, sintering temperature, compressing pressure, etc. Sometimes, the product does not require high density and the sintered product is directly used as a final product.
