
Control limits, also known as natural process limits, are horizontal lines drawn on a statistical process control chart, usually at a distance of ±3 standard deviations of the plotted statistic from the statistic's mean.
How do you calculate control limits?
Control limits are calculated by: Estimating the standard deviation, σ, of the sample data. Multiplying that number by three. Adding (3 x σ to the average) for the UCL and subtracting (3 x σ from the average) for the LCL.
What are statistical control limits?
These are:
- Distribution of the individual values
- Distribution of the subgroup averages
- Distribution of the subgroup ranges
How to calculate statistical process control limits?
The Estimated Standard Deviation and Control Charts
- Data Subgroups. The data we will use are shown in the table. ...
- Three Ways to Estimate the Standard Deviation. We will look at three different ways to estimate the standard deviation. ...
- Average of Subgroup Ranges. ...
- Average of Subgroup Standard Deviations. ...
- Pooled Standard Deviation. ...
- Summary. ...
How to set control limits?
If what the toddler is doing is not bothering anyone or ruining anything important, then it may not be necessary to set limits. This is important to note, according to the publication, because if there are too many limits, toddlers will rebel and the situation will be worse than when it started.
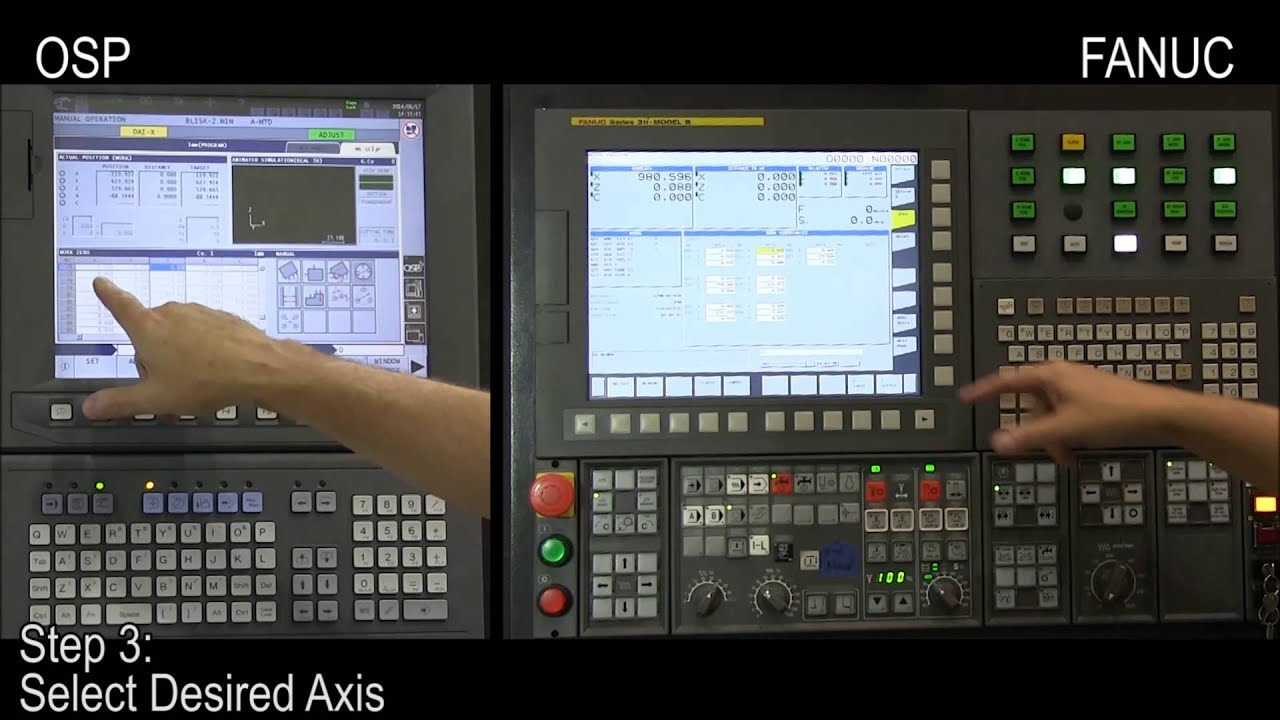
How do you explain control limits?
Control limits are the horizontal lines in a control chart that delineate the upper and lower limits of the acceptable range of results for a process. When plotted data exceeds a control limit, it indicates that a process is out of control, and requires management attention.
How do you find control limits?
Control limits are calculated by:Estimating the standard deviation, σ, of the sample data.Multiplying that number by three.Adding (3 x σ to the average) for the UCL and subtracting (3 x σ from the average) for the LCL.
What is the purpose of control limits in a control chart?
The control limits of your control chart represent your process variation and help indicate when your process is out of control. Control limits are the horizontal lines above and below the center line that are used to judge whether a process is out of control.
What are the 3 control limits for chart?
Three-sigma limits are used to set the upper and lower control limits in statistical quality control charts. On a bell curve, data that lie above the average and beyond the three-sigma line represent less than 1% of all data points.
What is UCL and LCL?
The Upper Control Limit (UCL) and the Lower Control Limit (LCL) form a corridor within which a quality characteristic meets the desired value or a normal deviation. Outside the limitations of UCL and LCL, the quality measured is considered as abnormal and requires intervention in the relevant process.
How are control limits set on charts?
The control chart is a graph used to study how a process changes over time. Data are plotted in time order. A control chart always has a central line for the average, an upper line for the upper control limit, and a lower line for the lower control limit. These lines are determined from historical data.
What is the difference between tolerance limits and control limits?
Question 13: What is the difference between tolerance limits and control limits? An important difference between tolerance limits and control limits is that the former are used to determine whether individual manufactured components are acceptable, whereas the latter are used to control the manufacturing process.
What is control limits and specification limits?
Specification limits are the targets set for the process/product by customer or market performance or internal target. In short it is the intended result on the metric that is measured. Control limits on the other hand are the indicators of the variation in the performance of the process.
What are the 4 types of control charts?
Types of Control Charts (SPC).X bar control chart. ... Range “R” control chart. ... Standard Deviation “S” control chart. ... Attribute Control Charts: ... “u” and “c” control charts. ... “p” and “np” control charts. ... Pre-control Charts.
Why are control limits set at 3-sigma?
Control limits on a control chart are commonly drawn at 3s from the center line because 3-sigma limits are a good balance point between two types of errors: Type I or alpha errors occur when a point falls outside the control limits even though no special cause is operating.
What is LSL and USL?
USL = Upper Specification Limit. LSL = Lower Specification Limit. The “customer” defines your specification limits.
How do you get UCL and LCL?
How to calculate upper control limit (UCL)? Upper control limit formulaThe upper control limit formula: UCL = x - (-L * σ)The lower control limit formula: LCL = x - (L * σ)
How do I find my UCL?
How to calculate upper control limit (UCL)? Upper control limit formulaThe upper control limit formula: UCL = x - (-L * σ)The lower control limit formula: LCL = x - (L * σ)
How do you find the control limit using Z?
It is determined by the following equation:z=(X-X)/σwhere X is the sample result, X is the average, and σ is the standard deviation. ... σ = R/1.128.z1 = (X-X1)/σ1 = (20-19.5)/4.5 = 0.11.z2 = (X-X2)/σ2 = (5-8.3)/2.1 = -1.57.σ(R) = 1.128.UCLR = 3.267R = (3.267)(1.128) = 3.686.
How do you find UCL and LCL in Excel?
Consider these steps to chart an upper control limit in Excel:Enter your data. ... Find the average of averages. ... Calculate the standard deviation. ... Add the UCL formula. ... Add the LCL formula. ... Copy the UCL, LCL and average of averages. ... Select your data and choose a chart. ... Change the chart title and save the workbook.
What are the control limits for NP chart?
The control limits are. , where n is the sample size and. is the estimate of the long-term process mean established during control-chart setup. The number nonconforming (np), rather than the fraction nonconforming (p), is plotted against the control limits.
Control Limit Equations
Control limit equations are based on three sigma limits. Just remember, it is three sigma limits of what is being plotted. So, what does that mean? If you are plotting individual values (e.g., the X control chart for the individuals control chart), the control limits are given by:
Distributions
There are three distributions to consider when discussing the control limit equations. These are:
The Data
To start, 100 subgroups of size 5 were generated in Microsoft Excel using the random number generator (must install the Analysis Tookpak add-in). The average used in the random number generator was 100 with a standard deviation of 10. You can download the workbook containing the data here: download workbook .
Distribution of Individual Values
The histogram for the distribution of individual values is shown below in Figure 1.
Distribution of Subgroup Averages
The histogram for the distribution of subgroup averages is shown below in Figure 2.
d 2 and d 3
There is a paper ( Tables of Range and Studentized Range, written by H. Leon Harter from 1960 that gives the moments of the range for samples of subgroup n from a normal distribution. For those of you who are interested in the details and the complicated equations, you can download the paper here.
Generating the Control Limit Equations
Now with the theoretical values of d 2 and d 3, we can move forward with finding the control limit equations.
What is the CPK requirement?
A normal requirement is that Cpk should be at least 1.33. Read more about capability ». Cmk (capability machine index) If you also want to study the position of the machine’s capability in relation to the tolerance limits, you use the Cmk index, which describes the capability corrected for position.
What is a high CPK index?
It is not much use having a high Cp index if the process setting is way off centre in relation to the middle of the tolerance range. A high Cpk index means, then, that you ...
What does CPK 1.00 mean?
Cpk 1.00 means that 2 700 PPM (0.27%) of the manufactured parts are out of tolerance, while Cpk 1.33 means that 63 PPM (0.0063%) are rejects. Note that the PPM index can be drastically improved by a relatively small improvement in the capability index (see Fig. 12).
What is process capability?
Process capability#N#Process capability is a long-term study, measured in Cp and Cpk, that shows how well a process is performing in relation to the tolerance limits while the study is in progress, as well as indicating likely performance in the immediate future.
What is the function of control limits?
The function of control limits is to centre the process on the target value, which is usually the same as the middle of the tolerance width, and to show where the limit of a stable process lies. This means, in principle, that you have no reason to react until the control chart signals certain behaviour.
What is the Cm index?
The Cm index describes machine capability; it is the number of times the spread of the machine fits into the tolerance width. The higher the value of Cm, the better the machine. Example: if Cm = 2.5, the spread fits 2½ times into the tolerance width, while Cm = 1 means that the spread is equal to the tolerance width.
What does Cp mean in math?
Example: if Cp = 2.5, the spread of the process fits 2½ times into the tolerance width, while Cp = 1 means that the spread is equal to the tolerance width. Note that even if the spread is off-centre, it is still the same size (Cp index). The figure takes no account of where ...
What is a control chart in healthcare?
Using Control Charts In A Healthcare Setting (PDF) This teaching case study features characters, hospitals, and healthcare data that are all fictional. Upon use of the case study in classrooms or organizations, readers should be able to create a control chart and interpret its results, and identify situations that would be appropriate for control chart analysis.
How to use control chart?
When to Use a Control Chart 1 When controlling ongoing processes by finding and correcting problems as they occur 2 When predicting the expected range of outcomes from a process 3 When determining whether a process is stable (in statistical control) 4 When analyzing patterns of process variation from special causes (non-routine events) or common causes (built into the process) 5 When determining whether your quality improvement project should aim to prevent specific problems or to make fundamental changes to the process
What is the central line on a control chart?
A control chart always has a central line for the average, an upper line for the upper control limit, and a lower line for the lower control limit. These lines are determined from historical data. By comparing current data to these lines, you can draw conclusions about whether the process variation is consistent (in control) or is unpredictable ...

Control Limit Equations
Control limits, also known as natural process limits, are horizontal lines drawn on a statistical process control chart, usually at a distance of ±3 standard deviations of the plotted statistic from the statistic's mean.
Control limits should not be confused with tolerance limits or specifications, which are completely independent of the distribution of the plotted sample statistic. Control limits describe what a pro…
Distributions
The Data
Distribution of Individual Values
Distribution of Subgroup Averages
- There are three distributions to consider when discussing the control limit equations. These are: 1. Distribution of the individual values 2. Distribution of the subgroup averages 3. Distribution of the subgroup ranges Each of these three distributions has a location parameter (the average) and a dispersion parameter (standard deviation). We will take a look at what these parameters are a…
Distribution of Range Values
- To start, 100 subgroups of size 5 were generated in Microsoft Excel using the random number generator (must install the Analysis Tookpak add-in). The average used in the random number generator was 100 with a standard deviation of 10. You can download the workbook containing the data here:download workbook . Since this a random number generator, it should generate a …
D2 and D3
- The histogram for the distribution of individual values is shown below in Figure 1. A normal curve has been superimposed on the histogram. As expected, the individual values are normally distribution. The location parameter for this distribution (histogram) is simply the average of the data. The dispersion parameter is the standard deviation of the data. The calculated average of t…
Generating The Control Limit Equations
- The histogram for the distribution of subgroup averages is shown below in Figure 2. Figure 2: Distribution of Subgroup Averages This distribution is also normally distributed as one would expect. The same x-axis scale was used for both Figure 1 and Figure 2. Note that the subgroup averages have less variation that the individual values. The location parameter for this distributi…