
Why is cullet used in glass manufacture?
The use of cullet in a glass furnace can significantly reduce the energy consumption because cullet has a lower melting energy requirement than the constituent raw materials – as the endothermic chemical reactions associated with glass formation have been completed – and its mass is approximately 20 % lower than the ...
How is glass cullet made?
The glass industry regularly mixes cullet—a granular material made by crushing bottles and jars usually collected from recycling programs—with sand, limestone, and other raw materials to produce the molten glass needed to manufacture new bottles and jars.
How do you use cullet?
But cullet can be used in many other ways, such as:as either base or surface coat (when mixed with asphalt) for roadways.as an additive to clay for brick-making.as an aggregate fill for moisture drainage; it can also be used in this way to filter water.for use in making spun glass fiberglass filaments for insulation.More items...
Is cullet recycled glass?
Recycled glass (cullet) is used as a replacement for minerals in the manufacture of glass packaging, helping to reduce reliance on primary raw materials whilst using substantially less energy.
What are the methods of processing glass?
Glass TechniquesCore-forming. the earliest method of making glass vessels is known as core-forming. ... Casting. This process involved the shaping of molten glass in a closed mould or over an open former. ... Blowing. ... Mould-blowing. ... Pattern-moulding. ... Tralling. ... Cutting. ... Fire-polishing.More items...
What is the manufacturing process of glass?
The company's glass manufacturing process follows a continuous and linear path. It starts with the loading of the raw materials in the melting furnace. Then, the glass gob is formed, and the bottle is shaped. The final stages are the annealing process and quality control.
What can I do with glass cullet?
Glass cullet has been used in different construction applications including cement replacement, aggregate replacement in concrete, road beds, pavement, trench fill, drainage medium, etc.; and in general use applications including abrasives, fluxes/additives, manufacturing of fiberglass insulation and foam insulation.
What type of waste is cullet?
Crushed glass also known as glass cullet refers to waste glass produced as a result of breakage and rejection on quality control grounds during the manufacturing process.
What are 3 ways to recycle glass?
How to recycle glass bottles: Carry a glass bottle as a reusable water bottle. Use a glass bottle as a candle holder inside or on the patio. Create mosaic art with broken pieces of colored glass bottles.
What is recycled glass called?
Unlike some materials, glass can be repeatedly recycled without losing its quality or strength, so glass manufacturers use crushed, recycled glass, called cullet, to reduce their production costs for glass items of many descriptions (see References 2).
Can glass be 100% recycled?
Glass is 100% recyclable and can be endlessly recycled with no loss of quality.
What are two types of glass that Cannot be recycled?
The following are examples of common glass items you cannot recycle:Glass cookware (eg heatproof jugs, Pyrex dishes, and microwave turntables) ... Light bulbs. ... Window glass. ... Drinking glasses and Vases. ... Nail varnish bottles. ... Mirrors. ... Spectacles.
How is glass mass manufactured?
The Press and Blow process is the most commonly used method in glass bottle manufacturing. It uses an individual section (IS) machine, which is separated into varying sections to produce several containers of the same size simultaneously. The molten glass is cut with a shearing blade into a specific gob size.
Can you turn sand back into glass?
0:141:25Turning glass back into sand - YouTubeYouTubeStart of suggested clipEnd of suggested clipIncluding high quality VicRoads approved road base and asphalt. And that's just one thing we do forMoreIncluding high quality VicRoads approved road base and asphalt. And that's just one thing we do for decades we have used well proven techniques to recycle engineers.
How is sand processed into glass?
The chemical process of creating glass is undergone by heating quartz sand, also known as silica sand, to temperatures above 3,090 degrees Fahrenheit until it melts into a clear liquid. Once the sand is in liquid form, it is cooled and undergoes a transformation that doesn't allow it to fully turn to a solid.
How is glass made from sand kids?
Glass is made from a mixture of sand, lime and soda. When these ingredients are heated together, they form a liquid glass. This liquid glass is made into sheets by cooling and flattening. To make objects like vases, craftsmen blow into a glob of liquid glass with the help of a long tube.
Why is cullet important?
Cullet is an important raw material that will help the glass industry achieve sustainability. The use of cullet improves energy efficiency, reduces carbon dioxide and NOx emissions, reduces wear and tear on furnaces, reduces the amount of waste going to landfills, and reduces the need to produce raw materials.
How does a cullet change from solid to liquid?
Cullet is already glass and no chemical reactions occur. The cullet simply heats up, softens and becomes liquid. There is no phase change from solid to liquid, as glass is a “super-cooled” liquid and therefore no latent melting energy. As stated earlier, the conversion of batch to glass begins with the decomposition and melting of the carbonates evolving into carbon dioxide. For every tonne of glass produced from SLS batch, approximately 175 kg of carbon dioxide is given off absorbing 0.16 GJ/tonne or 38.2 kcal/kg of energy, as it is heated to the furnace exhaust temperature.
What is the melting point of glass?
Silica, the major component of most commercial glasses, has a melting point of 1713°C (3115°F), a temperature well above that found in the majority of furnaces. Clearly something other than melting is occurring. Soda ash (sodium carbonate) starts to melt and decompose at about 800°C (1472°F), forming carbon dioxide gas and sodium oxide liquid. The sodium oxide liquid surrounds each sand grain and reacts with the silica at the surface forming sodium silicate. The calcium and magnesium carbonates also melt and decompose, giving off more carbon dioxide, the resulting oxides reacting with the sodium silicate to form soda-lime-silica (SLS) glass. These chemical reactions require time for the reacting species to diffuse through the boundary layer, react and then diffuse away again with energy, as these reactions are endothermic. The amount of energy absorbed by these glass-forming reactions is 490 kJ/kg or 116 kcal/kg.
What is recycled glass?
Recycled glass or cullet is a batch ingredient that is often not given the attention it deserves , but as the fraction in the batch mix increases, the impact on the final product also increases. As with any raw material the cullet should be of consistent and repeatable quality, there is much truth in the old adage “garbage in, garbage out.”
Why should cullet be stored?
No matter what the source, cullet should be stored and handled with the same care as the other raw materials to prevent degradation by size reduction, contamination or weathering. Cullet can bring positive benefits and the quality should not be compromised.
What is the density of a batch with no cullet?
The density of batch with no cullet is about 1300 kg/m 3, that of cullet is about 2500 kg/m 3 and, as the fraction of cullet increases in the mixture, its density increases non-linearly, as shown in Figure 2. Figure 2: Mixed Batch Density - More cullet the higher the density.
What temperature does glass need to be to produce glass?
The energy required reduces as the amount of cullet in batch increases. The amount of energy required to produce glass at 1500°C (2732°F) comprises three components, the glass forming reactions, the energy to heat the carbon dioxide and the sensible energy to heat glass to the production temperature, as shown in Figure 1.
What is glass container production?
Glass container production. Broadly, modern glass container factories are three-part operations: the batch house, the hot end, and the cold end. The batch house handles the raw materials; the hot end handles the manufacture proper—the forehearth, forming machines, and annealing ovens; and the cold end handles the product-inspection ...
What is the process of making glass?
Forming process. There are currently two primary methods of making glass containers: the blow and blow method for narrow-neck containers only, and the press and blow method used for jars and tapered narrow-neck containers.
Why is glass so weak?
Uneven cooling causes weak glass due to stress. Even cooling is achieved by annealing. An annealing oven (known in the industry as a lehr) heats the container to about 580 °C (1,076 °F), then cools it, depending on the glass thickness, over a 20 – 60 minute period.
What is the hot end of glass?
The hot end of a glassworks is where the molten glass is manufactured into glass products. The batch enters the furnace, then passes to the forming process, internal treatment, and annealing.
How long does a batch house hold glass?
The batch house simply houses the raw materials in large silos (fed by truck or railcar) and holds anywhere from 1–5 days of material.
What is a French kilner jar?
A modern "French Kilner" jar. Glass production involves two main methods – the float glass process that produces sheet glass, and glassblowing that produces bottles and other containers. It has been done in a variety of ways during the history of glass .
Is glass container manufacturing a business?
Glass container manufacture in the developed world is a mature market business. World demand for flat glass was approximately 52 million tonnes in 2009. The United States, Europe and China account for 75% of demand, with China's consumption having increased from 20% in the early 1990s to 50%. Glass container manufacture is also a geographical business ; the product is heavy and large in volume, and the major raw materials (sand, soda ash and limestone) are generally readily available. Therefore production facilities need to be located close to their markets. A typical glass furnace holds hundreds of tonnes of molten glass, and so it is simply not practical to shut it down every night, or in fact in any period short of a month. Factories therefore run 24 hours a day 7 days a week. This means that there is little opportunity to either increase or decrease production rates by more than a few percent. New furnaces and forming machines cost tens of millions of dollars and require at least 18 months of planning. Given this fact, and the fact that there are usually more products than machine lines, products are sold from stock. The marketing/production challenge is therefore to predict demand both in the short 4- to 12-week term and over the 24- to 48-month-long term. Factories are generally sized to service the requirements of a city; in developed countries there is usually a factory per 1–2 million people. A typical factory will produce 1–3 million containers a day. Despite its positioning as a mature market product, glass does enjoy a high level of consumer acceptance and is perceived as a "premium" quality packaging format.
Why is cullet used in glass?
Because the chemical energy required to melt the raw materials has already been expended, the use of cullet can significantly reduce energy consumption compared with manufacturing new glass from silica (SiO2), soda ash (Na2CO3), and lime (CaCO3).
What are the contaminants that can be removed from a cullet?
To be able to use external cullet in production, any contaminants should be removed as much as possible. Typical contaminations are : Organics: Paper, plastics, caps, rings, PVB foils for flat glass. Inorganics: Stones, ceramics, porcelains. Metals: Ferrous and non-ferrous metals.
Why do you separate colors in glass recycling?
Many collection points have separate bins for clear (flint), green and brown (amber). Glass re-processors intending to make new glass containers require separation by color, because glass tends to retain its color after recycling. If the recycled glass is not going to be made into more glass, or if the glass re-processor uses newer optical sorting equipment, separation by color at the collection point may not be required. Heat-resistant glass, such as Pyrex or borosilicate glass, must not be part of the glass recycling stream, because even a small piece of such material will alter the viscosity of the fluid in the furnace at remelt.
Why is the UK not recycling glass?
The waste recycling industry in the UK cannot consume all of the recycled container glass that will become available over the coming years, mainly due to the colour imbalance between that which is manufactured and that which is consumed. The UK imports much more green glass in the form of wine bottles than it uses, leading to a surplus amount for recycling.
What is glass recycling?
Glass recycling is the processing of waste glass into usable products. Glass that is crushed and ready to be remelted is called cullet. There are two types of cullet: internal and external. Internal cullet is composed of defective products detected and rejected by a quality control process during the industrial process of glass manufacturing, ...
How much glass was recycled in Germany in 2004?
Germany. In 2004, Germany recycled 2.116 million tons of glass. Reusable glass or plastic (PET) bottles are available for many drinks, especially beer and carbonated water as well as soft drinks ( Mehrwegflaschen ).
What color glass is best for recycling?
The most common colours used for consumer containers are clear (flint) glass, green glass, and brown (amber) glass. Glass is ideal for recycling since none of the material is degraded by normal use. Many collection points have separate bins ...
Why use more cullet glass?
While there are some benefits to using more cullet in glassmaking operations, environmental concerns and energy reduction costs are the major elements that are driving the move toward the use of more outside cullet.
Why is cullet important?
Possessing a precise and detailed understanding of the cullet cycle is of paramount importance as we examine the key to higher sustainability in batch plants and cullet handling systems. As shown in Figure 1, cullet processing considerations are intricately interrelated. In many circumstances the material is generated from defective and broken products from the glass plant. However, cullet from recycling operations or foreign cullet plants now form significant proportions of the container glass and glass fiber batch compositions. While there are some benefits to using more cullet in glassmaking operations, environmental concerns and energy reduction costs are the major elements that are driving the move toward the use of more outside cullet.
How does a cullet move?
Once produced, the cullet moves via conveyors, bucket elevators, diverters, chutes and other equipment specifically designed to handle this material . However, this equipment is subject to severe abrasive attack due to the relative hardness of glass and the sharp edges of cullet. An experienced contractor and knowledgeable engineering team can make a significant difference by implementing numerous techniques that minimize or eliminate wear on chutes, elbows, deflector plates and other material contact points.
What is the next step in handling cullet efficiently?
The next step in handling cullet efficiently is the cullet crushing process. Several types of cullet crushing equipment are available. Choosing the suitable apparatus and machinery for any given facility depends on the specifications, budget and other pertinent factors of the project.
What are the trends in glass industry?
Two primary trends have emerged in the glass industry regarding the use and handling of cullet. First is the significant increase in the use of foreign cullet (i.e . bought in cullet), which reduces raw material and melting costs, while lessening refractory erosion and decreasing furnace emissions. Second, the automated handling of cullet has become prevalent, thus reducing manpower and curtailing personnel safety risk.
Where is cullet conveyed?
The cullet is conveyed back to the batch plant where it can be crushed and further reduced in size if necessary and transported directly to the cullet silo. Float glass conditioning offers capabilities that streamline the cullet handling process and results in sustainability that is key to the long life of the plant.
Can stainless steel be used for glass?
It is important to keep in mind not all alloys are suitable for use at certain wear points. For example, stainless steel can cause nickel-sulfide stones, while abraded iron and chrome can also create problems if they excessively contaminate the glass. Ultimately, the batch plant contractor must possess extensive knowledge of glassmaking chemistry to avoid selecting improper materials and application designs.
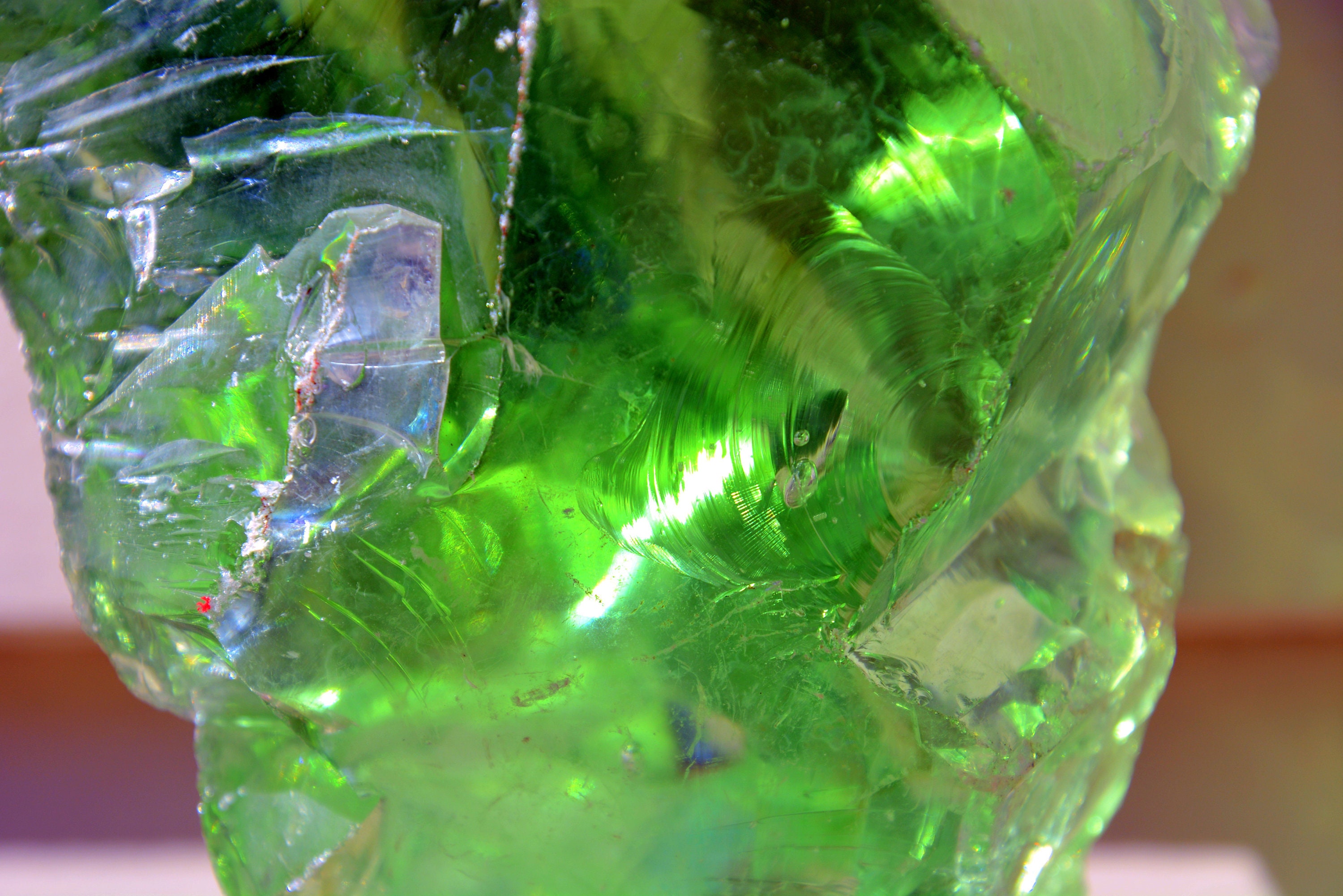