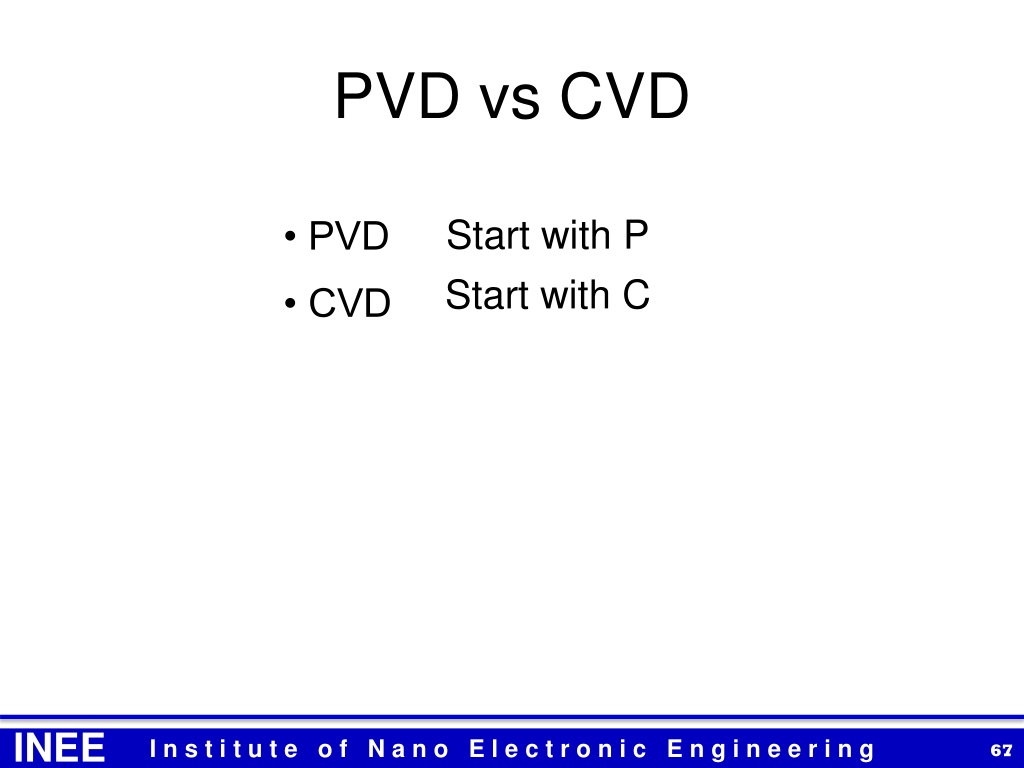
What is the difference between PVD and CVD?
PVD vs CVD
- What are PVD and CVD Processes? PVD and CVD are both highly advanced thin-film coating processes. ...
- Differences between PVD and CVD There are many differences between PVD and CVD coating processes, such as their working mechanisms, operating temperatures, coating substances nature, coating coverage area, film ...
- How to Choose the Right Coating? ...
What's the difference between PVD and DLC?
A comparison most watch lovers will understand is this: PVD is like a hardlex crystal, whereas DLC is like a sapphire one. They both do the same job, but DLC offers a greater, more robust and a better level of scratch proof finish.
What is PVD or IP plating?
“Ion plating (IP) is a physical vapor deposition (PVD) process that is sometimes called ion assisted deposition (IAD) or ion vapor deposition (IVD) and is a version of vacuum deposition. … this basically means that gas metal ions are zapped onto the jewelry to create an extremely tight chemical bond. What is IPS plating?
What does PVD stand for in a watch?
PVD stands for “Physical Vapor Deposition”. PVD is the chemical process where you bind tiny particles to a surface – in this case, watches. More specifically, the process bonds a small layer of metal compounds to the watch. The metals are vaporized, and in that way bound to the surface in layers, using a heated vacuum.

How is PVD different from CVD?
PVD, or physical vapor deposition, is a line-of-sight coating process which allows for thin coatings and sharp edges. CVD, on the other hand, stands for chemical vapor deposition and is thicker to protect against heat. PVD is typically applied to finishing tools, whereas CVD proves best for roughing.
Is PVD better than CVD?
The layer quality of the CVD coating is more resistant to abrasion and wear than PVD coating. CVD coating is also suitable for coating irregularly shaped surfaces such as drill bits, end mills or other threading equipment. It can also be used as a coating to create semiconductor for electrical equipment as well.
What is the main difference between chemical vapor deposition CVD and PVD processes?
Chemical vapor deposition is a highly versatile, popular process that can be modified to a multitude of different applications. The major difference between PVD and CVD is the use of one or more chemical precursors that break down the source material and carry it to the substrate, where it is deposited.
What is the advantage of CVD over PVD?
One of the biggest advantages of using CVD is that it can be used to evenly coat irregular surfaces, including screw threads and recesses. The process is also extremely versatile; it has been used with an extremely wide range of elements and compounds. CVD also produces a thin film with very high purity and density.
Can you remove PVD coating?
The most common method for removing PVD coatings in the past has been media blasting using either sand or dry ice. This aggressive way of knocking off the material is effective but only to a point, as it causes damage to the substrate.
What are the advantages of PVD?
Advantages. PVD coatings are sometimes harder and more corrosion-resistant than coatings applied by electroplating processes. Most coatings have high temperature and good impact strength, excellent abrasion resistance and are so durable that protective topcoats are rarely necessary.
What are the two types of PVD deposition techniques?
Here Are the Three Main Types of PVD CoatingThermal Evaporation. There are two types of thermal evaporation: pulsed laser deposition and electron beam deposition. ... Sputter Deposition. ... Arc Vapor Deposition.
What is CVD used for?
Chemical vapor deposition (CVD) is a deposition method used to produce high-quality, high-performance, solid materials, typically under vacuum.
Which gas is used in CVD process?
Hydrogen gas and inert gases such as argon are flowed into the system. These gases act as a carrier, enhancing surface reaction and improving reaction rate, thereby increasing deposition of graphene onto the substrate. Standard quartz tubing and chambers are used in CVD of graphene.
What are the advantages and disadvantages of the PVD process?
Advantages and Disadvantages of Coating PVD Coating PVD is safer than those methods. Also, coating PVD can be used on almost any type of inorganic material. One disadvantage of coating PVD is higher costs. The process requires complex machines that need skilled operators.
How is CVD done?
Chemical vapor deposition is a process that involves the reaction of a volatile precursor which is injected into a chamber (typically under vacuum). The chamber is heated to a reaction temperature that causes the precursor gas to react or break down into the desired coating and bond to the material surface.
What is a CVD coating?
Chemical vapour deposition (CVD) is a coating process that uses thermally induced chemical reactions at the surface of a heated substrate, with reagents supplied in gaseous form. These reactions may involve the substrate material itself, but often do not.
What are the advantages and disadvantages of the PVD process?
Advantages and Disadvantages of Coating PVD Coating PVD is safer than those methods. Also, coating PVD can be used on almost any type of inorganic material. One disadvantage of coating PVD is higher costs. The process requires complex machines that need skilled operators.
What is CVD coating?
Chemical vapour deposition (CVD) is a coating process that uses thermally induced chemical reactions at the surface of a heated substrate, with reagents supplied in gaseous form. These reactions may involve the substrate material itself, but often do not.
What are the two types of PVD deposition techniques?
Here Are the Three Main Types of PVD CoatingThermal Evaporation. There are two types of thermal evaporation: pulsed laser deposition and electron beam deposition. ... Sputter Deposition. ... Arc Vapor Deposition.
What is the difference between evaporation and sputtering?
E-beam evaporation allows the evaporation of a wider range of metals with higher melting points. Physical sputtering uses ionized gases (Ar) to move material from the target to the substrate.
1. What are PVD and CVD Processes?
PVD and CVD are both highly advanced thin-film coating processes. Both of these processes need vacuum conditions and high temperatures for their working.
2. Differences between PVD and CVD
There are many differences between PVD and CVD coating processes, such as their working mechanisms, operating temperatures, coating substances nature, coating coverage area, film thickness, smoothness of coating, applications, and much more.
3. How to Choose the Right Coating?
After understanding the differences between the 2 coatings, you can learn how to choose the right one for your items in terms of these factors. In the following, I’ll give you some tips.
4. Are you able to remove your PVD and CVD coatings?
No, PVD and CVD coatings do not fall off their own. They are very hard, almost as hard as diamonds, so even scratching them is very difficult.
What is the difference between PVD and CVD?
From their definitions, we can clearly see the difference of PVD and CVD that the former involves evaporation of the material from gas phase to solid phase, while the latter includes chemical reaction. And that’s how they got their names—physical and chemical.
What is PVD in physics?
Definition. Physical vapor deposition (PVD) uses low-voltage, high-current arc discharge technology under vacuum conditions to evaporate the target and ionize the vaporized material and the gas, and finally make the evaporated material and its reaction deposited on the workpiece.
What is PVD in coating?
In recent years, physical vapor deposition (PVD) and chemical vapor deposition (PVD) have wide applications in various industries to increase the hardness of tools and molds or apply beautiful colors to the products. Thus these two methods are considered as the most attractive surface coating technologies. Then, using the example of cutting tools, let’s make a detailed comparison between these two methods.
Why is PVD coating so poor?
Nearly all PVD technologies have poor coating performance both on the back and sides of the tool due to low air pressure. The PVD reactor must reduce the loading density to avoid shadow formation, and the loading and fixing are complicated.
What is a vapor deposition?
Chemical vapor deposition (CVD) refers to a process in which a vapor, containing a gaseous reactant or a liquid reactant constituting a thin film element, and other gases required for the reaction are introduced into a reaction chamber to chemically react on the surface of the substrate to form a thin film.
How thick is CVD?
The CVD coating (about 7.5 μm) on the surface of the tool is thicker than the PVD coating (about 2.5 μm). So it is also a factor to be considered when you are choosing the coating method.
Is PVD a green engineering?
PVD is a kind of “green engineering”, which produces little pollution during the process because it is “physical”. In contrast, the reactive gas and reaction tail gas of CVD may have certain corrosiveness, flammability and toxicity, and there may be powdery and fragmented substances in the reaction tail gas, so certain measures must be taken ...
Chemical Vapor Deposition
Chemical vapor deposition (CVD) is the process by which a deposition material mixes with a precursor substance and then bonds with a substrate. This deposition material can vary by project, while the precursor—often a halide or hydride—is the medium that prepares and transports the deposition material to the substrate or intended surface.
Physical Vapor Deposition
Meanwhile, physical vapor deposition (PVD) is—unsurprising, given its name—deposition by physical rather than chemical means. One of the more popular physical methods, the one Deep Coat uses when vacuum metalizing plastic, is evaporation.
Why is CVD process higher than PVD?
The temperatures required in the CVD process are significantly higher than PVD coating because this method requires a chemical reaction to occur between gases flowed into the chamber and the substrate. High temperatures are required to initiate and maintain these reactions.
What temperature is a plasma chamber heated to?
The chamber is heated to temperatures ranging from 150 – 750°C (302 – 1382°F). The temperature of the chamber is dependent on the coating that is being applied to create an ideal chemical reaction and adhesion between the plasma and substrate. A high current of around 100 A is applied to the metallic material causing an explosive reaction.
What is PVD and CVD?
PVD and CVD are mostly used in the generation of semiconductors where very thin layers of n-type and p-type materials are used to create the required structural junctions. The fundamental difference between the two processes is their approach to addressing the same task.
What are the drawbacks of PVD?
The process does have a few drawbacks. One of the main drawbacks is its high cost, due in part to the intense heating and cooling that is required. PVD is also a ‘line of sight’ technique, which means it is not ideal for coating non-visible surfaces. The process is also considered to be relatively slow.
How is PVD made?
First, a solid precursor material is gasified, typically through the use of high-power electricity or laser. The gasified atoms are then moved into a reacting chamber where the coating substrate is located.
What is CVD in chemical vapor deposition?
Similar to PVD in that it is used to produce high-purity, specialized thin coatings, CVD involves mixing the source material with one or more volatile precursors that functions as a carrier device. These precursors, which are typically halides or hydrides, chemically interact and break down the source material.
Why is CVD used?
Because numerous parts can be coated simultaneously, CVD is a relatively economical deposition process. CVD has been used across a wide range of industries. Some organizations use it to apply coatings for wear resistance and temperature protection. Others use it to produce semiconductors for electronic devices.
What is the CVD process?
The entire CVD process is known to generate volatile by-products that must be safely removed via gas flow through the reaction chamber.
Is PVD a good deposition method?
PVD is used as the deposition method to produce an extremely hard, corrosion-resistant coating. Thin films made with PVD have a high-temperature tolerance and superior ablation resistance. PVD is also considered an environmentally-friendly process. The process does have a few drawbacks.
What is PVD in film?
Definition. Physical vapor deposition (PVD) is a series of vacuum deposition methods used to produce films and coatings. PVD is characterized by a process in which the material changes from a condensed phase to a gas phase and then back to the condensed phase of the film (physical process). The most common PVD processes are sputtering ...
What is PVD process?
The most common PVD processes are sputtering and evaporation. Chemical vapor deposition (CVD) is a vacuum deposition method. In a typical CVD, the wafer (substrate) is exposed to one or more volatile precursors that react and/or decompose on the surface of the substrate to produce the desired deposit. Volatile by-products are also typically ...
What is PVD coating?
Physical vapor deposition (PVD) and chemical vapor deposition (PVD) are considered to be the most attractive surface coating technologies and have a wide range of applications in various industries. Let us compare these two methods in details.
Why is PVD coating so poor?
Nearly all PVD technologies have poor coating performance both on the back and sides of the tool due to low air pressure. The PVD reactor must reduce the loading density to avoid shadow formation, and the loading and fixing are complicated.
Does PVD have a good luster?
The PVD coating well reflects the surface of the tool and has a good metallic luster without grinding. The surface of the CVD coating is slightly rougher than the surface of the substrate. Nearly all PVD technologies have poor coating performance both on the back and sides of the tool due to low air pressure.
Is PVD a green engineering?
PVD is a kind of “green engineering”, which produces little pollution during the process because it is “physical”. The reactive gas and reaction tail gas of CVD may have certain corrosiveness, flammability and toxicity, and there may be powdery and fragmented substances in the reaction tail gas.
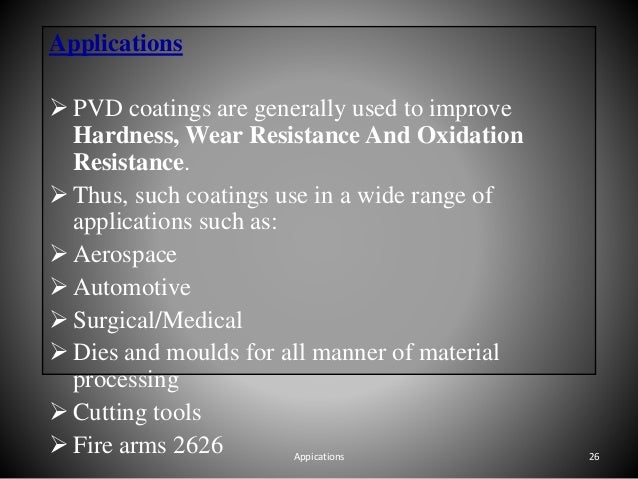