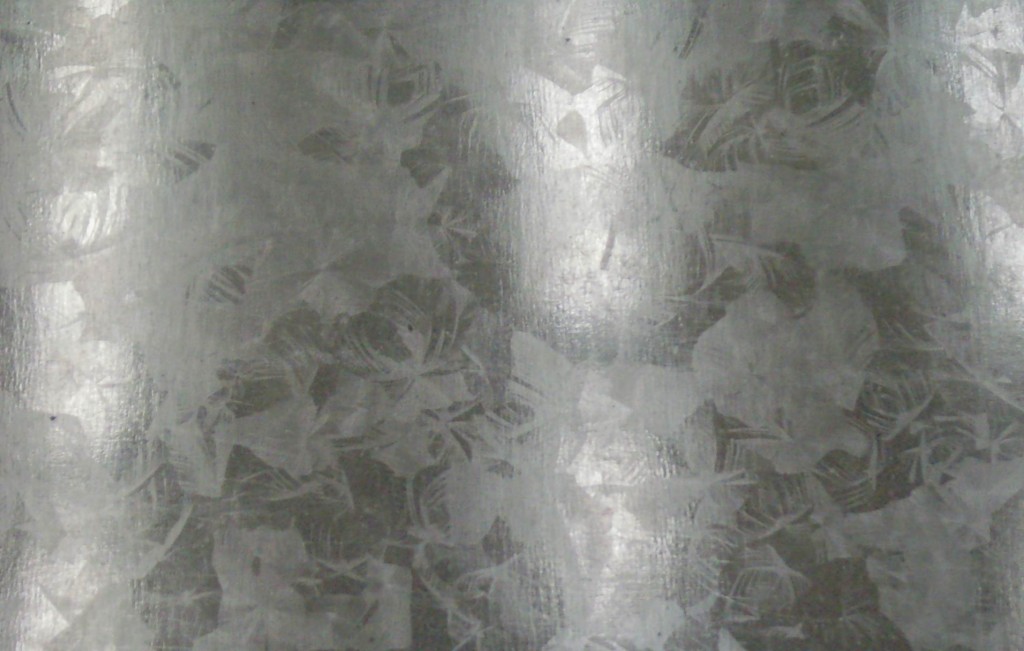
Why do we dip coat?
Plastic Dip Coating is a process that involves immersing a preheated part into liquid Plastisol to form a plastic coating that can add protection and aesthetics to most metal parts. The procedure can enhance the appearance of the part, provide a soft grip, or protect the part from chemicals and abrasion.
What is dip coating metal?
Dip coating is a practical, cost effective method to apply a coating to a variety of metal parts. This coating could provide a protective layer against other materials or possibly prevent corrosion. An example of a dip coated product would be a tool grip/handle.
What products are made by dip coating?
Dip coating and materials For this reason, the dip coating process is used for handles, levers, tools and furniture, as well as electric insulation and outdoor play equipment.
What machine is used for dip coating?
The RDC21 Dip Coater machine is designed for the dip coating of modern liquid resists. Microprocessor controlled with stepper motor drive to meet all possible applications and the design affords smooth vibration free variable speed travel in both directions.
How many types of coating are there?
Coatings are varied, but primarily fall into three categories: Architectural, Industrial, and Special Purpose.
How long does dip coating take?
Allow 4 hours per coat for complete dry. Keep container tightly closed when not in use. When applied properly Plasti Dip can be removed from most surfaces, if desired.
Can steel be dip coated?
A dip coating is very similar to hot dip galvanizing. Hot-dip galvanizing (HDG) is the process of coating iron, steel or ferrous materials with a layer of zinc. This is done by passing the metal through molten zinc at a temperature of 860°F (460°C) to form zinc carbonate (ZnC03).
Can you dip coat aluminium?
The surfaces of aluminium alloys and anodizing layers are sealed with the aid of a dipping varnish. Very even layers are created, even on complex components with internal surfaces such as drill holes or cavities. Sealing the surface increases corrosion resistance and significantly increases alkali resistance.
When was dip coating invented?
1939Among the various wet chemical thin film deposition methods dip coating represents the oldest commercially applied coating process. The first patent based on this process was issued to Jenaer Glaswerk Schott & Gen. in 1939 for sol-gel derived silica films [1].
What is deep coating?
Dip coating refers to the immersing of a substrate into a tank containing coating material, removing the piece from the tank, and allowing it to drain. The coated piece can then be dried by force-drying or baking.
What is Dipcoat primed?
During dipcoat priming, the individual parts are coating through immersion in a paint dip conforming to client specifications. Immersion in two different vats strengthens the opacity of the coating.
Can steel be dip coated?
A dip coating is very similar to hot dip galvanizing. Hot-dip galvanizing (HDG) is the process of coating iron, steel or ferrous materials with a layer of zinc. This is done by passing the metal through molten zinc at a temperature of 860°F (460°C) to form zinc carbonate (ZnC03).
How do you dip metal paint?
1:533:47How to Hydro Dip Using X-O Rust Direct to Metal Metallic PaintYouTubeStart of suggested clipEnd of suggested clipCool be sure to put enough paint in that will cover your entire object because we're going to dip itMoreCool be sure to put enough paint in that will cover your entire object because we're going to dip it into the paint. And then down into the water for the actual. Finish.
Can aluminium be dip coated?
Aluminium coatings can be applied through various methods. The most common is hot dipping, a galvanic coating that uses high temperature baths to create protective coatings. The steel workpiece must be cleaned before hot dipping to ensure that the aluminium atoms will adhere to the surface of the material.
What is cathodic dip coating?
Cathodic dip coating (CDC) – also known as “cataphorisis” – is a proven electrochemical coating process and is used in applications such as the surface coating of car bodies. In the coating process the substrate or item to be painted is immersed in a watery dip coating and used as a cathode.
Introduction
Sarat Kumar Sahoo, ... Narendiran Sivakumar, in Perovskite Photovoltaics, 2018
Chemical solution deposition techniques for epitaxial growth of complex oxides
Dip coating involves immersing a substrate in a precursor solution and then lifting it vertically from the solution with a velocity v0. A wet film with thickness λ is dragged from the liquid upward along with the moving substrate.
Mechanical engineering of solid oxide fuel cell systems: geometric design, mechanical configuration, and thermal analysis
Alireza Mohammadzadeh, ... Mahdi Sharifzadeh, in Design and Operation of Solid Oxide Fuel Cells, 2020
Adhesive Applications and Bonding Processes
Sina Ebnesajjad PhD, Arthur H. Landrock, in Adhesives Technology Handbook (Third Edition), 2015
Graphene Surfaces
Karim Kakaei, ... Ali Ehsani, in Interface Science and Technology, 2019
Application technologies for coating, lamination and finishing of technical textiles
M. Joshi, B.S. Butola, in Advances in the Dyeing and Finishing of Technical Textiles, 2013
The perspective of using nanocatalysts in the environmental requirements and energy needs of industry
Dip-coating technique for the preparation of thin and thick films consists of several consecutive steps. In the first step, the substrate has to be immersed in a solution containing coating material with a constant speed. After remaining inside the solution for some time, the substrate with thin layer of material is pulled up, at a constant speed.
Overview of Dip Coating
Dip coating involves the deposition of a liquid film via the precise and controlled withdrawal of a substrate from a solution using a dip coater. The dip coating process involves a minimum of four unique steps (or stages) followed an optional fifth curing step:
Withdrawal and Film Formation
The withdrawal stage of the dip coating process can be simply seen as the interaction of several sets of forces. These forces can be placed into one of two categories: draining forces and entraining forces. Draining forces work to draw the liquid away from the substrate and back towards the bath.
Viscous Flow and Drainage Regime
The first coating regime is the viscous flow regime. This occurs for high velocities and viscous solutions. Here, the coating is dominated by viscous forces and gravitational attraction. In this case, the thickness of the liquid layer can be given by Equation 1.
Capillary Regime
In the capillary regime, the wet film thickness is not considered. This is because a constant thickness zone is never truly achieved at these coating speeds. In the capillary regime, the final thickness is therefore dependent upon i) the rate of withdrawal, ii) the properties of the solution, and iii) the evaporation rate of the solvent.
Film Thickness vs Withdrawal Speed
The dry film thickness as a function of withdrawal speed requires both the Landau-Levich equation and the capillary regime equation to be used. Figure 5 shows an example withdrawal speed vs film thickness graph for the dip coating process. A minimum thickness for dip coating is achieved during the crossover between these two coating regimes.
Minimum Film Thickness Equations
To determine the minimum thickness, both the equations governing the thickness during the drainage regime and the capillary regime must be combined. The first step in this is modifying Equation 2 to relate the wet film thickness to the dry film thickness. This can be done simply by including the 'materials proportion' constant into the equation.
Troubleshooting Dip Coating Defects
Dip coating defects can broadly be classified into two main categories based on the two main things that dip coating is vulnerable to. These categories are:
Applications in research
The dip coating technique is used for making thin films by self-assembly and with the sol-gel technique. Self-assembly can give film thicknesses of exactly one mono layer. The sol-gel technique creates films of increased, precisely controlled thickness that are mainly determined by the deposition speed and solution viscosity.
Nanoparticle coatings
Dip coating have been utilized for example in the fabrication of bioceramic nanoparticles, biosensors, implants and hybrid coatings. For example, dip coating has been used to establish a simple yet fast nonthermal coating method to immobilize hydroxyapatite and TiO2 nanoparticles on polymethyl methacrylate.
Sol-gel technique
Dip coating of inorganic sols (or so-called sol-gel synthesis) is a way of creating thin inorganic or polymeric coatings. In sol-gel synthesis the speed of deposition is an important parameter that affects, for example, layer thickness, density and porosity.
Providing Innovative Solutions for Your Business
With over 30 years' experience in the industry and a highly skilled team, Precision Dip Coating is committed to providing innovative solutions to all your coating needs. Our in house Engineering and development team are committed to turning your ideas into a reality.
What Is Plastic Dip Coating?
Plastic Dip Coating is a process that involves immersing a preheated part into liquid Plastisol to form a plastic coating that can add protection and aesthetics to most metal parts. The procedure can enhance the appearance of the part, provide a soft grip, or protect the part from chemicals and abrasion.
The Plastic Dip Coating Process
The part is pretreated (that is, the cleaning and the application of a primer if desired).
Call Us Today!
For more information on Plastic Dip coating, contact us, we will advise you on the best service for your product. With Precision Dip Coating, you are assured of the best quality because we adhere to industry standards and are committed to customer satisfaction.
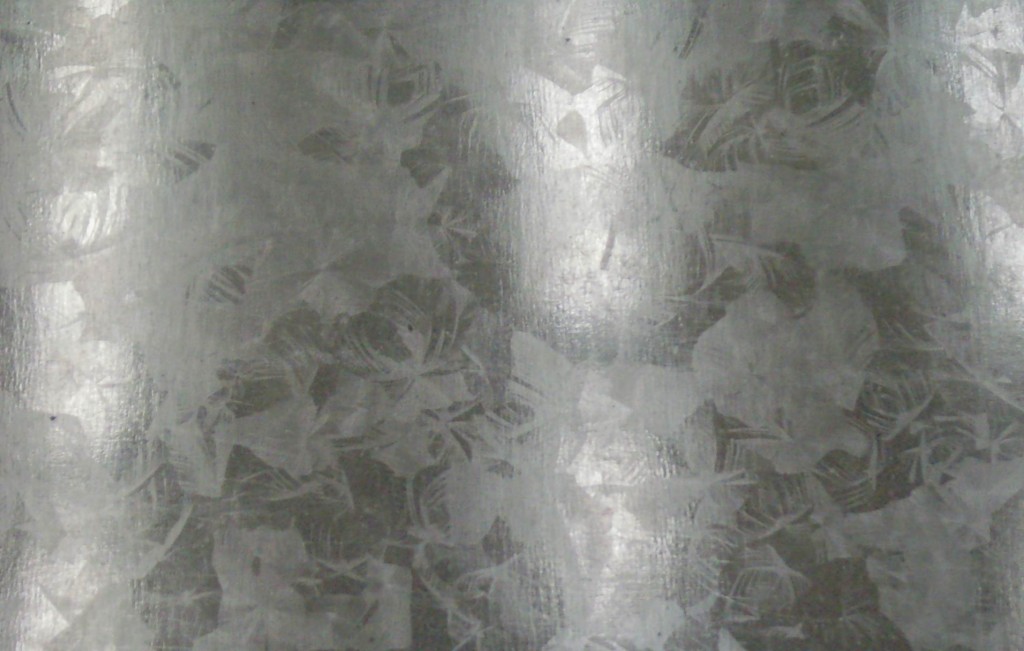