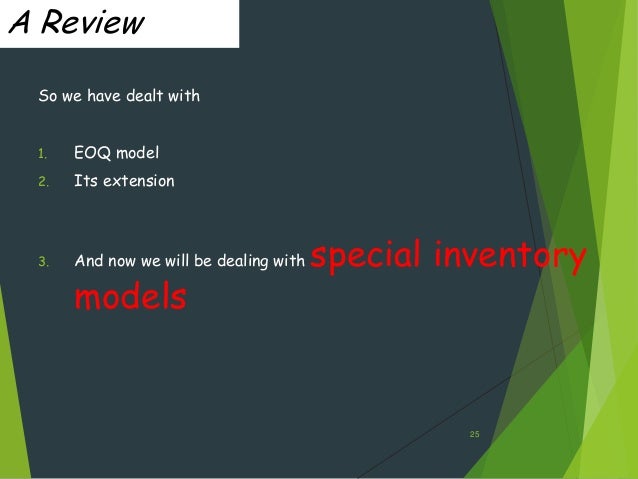
What is the EOQ method?
Economic Order Quantity, or EOQ, is about ordering the ideal quantity of inventory with the lowest associated overhead costs, such as order costs, shortage costs, and holding costs to a business. The EOQ method is mainly used as an inventory management technique that seeks to balance out inventory holding costs with inventory set-up costs.
How to calculate economic order quantity (EOQ)?
The economic order quantity formula
- Q = The number of EOQ units
- D = Annual demand you get for a product
- S = Order cost, or “setup cost,” which is how much one order costs per purchase
- H = Holding costs, or “carrying costs,” which is the total cost of holding inventory
How to implement effective inventory management procedures?
Effective stock control and inventory management tips involve both practices and tools. These include wisely and accurately labeling items, their statuses, monitoring stock levels, and setting thresholds with the help of digital tools. Managing inventory is a crucial aspect of business operations.
What does EOQ mean?
Economic order quantity (EOQ) is the order size that minimizes the sum of ordering and holding costs related to raw materials or merchandise inventories. In other words, it is the optimal inventory size that should be ordered with the supplier to minimize the total annual inventory cost of the business.
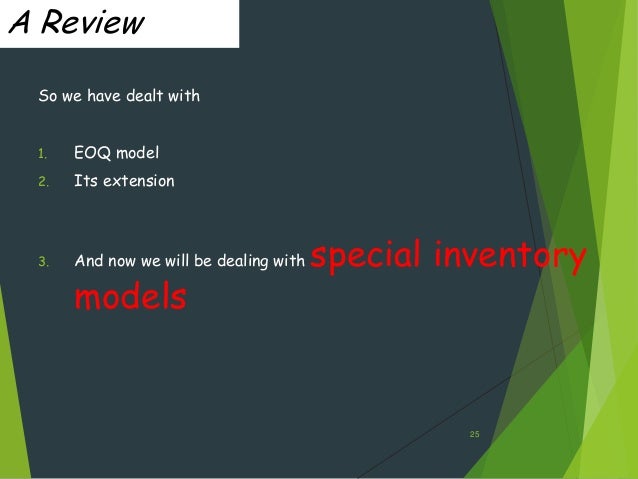
What is the EOQ model?
Economic order quantity (EOQ) is the ideal order quantity a company should purchase to minimize inventory costs such as holding costs, shortage costs, and order costs. This production-scheduling model was developed in 1913 by Ford W.
What is the importance of EOQ in inventory management?
The economic order quantity calculation helps businesses and organizations have a consistent supply of inventory so that they can avoid any shortage costs. When using EOQ, companies understand how much inventory they need to order and the frequency of their shipments to ensure they always have goods in stock.
What is EOQ and its formula?
The EOQ formula is as follows. EOQ = Square root of [(2 x demand x ordering cost) / carrying cost] Demand. The demand remains constant according to the assumptions made by EOQ. The demand is how much inventory is used per year or how many units are sold per year.
What is EOQ in simple words?
The Economic Order Quantity (EOQ) is the number of units that a company should add to inventory with each order to minimize the total costs of inventory—such as holding costs, order costs, and shortage costs.
What is the objective of EOQ?
Its objective is to determine the optimal (i.e., lowest cost) production or purchase order quantity based on the tradeoff between setup and holding costs.
Why EOQ is calculated?
Why do you need the Economic Order Quantity formula? The Economic Order Quantity (EOQ) formula helps to avoid these mis-stocking situations. It calculates the ideal number of units you should order, such that the cost involved is minimal and number of units is optimal.
How is EOQ ordering cost calculated?
Number of orders = D / Q D = Annual quantity demanded. Q = Volume per order. Annual Ordering Cost.
How is total cost of EOQ calculated?
As a formula: TC = PC + OC + HC, where TC is the Total Cost; PC is Purchase Cost; OC is Ordering Cost; and HC is Holding Cost.
Why is there 2 in EOQ?
What does it mean? The numerator and denominator of the equation are multiplied by two to remove the division by “2” within the denominator. There is now a constant of “2” in the numerator: (2* Cost of Reordering * Annual Demand) ÷ (Cost of Carrying Inventory * Unit Cost).
How do you calculate order size?
Order Quantity Formula To calculate the optimum order quantity "Q," take the square root of the following: "2N" multiplied by "P" and divided by "H." "N" is the number of units sold per year, "P" is the cost to place one order and "H" is the cost of holding one unit of inventory for one year.
What are the limitations of EOQ model?
The limitations of the formula makes it almost impossible to account for businesses that are particularly sensitive to events such as changing consumer demand, unpredictable seasonal changes in inventory, or discounts a company can leverage by buying inventory in larger quantities.
Who developed economic order quantity model?
Ford Whitman HarrisFord Whitman Harris first presented the familiar economic order quantity (EOQ) model in a paper published in 1913. Even though Harris's original paper was disseminated widely, it apparently was unnoticed for many years before its rediscovery in 1988.
What is the formula of total cost?
Consequently, total cost is fixed cost (FC) plus variable cost (VC), or TC = FC + VC = Kr+Lw.
How do you solve EOQ problems?
EOQ formula Multiply the demand by 2, then multiply the result by the order cost. Divide the result by the holding cost. Calculate the square root of the result to obtain EOQ.
What is average inventory formula?
You can calculate your average inventory by adding your beginning period inventory and ending period inventory, then dividing that total by the time period.
What is EOQ PDF?
In stock management, Economic Order Quantity (EOQ) is an important inventory management system that demonstrates the quantity of an item to reduce the total cost of both handling of inventory (Handling Cost) and order processing (Ordering Cost).
ECONOMIC ORDER QUANTITY (EOQ) MODEL
The economic order quantity (EOQ) is the order quantity that minimizes total holding and ordering costs for the year. Even if all the assumptions don’t hold exactly, the EOQ gives us a good indication of whether or not current order quantities are reasonable.
Same Problem
Pam runs a mail-order business for gym equipment. Annual demand for the TricoFlexers is 16,000. The annual holding cost per unit is $2.50 and the cost to place an order is $50. What is the economic order quantity?
How are ordering costs related to inventory carrying costs?
The ordering costs are inversely related to the inventory carrying costs, i.e. the lower the carrying costs, the higher the ordering costs.
How is total inventory cost calculated?
It is calculated so that total inventory costs are at a minimum for that particular stock item. Total inventory costs for an item of stock are computed for a given period usually an accounting year by combining the costs of ordering and the costs of carrying that item.
What are the assumptions of the EOQ model?
Assumptions of the EOQ Model. To be able to calculate a basic EOQ certain assumptions are necessary. Demand for a product should be constant over the year. This assumption is rarely satisfied in practice. However, the model produces good results where demand is relatively stable over time.
What is the main objective of managing inventory?
The major objective of managing inventory is to discover and maintain the optimum level of investment in inventory. The optimum level will be that quantity which minimizes the total costs associated with inventory.
What is carrying cost?
Carrying cost refers to the cost of holding stocks in storage over a period of time. It includes: Storage costs (rent, lighting, heating, refrigeration, etc). Stores staffing, equipment maintenance, and running costs. Handing costs. Audit, stock taking or perpetual inventory costs.
What is the second major decision in dealing with cost of goods available for sale?
The second major decision in dealing with cost of goods available for sale is when to order . The reorder level is the quantity level of the inventory on hand that triggers a new order. The reorder level is simple to compute:
What is the first major decision in managing goods for sale?
The first major decision in managing goods for sale is deciding how much of a given product to order. A firm can use the Economic Order Quantity (EOQ) procurement model to calculate the optimal quantity of inventory to order.
What is EOQ?
Economic order quantity is the ideal quantity of an inventory item that companies should purchase to minimize the inventory's overall cost, including:
What is economic order quantity?
Economic order quantity (EOQ) is a helpful formula companies and businesses use to help increase the efficiency and effectiveness of their inventory management. If you're hoping to reduce your inventory expenses and avoid shortage costs, it's important to understand what EOQ is and how it can help you. In this article, we discuss what EOQ is, why it's important and how to calculate it using a helpful formula, list of steps and informative examples.
What are the costs of shortage?
Shortage costs: Shortage costs occur when a business or organization doesn't have the inventory in stock to satisfy current customer demand. The costs that occur during an inventory shortage can include a loss in potential profit and expensive overnight shipping.
Why do companies use EOQ?
When a business uses the EOQ calculation to order the right amount of inventory and decrease their inventory expenses, they often have extra cash to invest in other company departments or projects, such as product development, marketing or customer service. Investing additional money into other areas of a company can help the company develop and generate more revenue by increasing customer outreach and satisfaction.
Why do businesses use economic order quantity?
The economic order quantity calculation helps businesses and organizations have a consistent supply of inventory so that they can avoid any shortage costs. When using EOQ, companies understand how much inventory they need to order and the frequency of their shipments to ensure they always have goods in stock. Having a consistent inventory supply also helps businesses increase customer satisfaction by meeting consumer demands. When a store or company has the products that a customer wants, they're more likely to buy from that company again.
How many units of inventory should Francine order?
Whenever Francine orders more gear-shift bikes, she should order approximately 89 units of inventory to ensure she meets consumer demand and minimizes inventory costs.
What is holding costs?
Holding costs: Holding costs are expenses that a company accumulates while in possession of their inventory. Holding costs can include damaged goods and the price of the storage facility, labor and insurance.
How Is the Economic Order Quantity Model Used in Inventory Management?
Information on fifteen items comprised of 10 non-seasonal and 5 seasonal items was collected from a supermarket in Ikot Ekpene town, Nigeria. The information includes the quantity of daily sales, the unit price, the lead time and the number of times an item is ordered in a month.
What are the main problems with a JIT (just in time) production strategy?
The model implementation is next presented using some numerical examples and finally the performances of the proposed GA and MA are compared using two statistical tests and a simple additive weighting method. The results show that GA has better performance than MA in terms of average objective function value and average run time using the two comparison procedures.
What the Economic Order Quantity Can Tell You?
Based on this information, a simple moving average and y-trend method of forecasting were used to forecast the sales quantity for the following month for the non-seasonal and seasonal items. Different scenarios were created to simulate the fuzzy logic EOQ after which the result of the conventional method, EOQ method, and fuzzy EOQ methods were obtained and compared. It was revealed that if the EOQ method is adopted, savings of 43% of holding and carrying cost would be made.
What is EOQ in inventory?
EOQ is an attempt to balance inventory holding or carrying costs with the costs incurred from ordering or setting up machinery. The total cost will minimized when the ordering cost and the carrying cost equal to each other. While customer order a significant quantities of products, cycle inventory would be able to save cost and act as a buffer for the company to purchase more supplies.
What is EOQ model?
The EOQ model assumes steady demand of a business product and immediate availability of items to be re-stocked. It assumes fixed costs of inventory units, ordering charges and holding charges. This inventory model requires continuous monitoring of inventory levels.
Why is XYZ using inventory control?
It is highly recommended that Company XYZ implements the inventory control model provided in order to reduce stock out and back orders. By doing so, the company could also reduce the total cost associated with their inventory. If the methods are used effectively, the company could remain competitive among their industry.
What is an EOQ?
The objective of the economic order quantity (EOQ) model is to minimize the total costs associated with the carrying and ordering costs as the mount ordered gets larger, average inventory increases and so do carrying costs. For example, if annual demand for an inventory item is 26,000 units, and a firm orders 500 each time, the firm will place 52 [26,000/500] orders per year. This order frequency gives the organizations an average inventory of 250 [ 500/ 2] units. If the order quantity is increased to 2,200 units, fewer orders [26,000 / 2,000] will be placed.
What is a reorder level?
Reorder Level (RL): Reorder level is the stock level, at which an alert is set off promptly to renew that specific inventory management models. Reorder level is characterized, keeping into thought the Safety Stock to stay away from any stock-out and Average Lead Time Demand on the grounds that even subsequent to raising the caution, it would take one complete interaction cycle (Lead Time) till the new inventories show up to recharge the current inventory.
What is EOQ in eCommerce?
Utilizing deterministic inventory management models – like the Economic Order Quantity (EOQ) model – will assist you with processing an ideal request amount that limits stock expenses (and keep away from the most dreaded part of eCommerce). The EOQ is a recipe that figures the most prudent number of things a business should request to limit costs and boost esteem when reloading stock.
What is a fixed reorder quantity?
Fixed Reorder Quantity System is an Inventory Model, where an alert is raised promptly when the inventory level dips under a fixed amount and new orders are raised to renew the inventory to an ideal level dependent on the interest. Where the inventory is requested for recharging is named as Reorder Point. The inventory amount at Reorder Point is named as Reorder Level and the amount of new inventory arranged is alluded to as Order Quantity.
What is EOQ model?
In any case, the EOQ model expects a (consistent) request of an item and prompt accessibility of things to be restocked. It does not represent occasional or economic fluctuations. It expects fixed expenses of inventory units, requesting charges and holding charges. No stockouts are allowed.
What are the three inventory management models?
Three of the most popular inventory management models are Economic Order Quantity (EOQ), Inventory Production Quantity and ABC Analysis.
What is the viability of the essential EOQ model?
The viability of the essential EOQ model is generally restricted by the presumption of a one-item business, and the recipe does not permit communication between items. Also, EOQ accepts a boundless arranging skyline and that there is no restriction on capital availability. #2. Inventory Production Quantity.
Why is inventory management important?
The significance of inventory management models is in the exactness it gives. You can discover which items are selling and which ones are not, which things you need to have available and explicitly what amount is required. Also, when you know these subtleties, you can lessen operational costs, lower stockpiling expenses and set aside your business cash.
What is EOQ?
EOQ, Economic Order Quantity, is a way businesses realize the quantity of stock they should order upon purchase.
Why is EOQ used?
This is because the Economic Order Quantity shows businesses a cost-effective way of purchasing that doesn’t use up extra costs and also ensures stock is readily available to meet the demand of the business.
What does EOQ stand for?
EOQ stands for Economic Order Quantity. Economic Order Quantity is calculated by businesses to have a better understanding of what quantity of purchase will be the most cost-effective for them.
What does Fenson use to make guitars?
Fenson uses wood to manufacture acoustic guitars. The manager of Fenson wants to know the optimal amount of wood she should order. This can be known using EOQ. To enable that, the manager acquires data to be used in the EOQ formula.
What is ERP software?
ERP Software is used by businesses to manage better, streamline operations under a business, and smoothen communications between departments.
What is the holding cost of inventory?
Holding Cost/Unit (H): Holding Cost/Unit refers to how much it costs to store the particular item in the order. The holding cost of inventory is an important item for using Economic Order Quantity in cost accounting as it tells how much it costs to store a single item of inventory .
What is setup cost?
Ordering (Setup) Cost (S): Ordering cost is how much ordering a purchase costs. This includes shipping and handling costs. Setup cost is per order, for example, if setup cost is $5, this means each order has the setup cost of $5.

Economic Order Quantity (EOQ) Model
What Is The EOQ Model?
- Cost Minimizing “Q”
- Assumptions:
What Would Holding and Ordering Costs Look Like For The years?
- A = Demand for the year Cp = Cost to place a single order Ch = Cost to hold one unit inventory for a year
Total Relevant* Cost
- Yearly Holding Cost + Yearly Ordering Cost * “Relevant” because they are affected by the order quantity Q Economic Order Quantity (EOQ)
Same Problem
- Pam runs a mail-order business for gym equipment. Annual demand for the TricoFlexers is 16,000. The annual holding cost per unit is $2.50 and the cost to place an order is $50. What is the economic order quantity? Related Tutorials 1. Introduction: Inventory Management Models : A Tutorial 2. Independent vs Dependent Demand Inventory Systems Tutorial – An Example of Inv…