
What is end milling cutters?
End mills are versatile milling cutters used to machine slots, profile, cavities, and more features, a drill bit is used to cutting or producing round holes 3. End mills can also be used to machine a hole, but it requires an already drilled hole, you can use a drill bit working with the material directly for processing a hole. 4.
What are the different types of milling cutters?
The most common types of milling cutters are: First, we should start with one of the primary questions. What is the difference between end milling and face milling? These are two of the most prevalent milling operations, each using different types of cutters – the and mill and the face mill.
What is successful hole milling?
What is successful milling? When milling a hole, linear ramping (2-axes simultaneously) is always preferred to peck milling. Peck milling is an alternative hole milling method, but it often produces long chips and generates undesirable cutting forces on the cutter.
What is a CNC milling cutter?
Milling cutters, or endmills, are used in a CNC machine: Computerised Numeral Controlled. Specialised software is used to send automated milling instructions or a ‘toolpath’ to the machine which then cuts away a design in your stock material.
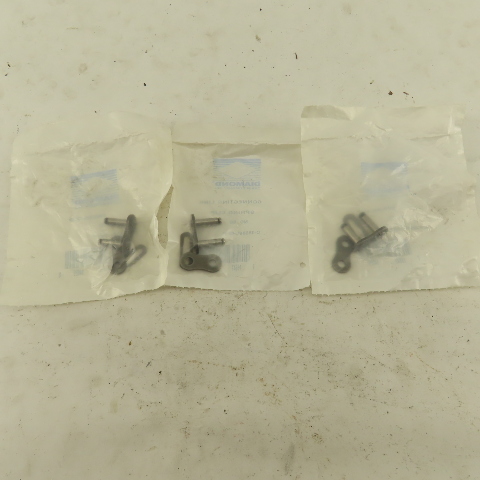
What is a hole mill?
A Hole-mill is normally an undersized reamer with a boring geometry i.e. the size of the hole-mill is normally 0.2-0.6mm more than the size of the drill so that there are no drill marks on the hole plus the hole axis is corrected for subsequent reaming operation.
What is the use of hole mill?
Overview: A Hole mill is normally used prior to the reaming operation to correct the axis of the pre-hole. It acts like a multi point boring tool for axis correction. A hole mill also maintains the stock necessary for reaming.
What are the 3 types of milling cutters?
The most common types of milling cutters are:End mill.Face mill.Ball cutter.Slab mill.Side-and-face cutter.Involute gear cutter.Fly cutter.Hollow mill.More items...•
What is the difference between hole mill and end mill?
There are a number of significant differences between an end mill and a drill bit. The most obvious one is their function. A drill bit is designed to bore straight down into the material – metal, plastic, or wood – whereas an end mill is designed for sideways cutting. The two cannot be interchanged.
What is a hole making tool?
Drilling and drill bits are most commonly associated with hole making tools. They provide a quick, easy, and economical way to produce machined holes. Drill bits work by entering the workpiece axially and then cutting a through-hole or blind hole with a diameter equal to the tool's.
How are holes machined?
Today, hole machining is carried out using drills (solid carbide, with replaceable plates or with soldered carbide plates – figure 3). Different tools offer varying machining accuracy. Monolithic tools usually provide better accuracy and less roughness of the machined hole surface.
What is the name of milling cutter?
Following are the types of milling cutters that we use in different milling machines: Roughing end mill. Slab mill. End mill cutter.
What is cutter used for?
Cutters are designed to cut materials of different kinds of products such as wires, cables (electrical, coax, multi-strand), wire ropes, fencing, bolts, rods, pre-stressed concrete wires, and strapping.
What is the classification of milling cutter?
Types of Milling Cutter Ball cutter. Slab mill. Side-and-face cutter. Involute gear cutter.
Why is it called an end mill?
It is distinguished from the drill bit in its application, geometry, and manufacture. While a drill bit can only cut in the axial direction, most milling bits can cut in the radial direction. Not all mills can cut axially; those designed to cut axially are known as end mills.
What is difference between milling and drilling?
The main difference between Milling vs. Drilling is that drilling is a process of making a hole into a solid surface. While, milling is a process where you create features like slots, walls, fins, webs, etc.
Can you drill holes with a mill?
Specialized drilling and boring tools do a fine job making accurate holes. Increasingly though, shops are successfully using interpolated milling cutters to drill and bore blind and through-holes. Usually this operation is performed with end mills.
What is hole milling and tapping operations?
Tapping is the operation of cutting internal threads in a hole using a cutting tool called Tap. A tap has cutting edges in the shape of threads. When the tap is screwed into a hole it removes metal and cuts internal threads for tapping the hole. drilled will be smaller than the tap size.
What is milling machine?
A milling machine removes material from a work piece by rotating a cutting tool (cutter) and moving it into the work piece. Milling machines, either vertical or hori- zontal, are usually used to machine flat and irregularly shaped surfaces and can be used to drill, bore, and cut gears, threads, and slots.
Which of the following is used to produce holes?
Detailed Solution. Drilling is an operation to produce a cylindrical hole in a workpiece. The tool used in called “drill bit”.
What is the process of creating holes in a workpiece?
What Is Drilling? Drilling is a cutting process that involves the use of a drill bit to cut a circular-shape hole in a workpiece. The drill bit used in drilling is a type of rotary cutting tool that, like other rotary cutting tools, rotates while subsequently scraping material out of the workpiece.
What is the difference between end milling and face milling?
The difference between end milling and face milling is that an end mill uses both the end and the sides of the cutter, whereas face milling is used for horizontal cutting.
What is milling centre?
It is a process where rotary cutters remove material, which makes it the opposite of CNC turning. The milling centres do not just perform the cutting automatically, but also the changing of tools. During the average process of creating a finished product from a block of metal, for example, various tools are used.
What is an end mill?
End mill. These tools usually have a flat bottom but not always. Round and radiused cutters are also available. End mills are similar to drills in the sense that they can cut axially. But the advantage for milling lies with the possibility of lateral cutting.
What is slab milling?
Slab mills are not that common with modern machining centres. Rather, they are still used with manual milling machines to quickly machine large surfaces. That is also why slab milling is often called surface milling.
Why are cut bits of metal smaller than usual?
The cut bits of metal are smaller than usual and therefore easier to clear. Multiple teeth come into contact with the workpiece at the same time. This reduces chatter and vibration, which could otherwise be larger because of the jagged teeth.
What is a side and face cutter?
A predecessor for the end mill. Side-and-face cutters have teeth around the circumference as well as on one side. This makes the functionality very similar to end mills but their popularity has waned over the years with the advancement of other technologies.
What is a hollow mill?
Hollow mills are basically the opposite of face mills. Here, the workpiece is fed into the inner part of the mill to produce a cylindrical outcome.
What is a hole mill?
A Hole-mill is normally an undersized reamer with a boring geometry i.e. the size of the hole-mill is normally 0.2-0.6mm more than the size of the drill so that there are no drill marks on the hole plus the hole axis is corrected for subsequent reaming operation.
What is the tolerance zone of a carbide drill?
Modern solid carbide drills produce holes in a tolerance zone of H8-H10; in which case the hole axis is accurate in half this tolerance. For eg:- A dia 10 hole drilled hole is between 22-45 microns which means the axis is controlled within 11-22 microns.
What is an Aayudh hole mill?
Aayudh Hole-mills are optimised for geometry based on the materials to be hole-milled and are generally straight fluted.
What is a milling tool?
The milling cutter has an important part of the milling machine. A milling tool is a rotating tool having one or more teeth for milling.
Significance of milling tools
In a typical milling operation, the tool in the milling machine moves perpendicular to its own axis, so that it can remove excess material from the workpiece around the tool.
Types of milling tools
In order to make milling a general machining process, there are a variety of milling cutters available on the market.
Selection principle of milling cutter
The selection of milling cutter diameter varies greatly due to different products and production batches.
In Conclusion
Whether we choose milling cutter on CNC milling machine or ordinary milling machine, we should comprehensively consider the milling material and hardness and the specifications of milling cutter, such as edge length, tool length, edge diameter, shank diameter, etc.
What is the fastest method of producing a hole?
Drilling is the traditional and fastest method of producing a hole, but chip breaking can be a challenge in some materials, and it lacks the flexibility to produce varying diameters and non-round shapes.
What is a Peck mill?
Peck milling is an alternative hole milling method, but it often produces long chips and generates undesirable cutting forces on the cutter.
Why avoid machining all the way against a 90° shoulder?
Note: Avoid machining all the way against a 90° shoulder because the effect of a low approach angle will be lost, i.e. the depth of cut increases dramatically.
Do you need a starting hole for internal shoulder milling?
Internal shoulder milling and plunge milling require a starting hole and should be compared to ramping a cavity directly into a solid block.
Is it better to drill or mill a hole?
Boring is normally the fastest method, for the same reasons as drilling, but hole milling is sometimes a good alternative. Two alternate milling methods can be used: circular ramping (3-axes) or circular milling (2-axes). Circular ramping is preferred when the hole is deeper than ap max, or in vibration sensitive applications. In addition, the roundness/concentricity of the hole becomes better when ramping, especially with long overhangs. Roundness will be improved if the workpiece is rotated instead of moving the milling cutter in a circular path in both circular ramping and milling operations.
What are 2 flute end mills for?
Two flute end mills are known as slot drills. They are primarily used for milling slots or pockets.
What is an end mill used for?
For an extremely basic answer, an end mill is rotated in the spindle of a milling machine and moved against a piece of material (metal or otherwise) and the rotating ‘blades’ on the edge of the tool will slice away material to produce the desired form or shape.
Can you drill with an end mill?
If it has cutting edges on the bottom face, yes, you can drill with an end mill.
What is a down cut end mill?
A down cut end mill is when the spiral of the side flutes is raked forward. This forces the material being removed downward. These types of tools are primarily used on softer materials such as wood and plastic.
How can you tell if an endmill is center cut?
The cutting edges on the bottom face will extend all the way to the center.
How many flutes do you need for milling steel?
There is no specific requirement for a certain amount of flutes for milling steel. The amount of flutes can dictate what abilities the tool may have that make it better for specific operations.
Is aluminum easier to mill than steel?
Yes, it’s a lot easier. Although trying to mill poor quality aluminum can be frustrating. The aluminum you can buy at the local big box store is not ideal for machining. It is typically gummy and clogs up and breaks end mills. It is too soft and only useful for fabrication etc.
What is a square endmill?
Square endmills can be used in the roughing or finishing stage. – Bull-nose end mills: also called corner radius end mills, this type of cutter is a combination of fishtail and ball-nose, also a flat bottom but with rounded corners. Bull-nose end mills are often used to mill molds (plastic injection molds, die cast molds, etc.) 2.
What is a fishtail end mill?
– Square end mill: also known as flat end mills, are general-purpose mills that generate flat-surfaced cuts with perfect 90° corners in the workpiece, involves milling operations like side milling, face milling, and more.
What is CNC milling?
Highly automated milling is a versatile machining process that is capable of producing components in almost any shape. There are a wide variety of CNC milling operations adopted for different manufacturing purposes. End milling mainly differs from other processes due to the type of tooling it is used for cutting materials. In this article, we’ll outline the types of end mills, what is end milling, and also figure out the difference between end mill and drill bit.
What materials are used in an end mill?
High-speed steel (HSS) and tungsten carbide are two of the most common materials for making the end mill. End mills allow precision cutting to manufacture milled parts for broad applications, including jewelry, sign making, mold making, circuit boards, wood engravings, machine parts, and more. Endmills are available in varying lengths, diameters, ...
What is a V bit end mill?
The v-bit end mill comes in two forms- 60°or 90°V-bit. – Fishtail end mill: with cutting edges on one end, which may be much thinner than the other end, fishtail end mills can plunge directly into your material and produce a flat surface, prevent any splintering or breakout, create clean edges on thin material and make pockets with flat bottoms, ...
Which direction do rotary end mills cut?
1. Rotary end mills cut side to side or in the horizontal direction, lots of mills can cut both axially and laterally, while drill bits that plunged directly into the material only move up and down and cut in vertically.
Can you use an end mill to machine a hole?
3. End mills can also be used to machine a hole, but it requires an already drilled hole, you can use a drill bit working with the material directly for processing a hole.
What is a CNC Machine?
Milling cutters, or endmills, are used in a CNC machine: Computerised Numeral Controlled.
Should I Use Carbide End Mills or HSS End Mills?
Most end mills are manufactured from either cobalt steel alloys – referred to as HSS (High Speed Steel), or from tungsten carbide.
Why use an endmill and not a drill bit?
So why use an Endmill and not a drill bit? In short, a drill bit moves up and down, an end mill moves side-to-side ( Note: there are endmills available that move in all directions).
What is an end mill?
End mills are the cutters of the milling world and are used for slotting, profiling, contouring, counter-boring, and reaming. 4. End mills allow for precision parts to be cut, anything from machine parts, jewellery designs, wood engravings, sign making, plastic cutting, mold making and circuit boards.
Why do endmills have chemical coatings?
Endmills with added chemical coatings are also popular today. Often more expensive, these coatings are added to the bit to reduce wear and friction. However, not all coatings are suitable for all materials and whilst a particular coating may be good for productivity on one material, it may be not be on another.
What is 4 flutes?
4 flutes are used on most other materials, can cut harder materials than 2 flutes and will create an overall smoother surface finish.
How many flutes does an end mill have?
End Mills have either 2, 3 or 4 flutes per bit. 2 and 4 flutes are the most popular.
What is an undercutting end mill?
Undercutting end mills, also known as lollipop cutters or spherical ball end mills, are a common choice for machining undercuts. An undercut is a common part feature characterized by one part of a workpiece “hanging” over another. Undercuts are typically difficult, or even impossible, to machine with a standard tool, especially on 3-axis machines.
What angle is used for deburring?
Deburring & Edgebreaking. Since undercuts have a wrap angle that is greater than 180°, they are very well-suited to deburring or edgebreaking anywhere on your workpiece, including the underside. Deburring your parts by hand can be inefficient for your shop – using an undercutting end mill instead will save you time and money.
What is the best angle for a wrap tool?
Exactly what tool to use depends on the geometry of the feature and the part. These tools are available with a range of wrap angles like 220°, 270°, and 300°. Greater wrap angles are the result of a thinner neck and create a more spherical cutting end. This style offers more clearance at the cost of rigidity. Likewise, undercutting end mills with lower wrap angles sacrifice clearance for greater rigidity.
What is reduced shank tool?
Reduced shank tools offer the most versatility in complex contouring and profiling operations. The ability to chuck these tools at any depth means that they are capable ...
What is the best angle for slotting?
Since only 180° of the cutting end can be used to slot, undercutting end mills with lower wrap angles and thicker necks are best suited to slotting. However, high helix undercutting tools may be ideal if improved finish and increased chip removal are important to the operation.
What is Harvey Performance Company?
Harvey Performance Company’s team of engineers works together to ensure that your every machining challenge – from tool selection and application support to designing the perfect custom tool for your next job – is rectified with a thoughtful, comprehensive solution.
Can you use an undercutting mill for slotting?
Most machinists might not think of undercutting end mills for slotting, but they are fully capable of this operation. An equivalent slot can be machined with a regular ball end mill, but doing so might not be feasible due to clearance issues – an undercutter has a reduced neck, unlike a standard ball end mill. Additionally, using an undercutter to slot can save time switching to an equivalent ball end mill.

What Is A Milling Tool?
- The milling cutter has an important part of the milling machine. A milling tool is a rotating tool having one or more teeth for milling. During operation, each cutter tooth intermittently cuts off the rest of the workpiece. The milling cutter is mainly used for milling plane, step, groove, forming surface, cutting workpiece, etc.
Significance of Milling Tools
- In a typical milling operation, the tool in the milling machine moves perpendicular to its own axis, so that it can remove excess material from the workpiece around the tool. A milling machine is a widely used machine, which can perform a variety of machining operations. Milling machines are used to process and manufacture parts of various shapes and sizes. Milling cutter is a necessar…
Types of Milling Tools
- In order to make milling a general machining process, there are a variety of milling cutters available on the market. These milling cutters are manufactured in various sizes, shapes and materials. Some milling cutters are made of high-speed steel (HSS), while others are carbide tips.
Selection Principle of Milling Cutter
- 1. Selection of milling cutter diameter
The selection of milling cutter diameter varies greatly due to different products and production batches. The choice of tool diameter mainly depends on the specification of the equipment and the machining size of the workpiece. Plane milling cutter When selecting the diameter of face mi… - 2. Selection of milling cutter blade
a. For finishing. It is best to use a grinding blade. This kind of blade has good dimensional accuracy, so milling is the positioning accuracy of cutting edge, which can obtain better machining accuracy and surface roughness. b. For rough machining, it is best to use pressing bl…
in Conclusion
- Whether we choose milling cutter on CNC milling machine or ordinary milling machine, we should comprehensively consider the milling material and hardness and the specifications of milling cutter, such as edge length, tool length, edge diameter, shank diameter, etc. High speed steel milling cutters are usually suitable for ordinary milling machines, while cemented carbide cutter…