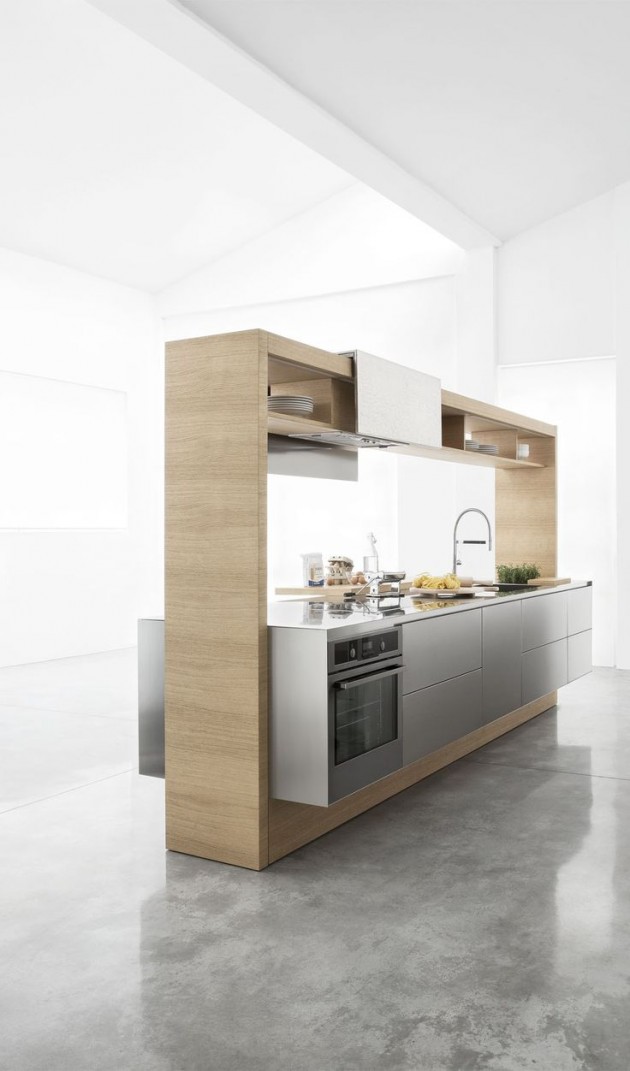
What is a house of quality template?
House of Quality example This house of quality template can help you: - Identify what your customer wants so you can design a product that meets their requirements. - Understand how customer requirements and design characteristics affect each other.
What is House of quality?
Concept & Advantages Explained With Example House of Quality can be defined as the most convenient, easy, and simple tool used to convert the customer needs into technical descriptors for the firm. House of Quality is actually a matrix and is also termed as Quality Matrix.
What is a house of quality diagram?
The House of Quality (HOQ) is defined as a product planning matrix that is built to show how customer requirements relate directly to the ways and methods companies can use to achieve those requirements. House of Quality diagrams use a design that resembles the outline of a house and can be created using technical and competitive benchmarkingdata.
What are the steps in the House of quality?
House of Quality Steps are as follows: Identify what customer wants. Identify how the product will satisfy the customer. Identify relationships between how’s. Develop importance ratings. Evaluate competing products or services. Determine the desirable technical attributes.
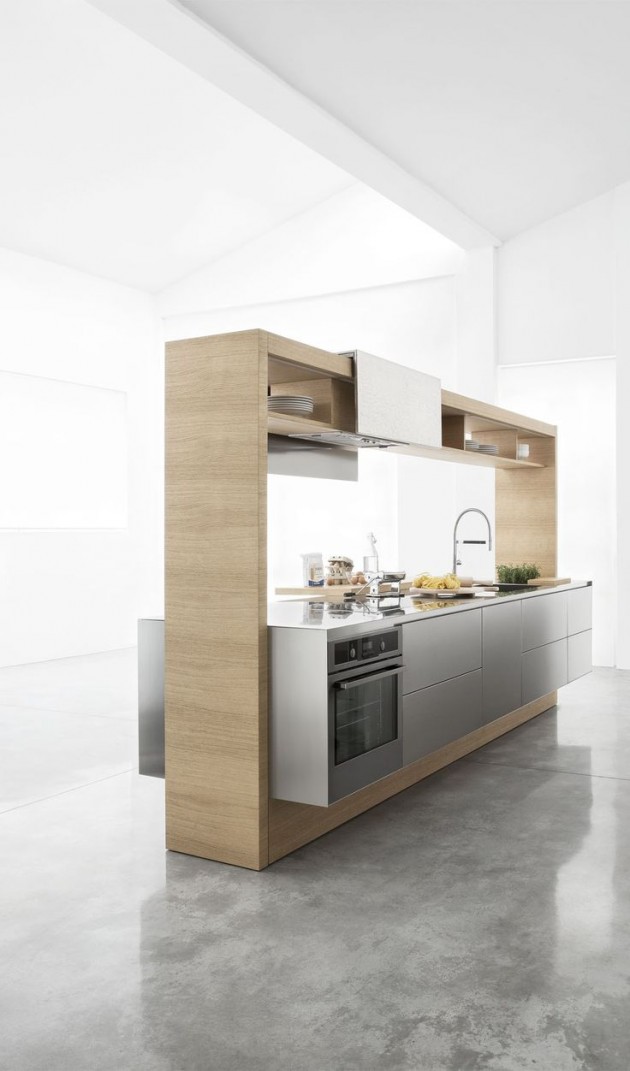
What is meant by House of quality?
House of Quality, or HOQ, is a product planning matrix that is used to show how your customer requirements relate directly to the actions you can take to achieve those requirements.
What are the components of House of quality?
[2002] believed that the principal stages necessary for the construction of the first HOQ matrix includes: 1) Identifying customer requirements (CRs) and their perceptions, 2) Identifying product and engineering design requirements (ECs), 3)Drawing up a relationship matrix, 4)Planning and deploying expected quality (by ...
How does a house of quality work?
A house of quality (HOQ) involves collecting and analyzing the “voice of the customer” and a key component of the Quality Functional Deployment technique. It is used to define the relationship between customer desires and the product or company capabilities.
Why is it called House of quality?
House of quality – the process explained The first and often most important matrix in QFD is called the house of quality because it's shaped like a house with a roof and body. In this matrix, you start by separating customer needs from technical requirements and evaluating the two factors independently of each other.
What are the six basic steps in building the House of Quality?
To build a house of quality, basic six steps are performed....House of Quality StepsIdentify what the customer wants.Identify how the product will satisfy customers. ... Identify relationships between how's. ... Develop importance ratings. ... Evaluate competing products or services. ... Determine the desirable technical attributes.
What are the four main elements of quality?
It has four main components: quality planning, quality assurance, quality control and quality improvement.
What is the House of Quality in Six Sigma?
House of Quality the correlation that company capabilities have with one another. a comparison of the organization's and the competition's ability to meet customer requirements.
Who is responsible for the quality?
Quality is under the responsibility of company management. Quality can only be achieved if all the departments care about achieving it… Everyone in everything he/she does. Otherwise, it is a case of "anybody, somebody, nobody."
Which of the following is true of the House of Quality?
Which of the following is true of the House of Quality? it contains key selling points and features. In the context of quality function deployment, one of the first steps to build the House of Quality is to: identify the technical features of the design of the product.
What is the difference between QFD and House of Quality?
Quality Function Deployment (QFD) is a structured approach followed by customer-driven organizations to transform customer requirements into their product specifications. The House of Quality (HOQ) is a diagram used by a product development team during the initial stage of the QFD process.
Is QFD the same as House of Quality?
What is QFD? House of Quality is a part of a larger process called QFD, which stands for Quality, Function, Deployment. This represents quality-monitoring, a focus on the function of execution of a quality plan, and the application of resources for deployment of that plan.
What are the benefits of QFD?
Benefits of QFDprioritize spoken and unspoken customer wants and needs;determine and translate customer needs into technical characteristics and specifications;build and deliver a quality product or service by focusing all employees toward customer satisfaction.More items...•
What are the three main components of quality?
The quality improvement methods mainly include three components: product improvement, process improvement, and people-based improvement. There are several methods of quality management and techniques that can be utilized.
What are the three components of quality service?
If you're going to improve the service aspect of your firm, you'll need to focus on the three components of service: the people delivering the service, the quality of the service delivery, and the systems the business uses to deliver that service.
What is base of our House of Quality?
The foundation of the house of quality is the belief that products should be designed to reflect customers' desires and tastes—so marketing people, design engineers, and manufacturing staff must work closely together from the time a product is first conceived.
What are the 3 elements of quality?
The entire process of Total Quality Management lies on the foundation of the elements consisting of ethics, integrity, and trust. TQM involves every employee in this level irrespective of their designation.
What is a house of quality?
House of Quality refers to a well-known process for product development that is inspired by customer desires for product or process development and anchored by the capabilities and resources of the organization seeking to meet those desires. It is a process of listening to customers, translating their desires into a written plan, ...
How are weights assigned to each quality?
Weights are assigned to each quality based on what is most important to the customer. How well each need is met is ultimately how the customer will judge your solution’s value. Often, disagreement or misunderstanding between departments of a customer’s organization can occur in relation to what is actually needed.
Why do customers need to be outside of their own perspective?
The goal is to understand customers perhaps even better that they understand themselves so as to open their eyes to ideal solutions. Understand Customer Priorities.
What is the purpose of the House of Quality?
House of Quality can be defined as the most convenient, easy, and simple tool used to convert the customer needs into technical descriptors for the firm. House of Quality is actually a matrix and is also termed as Quality Matrix.
What are the resources required to do the same?
Whether developing a physical product or creating the process for a customer, effective resources are required to do the same. Human resources, machinery, computer systems, construction materials, along with the disposable materials and more must be accounted for.
Why do customers need to be outside of their own perspective?
The goal is to understand customers perhaps in a better manner so that they understand themselves so as to open their eyes to ideal and best solutions available to them.
Why is HOQ important?
HOQ is considered the primary tool used during quality function deployment to help facilitate group decision making. Benefits of building a House of Quality include: A customer’s needs and requirements are established, then used to build and prioritize service offerings and products.
What is a HOQ?
The House of Quality (HOQ) is defined as a product planning matrix that is built to show how customer requirements relate directly to the ways and methods companies can use to achieve those requirements.
What is QFD house of quality?
The QFD house of quality combines different aspects of product development in which different departments collectively develop the matrix. Ideally, the marketing, research, and production departments collaborate on the house of quality.
How many steps are there in a house of quality?
The house of quality is normally built in 10 steps (sometimes 11). You start by recording the customer’s desires, evaluating competing products, and then focus on technical attributes. Ratings play a major role here: You use points to rate the technical requirements and importance levels on different scales.
What are the benefits of the HOQ?
The first benefit comes from simply creating the diagram. Employees from different departmentscome together and collaborate on the house of quality. This inevitably leads to constructive discussions. The input from different departments ultimately ensures a high-quality, long-lasting, and successful product.
Why is QFD important?
The first and often most important matrix in QFD is called the house of quality because it’s shaped like a house with a roof and body.
What is a HOQ?
The house of quality (HOQ) is an excellent starting point for product development planning. The “ Kano Model ” is another way to increase customer satisfaction in future projects. The perspective of the potential customer also plays a major role in this approach.
What scale is used in the HOQ?
This matrix uses a logarithmic scale instead of the linear scale used in other parts of the HOQ (house of quality). This is important for the final evaluation.
How to solicit information for classifying requirements?
You can solicit the information you need for classifying requirements by conducting customer surveys or communicating with customers. You can then figure out which requirements you should focus on in the planning process. In our example, the range of functions is most important for customers.
What is the House of Quality?
The house of quality is a kind of conceptual map that provides the means for interfunctional planning and communications. People with different problems and responsibilities can thrash out design priorities while referring to patterns of evidence on the house’s grid.
What companies use the House of Quality?
The “house of quality,” the basic design tool of the management approach known as quality function deployment (QFD), originated in 1972 at Mitsubishi’s Kobe shipyard site. Toyota and its suppliers then developed it in numerous ways. The house of quality has been used successfully by Japanese manufacturers of consumer electronics, home appliances, clothing, integrated circuits, synthetic rubber, construction equipment, and agricultural engines. Japanese designers use it for services like swimming schools and retail outlets and even for planning apartment layouts.
What does strategic quality management mean?
1 Strategic quality management means more than avoiding repairs for consumers. It means that companies learn from customer experience and reconcile what they want with what engineers can reasonably build.
How does the house lead to the bottom line?
How does the house lead to the bottom line? There is no cookbook procedure, but the house helps the team to set targets, which are, in fact, entered on bottom line of the house. For engineers it is a way to summarize basic data in usable form. For marketing executives it represents the customer’s voice. General managers use it to discover strategic opportunities. Indeed, the house encourages all of these groups to work together to understand one another’s priorities and goals.
What is Toyota's house of quality?
The house of quality has been used successfully by Japanese manufacturers of consumer electronics, home appliances, clothing, integrated circuits, synthetic rubber, construction equipment, and agricultural engines.
Why do marketing executives use the house?
For marketing executives it represents the customer’s voice. General managers use it to discover strategic opportunities. Indeed, the house encourages all of these groups to work together to understand one another’s priorities and goals. The house relieves no one of the responsibility of making tough decisions.
Who wrote the Eight Dimensions of Quality?
1. David A. Garvin, “Competing on the Eight Dimensions of Quality,” HBR November–December 1987, p. 101.
Why does QFD end with HOQ #3?
The QFD ends with HOQ #3. This is due primarily to the fact that all of its parts/materials are purchased rather than manufactured. Had a different product been chosen, a 4th HOQ could have been added that mapped parts/materials attributes to processes and/or initiatives for manufacturing the parts that met those specifications.
Is the weight requirement in HOQ #1 valuable?
The “Weight” requirement (colum n #4) in HOQ #1 may not be a valuable requirement. You can tell that this requirement is suspect by the fact that its “Max Relationship Value in Column ” is only 1. (Note: the template auto-highlights warning values.) The “Weight” requirement (row #4) in HOQ #2 is not being addressed.
Why is the House of Quality called the House of Quality?
It’s called the House of Quality because of the correlation matrix that is roof shaped and sits on top of the main body of the matrix. The correlation matrix evaluates how the defined product specifications optimize or sub-optimize each other. « Back to Dictionary Index.
What is a HOQ?
House of Quality, or HOQ, is a product planning matrix that is used to show how your customer requirements relate directly to the actions you can take to achieve those requirements.
What is the power of HOQ?
The power of HOQ is in the collaboration of team members, input of the customer, and the deep understanding of how to convert the customer whats to the design hows.
What is customer needs?
Customer needs: For each critical customer segment, capture customer feedback and VOC input consisting of your customer’s needs and the priority or weight of each need.
Why is it important to design a process?
It will be important to coordinate with the rest of the organization to be sure that they understand how they can make your design tangible.
Is it hard to develop a HOQ?
Although it can be a bit of a pain to develop and build your HOQ, the benefits of having all of the elements in one easy-to-read diagram far outweigh the work and effort required to develop it.
What is the House of Quality?
The House of Quality, or Quality Function Deployment ( QFD ), is a useful tool that Six Sigma Black Belt practitioners use during the Define phase of the DMAIC cycle of Six Sigma projects. The topic can be briefly discussed in Green Belt training or sometimes on online free Six Sigma courses. However, the House of Quality is one of the more advanced LEAN techniques.
What is the last step in building a house of quality?
The last step in building a House of Quality is determining of technical attributes and checking our performance with respect to market products.
How many steps are needed to build a house of quality?
To build the house of quality, basic six steps are performed. House of Quality Steps are as follows:
What is the 5th feature of Quick and Hot?
The fifth main feature is fresh and hot delivery. No one wants to have a stale pizza. Everyone wants a fresh and hot pizza, even if they’d ordered it home. Quick-n- Hot delivery should be maintained for all customers or else we’ll lose our customers.
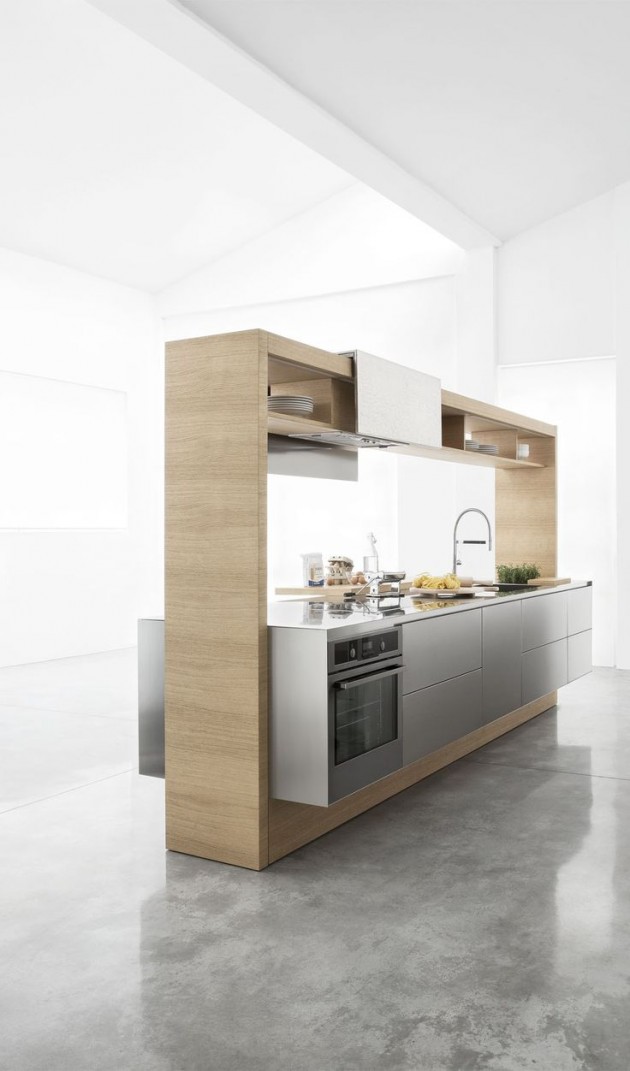
What Is QFD?
Primary Purposes of QFD & House of Quality
- We’ll now cover some primary purposes of QFD / House of Quality: 1. Understand Customer Desires Many times, customers need outside perspective to discover what they really need to build their product or process. The goal is to understand customers perhaps even better that they understand themselves so as to open their eyes to ideal solutions. 2. Understand Customer Prio…
House of Quality Diagram
- Below is an example of a House of Quality Diagram. We will now walk through a summary overview of its various parts. We continue our example of a media-production drone manufacturer. The Customer Specifications section to the left lays out the specific priority features on which the customer has set focus. The numbers just to the right represent th...
in Closing
- There are various levels of detail into which one can go using the House of Quality diagram. Some might include ratings for each engineering specification that indicate technical difficulty of execution, and so forth. But the example above is widely applicable and fairly detailed.
Anatomy of House of Qualities
Steps in House of Qualities
- Identify what are the exact needs and demands of the customer in the target market.
- Identify how the product will satisfy the targeted customer. house of quality refers to identifying specific product characteristics, features or attributes that the customer is looking for and sho...
- Identify relationships between How’s and What. A couple of questions, those are to be answe…
- Identify what are the exact needs and demands of the customer in the target market.
- Identify how the product will satisfy the targeted customer. house of quality refers to identifying specific product characteristics, features or attributes that the customer is looking for and sho...
- Identify relationships between How’s and What. A couple of questions, those are to be answered here: How do our how’s tie together? What is the relationship between our two or more how’s in the ent...
- Develop the importance of ratings as house of quality refers to using the customer’s importance ratings and weights from the relationships in the matrix to compute the important ratings.
Primary Purposes of QFD & House of Quality
- Understand Customer needs and desires
Many times, customers need outside perspective to discover what they really require to build their product or process. The goal is to understand customers perhaps in a better manner so that they understand themselves so as to open their eyes to ideal and best solutions available to them. - Understand the priorities of the Customer:
During the interview stage, get to know the exact customer needs, but then break those needs down into prioritized parts in an effective manner. For instance, if a customer is building drones for media production, how important is the battery life as compared to camera quality? How imp…
Technical Benchmarking
Competitive Benchmarking
- Competitive benchmarking compares one company against a selection of leading competitors. The company is evaluated based on how well or poorly it’s doing by examining and understanding the important aspects associated with its product or services. Add another "room" on the right side of the House of Quality to reflect how well your organization and the competition satisfy cu…
Identifying Benchmark Target Values Using House of Quality
- Establishing target values for each design requirement is necessary. This action establishes concrete goals for the design engineers and further defines customer requirements. These values need to be measurable, and you can develop them from historical records, designed experiments, or analysis of what the competition is doing. Once the team agrees on the target values, enter th…
House of Quality Example
- In this example of a House of Quality, a company is takes on a contract to install a new server system design to help a customer’s increased need for faster response times and better information management. This company selects a group of employees tasked with ensuring the customer’s requirements are included. With the use of focus groups and multi...