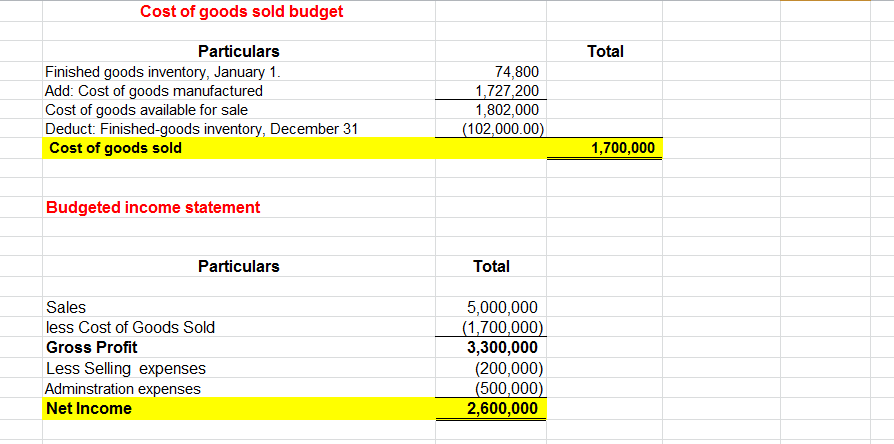
What cost should be included in finished goods inventory?
The finished goods inventory of a manufacturer must include the cost of both variable and fixed manufacturing overhead. Interest cost should not be capitalized for inventories that are routinely manufactured or otherwise produced in large quantities on a repetitive basis.
Are finished goods a current asset?
The value of finished goods is classified as true value inventory and appears on the company’s balance sheet and financial statements. Finished goods are considered a short-term or current asset on a company's balance sheet because they are usually sold within a year.
How do you calculate finished goods?
There are two different methods for calculating finished goods inventory. The account method is as follows: Beginning balance + cost of goods manufactured – cost of goods sold = finished goods inventory This will give you a value for all the products within the time frame in question.
What are the costs of not holding enough inventory?
The cost of not holding enough inventory. araafanzana March 13, 2009 Leave a Comment. Loss of sales from delay in supply. Loss of goodwill and delayed payment from customers if orders are not delivered in full. Higher transportation costs to fill “rush” orders. Disruption of the production process.
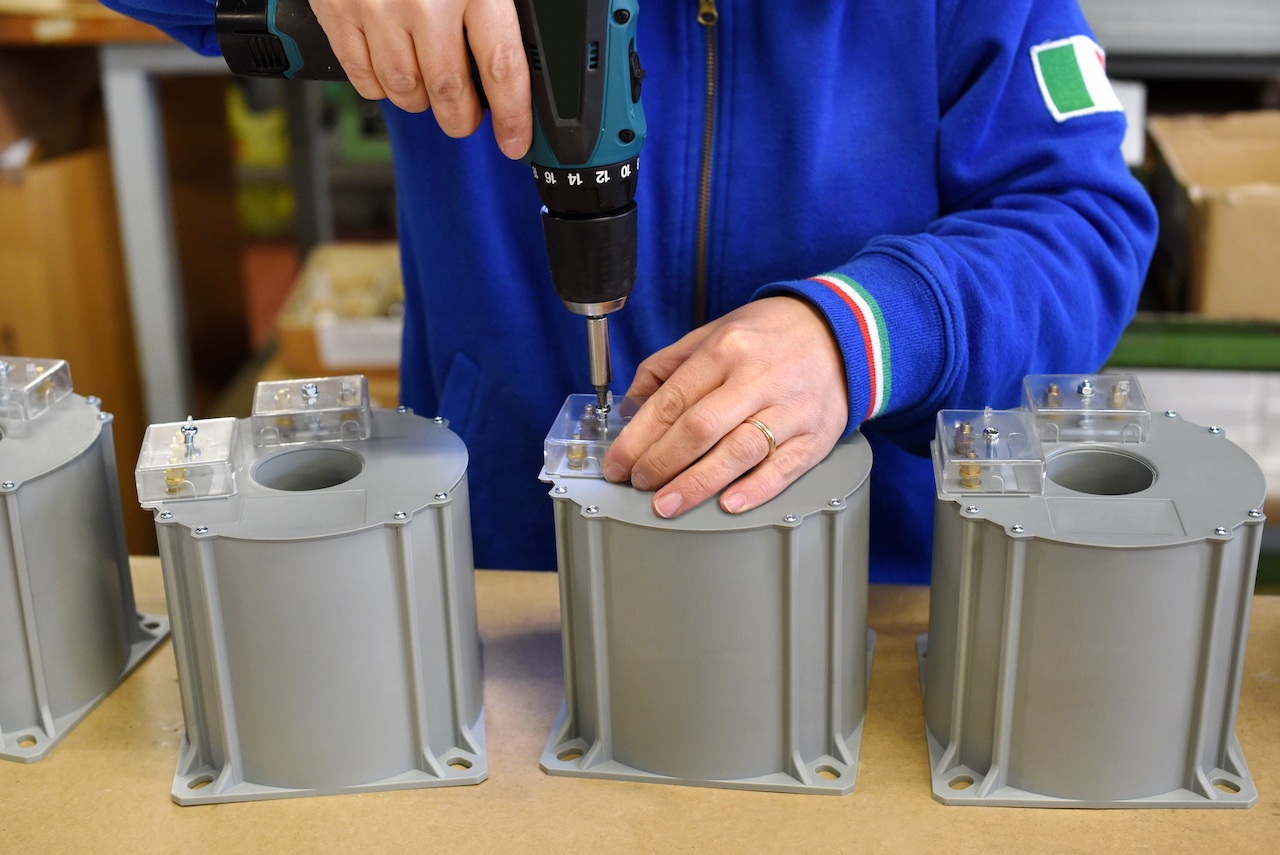
What does finished goods consist of?
What are finished goods? Finished goods are products that have completed a company's production cycle. This means that the inventory has been turned from raw materials into a product that is ready for sale.
What type of product is included in the finished goods inventory account?
Finished goods is a category of inventory unique to manufacturing businesses. They are products that have completed the manufacturing process but have not yet been sold or distributed to vendors or retailers.
How is finished goods inventory calculated?
The finished goods inventory formula (finished goods inventory = beginning finished goods + cost of manufactured goods - COGS) refers to the calculation businesses use to determine how many inventory items are ready for sale.
What are examples of finished goods?
Examples of finished goods include:Fruits and vegetables.Meats.Processed foods such as cereal and sardines.Clothes.Toys.Electronics.Gasoline.
What costs are not included in inventory?
Under both IFRS and US GAAP, the costs that are excluded from inventory include abnormal costs that are incurred as a result of material waste, labor or other production conversion inputs, storage costs (unless required as part of the production process), and all administrative overhead and selling costs.
Which of the following costs are not included in finished goods inventory quizlet?
[D] Under absorption costing, VARIABLE AND FIXED SELLING AND ADMINISTRATIVE EXPENSES would not be included in finished goods inventory.
How do you calculate the ending finished goods inventory budget?
Subtract the cost of goods sold during that period from your total inventory to calculate the finished goods inventory for a new period. From the $60 inventory, if you sold goods that cost you $50 to produce during that period, then your finished goods inventory for the period is $10.
Where is finished goods found in the balance sheet?
The total amount of finished goods inventory on hand as of the end of a reporting period is typically aggregated with the costs of raw materials and work-in-process, and is reported within a single "Inventory" line item on the balance sheet.
What should be the amount in the finished goods inventory at the beginning of the year?
The Beginning Finished Goods Inventory is the value of unsold goods from the previous year. This is found in the balance sheet as the ending finished inventory from the previous accounting period. Thus, this amount is carried forward into the current year as the beginning finished inventory.
What is the difference between raw materials and finished goods?
A manufacturing company handles two different types of inventory -- raw materials and finished goods. The primary difference is that raw materials inventory is used in the production of goods and finished goods inventory is what the company produces and eventually sells to a product reseller.
What are unfinished goods?
Define Unfinished goods items that are used to produce finished goods items. Unfinished goods are often called components, ingredients, raw materials, semi-processed materials, and subassemblies.
What do you call a finished product?
The final version of a product. end product. upshot. outcome. consequence.
What type of account is finished goods inventory quizlet?
The three inventory accounts ("raw materials", "work-in-process", and "finished goods") are all asset accounts and together they make up the total "Inventory" that is reported on the company's Balance Sheet.
What are 3 types of inventory?
Raw materials, semi-finished goods, and finished goods are the three main categories of inventory that are accounted for in a company's financial accounts. There are other types as well which are maintained as a precautionary measure or for some other specific purpose.
What are the 3 main components of inventory?
Inventory is the raw materials used to produce goods as well as the goods that are available for sale. It is classified as a current asset on a company's balance sheet. The three types of inventory include raw materials, work-in-progress, and finished goods.
What are the types of inventories used in inventory accounting?
While there are many types of inventory, the four major ones are raw materials and components, work in progress, finished goods and maintenance, repair and operating supplies.
What Are Finished Goods?
Finished goods are products that have passed through all the stages of manufacturing and are ready for sale. Think of finished goods as what you see on the shelves in stores — i.e., the “merchandise” — though finished goods may also be found in warehouses and distribution centers.
Key Takeaways
Knowing the amount and value of finished goods inventory helps a company understand its profit and determine future budgeting needs.
Finished Goods Inventory Defined
Finished goods inventory is the third and final classification of inventory that is used for accounting purposes by manufacturing companies, the items that are sold to the customer. Manufactured products begin as raw materials and then move into the work-in-progress (WIP) stage as they are being produced.
Why Is Finished Goods Inventory Important?
Well-managed finished goods inventory is important to the success of a manufacturing company or a retail store. By tracking it, a company better understands the inventory it has in stock for sale, helping to gauge how large an order it could accept at a specific point in time.
3 Steps to Becoming Finished Goods
For a manufacturing product to be considered finished goods, it must go through three accounting stages that reflect its production process. To illustrate those steps, consider the hypothetical rowboat manufacturing firm, Oar Master Inc. (OMI).
Finished Goods Examples
Everything people buy is a finished good, including the device on which you’re reading this article. The items you bought the last time you went food shopping are finished goods. The car you drove to get to the supermarket is a finished good. The wallet that held your cash and credit cards is a finished good.
Finished Goods Terminology
When it comes to understanding finished goods inventory and how to determine its value, it’s important to be familiar with the key components that go into its calculation.
What is finished goods inventory management?
Finished goods inventory management is an essential part of the eCommerce business. It allows you to know what a business owns, the value of the products or goods it owns, and to reduce waste.
How many values are there in finished goods inventory?
The finished goods inventory is determined by 3 values:
What are 4 types of inventory?
Raw materials: all the initial products used in the production or manufacture of finished or manufactured products. These are materials produced by nature that require processing for use. The definition of raw materials includes both the materials used to manufacture these finished products and the energy commodities required for their production.
How does knowing finished goods inventory affect production?
Positively affected the whole production efficiency, logistic, and inventory process: By knowing finished goods inventory, you can track manufacturing cost and preview the cost of logistics and production and preview the amount of product needed.
Why is inventory important in accounting?
Ensure the correct accounting process: The inventory makes it possible to identify any differences between the theoretical quantities (as they are calculated by the computer software, taking into account the inputs and outputs) and the actual quantities (as they were identified by the account teams). The reasons that may explain such deviations are loss, theft, damage, errors in the quantities delivered or shipped. By calculating the finished goods inventory, you can track all the information such as the amount of raw materials, the work in progress (WIP) process,…
What is MRO inventory?
MRO inventory: MRO stands for maintenance, repair, and operation inventory: It’s all the materials or supplies that will be used in the production and manufacturing process to fabricate a finished product.
What is inventory in accounting?
The inventory is the act by which we identify all the movable and immovable property of an individual, a trade, or a company. It consists in counting the possessions of a company, for example, its stock, or its fixed assets.
What are the two types of finished goods inventories?
There are two types of finished goods inventories: one at the beginning of an accounting period and one at the end. Whenever anyone speaks about calculating finished goods inventory, they’re talking about ending finished goods inventory. How to find finished goods inventory requires three piece of information:
What is beginning inventory of finished goods?
That’s because beginning inventory of finished goods is the ending finished goods inventory from last period. If you’re calculating finished goods inventory regularly, determining beginning inventory of finished goods is typically as easy as looking at your past balance sheet.
What is finished product inventory?
“Finished” is a relative term, though. One manufacturer’s finished goods inventory may be a retailer’s merchandise inventory, dropshipping inventory, or another manufacturer’s raw material or component. It depends where those finished goods go after their completion.
How does finished goods inventory affect the cost of goods sold?
Finished goods inventory has a big effect on the cost of goods sold (COGS). That’s because a manufacturer creates revenue when finished goods inventory is sold. Recognizing that revenue requires recognizing the COGS—because COGS considers the materials and labor costs applied to each unit sold.
What is finished goods turnover rate?
It measures the rate at which a company’s finished goods inventory is sold and replaced (turned over) during a set time frame. Here’s how to find annual finished goods inventory turnover rate:
What is WIP inventory?
Work in process inventory (AKA work in progress or WIP inventory) is everything that happens to inventory in between raw materials and finished goods. This is when the actual manufacturing is happening. There are some very short or simple manufacturing processes that don’t require specific reporting of WIP inventory.
How to calculate finished goods on hand?
First, take your cost of goods manufactured (COGM) and subtract your cost of goods sold (COGS) from your COGM. Second, add your previous cycle’s finished goods inventory. The result is your finished goods inventory for your current cycle.
What is Finished Goods Inventory?
Finished goods are goods that have been completed by the manufacturing process, or purchased in a completed form, but which have not yet been sold to customers. Goods that have been purchased in completed form are known as merchandise.
Accounting for Finished Goods Inventory
The carrying amount of finished goods inventory is at the cost of the acquired goods, plus any applicable freight in charges and taxes. If the goods were manufactured by the business, then the carrying amount of the inventory is the aggregate cost of the direct materials, direct labor, and factory overhead used to create them.
Presentation of Finished Goods Inventory
The cost of finished goods inventory is considered a short-term asset, since the expectation is that these items will be sold in less than one year.
What Does Finished Goods Inventory Mean?
Finished goods inventory is a unique asset to manufacturers. Retailers don’t have to classify their inventory into segments because all of their inventory is completed and ready for sale.
What is raw material inventory?
When a manufacturer decides to make a product, it must order the basis stock needed to build the product. This stock could be bars of steel, sheets of metal, or blanks of plastic—anything in its raw form. The stock is classified as raw materials inventory.
What happens after a product is made through the assembly line?
After the goods have made it through the entire assembly line and are completely ready for sale, they are transferred out of the work in process account to the finished goods inventory account. As you can see, this process allows a manufacturer to track how much inventory it has at any stage in the production process.
Do manufacturers have to account for inventory?
Manufacturers, on the other hand, physically produce their inventory and have to account for it throughout the production process. It might be helpful to take a look at the production process. Let’s look at an example.
Is finished goods worth more than raw materials?
In other words, finished goods are usually worth much more than raw materials.
What is inventory?
Inventory (also called stock) is any type of good held by a company for the purpose of sales. Since inventory items have value and is expected to bring in a profit after sales, it is counted as a current asset on a company’s balance sheet.
1. Raw materials inventory
Raw materials inventory involves items used to make finished products. Raw materials can be commodities or components that businesses buy or extract themselves. In sum, they’re all the stock that hasn’t been used for manufacturing yet.
2. Maintenance, Repair, and Operating (MRO) inventory
MRO inventory consists of items used to keep a manufacturing company running smoothly. MRO inventory can include employee uniforms, industrial equipment, cleaning or operating supplies, safety equipment, and any materials you use to repair or maintain manufacturing equipment.
3. Decoupling inventory
Decoupling inventory includes any extra components or raw materials that enable a manufacturer to continue with production, even in the case of unforeseen supply stockouts. Inventory is typically composed of several parts that are needed before the finished product can be sold.
4. Work In Progress (WIP) inventory
All the materials used to create a finished product are considered WIP inventory. If you manufacture bicycles, all of the unfinished bikes in your shop could be considered WIP inventory.
5. Finished goods inventory
Finished goods are items that are ready for showtime. They’ve been manufactured from raw materials or purchased from a supplier, and are ready to be sold to customers. Finished goods that are purchased as completed for sale are considered merchandise by retailers.
6. Safety stock and other types of stock
Safety stock is any extra buffer inventory held to protect against going out of stock. Even after calculating average inventory turnover and seasonal trends, there’s always a chance of experiencing unforeseen surges in demand or supply shortages.
What is included in finished goods inventory?
What is finished goods inventory? Finished goods inventory refers to the number of manufactured products in stock that are available for customers to purchase. The finished goods inventory formula is an important inventory ratio that can be used to calculate the value of these goods for sale.
Which of the following cost is not included in finished goods inventory?
Factory overhead is the cost that is not directly related to the production of goods or services in the organization. These costs that are included are indirect labor or indirect other overheads. It is also known as manufacturing overhead.
What costs are included in inventory?
The cost of inventory includes the cost of purchased merchandise, less discounts that are taken, plus any duties and transportation costs paid by the purchaser.
Is finished goods inventory a product cost?
All manufacturing expenses, costs incurred in the factory or production process, (i.e., direct materials, direct labor, and factory overhead) are product costs. … In the accounting records, the cost of finished products is accumulated in an inventory account – usually “Finished Goods Inventory”.
Which of the following costs is not included in factory overhead?
Manufacturing overhead does not include any of the selling or administrative functions of a business. Thus, the costs of such items as corporate salaries, audit and legal fees, and bad debts are not included in manufacturing overhead.
Which is not an inventory?
Non-Inventory Item – is a type of product that is purchased or sold but whose quantity is not tracked. This type of items are purchased for company use or custom product purchased for Projects. Non-Inventory Items appear in sales process (on Sales Quotes, Sales Orders, Sales Invoices, or customer Credit Notes).
What finished cost?
The typical costs of finishing include labor, coatings (applied and wasted), energy, water, consumables, maintenance) including cleanup, waste disposal. … Each step adds more cost to the finished product. Calculating Labor Costs. The labor involved in finishing can be significant.
What is inventory in manufacturing?
In other words, inventory represents finished goods or goods in different stages of production that a company keeps at its premises or at third-party locations with ownership interest retained until goods are sold. The three most important types of inventory are the raw materials, the work in progress (WIP) inventory, and the finished goods.
What are the three types of inventory?
There are three types of inventory listed – raw material and supplies, work in progress, and finished goods. Also, note that the majority of Colgate’s inventory is the Finished goods inventory.
What is inventory in business?
Inventories are the assets that will be of have been converted to the final products of a company. They are of three major types, namely raw materials, work in progress, and finished goods. The management of inventory calls for an optimum level of inventory that can be maintained by creating an inventory purchasing plan as per the strategy adopted by the company.
What is packing inventory?
As the name suggests, the packing inventory is the inventory of the materials that are used by the company to pack the goods. Within this category, there is something called the primary packing inventory and the secondary packing inventory. Primary packing is something without which the goods can’t be used.
What is raw material inventory?
Raw material inventory is part of inventory cost which is reported under current assets on the balance sheet. read more. in stock, it will incur higher carrying costs, and there is also the undesirable possibility of the inventory getting obsolete. For example, in the pharmaceutical or food industry, the raw materials may be perishable.
Why is it important to optimize raw material inventory?
It is essential to optimize raw material inventory. It is because if a company keeps too much raw material inventory. Raw Material Inventory Raw materials inventory is the cost of products in the inventory of the company which has not been used for finished products and work in progress inventory. Raw material inventory is part ...
Why is work in progress inventory minimized?
So it is most desirable that the volume of inventory that is lying in the form of work in progress be minimized, and the time is taken to convert it into the final, also be minimized so that the locked-up value can be released as quickly as possible. The idea is that this capital, which is locked-up in the form of work in progress inventory, can otherwise be invested somewhere else to achieve much better returns.
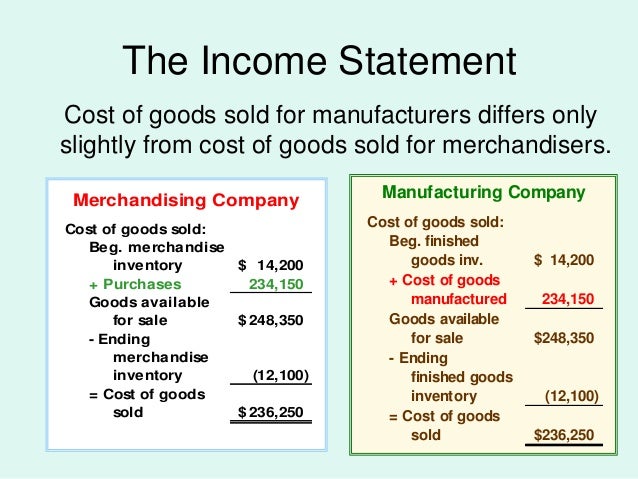