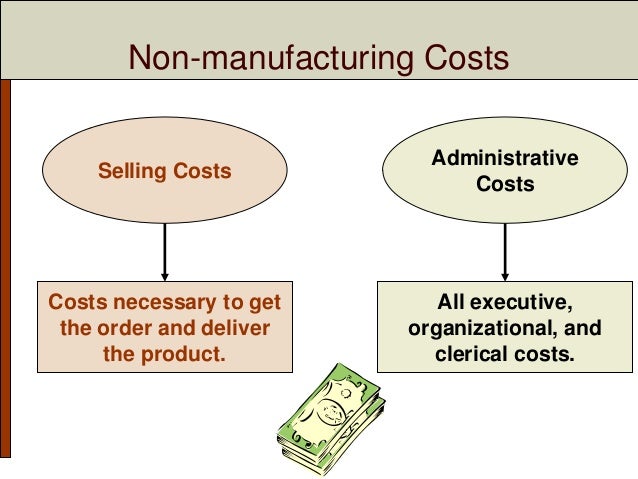
Some examples of manufacturing overhead costs include the following:
- depreciation, rent and property taxes on the manufacturing facilities
- depreciation on the manufacturing equipment
- managers and supervisors in the manufacturing facilities
- repairs and maintenance employees in the manufacturing facilities
- electricity and gas used in the manufacturing facilities
- indirect factory supplies, and much more
What exactly is included in overhead costs?
These include:
- Direct Material Costs
- Direct Labor Costs
- Manufacturing Overhead Costs
How do you calculate budgeted manufacturing overhead rate?
To calculate the overhead rate per employee, follow the steps below:
- Calculate the labor cost which includes not just the weekly or hourly pay but also health benefits, vacation pay, pension and retirement benefits paid by the employer.
- Compute the total overheads of the business.
- Divide the overhead costs by the number of billable hours. ...
What is total manufacturing overhead cost?
The manufacturing overhead cost — also known as the factory overhead cost or manufacturing support cost — is the cost that business owners incur outside the expenses associated with direct labor or the cost of raw and direct materials. This calculation tracks a specific overhead rate, looking at the finances associated with the general ...
What is the formula for calculating Manufacturing overhead?
Overhead Allocation According to GAAP Standards
- Calculate total manufacturing overhead.
- Choose an allocation base. ...
- Divide total overhead by the allocation base. ...
- Review the payroll and maintenance records to find the total allocation base generated in the previous accounting period.
- Divide allocation base by the number of production units. ...
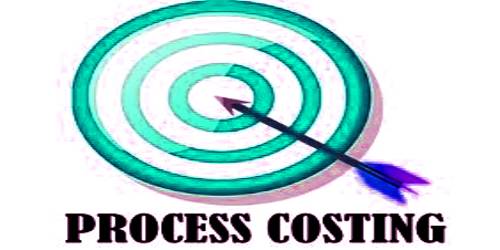
What is not included in overhead cost?
Overhead costs are all of the costs on the company's income statement except for those that are directly related to manufacturing or selling a product, or providing a service. A potter's clay and potting wheel are not overhead costs because they are directly related to the products made.
What are examples of overhead costs?
Examples of Overhead CostsRent. Rent is the cost that a business pays for using its business premises. ... Administrative costs. ... Utilities. ... Insurance. ... Sales and marketing. ... Repair and maintenance of motor vehicles and machinery.
What are 4 examples of manufacturing overhead?
Examples of manufacturing overhead costs are:Rent of the production building.Property taxes and insurance on manufacturing facilities and equipment.Communication systems and computers for a manufacturing facility.Depreciation on manufacturing equipment.Salaries of maintenance personnel.More items...
How do you calculate manufacturing overhead?
Manufacturing Overhead Formula First, you have to identify the manufacturing expenses in your business. Once you do, add them all up or multiply the overhead cost per unit by the number of units you manufacture. To get a percentage, divide by your monthly sales and multiply that number by 100.
What are the 2 types of overhead costs?
Think of the expense as being split into two parts: the fixed overhead (the monthly cost of your phone plan) and the variable overhead (the fees for data overage and/or international travel).
What is typical overhead?
Typical overhead ratios will vary significantly from industry to industry. For restaurants, for example, overhead should be about 35% of sales. In retail, typical overhead ratios are more like 20-25%, while professional services firms may have overhead costs as high as 50% of sales.
What are product overhead costs?
Manufacturing overhead (MOH) cost is the sum of all the indirect costs which are incurred while manufacturing a product. It is added to the cost of the final product along with the direct material and direct labor costs.
What is manufacturing overhead?
Manufacturing overhead (also referred to as factory overhead, factory burden, and manufacturing support costs) refers to indirect factory-related costs that are incurred when a product is manufactured.
Why is manufacturing overhead important?
Introduction to Manufacturing Overhead. In the world of manufacturing—as competition becomes more intense and customers demand more services— it is important that management not only control its overhead but also understand how it is assigned to products and ultimately reported on the company's financial statements.
Why is it important to control overhead?
In the world of manufacturing—as competition becomes more intense and customers demand more services —it is important that management not only control its overhead but also understand how it is assigned to products and ultimately reported on the company's financial statements. We view overhead as two types of costs and define them as follows:
What is a material handler?
Material handlers (forklift operators who move materials and units ).
Is non manufacturing cost a product?
Although nonmanufacturing costs are not assigned to products for purposes of reporting inventory and the cost of goods sold on a company's financial statements , they should always be considered as part of the total cost of providing a specific product to a specific customer. For a product to be profitable, its selling price must be greater than the sum of the product cost (direct material, direct labor, and manufacturing overhead) plus the nonmanufacturing costs and expenses.
Is manufacturing overhead included in the cost of goods sold?
According to generally accepted accounting principles (GAAP), manufacturing overhead must be included in the cost of Work in Process Inventory and Finished Goods Inventory on a manufacturer's balance sheet, as well as in the Cost of Goods Sold on its income statement.
What is manufacturing overhead?
Manufacturing overhead is any cost not directly related to a facility's production. The indirect costs in manufacturing overhead can also be called factory overhead, production overhead or factory burden. Direct costs, like the price of material and labor, are directly related to a facility's manufacturing efforts, and therefore aren't part of the manufacturing overhead.
What are the three types of overhead costs?
Also, business activity does not cause these costs to change. Fixed overhead costs include rent, mortgage , government fees and property taxes. Variable: These are costs that can change with production output.
What to do with extra room in a facility?
If you have extra or unused rooms in your facility, consider renting them out to small businesses or organizations to help pay the rental or mortgage costs on your building. You may have some employees that are not always required to work in-office, so you could consider letting them work from home to free up possible rental space.
What is an in house repair?
An in-house repair professional can perform routine checks, preventative maintenance and minor repairs on your equipment. This hiring decision could save money on unexpected repair costs or work fees for an external repair vendor. Having an on-site person who can also perform emergency repairs could prevent you from paying an outside person overtime or extra costs if your equipment breaks after operation hours.
How to budget for overhead?
1. Budget for a higher estimate of overhead costs. Every month, calculate your facility's estimated overhead costs. You can use past bills, statements and records to determine how much you should allocate for overhead in your budget. Consider setting aside an amount over your estimate to account for any potential repairs or other unforeseen costs. ...
What are variable costs?
Variable: These are costs that can change with production output. These items include some operational utilities such as electric, gas and trash service. Output can also impact shipping costs, maintenance situations, legal fees and advertising.
How to save money on equipment?
Perform preventative maintenance. Keeping your equipment up to date and maintaining it can ensure it operates efficiently and lasts longer. Preventative maintenance can save money on equipment costs, such as repairs and replacements.
What are the different types of indirect costs related to manufacturing overhead?
Overhead absorption rate is the manufacturing overhead costs per unit of the activity (also called as the cost driver) like labor costs, labor hours and machine hours. Here are the types of costs that are included in manufacturing overhead:
What is fixed overhead cost?
Fixed overhead costs: These costs don’t fluctuate based on the manufacturing output.
What is manufacturing overhead cost?
Manufacturing overhead cost is the sum of all the indirect costs which are incurred while manufacturing a product. It is added to the cost of the final product along with the direct material and direct labor costs. Usually manufacturing overhead costs include depreciation of equipment, salary and wages paid to factory personnel and electricity used to operate the equipment.
What is indirect labor?
Indirect labor is the cost to the company for employees who aren’t directly involved in the production of the product. For example, the salaries for security guards, janitors, machine repairmen, plant managers, supervisors, and quality inspectors are all indirect labor costs. Cost accountants derive the indirect labor cost through activity-based costing, which involves identifying and assigning costs to overhead activities and then assigning those costs to the product. For example, in activity based costing, every employee who is working in the manufacturing facility but not directly involved in the manufacturing process, keeps a log on the amount of hours spent on their job and from that the total cost is calculated and then the cost is assigned to each product being manufactured.
What is semi variable overhead?
Semi-variable overhead costs. Semi-variable overhead costs are partially variable and partially fixed in nature. Since they contain both a fixed and variable component, it doesn’t change directly in proportion to the manufacturing output. For example, telephone charges, repairs and maintenance of the equipment etc.,
What is indirect material cost?
Indirect material costs are mostly related to consumables like machine lubricants, light bulbs , and janitorial supplies. Cost accountants spread these costs over the entire inventory, since it is not possible to track the individual indirect material used.
How to predict manufacturing overhead?
If it plans to produce 15,000 units the next year, the total manufacturing overhead can be predicted by multiplying the manufacturing overhead of one unit by the total number of units it intends to produce.
How to calculate production overhead?
The organization decides on its own how this distribution will take place: 1 If the company has a large number of key production personnel, it makes sense to calculate production overheads in proportion to the payroll of the main production employees; 2 With a small number of main workers (for example, with fully automated production), it is better to distribute overhead costs in proportion to sales volumes or the operating time of production equipment (machine-hours); 3 The ratio of direct costs incurred per unit of production to the total amount of costs can also serve as the basis for distribution. This method is convenient for enterprises where direct costs significantly exceed indirect costs;
Why is manufacturing overhead cost important?
The most obvious goal of accounting for manufacturing overhead costs is financial planning for future profits, which are influenced by all the costs incurred by the business. If overhead costs are incorrectly accounted for, they exceed planned or necessary amounts, the cost of products or services is overstated/understated, and the level of the factory profit is reduced. Control of costs allows for their effective planning and, therefore, improves the economic situation of the company.
What is the basis for distribution?
The ratio of direct costs incurred per unit of production to the total amount of costs can also serve as the basis for distribution. This method is convenient for enterprises where direct costs significantly exceed indirect costs;
What is overhead cost?
Overhead costs are those that are associated with the production of all products of the enterprise at once, management, and sales. This is a diverse set of costs that cannot be directly attributed to specific types of finished products. Overhead costs are indirect costs that are associated with the costing and accounting item/s, but it is not economically feasible to directly attribute them to it. They are accumulated on special accounts throughout the month and then distributed between all the products manufactured in the factory.
What is included in manufacturing overhead?
What is included in the manufacturing overhead? In contrast to direct costs, consisting of costs of raw materials, components and materials for production and salaries of key production personnel, overhead costs include a wider list of general production and general business costs:
Can overhead costs be ignored?
The specificity of overhead costs is such that they cannot be immediately attributed to any specific type of products or services provided, but they cannot be ignored, since this can lead to inaccuracy in pricing. Therefore, in order to determine the cost per unit of production, the overhead costs must be allocated:
How to Calculate Overhead Cost?
Now let’s understand how you can calculate the overhead cost as we now know the various methods of calculating the absorption rate.
What is the next step after calculating overhead rate?
After calculating the overhead rate, the next step is to calculate the overheads to be charged to production.
What is factory overhead?
Manufacturing or Factory Overheads. The Factory Overheads refer to the expenses incurred to run the manufacturing division of your company. These are indirect production costs other than direct material, direct labor, and direct expenses.
Why is it important to calculate the overhead rate?
These could include direct labor costs, machine hours, etc. Therefore, it is important to calculate the overhead rate because it helps you to achieve the following.
Why are overhead costs important?
This is because there may be times when the Overhead Expenses may exceed the direct costs of producing goods or services.
What are the overhead costs of manufacturing?
Other manufacturing overheads are the costs that include the costs of factory utilities. These include gas and electricity, depreciation on manufacturing equipment, rent and property taxes on manufacturing facilities, etc.
What is overhead cost?
As stated earlier, the overhead costs are the indirect costs that cannot be directly assigned to a particular product, job, process, or work order. Accordingly, Overhead costs are classified into indirect material, indirect labor, and indirect overheads. Indirect Material.
What is research and development overhead?
Research and Development Overheads. These Overhead expenses are usually incurred on a new product or process development. They are not identifiable to be charged on any specific product or service line cater by the business. Examples include the cost of raw material used in research, staff cost indulged in Research, etc.
What is factory overhead?
Factory Overheads Factory Overhead, also called Factory Burden, is the total of all the indirect expenses related to the production of goods such as Quality Assurance Salaries, Factory Rent, & Factory Building Insurance etc. read more. , Work Overheads, etc.
What is overhead cost?
Overhead Cost refers to the cost of indirect material, indirect labor, and other operating expenses, which are associated with the typical day to day running of the business but cannot be conveniently charged directly to any specific product or service or cost center. In other words, it is the cost incurred on labor, material, ...
What is semi variable overhead?
Semi-Variable Overhead Expenses are the ones which are partly fixed and party variable in nature. As such, they contain both fixed and variable elements and, therefore, don’t fluctuate in direct proportion to business output. Semi-variable overhead examples include Telephone Charges etc.
What is work overhead based on?
Work Overhead is levied based on Direc Labor Hour Rate
What is indirect cost?
In other words, it is the cost incurred on labor, material, or services that cannot be economically identified with a specific saleable cost of goods or service per unit of the business. They are Indirect and need to be shared out among the cost units as precisely as possible.
What are overhead expenses?
Such Overhead expenses are the ones that vary in direct proportion to the volume of output. These overhead expenses are directly affected by business activity. Variable Overhead Examples include Shipping expenses, Advertising Costs, etc.
How Do You Calculate Overhead Cost?
To calculate overhead costs of the business, you need to categorize each overhead expense of your business for a specific time period, typically by breaking them down by month. While all indirect costs are overheads, you need to be careful while categorizing these costs.
Why do businesses have to take into account both overhead costs and direct expenses to calculate the long-term product and service prices?
Doing so allows the business to earn profits on a long-term basis.
Why is overhead cost important?
Calculating overhead costs is not just important for budgeting but also determining how much the business should charge for a service or product to make a profit. For example, if you have a service-based business, then apart from the direct costs of providing the service, you will also incur overhead costs such as rent, utilities and insurance.
What are some examples of overhead costs?
Some examples of overhead costs are: Overhead costs can include fixed monthly and annual expenses such as rent, salaries and insurance or variable costs such as advertising expenses that can vary month-on-month based on the level of business activity.
How to apply overhead rate?
Apply the overhead by multiplying the overhead allocation rate by the number of direct labor hours needed to make each product.
Why is it important to monitor overhead costs?
It is important that businesses monitor their overhead costs as they can drain business funds unnecessarily when not properly controlled. As they are not directly related to income, these expenses can become a larger share of the total costs and burden a business. RELATED ARTICLES.
What is manufacturing overhead?
While administrative overhead includes costs front office administration and sales, manufacturing overhead is all of the costs that a manufacturing facility incurs, other than direct costs.
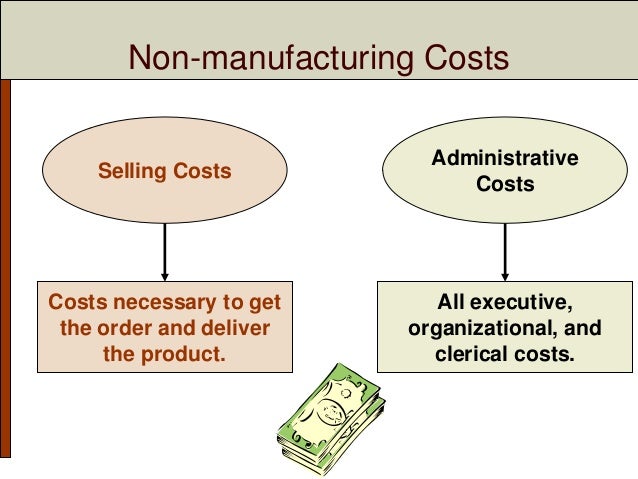