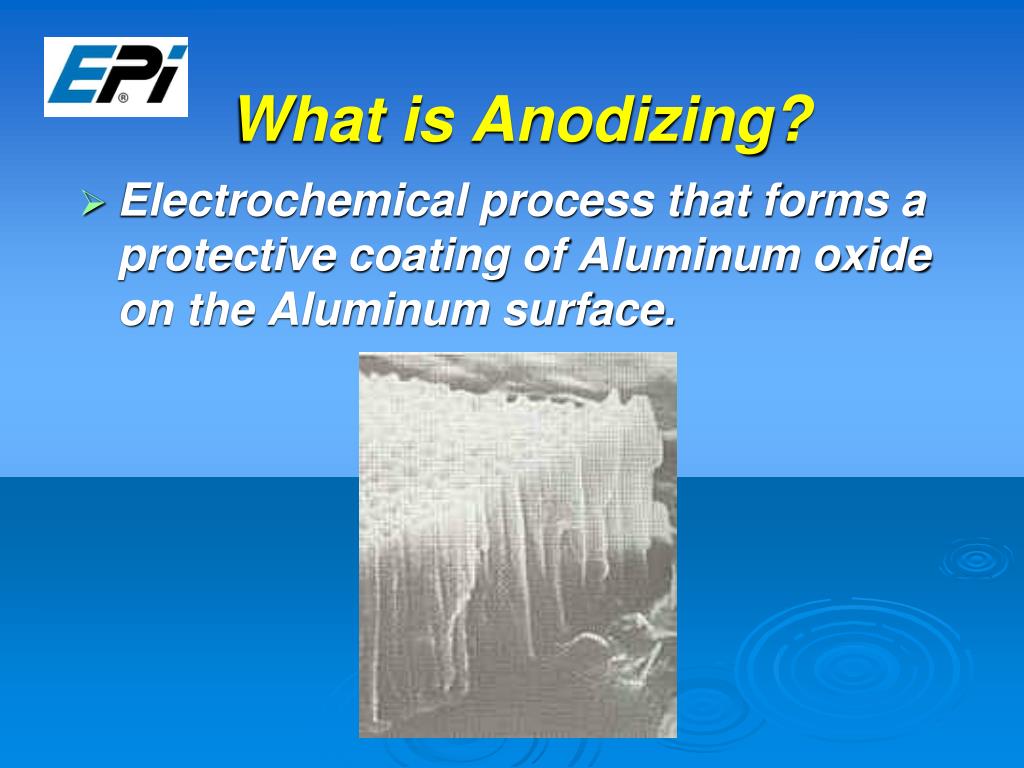
Anodization is an electrolytic passivation process used to increase the thickness of the natural oxide layer on the surface of metal parts. A limited number of metals, such as stainless steels, can achieve passivity. The process is called anodizing because the part to be treated forms the anode electrode of an electrolytic cell.
Does anodization provide good insulation?
The most commonly used anodic oxidation coatings in industrial anodizing provide electrical and thermal insulation. This layer of aluminum oxide consists of hydrated aluminum oxide that is considered impervious to corrosion. However, the benefits of aluminum anodizing do not end there.
What metals can be anodized?
What Metals Can Be Anodized? Aluminum is the most commonly anodized material. However, there are several other types of materials that can be anodized. Magnesium can be anodized but its applications are very limited. Titanium is perhaps the second most commonly anodized material, though still nowhere near as popular as aluminum.
What metals can you Anodize?
Most common metal to be anodized is Aluminum. Other metals like, Copper, Manganese, Silicon, Magnesium, Magnesium and Silicon, Zinc can also be anodized. Stainless steel is already oxidized (chromium oxide) and have a passive layer on the surface and passive layer is generally corrosion resistance.
How is Anodize process done?
Understanding the Process
- Pre-treatment. The first step in anodizing includes pre-treating the aluminum through degreasing and pickling and providing a visible finish.
- Anodic oxide. The anodizing process requires submersion of the material in an acid electrolyte bath while an electric current passes through.
- Colour anodizing. ...
- Sealing. ...

What do you mean by anodising class 10th?
Anodising is the process of forming a thick oxide layer of aluminium. This aluminium oxide coat makes it resistant to further corrosion.
What is anodize used for?
Anodizing is a process that converts the surface of a non-ferrous metal into a corrosion-resistant, decorative, non-conductive oxide. It is a very common finishing technique for aluminum, although other metals such as titanium and magnesium can also be anodized.
What is anodizing example?
The most common anodizing processes, for example, sulphuric acid on aluminium, produce a porous surface which can accept dyes easily. The number of dye colours is almost endless; however, the colours produced tend to vary according to the base alloy.
How do you do anodization?
How to Anodize Aluminum at HomeUse the Scotch-Brite pad to clean the surface and remove any machining marks.Put on your safety equipment, including gloves.Use the degreaser to clean the part well, then rinse with the distilled water.Etch the part by dipping in a lye bath for 3-5 minutes.More items...•
What types of materials can be anodized?
Aluminum, aluminum alloys, magnesium, titanium and stainless steel can be anodized. Aluminum is by far the most common due to its high strength to weight ratio and availability. Anodized aluminum is capable of achieving many colors as dyes can be used to get the desired shade.
Is anodizing a coating?
What Is Anodizing? Anodizing is a simple electrochemical process developed 100 years ago that forms a protective coating of aluminum oxide on the surface of the aluminum. The lifetime of the finish is proportional to the thickness of the anodic coating applied.
What acid is used in anodizing?
Sulfuric AcidSulfuric Acid is the preferred method among anodizers The predominant anodizing process today. Coatings 0.1-1.0 mil thick formed in a 15 pct.
Is anodised aluminium safe?
While there are health concerns of cooking with aluminum, anodized aluminum is generally considered to be safe as it is sealed and doesn't interact with acid the way typical aluminum does.
Can any metal be anodized?
Anodizing is a process that thickens the natural oxide layer on a metal part's surface into an anodic oxide film. This extra thickness protects the part's surface and improves aesthetics. Aluminum and titanium are the most commonly anodized metals, but other nonferrous metals can also undergo the process.
What are the 5 steps to anodizing?
Batch and coil anodizing are accomplished in five carefully controlled, calibrated, quality-tested stages:Cleaning. Alkaline and/or acid cleaners remove grease, and surface dirt.Pre-Treatment. ◦ Etching. ... Anodizing. ... Coloring. ... Sealing.
Which is better hard anodized or stainless steel?
Stainless steel is a kitchen-friendly option that's easy to maintain. However, hard anodized cookware is a better conductor of heat and can yield fantastic cooking results.
Can anodizing be removed?
The bottom line here is – you can use oven cleaner to strip the anodize layer, or you can make do with drain cleaner to remove anodizing from aluminum.
What is the difference between powder coating and anodizing?
Anodizing is an inorganic finish, while powder coating is an organic finish. Powder coatings are some of the best organic finishes (paints) on the market. However, they cannot withstand the same abuse as inorganic finishes, such as plating or anodizing.
How much does it cost to anodize?
How much does Anodizing cost? It is common to see a minimum charges ranging from $65 to $125. This is for Type II and only for colors that your anodizer is already running (e.g. clear, black, etc). Anodizing is inexpensive when done in bulk.
What is the difference between anodized aluminum and aluminum?
Anodized aluminum has a thicker passive layer than naturally passivated aluminum, meaning it is more resistant to degradation and subsequent corrosion.
Why do you anodize parts?
Anodizing is a necessary step in manufacturing aluminum parts. The process improves the part’s mechanical and aesthetic properties, making the part...
How does anodizing work?
Anodizing works by immersing a metal part into an acid electrolyte bath and electrifying both the part and the solution. It’s an electrochemical pr...
How do I assess the quality of anodized parts?
To assess the quality of anodization, you should test how resistant the part is to abrasion and corrosion. If the material finish bleeds when teste...
Why should I include jig marks in my design?
When designing a part that will be anodized, it’s important to clearly include and distinguish between the A and B sides. One side will have jig ma...
Is anodizing conductive?
Anodizing is not conductive. If your part requires conductive features, you may need to apply a clear chemical conversion coating. This means that...
What materials can I anodize?
Anodization is key for all grades of aluminum, and can be used for other metals, including titanium, zinc, tantalum and niobium.
Is anodizing expensive?
Anodizing costs depend on the quantity, dimensions, color and shape of your part, as well as the anodizing type. While anodizing can get expensive,...
Will anodization wear off?
While anodizing leaves a very durable surface finish on your part, an acid wash or general use can wear off anodize eventually.
What chemicals does anodizing use?
To anodize aluminum parts, it’s most common to use either chromic acid, oxalic acid or sulfuric acid. Phosphoric acid and boric sulfuric acid mix a...
What’s the difference between Type II and Type III anodizing?
Type II anodization is the more standard process of using sulfuric acid, while Type III (hardcoat) involves more demanding conditions to achieve ha...
What is anodizing metal?
Anodizing is an electrochemical process that converts the metal surface into a decorative, durable, corrosion-resistant, anodic oxide finish. Aluminum is ideally suited to anodizing, although other nonferrous metals, such as magnesium and titanium, also can be anodized. The anodic oxide structure originates from the aluminum substrate ...
How is anodizing accomplished?
Anodizing is accomplished by immersing the aluminum into an acid electrolyte bath and passing an electric current through the medium. A cathode is mounted to the inside of the anodizing tank; the aluminum acts as an anode, so that oxygen ions are released from the electrolyte to combine with the aluminum atoms at the surface ...
What is anodizing?
Anodizing is a key step in manufacturing aluminum parts. An electrochemical process that involves coating a metal part with an oxide surface layer, anodizing gives the part additional sturdiness and a more attractive finish. While anodizing is most common with aluminum, other substrates can be anodized, including magnesium and titanium .
How does anodizing work?
To anodize a part, you connect it to a positive terminal of an electrical circuit, also called an anode. You then submerge the part in an acidic electrolyte bath solution. This solution contains chemical compounds, such as sodium phosphate, which fill the bath with positive and negative ions.
How does anodizing work in practice?
Anodizing follows the same broad strokes as many other finishing processes. In practice, this means that you should follow this process:
How do you anodize aluminum?
Here is a detailed introduction to anodizing and why it’s an ideal finishing process (and essential for aluminum parts). We cover correct racking, cleaning and etching, desmutting, coloring, sealing, curing and wrapping.
What is anodizing in the military?
The most widely used anodizing specification in the US is a U.S. military spec, MIL-A-8625, which defines three types of aluminium anodizing. Type I is chromic acid anodizing, Type II is sulphuric acid anodizing, and Type III is sulphuric acid hard anodizing. Other anodizing specifications include more MIL-SPECs (e.g., MIL-A-63576), aerospace industry specs by organizations such as SAE, ASTM, and ISO (e.g., AMS 2469, AMS 2470, AMS 2471, AMS 2472, AMS 2482, ASTM B580, ASTM D3933, ISO 10074, and BS 5599), and corporation-specific specs (such as those of Boeing, Lockheed Martin, Airbus and other large contractors). AMS 2468 is obsolete. None of these specifications define a detailed process or chemistry, but rather a set of tests and quality assurance measures which the anodized product must meet. BS 1615 guides the selection of alloys for anodizing. For British defense work, a detailed chromic and sulfuric anodizing processes are described by DEF STAN 03-24/3 and DEF STAN 03-25/3 respectively.
Why is aluminum anodized?
Aluminium alloys are anodized to increase corrosion resistance and to allow dyeing (colouring), improved lubrication, or improved adhesion. However, anodizing does not increase the strength of the aluminium object. The anodic layer is insulative.
What is the difference between anodizing and chromate conversion?
The reason for combining the processes can vary, however, the significant difference between anodizing and chromate conversion coating is the electrical conductivity of the films produced. Although both stable compounds, chromate conversion coating has a greatly increased electrical conductivity.
How is anodized aluminum grown?
The anodized aluminium layer is grown by passing a direct current through an electrolytic solution, with the aluminium object serving as the anode (the positive electrode). The current releases hydrogen at the cathode (the negative electrode) and oxygen at the surface of the aluminium anode, creating a build-up of aluminium oxide. Alternating current and pulsed current is also possible but rarely used. The voltage required by various solutions may range from 1 to 300 V DC, although most fall in the range of 15 to 21 V. Higher voltages are typically required for thicker coatings formed in sulfuric and organic acid. The anodizing current varies with the area of aluminium being anodized and typically ranges from 30 to 300 A / m 2 .
What is the current of anodizing aluminium?
The anodizing current varies with the area of aluminium being anodized and typically ranges from 30 to 300 A / m 2 . Aluminium anodizing (eloxal or El ectrolytic Ox idation of Al uminium) is usually performed in an acidic solution, typically sulphuric acid or chromic acid, which slowly dissolves the aluminium oxide.
How does anodizing an aluminum surface affect the dimensions?
Therefore, anodizing will increase the part dimensions on each surface by half the oxide thickness. For example, a coating that is 2 μm thick will increase the part dimensions by 1 μm per surface. If the part is anodized on all sides, then all linear dimensions will increase by the oxide thickness. Anodized aluminium surfaces are harder than aluminium but have low to moderate wear resistance, although this can be improved with thickness and sealing.
Why is anodizing used in paint?
The process is called anodizing because the part to be treated forms the anode electrode of an electrolytic cell. Anodizing increases resistance to corrosion and wear, and provides better adhesion for paint primers and glues than bare metal does.
Why is anodizing called anodizing?
The process is called anodizing because the part to be treated forms the anode electrode of an electrical circuit
Why is anodizing used?
Anodizing is also used to prevent galling of threaded components and to make dielectric films for electrolytic capacitors.
Why is the anode positively charged?
This is because the electrode connected to the positive terminal of the battery is where the negatively charged ions go to lose electrons, that is, to get oxidized. Thus, being connected to the positive terminal of the battery makes the anode positive in an electrolytic cell.
What is anodizing aluminum?
Anodization is an electrochemical process that converts the metal surface into a decorative, durable, corrosion-resistant, anodic oxide finish. This aluminum oxide is not applied to the surface like paint or plating, but is fully integrated with the underlying aluminum substrate, so cannot chip or peel. It has a highly ordered, porous structure that allows for secondary processes such as coloring and sealing. Anodizing is accomplished by immersing the aluminum into an acid electrolyte bath and passing an electric current through the medium. A cathode is mounted to the inside of the anodizing tank; the aluminum acts as an anode, so that oxygen ions are released from the electrolyte to combine with the aluminum atoms at the surface of the part being anodized. Anodizing is, therefore, a matter of highly controlled oxidation—the enhancement of a naturally occurring phenomenon.
What is the difference between anode and cathode?
battery). The anode is the positively charged electrode and the cathode is the negatively charge electrode. The anode attracts negative charge and the cathode attracts positive charge.
How is anodising done?
Anodising is done by immersing aluminium into acid electrolyte bath and by passing electric current through it.
What happens when an anode is negatively charged?
In an electrochemical cell, (one used for current supply), the anode is negatively charged, as the negatively charged ions lose their electrons to an initially uncharged anode, making it negatively charged. On connecting an external circuit to an electrochemical cell, the electrons flow from the negatively charged anode to the positively charged cathode. So, current flows from the cathode to the anode.
What is anodization process?
In anodizationprocess, the current flows through an electrolyte in which aluminium sheet is used as anode.
What does "anodized" mean?
tr.v. an·o·dized , an·o·diz·ing , an·o·diz·es To coat electrolytically with a protective or decorative oxide. an′o·di·za′tion n. American Heritage®...
What is titanium anodization?
Titanium alloy anodization produces anti-galling and wear resistant properties, and can also be used cosmetically to achieve a spectrum of colors. Face Value: Orthopedic and spinal device surface treatments are necessary for a variety of aesthetic and functional improvements.
Is anodization available on extrusions?
The extrusions are provided unfinished (degreased) with custom finishes ( anodization) available on request to meet application-specific requirements.
What is anodizing?
Anodizing is a process that thickens the natural oxide layer on a metal part’s surface into an anodic oxide film. This extra thickness protects the part’s surface and improves aesthetics.
How does anodizing metal work?
Anodizing metal components can result in significant economic impact down the line. Anodizing typically reduces the amount of long-term maintenance when compared with untreated aluminum, which results in substantial cost savings. Additionally, while the chemical reactions behind the anodizing process are complicated, the process itself is relatively low-cost.
What is anodized metal used for?
Anodizing is used throughout the construction, aerospace, and consumer goods industries. Anodized metals can be found in building exteriors like curtain walls and roofs, interiors like ceilings and floors, plus staircases and escalators. Satellites also commonly have anodized components, which helps them function in the harsh environment of outer space. Consumer electronics such as laptops, smartphones, and smartwatches also commonly utilize anodized finishes.
How does anodizing affect the surface of an object?
The anodizing process adds to the surface of an object, meaning there will be dimensional changes to the bare metal part. Dimensional growth changes depending on the type of anodization but is typically around 50 percent of the total anodic layer thickness. The thickness of the oxide layer must be considered when determining tolerances, particularly with holes or any mating surfaces. One way this can be mitigated is with chemical or physical masks, as they can be used to keep areas of the raw metal untreated.
What is anodizing aluminum?
Anodizing is a popular finishing choice for aluminum and titanium parts as well as other non-ferrous metals. In this article, we’ll cover the basics of anodization, its benefits, and key considerations for product teams.
Why is anodizing metal important?
Durability. Anodizing a metal component extends its lifespan thanks to improved abrasion resistance and corrosion resistance. This increased durability makes it take much longer for anodized metal parts to wear down during installation, handling, and regular use.
What type of acid is used to produce a very thin oxide layer?
Type I: Uses chromic acid to produce a very thin oxide layer.
Where is Anodized Aluminum Used?
Anodized aluminum can be used in any application that already makes use of another metal material. At Lorin Industries, we manufacture anodized aluminum for the following industries:
Why is coil anodizing a continuous process?
Coil anodizing is a continuous process that requires little to no handling at all, reducing the potential for damage and saving money.
How is Coil Anodized Aluminum Different?
At Lorin Industries, we produce anodized aluminum using a tightly controlled coil anodizing process that delivers a higher quality product at lower processing costs.
What Are The Benefits of Anodized Aluminum?
Anodized aluminum creates a surface that is three times harder than standard aluminum, and will not chip, flake, or peel, even when processed to add color. Because the anodization process is controlled oxidation of the aluminum, the product will also never rust, patina, or weather. Anodized aluminum is one of the toughest, most versatile metal products on the market.
What happens when you dip aluminum in a tank?
Unlike the coil anodizing process, during batch processing, the aluminum pieces or panels are individually dipped into each tank which leads to some parts of the metal spending more time in each part of the process and causes inconsistent color and anodized layer thickness.
Can anodized aluminum be made in any color?
Because anodized aluminum can be made to order in any color, finish, or texture, it’s also an attractive, lightweight, and affordable option for interior finishes like ceiling panels, store signage, and elevator panels.
Is aluminum anodized?
Anodized aluminum is a lightweight metal, weighing approximately 60 percent less than stainless steel, copper or brass. This makes shipping the material much more cost effective, and can solve a myriad of design issues. From architecture to designing consumer goods, wherever a lightweight, durable, and attractive material is necessary, anodized aluminum offers a versatile solution.
What is anodized aluminum?
Anodized aluminum is the aluminum with an anodized layer, which is created through an electrolytic solution where the metal is immersed in, the anodizing layer is grown from the metal itself. With the layer, anodized aluminum got enhanced visual effects and functions. Anodized aluminum is exceptionally durable, ...
How does aluminum anodize?
Aluminum anodizing is a process to electrolytically coat the aluminum surface with a protective or decorative oxide. When the aluminum CNC machining parts or material is submerged in the electrolytic solution, the electric current releases oxygen on the surface of aluminum, forming the accumulation of aluminum oxide. Introducing the electrochemical process, the current makes the positive ions be attracted to the negatively charged plate, while the negative ions attract to the aluminum part, which is the positive anode. The electrochemical reaction forces the pores on the surface of the aluminum to open and positive ions to escape. These holes drill down into the base of the part. A barrier layer is formed by the combination of negative ions and aluminum surface. The resulting anode film or layer is much denser than natural oxidation, and evenly distributed on the workpiece surface, make the aluminum parts resistant to corrosion. The electrolytic solution is usually an acid solution, such as sulfuric or chromic acid.
What is the best way to color anodized aluminum?
1. Dye: immerse the anodized aluminum part in a liquid solution that contains a dissolved dye, the porous anodic coating will absorb the dye. 2. Integral coloring: combines anodizing and coloring to both form and color bronze and black shaded oxidation cell walls. 3.
What type of anodizing is best for aluminum?
Types of Anodizing Aluminum. Type II anodization is best suited for aluminum, but it may also be used for nonferrous metals such as titanium or magnesium. – Type I: use chromic acid to produce a thin and ductile anodized layer on an aluminum part. – Type II: use sulfuric acid to produce a thicker anodized layer on metal part, better for coloring.
What is the solution used to make aluminum resistant to corrosion?
The electrolytic solution is usually an acid solution, such as sulfuric or chromic acid.
What are the advantages of anodizing aluminum?
Advantages of Anodized Aluminum. The oxide layer formed in the anodizing process can effectively improves the corrosion resistance and other properties of metal parts, and simultaneously enhances the visual quality.
Is anodized aluminum stronger than stainless steel?
Anodized aluminum is exceptionally durable, and much harder than the raw material but lighter than stainless steel and copper, remaining the natural luster, texture, and beauty of the metal itself, will not chip, flake or peel, and never wear in normal conditions.

Overview
Anodizing is an electrolytic passivation process used to increase the thickness of the natural oxide layer on the surface of metal parts.
The process is called anodizing because the part to be treated forms the anode electrode of an electrolytic cell. Anodizing increases resistance to corrosion and wear, and provides better adhesion for paint primers and glues than bare meta…
History
Anodizing was first used on an industrial scale in 1923 to protect Duralumin seaplane parts from corrosion. This early chromic acid–based process was called the Bengough–Stuart process and was documented in British defence specification DEF STAN 03-24/3. It is still used today despite its legacy requirements for a complicated voltage cycle now known to be unnecessary. Variations of this process soon evolved, and the first sulfuric acid anodizing process was patented by Gow…
Aluminium
Aluminium alloys are anodized to increase corrosion resistance and to allow dyeing (colouring), improved lubrication, or improved adhesion. However, anodizing does not increase the strength of the aluminium object. The anodic layer is insulative.
When exposed to air at room temperature, or any other gas containing oxygen…
Other widely used specifications
The most widely used anodizing specification in the US is a U.S. military spec, MIL-A-8625, which defines three types of aluminium anodizing. Type I is chromic acid anodizing, Type II is sulphuric acid anodizing, and Type III is sulphuric acid hard anodizing. Other anodizing specifications include more MIL-SPECs (e.g., MIL-A-63576), aerospace industry specs by organizations such as SAE, ASTM, and ISO (e.g., AMS 2469, AMS 2470, AMS 2471, AMS 2472, AMS 2482, ASTM B580, A…
Other metals
Magnesium is anodized primarily as a primer for paint. A thin (5 μm) film is sufficient for this. Thicker coatings of 25 μm and up can provide mild corrosion resistance when sealed with oil, wax, or sodium silicate. Standards for magnesium anodizing are given in AMS 2466, AMS 2478, AMS 2479, and ASTM B893.
Niobium anodizes in a similar fashion to titanium with a range of attractive colors being formed …
Dyeing
The most common anodizing processes, for example, sulphuric acid on aluminium, produce a porous surface which can accept dyes easily. The number of dye colours is almost endless; however, the colours produced tend to vary according to the base alloy. The most common colours in the industry, due to them being relatively cheap, are yellow, green, blue, black, orange, purple and r…
Sealing
Sealing is the final step in the anodizing process. Acidic anodizing solutions produce pores in the anodized coating. These pores can absorb dyes and retain lubricants but are also an avenue for corrosion. When lubrication properties are not critical, they are usually sealed after dyeing to increase corrosion resistance and dye retention. There are three most common types of sealing. First, long immersion in boiling-hot (96–100°C/205-212°F) deionized water or steam is the simpl…
Cleaning
Anodized aluminium surfaces that are not regularly cleaned are susceptible to panel edge staining, a unique type of surface staining that can affect the structural integrity of the metal.