
What is the House of quality process?
The house of quality process is a component of quality function deployment (QFD). The QFD method helps you assure quality when you develop products and deliver services. QFD uses various matrices for this purpose.
What is the House of quality glossary?
Quality Glossary Definition: House of Quality. The House of Quality (HOQ) is defined as a product planning matrix that is built to show how customer requirements relate directly to the ways and methods companies can use to achieve those requirements.
What is Hoq (House of quality)?
A house of quality (HOQ) involves collecting and analyzing the “voice of the customer” and a key component of the Quality Functional Deployment technique. It is used to define the relationship between customer desires and the product or company capabilities. Step 1: Customer Requirements – “Voice of the Customer”
What is the importance of quality house in design?
The quality house makes it easy to translate customer wishes and market demands into a design. In addition to function requirements, the functional specifications and technical design will also be considered. For instance, through the use of programme and system tests, it can be evaluated if the product meets the customers’ expectations.
What are the benefits of the house of quality?
Why is QFD important?
What is the Kano model?
Why do we use market analysis to determine requirements?
How to find out what customers want?
How to solicit information for classifying requirements?
What are the advantages of visualization?
See 4 more
About this website
Why is it called House of Quality?
House of quality – the process explained The first and often most important matrix in QFD is called the house of quality because it's shaped like a house with a roof and body. In this matrix, you start by separating customer needs from technical requirements and evaluating the two factors independently of each other.
What is the House of Quality in Six Sigma?
The matrix used to connect customer requirements to internal process and product requirements is called the House of Quality, it contains: the features customers want in the order of importance. the capabilities the company can use to meet customer requirements.
How do you House quality?
House of Quality Steps are as follows:Identify what the customer wants.Identify how the product will satisfy customers. ... Identify relationships between how's. ... Develop importance ratings. ... Evaluate competing products or services. ... Determine the desirable technical attributes.
What is the first step in building the House of Quality?
Developing a house of quality goes through six steps. The first step is identifying the customer requirements. This stage entails establishing, elucidating and detailing customer's needs. Establishing of customer needs entails translating the customer's wish into some tangible value.
What is the difference between QFD and House of Quality?
Quality Function Deployment (QFD) is a structured approach followed by customer-driven organizations to transform customer requirements into their product specifications. The House of Quality (HOQ) is a diagram used by a product development team during the initial stage of the QFD process.
What is the definition of quality in Six Sigma?
"Six Sigma quality" is a term generally used to indicate a process is well controlled (within process limits ±3s from the center line in a control chart, and requirements/tolerance limits ±6s from the center line).
What is House of Quality with examples?
House of Quality refers to a well-known process for product development that is inspired by customer desires for product or process development and anchored by the capabilities and resources of the organization seeking to meet those desires.
What are the two qualities of good house?
The Top 7 Qualities of An Ideal House Built By The Good Real Estate DevelopersThe home should be airy and well-ventilated. ... The design of the interiors should be ergonomic. ... The material used in construction should be of good quality. ... The height of the ceilings should be between 10-12 feet.More items...•
How do I make a House of Quality template?
How to create a House of Quality (in Excel)Download a template. First off, you need a House of Quality template to proceed. ... Identify the customer's needs. ... Create importance ratings for customer needs. ... Identify product design requirements.
What are the 7 steps of quality?
7 Steps to Quality ImprovementStep 1: People.Step 2: Problem.Step 3: Aim.Step 4: Measures.Step 5: Change ideas.Step 6: Tests of change.Step 7: Spread. Now you have cracked the formula think about who else could benefit from your wisdom. Who might be facing a similar problem? Share your learning and knowledge.
What are the 5 steps of quality?
If playback doesn't begin shortly, try restarting your device....5 Steps to qualityAssessment (planning & context) ... Design (framework) ... Implement (do & establish) ... Certification (recognition) ... Improve (as measured, as needed)
What are the 5 stages of building a house?
6 Major Phases of the Home Building ProcessHome Building Phase #1: Plans and Permitting. ... Home Building Phase #2: The Site Work and Masonry Phase. ... Home Building Phase #3: Framing. ... Home Building Phase #4: Plumbing, Electric & More. ... Home Building Phase #5: Insulation, Drywall & Flooring.More items...•
What are the components of House of Quality?
A house of quality (HOQ) involves collecting and analyzing the “voice of the customer” and a key component of the Quality Functional Deployment technique. It is used to define the relationship between customer desires and the product or company capabilities.
What is the main part of the House in the House of Quality used for?
The House of Quality is used mainly in the Product Planning and Design phase and consists of a correlation matrix that is usually roof shaped and is found at the top of the main part of the matrix.
What are the 3 spheres of quality?
The spheres of quality consist of three components: quality management and planning, quality control, and quality assurance. The quality spheres are implemented in the organization to ensure the consistency of the production process.
What are the components of House of Quality matrix?
[2002] believed that the principal stages necessary for the construction of the first HOQ matrix includes: 1) Identifying customer requirements (CRs) and their perceptions, 2) Identifying product and engineering design requirements (ECs), 3)Drawing up a relationship matrix, 4)Planning and deploying expected quality (by ...
House of Quality: Definition, Process and Template - Toolshero
House of Quality: this article provides a practical explanation of the concept of House of Quality, developed by Yoji Akao and Shigeru Mizuno.. After reading, you will have a basic understanding of this powerful quality management tool.. This article contains a general definition of the concept of House of Quality, its elements, processes.
What is the House of Quality?
The house of quality is a kind of conceptual map that provides the means for interfunctional planning and communications. People with different problems and responsibilities can thrash out design priorities while referring to patterns of evidence on the house’s grid.
How did Toyota improve its rust prevention record?
In contrast, Toyota improved its rust prevention record from one of the worst in the world to one of the best by coordinating design and production decisions to focus on this customer concern. Using the house of quality, designers broke down “body durability” into 53 items covering everything from climate to modes of operation. They obtained customer evaluations and ran experiments on nearly every detail of production, from pump operation to temperature control and coating composition. Decisions on sheet metal details, coating materials, and baking temperatures were all focused on those aspects of rust prevention most important to customers.
What is a fiefdom today?
Today’s fiefdoms are mainly inside corporations. Marketing people have their domain, engineers theirs. Customer surveys will find their way onto designers’ desks, and R&D plans reach manufacturing engineers. But usually, managerial functions remain disconnected, producing a costly and demoralizing environment in which product quality and the quality of the production process itself suffer.
What does strategic quality management mean?
1 Strategic quality management means more than avoiding repairs for consumers. It means that companies learn from customer experience and reconcile what they want with what engineers can reasonably build.
How can companies reduce prelaunch time?
By looking first at customer needs, then designing across corporate functions, manufacturers can reduce prelaunch time and after-launch tinkering .
How does the house lead to the bottom line?
How does the house lead to the bottom line? There is no cookbook procedure, but the house helps the team to set targets, which are, in fact, entered on bottom line of the house. For engineers it is a way to summarize basic data in usable form. For marketing executives it represents the customer’s voice. General managers use it to discover strategic opportunities. Indeed, the house encourages all of these groups to work together to understand one another’s priorities and goals.
What is the purpose of a quality function deployment?
A set of planning and communication routines, quality function deployment focuses and coordinates skills within an organization, first to design, then to manufacture and market goods that customers want to purchase and will continue to purchase. The foundation of the house of quality is the belief that products should be designed to reflect customers’ desires and tastes—so marketing people, design engineers, and manufacturing staff must work closely together from the time a product is first conceived.
Understand Customer needs and desires
Many times, customers need outside perspective to discover what they really require to build their product or process. The goal is to understand customers perhaps in a better manner so that they understand themselves so as to open their eyes to ideal and best solutions available to them.
Understand the priorities of the Customer
During the interview stage, get to know the exact customer needs, but then break those needs down into prioritized parts in an effective manner.
Departmental Buy-In
Quite often, disagreement or misunderstanding between various departments of a customer’s organization can occur in relation to what is actually needed and required.
Translate Customer Desires into Goals & technicalities
This is at the heart of the QFD process where the recorded desires of the customer are ranked on the basis of the priority and specific process and where resource planning takes place. They are laid out onto a useful diagram labeled as the House of Quality.
Specify traceable requirements
Specific requirements for the execution of the customer’s product or process should be laid out in an effective and efficient manner.
Provide structure
It is quite easy for customers to jump all over the place stating what they desire and are tossing out the ideas. But, at the end of the day, your role is to hone in on what they actually want and provide a logical, executable, and the traceable structure to organize their ideas.
Allocate resources
Whether developing a physical product or creating the process for a customer, effective resources are required to do the same. Human resources, machinery, computer systems, construction materials, along with the disposable materials and more must be accounted for.
What is QFD?
House of Quality is a part of a larger process called QFD, which stands for Q uality, F unction, D eployment. This represents quality -monitoring, a focus on the function of execution of a quality plan, and the application of resources for deployment of that plan. While the name, QFD, does not encapsulate all that QFD covers, it is a name that has been around for quite some time. It is familiar, so organizations continue to use it. The House of Quality name comes from the very useful diagram used to make this plan that resembles a house, which we will dig into shortly.
What is the blue dotted line on a drone?
Referring to the blue dotted line, you see that there is a strong positive correlation between the unit’s weight and the noise output. When the weight goes up, the propellers must work harder to keep the drone suspended, so the noise level also goes up. Just below the roof, the up and down arrows indicate which direction the customer would like each engineering specification to go. For example, they want style up, noise level down, and battery run time up.
What is center grid?
The center grid containing symbols displays how strong a relationship each customer specification has to each
What is the customer specification?
The Customer Specifications section to the left lays out the specific priority features on which the customer has set focus. The numbers just to the right represent their importance to the customer on a scale of one to five. The Engineering Specifications section displays engineering methods needed to measure and execute production. At the base, the engineering specifications are detailed in specific measurements.
What is a house of quality?
House of Quality refers to a well-known process for product development that is inspired by customer desires for product or process development and anchored by the capabilities and resources of the organization seeking to meet those desires. It is a process of listening to customers, translating their desires into a written plan, ...
What is a customer listening plan?
It is a process of listening to customers, translating their desires into a written plan, prioritizing steps of execution based on what is most important to the customer, and putting a realistic plan on paper.
Why do customers need to be outside of their own perspective?
The goal is to understand customers perhaps even better that they understand themselves so as to open their eyes to ideal solutions. Understand Customer Priorities.
What is a VOC diagram?
VOC is a way of obtaining and implementing the customer’s stated needs and requirements for their services or products.
What is a HOQ?
The House of Quality (HOQ) is defined as a product planning matrix that is built to show how customer requirements relate directly to the ways and methods companies can use to achieve those requirements.
What is the purpose of identifying customer needs and requirements?
Identifying customer needs and requirements, then ensuring they are achieved, leads to customer satisfaction and loyalty.
Why is HOQ important?
HOQ is considered the primary tool used during quality function deployment to help facilitate group decision making. Benefits of building a House of Quality include: A customer’s needs and requirements are established, then used to build and prioritize service offerings and products.
What is technical benchmarking?
Technical benchmarking means determining how well both your organization and the competition fulfill customer needs in terms of design requirements.This work is usually performed by design staff to ascertain the capabilities of products or services, especially in comparison to the products or services of leading competitors.
What is the purpose of setting target values?
This action establishes concrete goals for the design engineers and further defines customer requirements. These values need to be measurable, and you can develop them from historical records, designed experiments, or analysis of what the competition is doing. Once the team agrees on the target values, enter them on the horizontal axis with the design requirements.
What is competitive benchmarking?
Competitive benchmarking compares one company against a selection of leading competitors. The company is evaluated based on how well or poorly it’s doing by examining and understanding the important aspects associated with its product or services.
What is the power of HOQ?
The power of HOQ is in the collaboration of team members, input of the customer, and the deep understanding of how to convert the customer whats to the design hows.
What is a HOQ?
House of Quality, or HOQ, is a product planning matrix that is used to show how your customer requirements relate directly to the actions you can take to achieve those requirements.
What is customer needs?
Customer needs: For each critical customer segment, capture customer feedback and VOC input consisting of your customer’s needs and the priority or weight of each need.
What is correlation matrix?
Correlation matrix: Compare CCRs to determine if they are in conflict with each other, leveraging each other, or have no effect on each other.
Why did hospitals create freestanding clinics?
A large hospital chain decided to create a chain of freestanding clinics for general medical practices to alleviate some of the pressure on their emergency rooms. The CEO, who had some Six Sigma training, decided to use QFD to design the clinic and patient experience.
What is your focus?
Your focus is on customer needs and how to meet them using specific and quantifiable targets and metrics.
Why is it important to design a process?
It will be important to coordinate with the rest of the organization to be sure that they understand how they can make your design tangible.
What is House of Quality?
The quality of products and/or services isn’t just important for businesses themselves, but especially for their customers. Customers decide what they think of a product/service. The better the quality in the opinion of the customers, the more likely that customers will have a positive response, come back, and recommend the product or service to others.
What is QFD in Lean Six Sigma?
QFD is part of the Lean Six Sigma quality system. It's a method to inventory customer wishes and market demands and to then include these in the design brief. This method enables organisation to focus even more on what their customers want. The result of the QFD method is a data matrix, also called 'the house of quality'.
What does QFD stand for?
Initially, QFD was used at Japanese shipyards, having resulted from Deming's PDCA cycle, which stands for Plan, Do, Check, and Act. Quality functions. The quality house is part of QFD and represents quality control.
How to find out what customers really want?
The first step is to find out what customers really want. That requires extensive research. Think of customer interviews, quest ionnaires, and collecting reviews. Complaints can also be a valuable source of information regarding what customers want exactly. Both existing customers and future customers can be useful sources of information. The goal of this phase is to get a better understanding of the customers’ wishes and to enable them to suggest their own ideal solution.
What is the most important score in an interview?
During this phase, you look at which customer wishes or requirements are considered the most important. This is indicated with ‘relative importance’. It involves assigning a score between 1 and 10, with 1 being least important, and 10 being most important. Interviews can be used to filter customer priorities. The value that a customer assigns to a certain specification or solution can also differ from what the manufacturer had in mind. For instance, a professional photographer might think that the quality of the lens and shutter time are more important than battery life.
When was QFD invented?
This house of quality can take on different shapes. In all cases, however, the representation will resemble a house. The QFD method was invented in 1960 by Japanese planning expert Yoji Akao and Japanese quality expert Shigeru Mizuno.
Why is quality house considered a part of Lean Six Sigma?
Because quality functions are being established, it's considered part of Lean Six Sigma. The quality house makes it easy to translate customer wishes and market demands into a design. In addition to function requirements, the functional specifications and technical design will also be considered.
What is the House of Quality (HOQ)?
A house of quality (HOQ) involves collecting and analyzing the “voice of the customer” and a key component of the Quality Functional Deployment technique. It is used to define the relationship between customer desires and the product or company capabilities.
What is a QFD?
Quality Function Deployment (QFD) and House of Quality (HOQ) is a structured approach for defining customer requirements and translating design specifications or product control characteristics in the form of a planning matrix. In other words, using QFD allows the charting of customer wants and the technical hows, which results in a better understanding of design relationships.
What is a triangular roof matrix?
The triangular “roof” matrix of the House of Quality is to identify how the design requirements interact with each other. It helps the designers in the next phase of QFD project. The triangular matrix looks like a house with a roof. The interrelations are rating strong positive as “+ +”, where as strong negative as “- -“and blank for no interrelation.
What is the first step in QFD?
The first step in a QFD is to determine the market segments and identification of prospective customers. Then team collects customer requirements for the product or service and rate on a scale of 1 to 5. With 5 being the most important and 1 being the least. Calculate the relative importance.
When was QFD developed?
Yoji Akao first developed quality Function Deployment in Japan in 1966 . QFD in the early stages of the design phase helps to incorporate all the customer needs into the final product. Furthermore, it is a planning tool to determine the key areas in which the effort should focus in relation to our technical capabilities.
What is product requirements?
Product requirements or technical characteristics are aligned to the voice of customer. This step can be quite difficult as it involves people working in groups to skim out the variable that may affect the customer requirement factors the most. Parameters should be meaningful, measurable, and global.
What is a customer driven process?
It is a customer-driven process for planning products and services. It helps to identify important parameters to include in the design. Allows to compare the design parameters with competitor products. Reduces the development time and cost-effective.
What are the benefits of the house of quality?
The first benefit comes from simply creating the diagram. Employees from different departmentscome together and collaborate on the house of quality. This inevitably leads to constructive discussions. The input from different departments ultimately ensures a high-quality, long-lasting, and successful product.
Why is QFD important?
The first and often most important matrix in QFD is called the house of quality because it’s shaped like a house with a roof and body.
What is the Kano model?
The “ Kano Model ” is another way to increase customer satisfaction in future projects. The perspective of the potential customer also plays a major role in this approach.
Why do we use market analysis to determine requirements?
You can also use other methods such as market analyses to determine requirements because even potential customers often don’t have a clear picture of what they need from a product. The list of customer needs is often referred to as the “ what ” versus the “ how ” of technical requirements.
How to find out what customers want?
This step involves the marketing team. You list all customer requirements that are relevant to the product. Conducting a survey is one way of finding out what customers want. You can also use other methods such as market analyses to determine requirements because even potential customers often don’t have a clear picture of what they need from a product. The list of customer needs is often referred to as the “ what ” versus the “ how ” of technical requirements.
How to solicit information for classifying requirements?
You can solicit the information you need for classifying requirements by conducting customer surveys or communicating with customers. You can then figure out which requirements you should focus on in the planning process. In our example, the range of functions is most important for customers.
What are the advantages of visualization?
Thanks to visualization, a lot of important information for planning and development is available at a glance. Teams can repeatedly consult the diagram with its graphs and matrices throughout the product development.
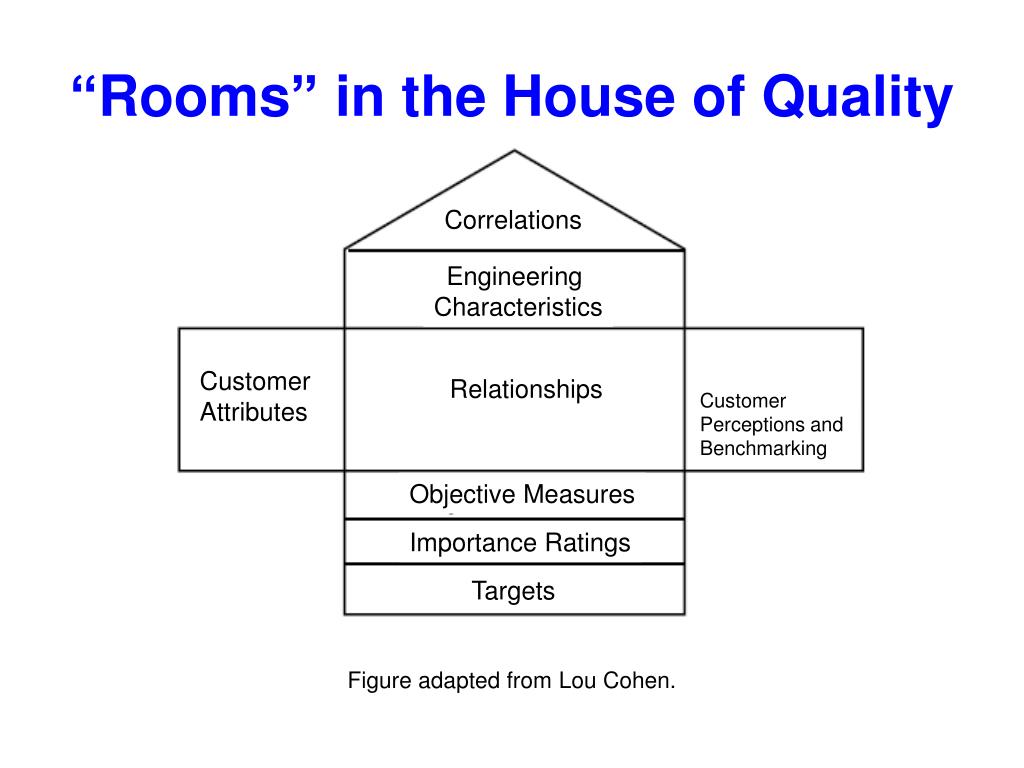
What’s So Hard About Design
Building The House
- There is nothing mysterious about the house of quality. There is nothing particularly difficult about it either, but it does require some effort to get used to its conventions. Eventually one’s eye can bounce knowingly around the house as it would over a road-map or a navigation chart. We have seen some applications that started with more than 100 customer requirements and more than …
Using The House
- How does the house lead to the bottom line? There is no cookbook procedure, but the house helps the team to set targets, which are, in fact, entered on bottom line of the house. For engineers it is a way to summarize basic data in usable form. For marketing executives it represents the customer’s voice. General managers use it to discover strategic opportunities. In…
The Houses Beyond
- The principles underlying the house of quality apply to any effort to establish clear relations between manufacturing functions and customer satisfaction that are not easy to visualize. Suppose that our team decides that doors closing easily is a critical attribute and that a relevant engineering characteristic is closing energy. Setting a target value for closing energy gives us a …
Anatomy of House of Qualities
Steps in House of Qualities
- Identify what are the exact needs and demands of the customer in the target market.
- Identify how the product will satisfy the targeted customer. house of quality refers to identifying specific product characteristics, features or attributes that the customer is looking for and sho...
- Identify relationships between How’s and What. A couple of questions, those are to be answe…
- Identify what are the exact needs and demands of the customer in the target market.
- Identify how the product will satisfy the targeted customer. house of quality refers to identifying specific product characteristics, features or attributes that the customer is looking for and sho...
- Identify relationships between How’s and What. A couple of questions, those are to be answered here: How do our how’s tie together? What is the relationship between our two or more how’s in the ent...
- Develop the importance of ratings as house of quality refers to using the customer’s importance ratings and weights from the relationships in the matrix to compute the important ratings.
Primary Purposes of QFD & House of Quality
- Understand Customer needs and desires
Many times, customers need outside perspective to discover what they really require to build their product or process. The goal is to understand customers perhaps in a better manner so that they understand themselves so as to open their eyes to ideal and best solutions available to them. - Understand the priorities of the Customer:
During the interview stage, get to know the exact customer needs, but then break those needs down into prioritized parts in an effective manner. For instance, if a customer is building drones for media production, how important is the battery life as compared to camera quality? How imp…
What Is QFD?
Primary Purposes of QFD & House of Quality
- We’ll now cover some primary purposes of QFD / House of Quality: 1. Understand Customer Desires Many times, customers need outside perspective to discover what they really need to build their product or process. The goal is to understand customers perhaps even better that they understand themselves so as to open their eyes to ideal solutions. 2. Understand Customer Prio…
House of Quality Diagram
- Below is an example of a House of Quality Diagram. We will now walk through a summary overview of its various parts. We continue our example of a media-production drone manufacturer. The Customer Specifications section to the left lays out the specific priority features on which the customer has set focus. The numbers just to the right represent their imp…
in Closing
- There are various levels of detail into which one can go using the House of Quality diagram. Some might include ratings for each engineering specification that indicate technical difficulty of execution, and so forth. But the example above is widely applicable and fairly detailed.