
Quality function deployment (QFD) is a method to transform qualitative user demands into quantitative parameters, to deploy the functions forming quality, and to deploy methods for achieving the design quality into subsystems and component parts, and ultimately to specific elements of the manufacturing process. Wikipedia
What is Quality Function Deployment QFD?
Quality Function Deployment (QFD) Definition: Quality Function Deployment, or QFD, is a model for product development and production popularized in Japan in the 1960s. The model aids in translating customer needs and expectations into technical requirements by listening to the voice of customer. What is Quality Function Deployment?
What is QFD and the House of quality?
Today QFD and the House of Quality can be found in various industries and are part of the Six Sigma toolbox. How Does Quality Function Deployment Work? The Quality Function Deployment process begins with collecting input from customers (or potential customers), typically through surveys.
What is the importance of product planning QFD?
Product Planning QFD. It helps identify service offerings characteristics, that best meet customer requirements, helps analyze competitive opportunities, and establishes critical target values too. Component Deployment QFD.
How do companies design quality into their products and services?
They actively design quality and customer perceived value into their products and services. These companies are utilizing a structured process to define their customer’s wants and needs and transforming them into specific product designs and process plans to produce products that satisfy the customer’s needs.
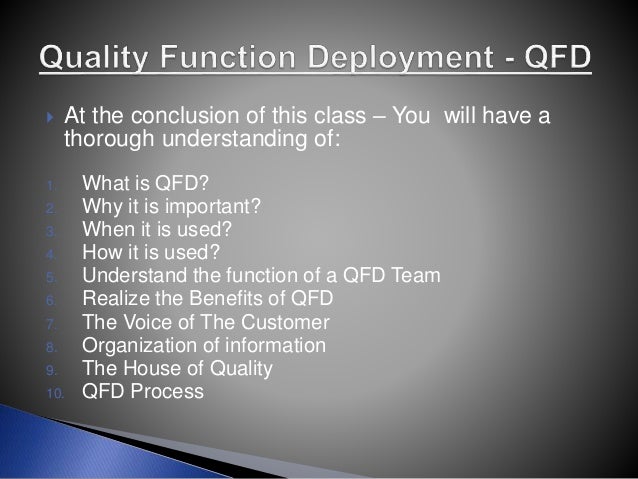
What does QFD mean?
Quality Glossary Definition: Quality function deployment (QFD) Also called: matrix product planning, decision matrices, customer-driven engineering. Every organization has customers. Some have only internal customers, some have only external customers, and some have both.
When should you use Quality Function Deployment?
Quality Function Deployment provides documentation for the decision-making process. QFD helps you to: Translate customer requirements into specific offering specifications. Prioritize possible offering specifications and make trade-off decisions based on weighted customer requirements and ranked competitive assessment.
What are the 4 phases of Quality Function Deployment?
The QFD Process Then, many phases of product quality deployment can be followed. Akao [4] has sited four phases of deployment: quality deployment, technology deployment, cost deployment and reliability deployment.
What do you mean by quality function development?
Quality Function Deployment can be described as a model used in Product Management that develops a product by prioritizing consumer - or customer - needs and preferences first.
What are the 8 steps of the QFD process?
Let's walk through the process of putting together a House of Quality example for a company building a new smartphone.Add customer needs and ratings. ... List design requirements. ... Weigh the relationship between customer needs and design requirements. ... Complete the correlation matrix. ... Add competitor research.
What is a QFD in Six Sigma?
Quality Function Deployment (QFD) is a process for planning products and services. It starts with the Voice of the Customer (VOC) which becomes the basis for setting requirements. From that, the organization identifies the what's – the most important needs of the VOC.
How many steps are there in QFD?
QFD is a four-phase process that takes your Voice of the Customer and translates that to customer requirements, then to specific part or component requirements, then to specific process requirements, and finally to quality control requirements.
At what stage QFD is implemented?
The Level 3 QFD is used during the Process Development Phase where we examine which of the processes or process steps have any correlation to meeting the component or part specifications.
What is QFD matrix explain with an example?
QFD is known by several names, such as matrix product planning, customer-driven engineering, and decision matrices. Regardless of the name, the point is the same: to take data from the customer and turn it into actionable steps in product development to satisfy needs and wants.
How do you do Quality Function Deployment?
Steps to the House of QualityStep 1: Customer Requirements – “Voice of the Customer” ... Step 2: Regulatory Requirements. ... Step 3: Customer Importance Ratings. ... Step 4: Customer Rating of the Competition. ... Step 5: Technical Descriptors – “Voice of the Engineer” ... Step 6: Direction of Improvement. ... Step 7: Relationship Matrix.More items...•
Why Quality Function Deployment is important?
Quality Function Deployment benefits companies primarily by ensuring they bring products to market that customers actually want, thanks to listening to customer preferences at the beginning of the design process.
What are the benefits of Quality Function Deployment?
Benefits of Quality Function Deploymentprioritize spoken and unspoken customer wants and needs;determine and translate customer needs into technical characteristics and specifications;build and deliver a quality product or service by focusing all employees toward customer satisfaction.More items...•
Why would a company choose to use a QFD?
So why should a company use QFD? It should be used because it is aimed at satisfying the customer throughout the whole business process from product/service development to delivery. It helps organizations reach agreement on measurement systems and performance specifications that will meet customer requirements.
Why quality function deployment is important?
Shorter Development Time and Lower Cost: QFD reduces the likelihood of late design changes by focusing on product features and improvements based on customer requirements. Effective QFD methodology prevents valuable project time and resources from being wasted on development of non-value added features or functions.
What are the benefits of quality function deployment?
Benefits of Quality Function Deploymentprioritize spoken and unspoken customer wants and needs;determine and translate customer needs into technical characteristics and specifications;build and deliver a quality product or service by focusing all employees toward customer satisfaction.More items...•
What is quality function deployment explain with suitable example?
• Quality function deployment or "QFD" is a flexible and comprehensive Decision making technique used in product or service development, brand marketing, and product management • Quality Function Deployment (QFD) is a structured approach defining to customer needs or requirements and translating them into specific ...
What is Quality Function Deployment?
Although it might sound like a modern testing methodology, Quality Function Deployment (QFD) has a 50-year track record of putting customer needs first throughout the entire product development process. Focusing consistently on customer desires, QFD ensures these are always considered during both the design process and various quality assurance milestones throughout the entire product lifecycle.
What are the Advantages and Disadvantages of Quality Function Deployment?
Quality Function Deployment benefits companies primarily by ensuring they bring products to market that customers actually want, thanks to listening to customer preferences at the beginning of the design process. Then, mandating these needs and desires is met throughout every aspect of the design and development process. In short, if something isn’t being built because a customer wants it (or it provides underlying support for a customer need), it doesn’t get built at all, which can prevent technology from driving strategy when it’s not directly beneficial to the customer experience.
How did QFD impact the design process?
Once adopted, QFD shortened design cycles significantly and reduced the total number of employees required in the design process. Shifting the focus from bottom-line cost analysis to customer satisfaction brought innovations and increased sales of domestic vehicles after the surge in popularity of Japanese imports in the 1970s.
Why is customer input important in product development?
Since collecting customer inputs and applying them throughout the product development process is such a cross-functional activity, it can also increase teamwork and ensure the entire organization is aligned around customer satisfaction instead of competing with other internal priorities.
When was QFD introduced?
Developed in 1960s Japan, QFD was imported to the United States in the early 1980s and caught on thanks to its popularity and successful track record in the automotive industry. Copying the model from manufacturers such as Toyota and Mitsubishi, the “big three” American car makers used QFD to bring customer centricity to their industry.
When is QFD appropriate?
QFD is most appropriate when companies are focused on relatively iterative innovation versus something completely new since there is a large base of customer feedback and input to drive the process. When a product is creating a completely new category, it’s more difficult to fully articulate the voice of the customer since they don’t necessarily have a frame of reference, but even in these cases carrying forward what is known about customer needs and preferences can provide value.
When to use QFD?
It is most effective when used throughout the entire product lifecycle, as its main purpose is to ensure a constant focus on the voice of the customer. You can’t “check it off” as completed since it is an ever-present ingredient every step of the way.
What happens at the end of the Quality Function Deployment process?
At the end of the Quality Function Deployment process, a clear catalog of measures will be produced. The knowledge gained must now be communicated and implemented in product development, product management, production, sales, and marketing.
What is the purpose of QFD?
The main aim of QFD is to improve a product or service so that it will be better received by the market. The focus here is also on customer satisfaction. Ideally, it’s best to apply QFD during the product planning phase, but you can also make adjustments to the product later on the basis of a QFD analysis.
What is QFD in business?
This technique allows you to systematically work out customer requirements and then present them in a clear way. QFD is mainly used in quality management, but it is also used in product management and product development. Ultimately, this method involves all areas of the company.
What is QFD in manufacturing?
Quality Function Deployment (QFD) is a systematic analysis of customer requirements that is used to improve the quality of your products. QFD originated in Japan in the 1960s and 70s and was primarily developed by Yōji Akao. Mitsubishi and Toyota, as well as many other companies, have used this method to better tailor their products and services to their target market and accelerate growth. As part of this method, customer requirements, product performance, and the products offered by the competition are all taken into consideration.
What are the advantages of QFD?
Another advantage of Quality Function Deployment – when implemented early and effectively – is that it can reduce development costs and times. As this method focuses on customer requirements with a well-thought-out method and is not based on assumptions, you can use it to make specific plans. Not only does QFD support companies by helping them to increase their revenue, but it also helps them to work in a more streamlined manner during production.
What to ask yourself during product development?
The first thing to ask yourself during the product development phase is who the product is aimed at or who will buy it later. You must also think about the distinction between B2B and B2C – a relatively banal subject. Next, you must consider information such as income, gender, marital status, age, and level of education. Finally, you may have to make some assumptions about details that are more difficult to measure, such as the requirements, standards, and values of potential customers.
Is quality function deployment a fixed model?
Quality Function Deployment is not a rigid, fixed model. It has undergone many further developments since it was first used by Yōji Akao (e.g. such as those implemented by Bob Kind or Emil Jovanov). Even Akao himself believed that it was incredibly important for each person to adapt the concept to their own situation. Something that all variants of the method have in common is that they proceed step by step, starting with a customer survey and finishing with production or the product launch.
Why is QFD important to understand?
Understanding this linkage and the cascading of the how of one phase feeds into the what of the next phase is the secret of being able to successfully use QFD.
What is the first phase of product planning?
Product Planning Matrix: The first phase starts with your collection of the VOC and translates your customer wants and needs into specific product and service requirements and specifications. It also involves a competitive analysis to evaluate how well your competitors fulfill your customer wants and needs. The initial design concept is based on the particular product and service performance requirements and specifications. This first House is referred to as the House of Quality and is the foundation of your QFD process.
Why is QFD important?
Every business, organization, and industry has customers. Meeting your customers’ needs is critical to success. Implementing QFD can enable you to drive the voice of your customers throughout your organizational processes to increase their satisfaction and delight.
What is QFD in Six Sigma?
A structured methodology and mathematical tool used to identify and quantify customers’ requirements and translate them into key critical parameters. In Six Sigma, Q FD helps you to prioritize actions to improve your process or product to meet customers’ expectations.
What is part deployment matrix?
Part Deployment Matrix: During this phase, the assemblies, systems, sub-systems, and components that have the most impact on meeting your product and service design requirements are identified. The critical product and service characteristics cascade down and are translated into critical parts and assembly characteristics or specifications as well as steps of a service process. These requirements or specifications are then defined for each relevant functional area.
What is the power of QFD?
The power of QFD is that it is your customers’ needs driving the technology, and not the technology driving your customers’ needs.
When was QFD invented?
QFD was developed in Japan by Yoji Akao in about 1966 while working for Mitsubishi. Toyota and other auto manufacturers started using the approach later on.
What is QFD in product development?
Structure and Documentation: QFD provides a structured method and tools for recording decisions made and lessons learned during the product development process. This knowledge base can serve as a historical record that can be utilized to aid future projects.
What is QFD process?
Process Quality Control: Prior to production launch, the QFD process identifies critical part and process characteristics. Process parameters are determined and appropriate process controls are developed and implemented. In addition, any inspection and test specifications are developed. Full production begins upon completion of process capability studies during the pilot build.
How does QFD reduce late design changes?
Shorter Development Time and Lower Cost: QFD reduces the likelihood of late design changes by focusing on product features and improvements based on customer requirements. Effective QFD methodology prevents valuable project time and resources from being wasted on development of non-value added features or functions.
What is QFD in manufacturing?
Quality Function Deployment (QFD) is a process and set of tools used to effectively define customer requirements and convert them into detailed engineering specifications and plans to produce the products that fulfill those requirements. QFD is used to translate customer requirements (or VOC) into measureable design targets and drive them from the assembly level down through the sub-assembly, component and production process levels. QFD methodology provides a defined set of matrices utilized to facilitate this progression.
What are the phases of QFD?
The four phases of QFD are: Product Definition: The Product Definition Phase begins with collection of VOC and translating the customer wants and needs into product specifications. It may also involve a competitive analysis to evaluate how effectively the competitor’s product fulfills the customer wants and needs.
What is a QFD house of quality?
VOC Competitor Analysis: The QFD “House of Quality” tool allows for direct comparison of how your design or product stacks up to the competition in meeting the VOC. This quick analysis can be beneficial in making design decisions that could place you ahead of the pack.
Why is QFD important?
The fact is that every business, organization and industry has customers. Meeting the customer’s needs is critical to success. Implementing QFD methodology can enable you to drive the voice of your customers throughout your processes to increase your ability to satisfy or even excite your customers.
What is quality function deployment?
There is no single definition for quality function deployment, but a general basic concept of this method is as follows: “Quality Function Deployment is a system with the purpose of translating and planning the VoC into the quality characteristics of products, processes and services for reaching customer satisfaction”.
What is component deployment QFD?
Component Deployment QFD. It helps identify the critical parts and assembly components using the prioritized offering characteristics in QFD 1 and establishes critical target values.
Why is QFD important?
QFD is not only a quality tool but also an important planning tool. It allows the consideration of the “voice of the customer” along the service development path to market entry.
What is QFD matrices?
QFD matrices also called “the house of quality”, are graphical displays of the result of the planning process. QFD matrices vary a great deal and may show such things as competitive targets and process priorities.
What is QFD in service design?
The QFD technique is based on the analysis of the clients’ requirements, which normally are expressed in qualitative terms, such as: “easy to use”, “safe”, “comfortable” or “luxurious”. In order to develop a service, it is necessary to “translate” these fuzzy requirements into quantitative service design requirements;
What is QFD in engineering?
In this approach, design engineers typically start progressive drill-down approach with planning the development and go through four phases to reach a deeper understanding of the required process control and quality. The details are as follows:
When was QFD first used?
History of QFD. The tool was first used to design an oil tanker at the Kobe shipyards of Japan in 1972 by Yoji Akao and Shigeru Mizuno to design customer satisfaction into a service offering before it is produced. Prior to this, quality control methods were primarily aimed at fixing a problem during or after production.
What is quality function deployment?
Therefore, quality function deployment is creating great value products by listening to what customers want and need and making plans to create products that fulfill those needs.
How does Roy help customers?
He can use the reviews his store has been receiving, send out surveys in the mail or on social media, or do some research in the industry and find out what other companies have been hearing from customers as well. Then he can begin to accommodate the customer by making products that meet their needs.
How does Roy know what satisfies his customers?
How will Roy know what satisfies his customers? Well, he learns that a good place to start is with the voice of the customer, which refers to the needs of the customer expressed by the customer.
What does "satisfied customers" mean?
1. Satifies the customer. Satisfied customers keeps Roy in business, as well as helps to spread a good reputation.
What is quality function?
Quality function deployment is a way of understanding what customers want and need and then creating products to meet those wants and needs. The entire process starts with the voice of the customer, in other words their needs, which need to be determined using surveys, or other methods of communication with them. It is then followed with house of quality which is the task of planning products that customers want. Quality function deployment is beneficial because it helps satisfy the customer, it is a comprehensive process, and it helps a company stay competitive.
What is the product that customers are unhappy about?
One product that customers are unhappy about is the pop up tent. When customers go to open the tent, sometimes it gets tangled up and does not pop up correctly. While the tent can be untangled and still used, customers prefer a tent that is less labor intensive and works correctly every time.
What is the task of planning products that customers want called?
The task of planning products that customers want is known as house of quality.
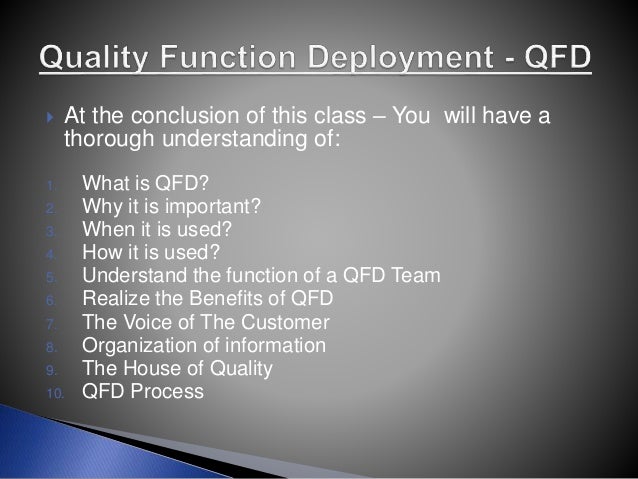