
Mechanical deaeration is the first step in eliminating oxygen and other corrosive gases from the feed water. Free carbon dioxide is also removed by deaeration, while combined carbon dioxide is released with the steam in the boiler and subsequently dissolves in the condensate. This can cause additional corrosion problems.
What is the difference between mechanical deaeration and chemical deaerator?
Mechanical Deaeration considered as a first stage process where most of the dissolved gases are escaped from water. On the other hand chemical Deaeration is acts as a polishing process which can remove trace amount of dissolved gases by adding proper oxygen scavenger chemicals in deaerator. Basically, Deaerator works based on two gas law.
What is deaeration process in deaerator?
Deaeration process in deaerator accomplished in two simple steps: First Step: Water is heated by steam within a few degree of its saturation temperature according to deaerator’s operating pressure. Approx. 97-98% of dissolved gases released with the steam & escaped from the vents of deaerators.
What is mechanical deaeration in a boiler?
Swapan Basu, Ajay Kumar Debnath, in Power Plant Instrumentation and Control Handbook (Second Edition), 2019 Though not a direct part of the boiler, this provides mechanical-type deaeration for the removal of the dissolved gases (CO2 and O 2) that are highly desirable for a boiler’s safe operation.
What does a deaerator do in a boiler?
Although not a direct part of the boiler, a deaerator provides mechanical-type deaeration for the removal of the dissolved gases (CO2 and O 2 ), which is highly desirable for safe boiler operation. The same is accomplished prior to dose chemical oxygen scavengers (hydrazine) by heating feedwater with steam.
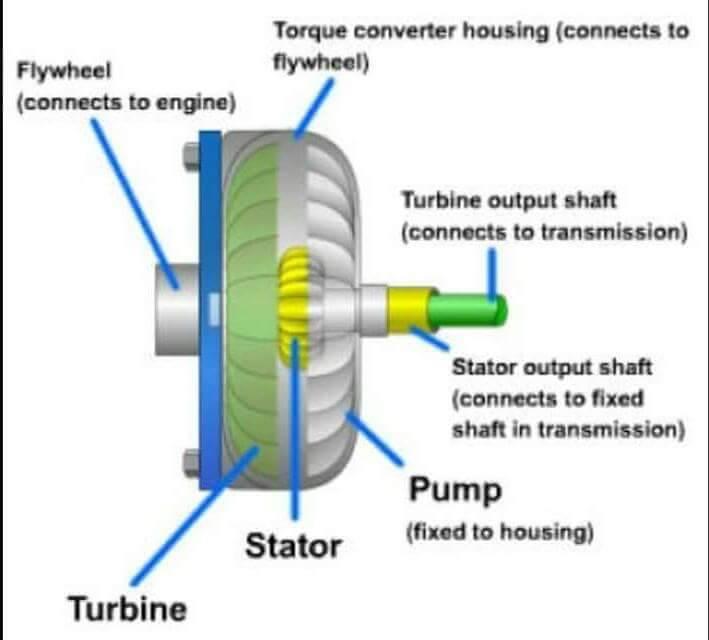
What is deaeration method?
The deaeration process is used to reduce corrosion and to remove dissolved gases in specific boiler feed water systems. The presence of dissolved gasses like oxygen and carbon dioxide causes accelerated corrosion that shortens the lifespan and reduces the efficiency of a boiler system.
What is deaeration vessel?
A deaerator is a device that is widely used for the removal of air and other dissolved gases from the feedwater to steam generating boilers.
What is the purpose of a deaeration tank?
What are Deaerator Tanks : The Deaerator tank in boiler acts as a Feed Water Tank to store cold and hot fluid in order to remove dissolved air or non-condensable gases from the fluid. Deaerating feed tank helps in removing non-condensable gases from a feed.
What is deaeration corrosion?
Deaeration is the process by which air is removed from a substance where the air has mixed with or dissolved in the substance. Deaeration is used for liquids, soils and foods to improve their quality and reduce contamination, and to remove oxygen from vessels that contain liquids to reduce the corrosion rate.
Is a deaerator a pressure vessel?
Deaerators are large, insulated tank-car-shaped pressure vessels. They produce preheated boiler feedwater to help ensure efficient steam-plant operation. Deaerators come in numerous sizes and shapes, depending on boiler-plant design, capacity, and system pressure rating.
What is the capacity of deaerator?
Deaerator, Capacity: 5000-10000 L.
What is also known as deaerator?
Deaerators are pressurised feedwater tanks also referred to as open feedwater heaters. Deaerators are critical components of many steam systems and have several functions: Remove non-condensable gases from boiler feedwater.
How oxygen is eliminated in boiler?
Boiler deaerators commonly are used to remove oxygen and other gases from the water that feeds into boilers that generate steam. Deaerators are useful because they remove the gases that attach to the metallic components of the steam system and cause corrosion by forming oxides, or rust.
How is oxygen removed from deaerator?
In a bubbling device deaerator, oxygen is removed following preheating of the water, through intimate contact of steam and water moving over perforated plates. In power generating stations, main turbine condensers have air ejectors to remove dissolved gases.
What should be the o2 concentration in boiler feed water?
Atmospheric boiler-feed tanks are normally operated at approximately 85-95 °C, which leaves an oxygen content of around 2mg/liter (ppm). It is not possible to operate at higher temperatures due to the possibility of cavitation in feed pump and close proximity to saturation temperature.
Is a deaerator a heat exchanger?
The deaerator serves as an “open” type heat exchanger with its primary function being the removal of oxygen and other corrosive gases from the boiler feedwater. This is accomplished using steam, which can give up about 970 Btu per pound, to support the deaeration process as well as preheat boiler feedwater.
What is deaerated water?
Deaeration of water at the deaerator is done to remove DO, carbon dioxide, and other noncondensable gases as well as to heat the water to the temperature where solubility of undesirable gases are at a minimum.
Why do deaerator boilers feed water?
The purpose of a deaerator is to reduce dissolved gases, particularly oxygen, to a low level and improve a plant's thermal efficiency by raising the water temperature. In addition, deaerators provide feedwater storage and proper suction conditions for boiler feedwater pumps.
How do you size a deaerator?
To calculate elevation of stand, determine required NPSH of pump from pump curve and add 2 feet of head as safety factor. The result is the MINIMUM required stand height. Each pump on a deaerator is sized based on the total load of boilers fed by the specific pump.
How does deaeration work?
Deaeration of water is accomplished by decreasing the concentration of the offending gas species (O2 , CO 2 , NH 3 , H 2 S) over the water sometimes with heating of the water, which decreases the solubility of most gases (e.g., Fig. 15.1 [Volume 2] for oxygen). This can be accomplished by applying a vacuum over the water, a method suitable for water distribution systems. However, the gases over boiler water are usually purged (flushed away) with the use of steam. Steam does not contaminate the water and raises the temperature of the water (which must be done anyway), thereby decreasing the solubility of the gases.
What is deaeration in the environment?
A particularly common case is deaeration of the environment, likely by the addition of reducing agents such as sulfites, carbohydrazide, etc. , that is, deaeration which for example guarantees the resistance to SCC of austenitic stainless steels in near-neutral chloride environments.
Why is steam used in boiler deaeration?
Though not a direct part of the boiler, this provides mechanical-type deaeration for the removal of the dissolved gases (CO2 and O 2) that are highly desirable for a boiler’s safe operation. The same is accomplished prior to dose chemical oxygen scavengers (hydrazine) by heating feed water by steam to reduce the concentration of oxygen and carbon dioxide from the feed water. Being most economical, it can reduce the oxygen content up to 0.005 mg/L. Steam is preferred for deaeration because steam is essentially free of O2 and CO 2. Readily available steam adds the heat required to complete the process.
What is the purpose of deaeration?
II.G.1 Mechanism. Deaeration is used to remove dissolved corrosive gases from plant water streams. The most important application is the removal of oxygen from boiler feedwater systems. A dissolved gas can be removed from water by reducing the partial pressure of that gas in the atmosphere contacting the liquid.
What are the two types of pressure deaerators?
The two major types of pressure deaerators or deaerating heaters are the tray type and the spray type. A typical tray-type deaerating heater is illustrated in Fig. 8.
Can a new pump be linked to a deinking machine?
The new pump can be linked directly to the deinking machine and forms a clean and closed disposal system. Because it can be placed at the same level as the flotation cells, the entire flotation system saves more space than previous systems. A cellar or an additional floor height for the flotation is no longer required.
What is Deaerator?
Deaerator is a mechanical equipment that removes dissolved gases mainly dissolved oxygen & other non-condensable gases from boiler feed water. Oxygen causes pitting type corrosion in feed water systems. The process of removing dissolved gases from water also known as mechanical Deaeration.
How does a deaerator work?
Basically, Deaerator works based on two gas law. Henry’s Law (scrubbing with oxygen free steam): The amount of dissolved gases present in water is directly proportional to the partial pressure of that gas in the vapor space above the water/gas interface.
Why is a deaerator placed at height?
Deaerator placed at height because it provides required NPSH (Net Positive Suction Head) for boiler feed pump to avoid cavitation at the suction of boiler feed pump.
What are the sections of a spray deaerator?
Spray deaerator consist of horizontal vessel (see above figure) & which has two sections namely preheating section and Deaeration section. Both the sections are separated by a baffle.
What is Henry's law?
Henry’s Law (scrubbing with oxygen free steam): The amount of dissolved gases present in water is directly proportional to the partial pressure of that gas in the vapor space above the water/gas interface.
What are the operating principles of water droplets?
Operating Principles: Formation of fine water droplets by spray nozzles (Henry’s law) Steam heats the fine water droplets near to saturation temperature (Charles’ law) Mechanical scrubbing of dissolved oxygen and other non-condensible gases from droplets by oxygen-free steam.
What Does Deaeration Mean?
Deaeration is the process by which air is removed from a substance where the air has mixed with or dissolved in the substance. Deaeration is used for liquids, soils and foods to improve their quality and reduce contamination, and to remove oxygen from vessels that contain liquids to reduce the corrosion rate.
How is deaeration achieved?
Deaeration of liquids (usually water) is achieved by passing the liquid through a tank (known as a deaeration tank) where reactions occur that remove the dissolved oxygen. Uses of deaeration include: Processing feedwater for steam boilers. Steam turbine systems. Thermal power plants.
Why is deaeration used in food?
Deaeration is used for liquids, soils and foods to improve their quality and reduce contamination, and to remove oxygen from vessels that contain liquids to reduce the corrosion rate.
What is mechanical separation?
Mechanical separation equipment employs mass differences, size differences, or a combination of both to selectively reject undesirable solids and retain desirable solids in a drilling fluid.
How to tell the difference between mechanical and thermal separation?
The basic difference between mechanical and thermal separation is that the productivity of the latter is limited whereas the productivity of the former is not. This property follows from the power constraint p ≤ pmax and the monotonic increase of productivity g with power p. The limiting productivity of thermal separation in gases can be found by solving a power equation with respect to g and then by substituting a known formula for pmax to the result obtained. With this approach, charts can be obtained that depict the dependence of maximum productivity on the concentration of a key component in the initial mixture and on the degree of separation ( Tsirlin and Kazakov, 2002a,b ).
How is heat used in thermal separation?
Heat is the form of energy flow that is frequently used in separation operations. In these operations, heat is received from a reservoir or source of high temperature T+ and rejected into a low- T reservoir, at temperature T−. The estimates for irreversible separation work or power allow us to estimate the lower bound for heat used in thermal separation. Whenever a minimal power pmin is lower than the maximum power pmax of a heat engine working between temperatures T+ and T−, then, an irreversible separation process can be accomplished for a prescribed productivity g and fixed concentrations in input and output streams ( Eq. 8.40 in Chapter 8 ). Expressions for maximum power pmax are known from the theory of CNCA engines and their generalizations. Eq. (8.14) of Chapter 8 can then be applied to find estimate for heat consumption after substitution into it the relevant minimum entropy production. As a general formula for σs in terms of power, p is valid:
What is extraction and storage?
Extraction and storage method is the simple extraction of contaminated soil cover, using a digger or bulldozer, and its storage in an appropriate place for further cleanup using another method (e.g., biodegradation and vitrification). The storage site has to be sheltered to prevent wind and water erosion.
What is the first stage of recycling?
During mechanical separation (often the first stage of recycling), the battery is milled and materials are separated from each other considering their properties such as density, conductivity and behavior in a magnetic field. This process includes removing housing, skinning, crushing, shredding, shearing and sieving. For safety reasons, spent batteries are immersed in liquid nitrogen before mechanical treatment. Today, mechanical treatment is done under a protective atmosphere instead of immersion in liquid nitrogen. The disadvantage of a mechanical process lies in the incomplete separation of all materials: for this reason, this process is often only the first stage of a recycling process.
What is the process of separation of soil?
The mechanical separation of soil is a physicochemical process in which the contaminated parts of soil are separated. This process leads to a decrease in volume of contaminated soil. The techniques most often used for separation are gravitational separation (based on differences in density between fractions) or in cyclones (based on the Coriolis effect) and sieve analysis (different grain size of elements) or magnetic separation (based on magnetic induction). The separated fraction containing the pollutants must be cleaned up or neutralized in another process. The advantages of this method are significant volume reduction of contaminated soil, and for many years, this technique has been applied in municipal waste management. The disadvantages of this method are the following: this technique could not be applied in the case of homogenous distribution of pollutants in soil. In that case, there is no satisfactory decrease in volume. This method is not effective for some soil types. The separated part of the contaminated soil must be cleaned up using another method.
Where is the waste incineration power plant?
The introduction of technological process is based on a waste incineration power plant in Foshan city, Guangdong province, China. The designed municipal solid waste (MSW) disposal capacity is 700 t/day, with the BA production of 140–210 t/day. A series of technologies including crushing, sieving, and sorting are applied and good results are obtained. The amount of separated wastes for scrap metal and MSW residue is 4–5 and 40–50 t, respectively, and the rest are BA. The BA has a stable characteristic and uniform size distribution, which can meet the standard for utilization. The process flow diagram of mechanical separation of BA of municipal solid waste incinerator is shown in Fig. 3.20.
What is a deaerator?
A deaerator is a device that removes oxygen and other dissolved gases from liquids and pumpable compounds.
How does a thermal deaerator work?
Thermal deaerators are commonly used to remove dissolved gases in feedwater for steam-generating boilers. Dissolved oxygen in feedwater will cause serious corrosion damage in a boiler by attaching to the walls of metal piping and other equipment and forming oxides (like rust). Dissolved carbon dioxide combines with water to form carbonic acid that may cause further corrosion. Most deaerators are designed to remove oxygen down to levels of 7 ppb by weight or less, as well as essentially eliminating carbon dioxide. The deaerators in the steam generating systems of most thermal power plants use low pressure steam obtained from an extraction point in their steam turbine system. However, the steam generators in many large industrial facilities such as petroleum refineries may use whatever low-pressure steam is available.
What is a spray type deaerator?
As shown in Figure 2, the typical spray-type deaerator is a horizontal vessel which has a preheating section (E) and a deaeration section (F). The two sections are separated by a baffle (C). Low-pressure steam enters the vessel through a sparger in the bottom of the vessel.
How to increase life of deaerator?
First, regular inspections (and testing) of the pressure vessel for cracking of welds, and repairing of any weld defects. Second, maintaining a proper water chemistry to reduce deaerator deterioration. Third, minimize temperature and pressure fluctuation. Fourth, internals and accessories should be inspected for proper operation.
How to prevent deaerator deterioration?
Second, maintaining a proper water chemistry to reduce deaerator deterioration. Third, minimize temperature and pressure fluctuation.
How much oxygen is removed by a deaerator?
Most deaerators are designed to remove oxygen down to levels of 7 ppb by weight or less, as well as essentially eliminating carbon dioxide. The deaerators in the steam generating systems of most thermal power plants use low pressure steam obtained from an extraction point in their steam turbine system.
When did the Navy buy the atomizing deaerator?
In 1934 the US Navy purchased an atomizing deaerator. Before 1867, deaerators were used as part of the ice manufacturing purification process. In 1899, George M Kleucker received a patent for an improved method of deaerating water. During the 1920 the feedwater headers and deaerators designs improved.
What is a spray type deaerator?
The spray type is a cylindrical tank that both deaerates the feed water and stores it.
What is boiler deaerator?
Boiler deaerators feature a mechanical design that enables them to use steam pressure and temperature to condition feed water. When the temperatures, pressure, and dissolved oxygen levels are within design limits, boiler deaerators operate at maximum efficiency. It is important to check the temperature and pressure daily and log ...
How to determine if boiler deaerator is working?
To determine how effectively your boiler deaerator is operating, you should conduct regularly scheduled annual dissolved oxygen studies (DO2 studies) to measure the dissolved oxygen level at the deaerator’s outlet. Physical inspections of deaerators also show whether an internal component failed. Be prepared to obtain a sample from the deaerator’s storage section and to disconnect the oxygen scavenger system from the deaerator while the feed water sample is being collected.
How does a boiler deaerator work?
Regardless of the type of boiler deaerator, each functions generally in the same way. When water passes from the feed water tank into the boiler deaerator, it enters through the inlet water connection. The water flows through a heating and venting section that is filled with steam. The water temperature rises, which releases most of the undissolved gases in it including oxygen and carbon dioxide. When the water flows through the deaerator, it passes to the scrubber section. It is in this section where the last step of deaeration takes place because it scrubs the water with steam that is free of oxygen.
Why do boilers need deaerators?
Boiler deaerators commonly are used to remove oxygen and other gases from the water that feeds into boilers that generate steam. Deaerators are useful because they remove the gases that attach to the metallic components of the steam system and cause corrosion by forming oxides, or rust. Both oxygen and carbon dioxide are responsible for corrosion, ...
What happens when water flows through a deaerator?
When the water flows through the deaerator, it passes to the scrubber section. It is in this section where the last step of deaeration takes place because it scrubs the water with steam that is free of oxygen.
Why is a boiler deaerator important?
Boiler deaerators serve a critical role in protecting steam systems from corrosion. It is important to understand how they operate and how to eliminate dissolved oxygen in the deaerator with the assistance of oxygen scavengers in order to determine whether your boiler deaerator is operating efficiently. Image via Pixabay by akiragiulia.
WHAT NEEDS TO HAPPEN FOR DEAERATION TO OCCUR?
1. Temperature – Water cannot absorb gasses when it is heated to saturation temperature. Water also only releases gasses when it reaches saturation temperature.
How does a deaerator work?
While there are many types of deaerators, they generally behave the same. Feedwater enters the DA through an inlet water connection. The steam in the tank then interacts with the make-up water which raises the water’s temperature. This breaks oxygen and other undissolved gasses up and allows them to escape through a vent located at the top of the DA tank.
What is a spray type deaerator?
The typical spray-type deaerator is a horizontal vessel which has a preheating section and a deaeration section. A baffle separates the two sections. Low-pressure steam enters the vessel through a sparger in the bottom of the vessel.
How is feed water deaerated?
The preheated feed water then flows into the deaeration section, where it is deaerated by the steam rising from the sparger system.
What is low pressure deaeration?
Low-pressure deaeration steam enters below the perforated trays and flows upward through the perforations. Some designs use various types of packed bed, rather than perforated trays. This provides good contact and mixing between the steam and the boiler feed water.
What is the purpose of a deaerator tank?
Deaerator tanks serve 3 primary purposes. 1.They store and supply consistent water to the boiler. 2.They bring the temperature of the water up before it supplies it to the boiler. They do this by mixing fresh make-up water with steam. This helps to prevent thermal shock as well as improve overall boiler room efficiency.
How to contact a boiler deaerator?
If you’re experiencing deaerator problems that have you stumped, reach out for a free estimate, call us at 1-800-237-3141 or chat with an agent. Our team is here to help!
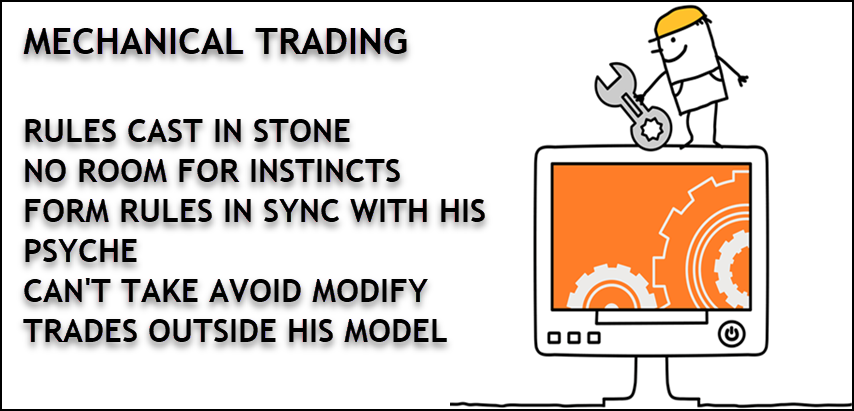