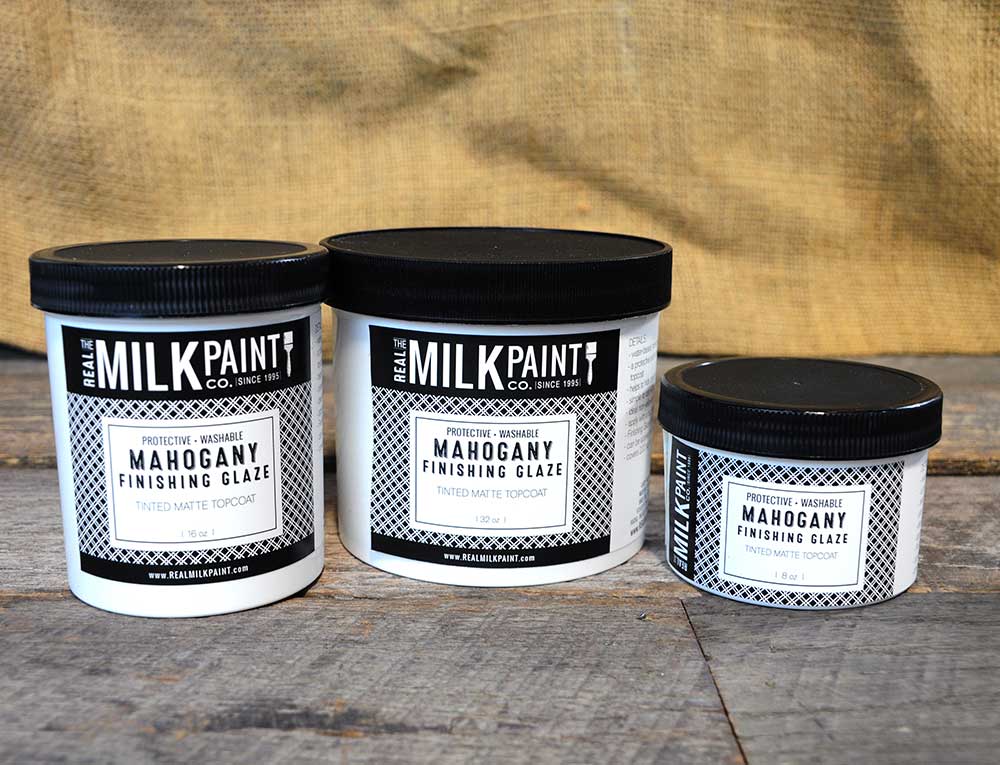
What is phosphate and oil finish? Phosphate & Oil Phosphate is a chemical conversion process that creates an insoluble lattice of crystalline phosphate on a metal surface. Once applied, the phosphate coats uniformly, is non-conductive and resists corrosion.
What is the process of'phosphate and oil'?
Can you please explain me in detail the process of 'Phosphate and oil'. Hello, Jayarajan. Phosphate and oil simply means to phosphate the part (probably zinc phosphate, maybe manganese phosphate), and then dip it in corrosion preventative oil.
What is phosphate coating?
Some of the threaded parts are treated with phosphate coatings, which improves their anti-galling and rust inhibiting characteristics. Zinc phosphate coatings are used as Chemical Agent Resistant Coating (CARC) paints on military equipment including munitions, aviation, and ground.
What is a phosphate finish on a gun?
The color of the pieces, once phosphatized, will vary from medium-grey to black, depending on which ingredients were used. A phosphate finish is mil-spec, meaning that it meets military specifications. This makes guns with a phosphate finish popular as military weapons. This finish is durable and erosion-resistant.
What is the meaning of phosphate and oil dip?
Hello, Jayarajan. Phosphate and oil simply means to phosphate the part (probably zinc phosphate, maybe manganese phosphate), and then dip it in corrosion preventative oil. Letter 7605 will be a brief introduction.
What is Jackson tumble finish?
What is calcium modified fine zinc phosphate used for?
What is phosphate coating?
What is dry to touch lubricant?
Does zinc phosphate extend shelf life?
Does manganese phosphate coating work?
See 1 more

What is Phos and oil coating?
Phosphate coating is the crystalline coating applied on the ferrous metals to inhibit corrosion. The phosphate coating lends a gray to black appearance of the surface. In many applications phosphate coating is followed by oil coating (P & O) to improve its rusting and anti-galling properties.
What does phosphate coating do?
The process of Phosphate coating is employed for the purpose of pretreatment prior to coating or painting, increasing corrosion protection and improving friction properties of sliding components.
Is phosphate coating rust proof?
Phosphate coatings are often used to protect steel parts against rusting and other types of corrosion. However, they are somewhat porous, so this use requires impregnating the coating with oil, paint, or some other sealing substance.
Can you paint over phosphate coating?
Ideally, you would paint the parts right after applying the phosphate coating. If the parts are not going to be painted, then you can apply some kind of rust inhibitor that can act as a barrier to corrosion.
Is phosphate a good finish?
The phosphate provides a long lasting resistance to corrosion. It is very common because it is inexpensive, durable and easy to apply. A phosphated surface generally has some texture to it which can allow it to "hold oil" better than other finishes.
Why is phosphate banned?
While phosphates are low toxicity, they instead cause nutrient pollution and feed the algae. This leads to eutrophication and harmful algal bloom. Many countries have banned the use of phosphates in detergent, including the European Union and the United States.
What is the most durable metal coating?
The galvanizing process has multiple advantages that make it a popular choice for numerous applications. For example, the zinc oxide coating is highly stable and adheres tightly to the metal substrate; it is very durable and does not flake off easily. Galvanizing is also renowned for its galvanic protection.
Can phosphate coating be removed?
Industrial laser cleaning can remove all types of phosphate coatings, including iron phosphate coatings, manganese phosphate coatings, and zinc phosphate coatings.
What is the best coating to prevent rust?
Galvanize. Galvanizing applies a protective coating of zinc over iron or steel. Since zinc corrodes about 30 times slower than iron, galvanizing can be a cheap and effective way to prevent rust.
How is phosphate coating applied?
A phosphate coating is applied by spraying or an immersion. The dipped bath in a heated solution is preffered and best. The crystalline phosphates are coated on the surface item, forming a barrier of protection.
What is the difference between nitrate and phosphate finish?
A nitride exterior will protect the barrel longer than a phosphate exterior finish. However, a chrome-lined, or phosphate, barrel will hold up better to sustained fire than a nitride interior. Nitride has a slight edge in accuracy and price. However, phosphate coated/chrome lined barrels are more common.
Is phosphate coating same as galvanized?
Phosphatizing is usually a pretreatment for paint or powder coating, whereas galvanizing is a heavy coating of hot-dipped zinc. A galvanized surface is far more corrosion resistant than an unpainted phosphatized surface, but can be difficult to paint.
How does phosphate prevent corrosion?
The phosphate process achieves a chemical alteration of the surface of a part, with the intent of creating corrosion resistance. The phosphate process for metal actually creates a new substance through a chemical reaction.
What is phosphate and why is it important?
Phosphate is necessary for the formation of bone and teeth. Phosphate is also used as a building block for several important substances, including those used by the cell for energy, cell membranes, and DNA (deoxyribonucleic acid). The body obtains phosphate from foods and excretes it in urine and sometimes stool.
Why do drywall screws have a phosphate coating?
Black drywall screws have a phosphate coating that is supposed to keep the wet drywall compound from causing the screw head to rust.
Why are screws coated with phosphate?
Phosphate Coated A phosphate coating on a fastener serves to provide lubrication when inserting the fastener by reducing friction. It also improves corrosion resistance, but should only be used indoors.
How to set up the Zinc Phosphate Process?
October 1, 2008. A. It is my feeling that it is difficult to overload a phosphate tank. BUT! If you have a huge weight of parts, the tank temp will drop and you will not get a good phosphate, so you will need a larger tank OR huge heaters OR add parts a few at a time and remove the ones that are done and immediately add more IE, you sequence the parts rather than an entire load at one time.
Phosphate and oil
Where the world gathers for plating, anodizing, & finishing Q&As since 1989 Phosphate and oil (-----) 2006Can you please explain me in detail the process of 'Phosphate and oil'.
Zinc Phosphate: Questions and Answers | Products Finishing
The Products Finishing clinics are one of the most popular features of the magazine. Occasionally, a reader may miss a question and answer in one column that may have benefited him/her. Because of this, Products Finishing has developed an article with readers’ questions and answers to zinc phosphating problems. Zinc Phosphate Sludge
Is phosphate paint better for concours?
Paint is easier to chip. The phosphate coating is more durable and resistant to corrosion, plus it's correct for concours restorations. Today, the Mustang Club of America is coming to terms with natural finishes. In the Concours Trailered classes, their plan is to "come up with requirements for owners to prepare their cars during ...
Do phosphate and oil last?
More than being concours correct, phosphate and oil finishes last indefinitely. A painted part, like a hood hinge, will eventually need to be removed and painted again due to metal-to-metal contact. Plus, the cost of phosphate and oil is, in Bob's words, "less than buying two rattle cans."
What is phosphate coating?
A Beginner’s Guide to Phosphate Coating. Phosphate coating is the crystalline coating applied on the ferrous metals to inhibit corrosion. The phosphate coating lends a gray to black appearance of the surface. In many applications phosphate coating is followed by oil coating (P & O) to improve its rusting and anti-galling properties.
What is manganese phosphate coating?
The manganese phosphate coatings are available in black and dark gray color. They are used as corrosion protection agents, anti-galling agents, and as a lubricant. These coatings have the highest hardness and superior corrosion resistances among all general phosphate coatings. The treatment time often varies from five to fifteen minutes. Some of its features and applications are:
What color is zinc phosphate?
These coatings are usually applied by spraying or immersion. The zinc phosphate coatings are available in black and dark gray colors, and lighter in comparison to manganese phosphate coatings.
What coatings are used on threaded parts?
Some of the threaded parts are treated with phosphate coatings, which improves their anti-galling and rust inhibiting characteristics.
Where is Microsurface Corporation located?
Microsurface Corporation in San Jose, California is one of the leading and well-known applicators of engineered lubricants, coatings, and manufacturer of Timesaver Lapping Compounds. Phosphate Coating Zinc Phosphate Coating.
What About Chrome Lining?
Chrome lining is an excellent option, especially when paired with a phosphate finish. The process of applying a chrome lining is to place the barrel’s breech into a chemical bath. Next, a moveable anode is placed in the bore of the gun. As the current passes through the chemical bath solution, the chromium from the bath is deposited on the inside of the bore.
Why do you need chrome lining on a gun?
Many gun users prefer using a chrome lining to improve the accuracy of the gun and make the barrel easier to clean. However, there is much debate over chrome-lined vs. nitride. Many users feel that with a nitride finish, you do not need the additional chrome lining. This is because the inside of the gun is also treated during the parkerizing process.
Why do you need to clean a phosphate gun?
The more textured phosphate finish requires more cleaning because it is more porous, and dirt can get stuck more quickly than with a smooth nitride finish. Therefore a phosphate gun will need more regular and thorough cleaning.
What temperature is a salt bath?
The temperatures of these salt baths range from 1000℉ (usually Tennifer method) to 1600℉ (usually Melonite method). The higher temperatures of the salt baths lead to thicker nitride layers.
What is a nitride finish?
A nitride finish is a choice for you if you enjoy a gun with a smooth finish, and if you do not enjoy toiling with cleaning your weapon regularly. A nitride finish is meant to last, so if you want a gun with a finish that will last for many years to come, then the nitride finish is a good option for you.
What is the benefit of nitride finish on a gun?
Another great advantage is the nitride finish’s high resistance to erosion. This finish is designed to keep your gun lasting for many years.
How long does it take to complete a Parkerization?
Once completely submerged in the solution, streams of bubbles will start rising from the metal parts. Once the stream of bubbles has stopped streaming, you will know the process has been completed. This usually takes about 30 minutes.
What is hard anodize?
Hard Anodize (Hard Coat) Type III Hard anodize, commonly referred to as hard coating is an electrochemical process that is performed by submerging an aluminum item in a chilled sulfuric acid bath that results in a hardness of 330 to 450 vickers.
What is bluing in firearms?
Black Oxide (Bluing) Black oxide finishing, also commonly referred to as bluing, is a traditional way to finish steel that protects firearms from corrosion while reducing glare, if properly pre-finished.
What is the color of anodized aluminum?
Other benefits of hard anodize in addition to hardness include abrasion and corrosion resistance. The natural color will vary from tan to dark gray depending on the alloy of aluminum. Most firearms products are coated to a thickness of .001 +/- .0002 and dyed to a black color then sealed in either hot water or a nickel acetate solution in accordance with Mil-A-8625 Type III.
What is the best finish for a gun barrel?
As one of the least expensive corrosion-resistant finishes on the market, black oxide is often the preferred finish used on gun barrels and small components. Gun oil is important to this type of finish to avoid rusting. Methods used are either a hot or cold process.
Why is it important to finish a firearm?
May 16, 2019. Good finishing is imperative to keep firearms functioning properly and in pristine condition, protected from the elements, corrosion, and wear-and-tear from regular use. Given the firearm industry’s stringent requirements, consistent high-quality firearm finishing is crucial to a successful project.
Does hard anodize thicken oxide?
However, unlike black oxide, hard anodize results in a dimensional increase of the parts treated. The hard anodize process thickens the oxide layer by 50% on the surface of the base metal and penetrates the base metal by 50%, therefore tolerances need to be adjusted accordingly.
Is manganese phosphate good for guns?
Other benefits of manganese phosphate include its superior corrosion protection in comparison to black oxide, as well as it’s anti-galling and self-lubrication properties which provide continuous protection on gun parts subject to wear.
What is Jackson tumble finish?
Jackson Tumble Finish offers a zinc phosphate and stearate lubricant process for the purposes of severe drawing and/or heading operations. This process is very successful in enhancing the longevity of tooling and draw life applications. Other lube options are available upon request.
What is calcium modified fine zinc phosphate used for?
Calcium modified fine zinc phosphate is often used as an under adhesive in paint, rubber overmold, and organic coatings. The highly-absorbent phosphate crystals allow the subsequent coating to penetrate into tiny valleys and increase the total surface area available for bonding.
What is phosphate coating?
P hosphate is a chemical conversion process that creates an insoluble lattice of crystalline phosphate on a metal surface. Once applied, the phosphate coats uniformly, is non-conductive and resists corrosion.
What is dry to touch lubricant?
Dry to touch lubricants can be added, creating less mess and satisfying a greater range of handling requirements. The ability to uniformly coat irregular product surfaces. A crystalline coating capable of retaining many different rust prevention methods.
Does zinc phosphate extend shelf life?
Zinc phosphating can extend the shelf life of your products in corrosive environments. By combining our zinc phosphate treatment with rust-inhibiting oils, wax, and other organic coatings, we can help your product withstand harsh conditions, such as up to 168 hours of continuous salt spray. Jackson Tumble Finish has the ability to coat heavy, ...
Does manganese phosphate coating work?
By aiding initial metal-to-metal contact, our manganese phosphate coating permits the rapid break-in of moving parts without abrading or galling. Plus, the oil held by the crystals improve lubricity of the treated surface and imparts corrosion resistance. Even after the break-in period is complete, a smooth and fine distribution of oil remains, assuring continued lubrication.
