
Plant layout Production Management
- Plant Layout
- Definition Plant layout refers to the arrangement of physical facilities such as machinery, equipment, furniture etc. ...
- Importance Minimizing material, Time and cost. ...
- Type’s Plant layout may be of four types: (a) Product or line layout (b) Process or functional layout (c) Fixed position or location layout (d) Combined or group layout
What is plant layout in operation management?
Plant Layout in Operation Management. Plant layout refers to the physical arrangement of production facilities. It is the configuration of departments, work centers and equipment in the conversion process. It is a floor plan of the physical facilities, which are used in production.
What are the advantages of plant layout?
Advantages. Plant layout is the most effective physical arrangement, either existing or in plans of industrial facilities i.e arrangement of machines, processing equipment and service departments to achieve greatest co-ordination and efficiency of 4M’s (Men, Materials, Machines and Methods) in a plant.
What is a plant layout study?
A plant layout study is an engineering study used to analyze different physical configurations for a manufacturing plant. Plant layout embraces the physical arrangement of industrial facilities.
What is meant by product layout and process layout?
In the product layout and process layout generally the machines have fixed installations and the operators are static in terms of their specified work stations. It is only the materials which move form operation to operation for the purpose of processing.
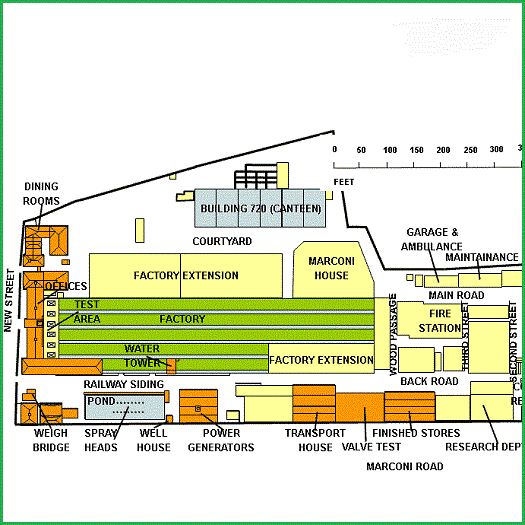
What is plant layout and types?
Plant layout is a plan for effective utilisation of facilities for the manufacture of products; involving a most efficient and economical arrangement of machines, materials, personnel, storage space and all supporting services, within available floor space.
What is product plant layout?
In manufacturing engineering, a product layout refers to a production system where the work stations and equipment are located along the line of production, as with assembly lines.
What is plant layout in simple words?
Plant layout means the disposition of the various facilities (equipment's, material, manpower etc.) within the areas of the site selected. Plant layout begins with the design of the factory building and goes up to the location and movement of work.
What is plant layout with example?
Plant Layout : Definition 2 According to Moore, “Plant layout is a plan of an optimum arrangement of facilities including personnel, operating equipment, storage space, material handling equipment and all other supporting services along with the design of best structure to contain all these facilities”.
What is importance of plant layout?
Plant layout is the most effective physical arrangement, either existing or in plans of industrial facilities i.e arrangement of machines, processing equipment and service departments to achieve greatest co-ordination and efficiency of 4M's (Men, Materials, Machines and Methods) in a plant.
What are the advantages of plant layout?
(i) Facilitates receipts, shipments and delivery of inputs and finished goods. (ii) Provides adequate and convenient storage facilities. (iii) Permits the maximum possible output with same input. (iv) Paces production & determines production flow.
What is principle of plant layout?
Plant Layout and its principles. A plant layout is the placing of the right items coupled with the right place and the right method, to permit the flow of production process through the shortest possible distance in the shortest possible time.
What is plant layout Wikipedia?
A plant layout study is an engineering study used to analyze different physical configurations for a manufacturing plant. It is also known as Facilities Planning and Layout.
What are the characteristics of plant layout?
Expert-verified answer questionCharacteristics: The characteristics of a plant layout are;(i) Flow of production is smooth.(ii) The available space is utilized to the maximum capacity.(iii) Movement of labour and machinery is easy.(iv) It has minimum handling.(v) Smaller enterprise.(vi) Better working conditions.More items...•
What are the three types of plant layout?
There are three main types of plant layout: 1) Functional or process layout, 2) product or line layout, and 3) stationary layout. Other types; 4) Combination and 5) Fixed Position Layout. However, the choice of one or the other type of layout depends upon the machines and techniques used in the production.
What are the 7 types of layout?
Types of LayoutProcess Layout. Merits of Process Layout. Low Investment in Equipment and Machines. ... Product Layout. Merits of Product Layout. Smooth Production Flow. ... Fixed Position Layout. Merits of Fixed Position Layout. ... Group Technology or Cellular Layout. Merits of Group Technology or Cellular Layout. ... Hybrid layout.
What is plant layout?
Plant layout refers to the physical arrangement of production facilities. It is the configuration of departments, work centers and equipment in the conversion process. It is a floor plan of the physical facilities, which are used in production.
What is the primary goal of plant layout?
The primary goal of the plant layout is to maximize the profit by arrangement of all the plant facilities to the best advantage of total manufacturing of the product. The objectives of plant layout are: Streamline the flow of materials through the plant. Facilitate the manufacturing process.
What is the principle of cubic space utilization?
Principle of cubic space utilization: The good layout is one that utilizes both horizontal and vertical space. It is not only enough if only the floor space is utilized optimally but the third dimension, i.e., the height is also to be utilized effectively.
What is plant layout?
Plant layout is a subset of process plant design, which itself fits into the wider background of an overall project life cycle. The details of project life cycles vary between industries, but there is a common core. Take, e.g., the life cycle for a pharmaceutical project:
What is process plant layout?
The process plant layout problem involves decisions concerning the spatial allocation of equipment items and the required connections among them (Mecklenburgh, 1985 ). Increased competition has led contractors and chemical companies to consider these decisions during the design or retrofit of chemical plants. In general, the process plant layout problem may be characterised by a number of cost drivers such as connection, land area, construction costs, as well as management/engineering issues (for example production organisation). So far, safety aspects are considered in a rather simplified way by introducing constraints with respect to the minimum allowable distance between specific equipment items. However, it is evident that there is a need for considering safety aspects in more detail within process plant layout and design frameworks.
How does plant layout affect the operation of a company?
Plant layout can affect the total operation of a company, including the production processes, equipment, storage, dispatch and administration. It has a direct effect upon production efficiency and economics of the operation, the morale of employees and can affect the physical health of operatives.
How does plant layout affect plant economics?
Security. Plant layout can have a large impact on plant economics. Additional space tends to increase safety, but is expensive in terms of land, additional piping, and operating costs. Space needs to be provided where it is necessary for safety but not wasted.
Why is plant layout important?
Plant layout is a crucial factor in the economics and safety of process plants. Some of the ways in which plant layout contributes to safety and loss prevention (SLP) are:
What is poor layout in plant design?
The typical plant exhibits a poor layout, in which the movement of work in process interferes with operations at individual workstations, where an accumulation of partly finished pieces is held until workers return to them.
What is plant layout?
Plant layout is a plan of optimum management of facilities which include; personnel, operating equipment, storage space, material handling equipment, and all other support services. It includes the arrangement and location of work centres and various service centres like inspection, storage, and shipping within the manufacturing/factory building.
What should be considered when deciding on the type of layout?
Climate: Temperature, illumination, ventilation should be considered while deciding on the type of layout. These factors should be considered in order to improve the health and welfare of employees. 6. Service facilities:The layout should provide for the comforts and welfare of the employees.
What type of layout is preferred if machines are heavy and emit more noise?
Type of machines:Stationary layout is preferable if machines are heavy and emit more noise. Such heavy machinery can be fitted on the floor. Adequate space should be provided for the location of machines and also there should be sufficient space between them to avoid accidents. 5.
What is plant layout?
Plant layout is a plan for effective utilisation of facilities for the manufacture of products; involving a most efficient and economical arrangement of machines, materials, personnel, storage space and all supporting services, within available floor space.
Why is plant layout so complex?
ADVERTISEMENTS: (i) Plant layout is very complex in nature; because it involves concepts relating to such fields as engineering, architecture, economics and business management. (ii) Most of managers now realize that after the site for plant location is selected; it is better to develop the layout and build the building around it – rather ...
What is stationary layout?
It is also called stationary layout. In this type of layout men, materials and machines are brought to a product that remains in one place owing to its size. Ship-building, air-craft manufacturing, wagon building, heavy construction of dams, bridges, buildings etc. are typical examples of such layout.
What are the two basic plans of the arrangement of manufacturing facilities?
Two basic plans of the arrangement of manufacturing facilities are – product layout and process layout. The only other alternative is a combination of product and process layouts, in the same plant.
Why is line layout called line layout?
It is called line layout because machines are arrange in a straight line. The raw materials are fed at one end and taken out as finished product to the other end. ADVERTISEMENTS: Special purpose machines are used which perform the required jobs (i.e. functions) quickly and reliably.
What is plant layout?
Plant layout is the most effective physical arrangement, either existing or in plans of industrial facilities i. e arrangement of machines, processing equipment and service departments to achieve greatest co-ordination and efficiency of 4M’s (Men, Materials, Machines and Methods) in a plant.
What is the name of the layout of a product?
1. Product or Line Layout: If all the processing equipment and machines are arranged according to the sequence of operations of a product, the layout is called product type of layout. In this type of layout, only one product or one type of products is produced in an operating area.
Why is process layout important?
The process layout is particularly useful where low volume of production is needed. If the products are not standardized, the process layout is more desirable, because it has greater process flexibility than other. In this type of layout the machines are not arranged according to the sequence of operations but are arranged according to the nature or type of the operations.
Why is flexibility important in design?
Flexibility is a very important factor, so layout should be such which can be moulded according to the requirements of industry, without much investment. If the good features of all types of layouts are connected, a compromise solution can be obtained which will be more economical and flexible.
What is plant layout?
Plant layout means the arrangement of equipment, material, etc facilities and services of the plant within the selected work area to achieve productivity as high as possible. Plant layout starts with building design and goes up to the movement of work table and material handling system. Production in details. Productivity in details.
Why assign one or more skilled workers from the start of a project to finish?
It is possible to assign one or more skilled workers from the start of a project to finish in order to ensure continuity of work. Involves the least movement of materials, manufacturing of large size product is possible. A number of quite different projects can be taken with the same layout.
What is the purpose of plant layout?
A properly planned plant layout aims at achieving the following objectives: 1. To achieve economies in handling of raw materials, work in- progress and finished goods. 2. To reduce the quantum of work-in-progress. 3. To have most effective and optimum utilisation of available floor space. 4.
Why is a new layout necessary?
A new layout may be necessary because of technological changes in the products as well as simple change in processes, machines, methods and materials”. A new layout also becomes necessary when the existing layout becomes ineffective and poor or is not conducive to the changed circumstances.
Is plant layout static or dynamic?
The concept of plant layout is not static but dynamic one. It is on account of continuous manufacturing and technological improvements taking place necessitating quick and immediate changes in production processes and designs.
What is the importance of plant layout?
Having an effective plant layout is one of the keys to success in factory management. It will not only have a direct effect on the efficiency of your operations but also affect the total operation of your company, including the production processes, inventory, dispatch, and administration.
Why is lean plant layout important?
Lean plant layouts use visual controls for better communication and set visual standards. Adhesive floor markings are used instead of ...
Why did Japanese factories use lean plant layouts?
Factories have to organise everything efficiently on tiny space as the land is precious there , which drove Japanese factories towards Lean plant layouts. Lean plant layouts usually have very little room between machines thus preventing inventory from building up, as well as reducing motion and transportation.
Why is it important to design a lean layout?
After the new layout is implemented, there could be a variety of changes: expansion due to demand increase, new product launches, changes in methods or equipment, or safety and environmental requirements. It’s therefore essential to design the layout in such a way that it’s flexible enough to adapt to changes. That’s why small and easy-to-move equipment is preferable in Lean Layout Development. Saving space for future expansion or new products is also worthwhile, rather than giving up space to excessive inventory.
What is a lean plant?
One of the critical factors of a Lean facility is that value streams connect to customer’s demand and provide quick response to customer demand. The entire value stream is either continuous flow to customers or pulled by real consumption from customers. Operators in every process understand the requirement from customers and also know what they do affects the customer’s decision.
Should a lean layout be developed by just one group of stakeholders?
A Lean layout should not be developed by just one group of stakeholders, it needs to be a collaborative effort from a range of stakeholders in the business after a future state map has been created.
Is it better to have a lean plant layout or not?
It might be painful while you are developing a Lean plant layout, but you will get rewarded by getting less pain afterward. Compared to traditional plant layout, a well-designed Lean plant layout can bring a variety of benefits: It will minimise the material handling distance and time; It will save floor space;
