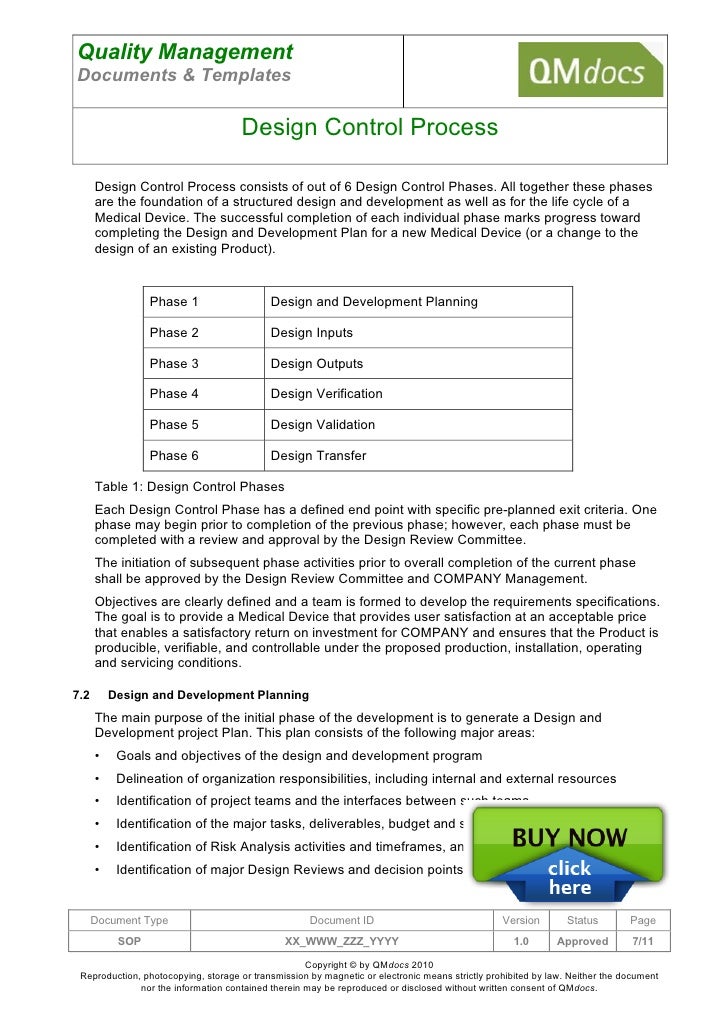
Quality Glossary Definition: Process capability Process capability is defined as a statistical measure of the inherent process variability of a given characteristic. You can use a process-capability study to assess the ability of a process to meet specifications.
What is capability of a process?
Capability is the ability of the process to produce output that meets specifications. A process is said to be capable if nearly 100% of the output from the process is within the specifications. A process can be in control, yet fail to meet specification requirements.
What is the difference between capability and control?
Capability vs. control A process is said to be in control or stable, if it is in statistical control. A process is in statistical control when all special causes of variation have been removed and only common cause variation remains. Control charts are used to determine whether a process is in statistical control or not.
What is process capability index in SAP?
Process Capability Index (Cpk) Process capability index (Cpk) is a statistical tool, to measure the ability of a process to produce output within customer’s specification limits. In simple words, it measures producer’s capability to produce a product within customer’s tolerance range.
What is a process capability CPK?
Cpk is a measure of the process performance capability. Cpk indicates the shifting of the process from the target value or mean value. How to Calculate Process Capability ? Example and Interpretation

What is process capability with example?
Process Capability Example 1: The ice cream that must be served in an ice cream parlor has to be between -15 degrees Celsius and -35 degrees Celsius. The process of refrigeration that keeps the temperature has a standard deviation (SD) of 2 degrees Celsius. And the mean value of this temperature is -25 degrees Celsius.
What is CP Cpk process capability?
Cp and Cpk, commonly referred to as process capability indices, are used to define the ability of a process to produce a product that meets requirements.
Why we do process capability?
[Potential] Process Capability Analysis (Cp, Cpk): A process capability study uses data from a sample to PREDICT the ability of a manufacturing process to produce parts conforming to specifications. This prediction enables us to "qualify" a new manufacturing process as being fit for use in production.
What are the components of process capability?
Two parts of process capability are: 1) measure the variability of the output of a process, and 2) compare that variability with a proposed specification or product tolerance.
What does a 1.33 Cpk mean?
is capableCpk = or >1.33 indicates that the process is capable and meets specification limits. Any value less than this may mean variation is too wide compared to the specification or the process average is away from the target.
What does Cpk of 1.67 mean?
The Capability Index, Cpk. The outcome of a Process Capability study is a single metric, which provides an indication of the ability of a process to consistently provide output which is within required specifications. CPK <1.00 (Poor, incapable) 1.00< CPK <1.67 (Fair) CPK >1.67 (Excellent, Capable)
What is process capability in simple words?
Process capability is defined as a statistical measure of the inherent process variability of a given characteristic. You can use a process-capability study to assess the ability of a process to meet specifications.
What is CP and Cpk in quality?
The Cp and Cpk indices are the primary capability indices. Cp shows whether the distribution can potentially fit inside the specification, while Cpk shows whether the overall average is centrally located. If the overall average is in the center of the specification, the Cp and Cpk values will be the same.
What is Cpk quality?
Definition: Cpk = Cpk = Process Capability Index. Adjustment of Cp for the effect of non-centered distribution. Cpk measures how close you are to your target and how consistent you are to around your average performance.
How process capability is measured?
Measures of Process Capability (Indices) K= (Process Centre-Process Mean)/50%of USL-LSL and if we talk about process center; Process center = (USL+LSL)/2, and the process mean is the average or mean of the process data points.
What are the two common measures of process capability?
Two commonly used measures of process capability are Cp, when the process is centered on the nominal value, and Cpk when the process is not centered on the nominal value.
How can process capability be improved?
How to Improve Process CapabilityExamine the process flowchart. Look for areas of duplicate work, extended cycle times or rework. ... Examine the control charts for outliers and variability. ... Prioritize improvements and create new control charts to examine the effects of the changes.
What does CP and Cpk mean?
Process Capability (Cp) and Performance (Cpk) Learn how to determine whether your process is meeting its full potential—and see opportunities for improvement.
What is CP and Cpk with example?
The Cp and Cpk indices are the primary capability indices. Cp shows whether the distribution can potentially fit inside the specification, while Cpk shows whether the overall average is centrally located. If the overall average is in the center of the specification, the Cp and Cpk values will be the same.
What does CP value mean?
Cp is an index used to assess the width of the process spread in comparison to the width of the specification. It is calculated by dividing the allowable spread by the actual spread. The allowable spread is the difference between the upper and lower specification limits.
What if CP is higher than Cpk?
When Cp is greater than Cpk, the mean is nearer to one specification limit or the other. Once you understand your process, you can make a good decision about how to prioritize your process improvement efforts.
What is process capability?
Process capability is defined as a statistical measure of the inherent process variability of a given characteristic. You can use a process-capability study to assess the ability of a process to meet specifications.
How many samples are needed to determine process capability?
Assessing process capability is not easy. Some textbooks teach users to wait until the process reaches equilibrium, take roughly 30 samples and calculate their standard deviation; however, it is difficult to know when the process reaches a state of equilibrium and if the recommended samples are representative of the process.
Why do you include several production runs with perhaps fewer sampling times per production run?
Estimates of the process capability made this way would be representative and independent of process mean changes that might take place from one sampling time to the next. Because the pooled, within-group standard deviation is calculated on observations taken close together in time, there is no opportunity for it to be contaminated by assignable sources of variation. It is as close to pure capability as you’re likely to get.
How do capacity estimates work?
Capability estimates like these essentially reflect the nonconformance rate of a process by expressing this performance in the form of a single number. Typically this involves calculating some ratio of the specification limits to process spread.
What is CPK in manufacturing?
Potential capability (Cp) and actual capability during production (Cpk) are process capability estimates. C p and C pk show how capable a process is of meeting its specification limits, used with continuous data. They are valuable tools for evaluating initial and ongoing capability of parts and processes.
What is the modern approach to quality progress?
Modern Approach ( Quality Progress) Traditional process capability analysis no longer is the best way to model performance in today’s digital age, where dynamic environments and remote process monitoring require more rapid data analysis cycles to support automation. The authors propose a new method that applies process capability and stability concurrently, which allows samples to be refreshed more frequently, thereby capturing the dynamic shifts in processes.
When is a capability estimate obtained?
During a quality improvement initiative, such as Six Sigma, a capability estimate is typically obtained at the start and end of the study to reflect the level of improvement that occurred.
What is process capability?
Process capability (Cp) is defined as (USL - LSL)/6s , the ratio between the tolerance (upper specification limit to lower specification limit) and the ±3s process spread. A second commonly used index, Cpk, incorporates a measure of how well the process is centered around the target value in addition to a measure of process variation. Therefore, Cpk provides an indicator of process bias as well as variation. This index is the one most commonly used in current manufacturing practice. By providing indicators of both method bias and variation, Cpk is a powerful statistical tool for measuring analytical performance.
Why is process capability important?
Process capability can be a powerful tool for managing laboratory operations and making improvements to meet increasing demands for accurate and precise results. In addition to providing a generally accepted metric of laboratory performance, process capability analysis will reinforce process management models in the laboratory.
Why do we need specification limits for process capability?
The calculation of process capability requires specification limits so that observed performance can be compared to expected performance. Typically analytical methods do not have specification limits in the classic industrial sense. An available alternative for analytical methods is the observed method variation from AOAC and ASTM collaborative studies. Since these values represent the variation found among a pool of laboratories, they could be used as method "specifications" for process capability calculations. Likewise, values derived from round robins or regional pools could be used where appropriate, recognizing that they are not as rigorous a procedure. Such values serve as a useful first approximation as we begin to study and define this approach to lab proficiency.
Why do laboratories use SQC?
Laboratories also have adopted some SQC techniques, mostly in response to external reporting requirements.
What is control chart in QA?
These charts tell us whether the analytical method is stable and whether accuracy is being maintained. (QA procedures dictate that in out-of-control conditions we reject any data coming from the analytical method until we re-establish a state of statistical control.)
How to illustrate laboratory process capability?
To illustrate laboratory process capability, consider the analysis of a standard material with a nominal value of 10. The analyses in the pool yield an expected variation of ± 0.9. The first step determines process stability using a control chart. Next, plotting our laboratory's analyses produces the following histogram:
Can control charts tell you if a method is accurate?
With the method's stability assured, we can now move toward capability. However, control charts do not tell us if the method's precision is acceptable. Most proficiency testing relies on examining results from analyses of known materials. Proficiency testing programs usually do not focus on the underlying analytical process nor do they provide laboratory managers with the tools to maintain and monitor analytical method capability.
What is process capability study?
Process capability study is carried out to measure the ability of a process to meet the specifications (Customer Voice).
What is stable process?
If product characteristics/specifications conform to engineering/customer requirements, then the process is considered as stable/capable and performing well as per set standards. A process is considered stable if there are only Common Causes of Variation present in the process.
What is process in engineering?
Process. The process is a set of interrelated activities that convert the inputs such as equipment, materials, people, methods, and environment into desirable output. The quality of the process is measured by the output of product quality characteristics.
What does Cp mean in a process?
Cp indicates the spread of variation present in a process.
What is a CPK?
Cpk is a measure of the process performance capability. Cpk indicates the shifting of the process from the target value or mean value.
What is a CPK in a process?
Cpk measures how close a process is performing compared to its specification limits and accounting for the natural variability of the process. Larger is better. The larger Cpk is, the less likely it is that any item will be outside the specification limits.
What is CPK in Six Sigma?
In Six Sigma we want to describe processes quality in terms of sigma because this gives us an easy way to talk about how capable different processes are using a common mathematical framework. In other words, it allows us to compare apple processes to orange processes!
What is the Difference Between Cp and Cpk?
Cp and Cpk measure how consistent you are to around your average performance.
What is Cpk?
Think of the walls of your garage – where you have to fit your car in – they become the customer specification limits. If you go past those limits, you will crash, and the customer will not be happy!
Why do CPK and PPK converge?
The values for Cpk and Ppk will converge to almost the same value because sigma and the sample standard deviation will be identical ( use an F test to determine ).
What does CPK mean in a garage?
Cpk tells you the relationship between the size of the car, the size of the garage and how far away from the middle of the garage you parked the car.”.
What is the CPK of a 3-2/3s function?
Now you end up with a Cpk of (3-2)/3s = 1/3s , but your Cp is still the same 1s as before. It is important to note that because Cpk uses the minimum function, it will always be equal to or smaller than the Cp for the same set of data.
What is process capability index?
Process capability index (Cpk) is a statistical tool, to measure the ability of a process to produce output within customer’s specification limits. In simple words, it measures producer’s capability to produce a product within customer’s tolerance range. Cpk is used to estimate how close you are to a given target and how consistent you are to around your average performance. Cpk gives you the best-case scenario for the existing process. It can also estimate future process performance, assuming performance is consistent over time.
What is a CPK in a process?
Cpk is a standard index to state the capability of one process, the higher the Cpk value the better the process is. For instance, Machine 1 has a Cpk of 1.7 and machine 2 has a Cpk of 1.1.
What is a process where almost all measurements fall inside the specification limits?
A process where almost all the measurements fall inside the specification limits is a capable process. This can be represented pictorially by the plot below:
What does CPK mean in a machine?
From the Cpk value, one can derive that Machine 1 is better than 2. Since Cpk uses specification limits and parts variation (sigma), we can also arrive at the yield processed and losses from the machine. Cpk = or >1.33 indicates that the process is capable and meets specification limits.
When is a process in control?
A process is in statistical control when all special causes of variation have been removed and only common cause variation remains.
What is the ability of a process to produce output that meets specifications?
Capability is the ability of the process to produce output that meets specifications. A process is said to be capable if nearly 100% of the output from the process is within the specifications. A process can be in control, yet fail to meet specification requirements.
What is control chart?
Control charts are used to determine whether a process is in statistical control or not. If there are no points beyond the control limits, no trends up, down, above, or below the centerline, and no patterns, the process is said to be in statistical control.
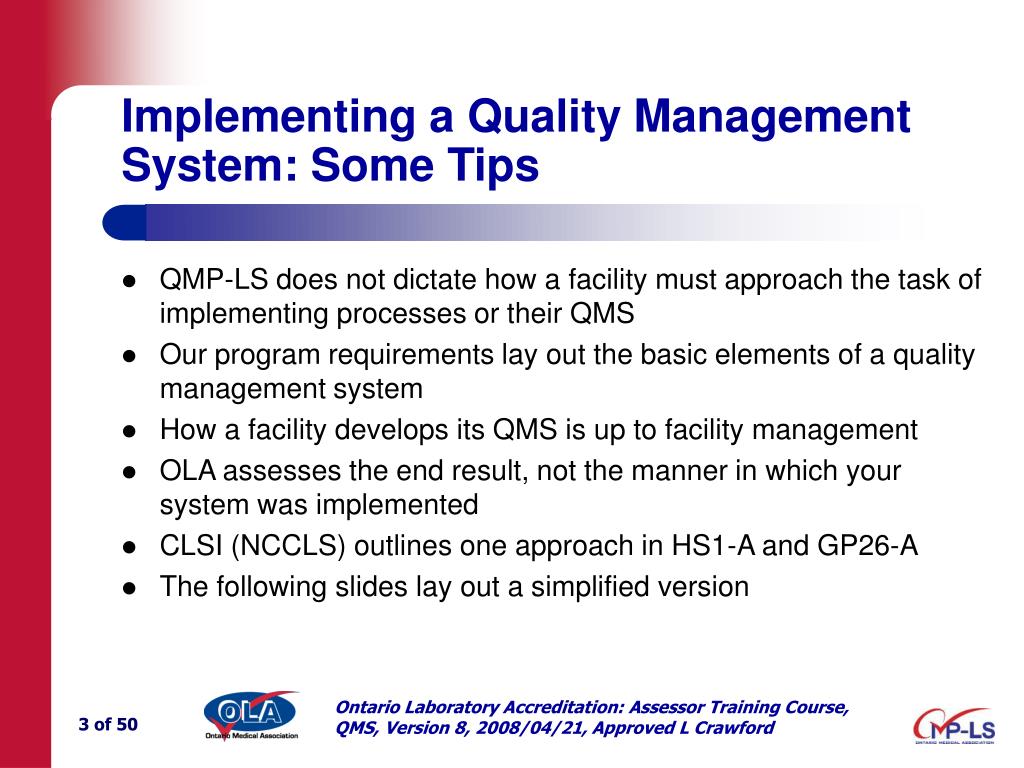