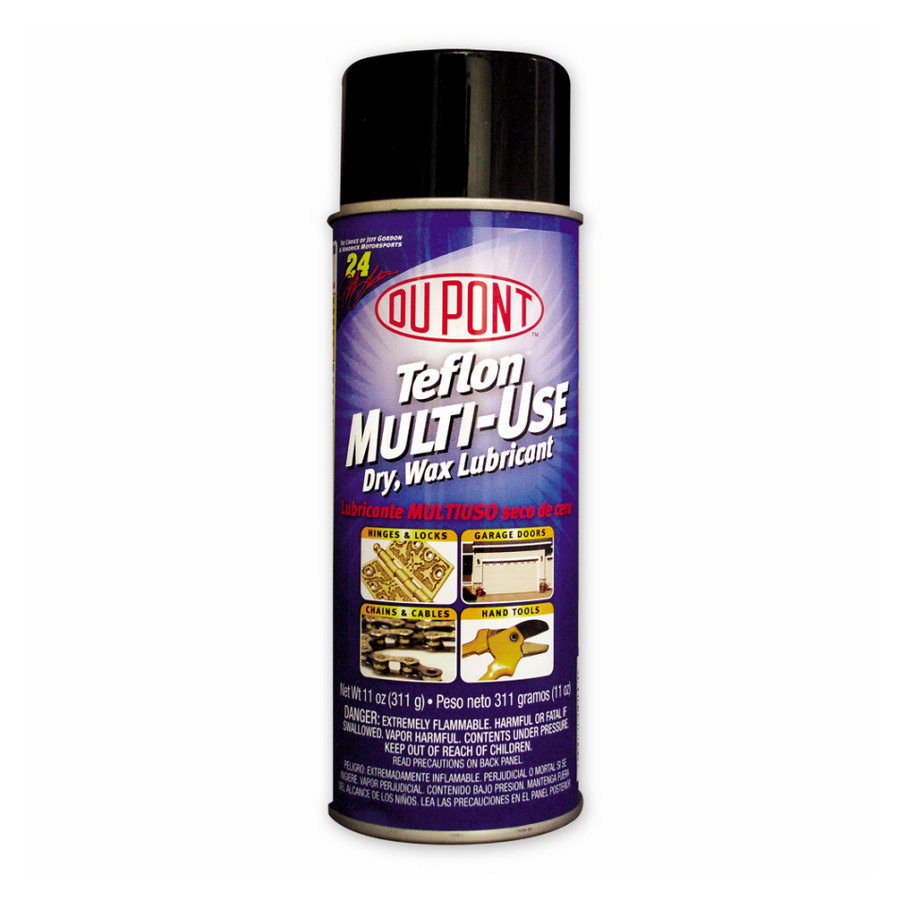
What is meant by PTFE?
The term PTFE stands for polytetrafluoroethylene, which is a polymer material containing fluorocarbon units as the repeating unit. The common name for this polymer material is Teflon. RPTFE, on the other hand, is the reinforced form of Teflon.
What are the different forms of PTFE that are used?
- Teflon PTFE. Polytetrafluoroethylene or PTFE is the most widely usedTeflon coating
- Teflon FEP. Fluorinated Ethylene Propylene Copolymer or FEP is a completely non-porous film
- Teflon PFA. Similar to FEP, PFA or Perfluoroalkoxy offers non-stick coating.
- Tetzel ETFE.
- Teflon One Coat
- Teflon Dry Lubricant
Is PTFE corrosion resistant material?
PTFE, commonly referred to by its brand name Teflon, is a chemical- and corrosion-resistant engineering thermoplastic with the lowest friction coefficient of any known solid material. PTFE is hydrophobic, meaning it won’t absorb water, and has good electrical insulating power in both hot and wet environments.
Are there any solvents to dissolve Teflon or PTFE?
The chemical resistance of PTFE is outstanding, there are no solvents which could dissolve PTFE at room temperature and the surface of PTFE at room temperature is affected only by molten alkali and fluorine in some cases. PTFE Packing or Teflon Packing is braided with high purity PTFE (Polytetrafluoroethylene, Teflon) filament. PTFE Packing can be used as a valve and pump packing material.
See more
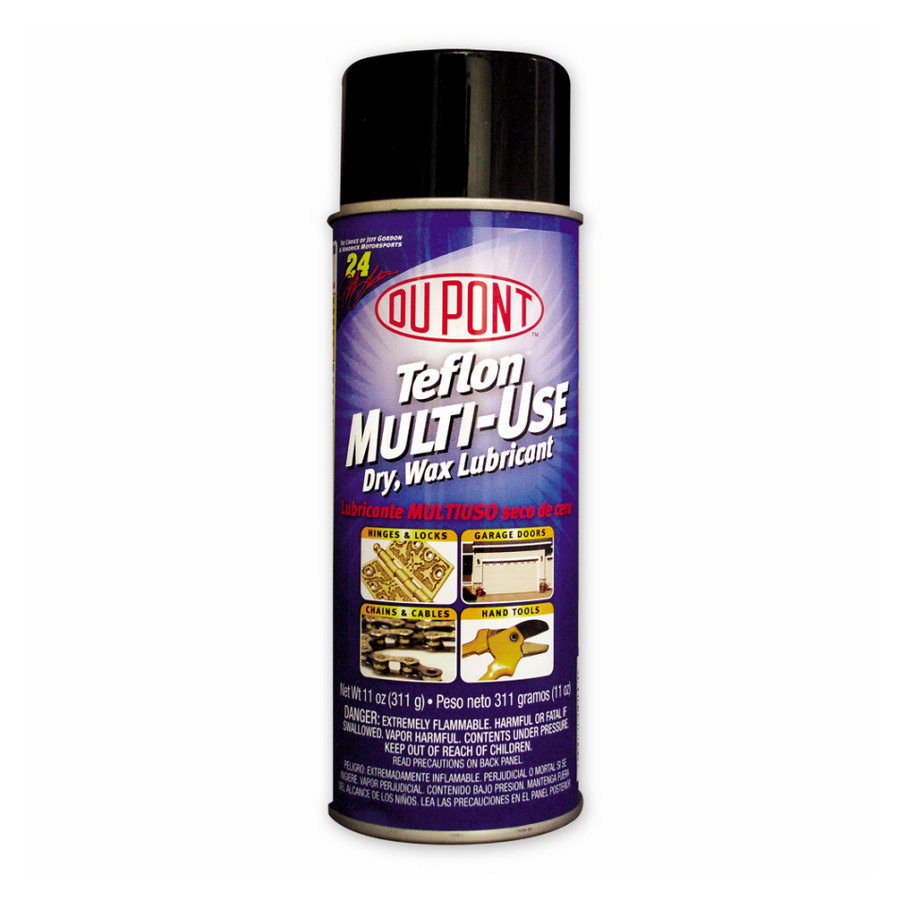
Is PTFE lubricant safe?
May cause eye, skin and respiratory irritation. Inhalation of vapors may cause irritation, dizziness and drowsiness.. Skin contact may cause drying of the skin. Indication of Immediate Medical Attention/Special Treatment Needed: Immediate medical attention is needed for ingestion.
What are PTFE lubricants?
PTFE stands for Polytetrafluoroethylene, which is a synthetic fluoropolymer. When used as a lubricant, PTFE can reduce friction, wear, and energy consumption of machinery. PTFE colloids, well known for their low friction, have at first glance, great appeal as oil additives.
What is PTFE lubricant best for?
PTFE lubricant is used for coating items such as cookware in PTFE. The process involves using a primer coat and a topcoat. PTFE lubricant is designed for application to areas that require low-friction, corrosion resistance, or dry lubrication.
Is PTFE the same as silicone lubricant?
Silicone or PTFE products are suitable for plastic-to-plastic lubrication, but the silicone will form a thicker, wetter layer that may collect dust and dirt. PTFE will have a thinner, yet harder layer that will not attract dust or absorb grime.
Is wd40 a PTFE?
WD-40 Specialist® Dry Lube. 10 oz. WD-40 Specialist® Dry Lube with PTFE is a dry lubricant that keeps your equipment running smoothly with long-lasting corrosion protection that does not attract dirt, dust, or oil. It provides superior lubrication and long-lasting corrosion protection with no oily residue.
What are the disadvantages using PTFE?
Depending on the application, the following disadvantages can rule out the selection of PTFE:Price – it is not a low-cost polymer.Production sizes – it is not easy to mass produce.It cannot be cemented.It can change shape under pressure.It is unweldable.More items...•
Does PTFE lubricant dry out?
PTFE based lubricants are food grade (U.S.D.A. rated H-1), non-toxic, biodegradable, and work in a wide range of temperatures (-65 degrees F to 500 degrees F). They are odorless and non-staining, they don't melt, wash out, or dry out, and they are safe to use on wood, metal, plastic, and rubber.
What are the advantages and disadvantages of PTFE?
PTFE Advantages and Disadvantages Virgin PTFE is white and has the advantages of a very high temperature rating, extremely high lubricity, and being inert to most caustic fluids. A disadvantage is that it's also very soft.
Is PTFE lubricant waterproof?
Applications that can be used on motors, o-rings, gaskets, bearings and water filters. Magic Lube is a PTFE based, non-melting formula that is waterproof for use in both wet and dry environments. A wide temperature range 0 - 425 F.
What is another name for PTFE?
Polytetrafluoroethylene (PTFE) is a fluoropolymer and is commonly known by its trade name, Teflon®. Unique properties of PTFE include nonreactivity, hydrophobicity, a low coefficient of friction, and good insulating properties. It is most commonly used as a nonstick coating for cookware.
Is PTFE rubber or plastic?
thermoplastic polymerIs it metal, rubber or plastic? The quick answer is neither of the three. It isn't metal, it isn't rubber, and it also isn't exactly plastic. More specifically, PTFE is a thermoplastic polymer primarily characterised by a slippery surface, high melting point, and resistance to “attack” by almost all chemicals.
How do you use PTFE lube?
2:226:02How to use a dry lubricant without attracting dirt and dust with Liqui ...YouTubeStart of suggested clipEnd of suggested clipSo in vehicle application of the proline ptfe powder spray is actually to use it on the seat belts.MoreSo in vehicle application of the proline ptfe powder spray is actually to use it on the seat belts. So a lot of times when you use it these mechanisms in here actually start to get sticky.
Is PTFE lubricant Teflon?
PTFE, better known under the brand name Teflon, is a common ingredient in bike chain lubricants due to its low friction and dirt- and water-repellent properties.
Is Lithium Grease a PTFE?
Tecflow Lithium Grease with PTFE is a unique high-performance and high-temperature lithium based grease enriched with Poly-Tetra-Fluoric-Ethylene (PTFE).
Is PTFE rubber or plastic?
thermoplastic polymerIs it metal, rubber or plastic? The quick answer is neither of the three. It isn't metal, it isn't rubber, and it also isn't exactly plastic. More specifically, PTFE is a thermoplastic polymer primarily characterised by a slippery surface, high melting point, and resistance to “attack” by almost all chemicals.
What is the brand name of PTFE?
Teflon™PolyTetraFluoroEthylene is the chemical term for the polymer (C2F4)n. Teflon™ is a registered trademark and a brand name (Teflon ®) owned by Chemours (formally DuPont) and is used on a range of products.
What is PTFE lubrication?
This is a type of film lubricant that reduces friction between two surfaces without the need for grease or oils. PTFE lubricant is used for coating items such as cookware in PTFE. The process involves using a primer coat and a topcoat. PTFE lubricant is designed for application to areas that require low-friction, corrosion resistance, or dry lubrication. RO-59 deposits a dry PTFE film lubricant and is ideal for long term sealing.
Why use PTFE lubricant?
Because dry film lubricants like PTFE offer reduced friction, they can be used in various applications. These range anywhere from cookware to automotive, and industrial industries.
What are the advantages of PTFE?
The advantages of PTFE lubricants 1 It is a highly inert substance, which means it is not generally reactive to other chemicals. This makes it a great solution for storing reactive compounds or lining materials that will come into contact with reactive agents. 2 Because dry film lubricants like PTFE offer reduced friction, they can be used in various applications. These range anywhere from cookware to automotive, and industrial industries. 3 PTFE lubricant provides high electrical resistance. This enables it to be employed for use on electrical cables and circuit boards. 4 It is extremely weatherable and provides superior water resistance. Many industries will use PTFE coating to not only improve the performance but also the durability of products and objects. 5 Using PTFE coating enables the application material to upgrade to high-temperature resistance. This type of film lubricant enables products with a lower temperature resistance to be coated with a more enduring substance. It’s high-temperature resistance also makes it non-flammable.
What is PTFE coating?
Using PTFE coating enables the application material to upgrade to high-temperature resistance. This type of film lubricant enables products with a lower temperature resistance to be coated with a more enduring substance. It’s high-temperature resistance also makes it non-flammable.
Is PTFE a fluoropolymer?
All of these contribute to making PTFE a unique Fluoropolymer like no other.
What is PTFE in chemical terms?
Chemical compound. Polytetrafluoroethylene ( PTFE) is a synthetic fluoropolymer of tetrafluoroethylene that has numerous applications. The commonly known brand name of PTFE-based compositions is Teflon ™ by Chemours, a spin-off from DuPont, which originally discovered the compound in 1938. Polytetrafluoroethylene is a fluorocarbon solid (at room ...
How is PTFE made?
Some PTFE parts are made by cold-moulding, a form of compression molding. Here, fine powdered PTFE is forced into a mould under high pressure (10–100 MPa). After a settling period, lasting from minutes to days, the mould is heated at 360 to 380 °C (680 to 716 °F), allowing the fine particles to fuse ( sinter) into a single mass.
Why is tetrafluoroethylene used in polymerization?
Because tetrafluoroethylene can explosively decompose to tetrafluoromethane and carbon, special apparatus is required for the polymerization to prevent hot spots that might initiate this dangerous side reaction . The process is typically initiated with persulfate, which homolyzes to generate sulfate radicals:
What temperature does PTFE melt?
PTFE is a thermoplastic polymer, which is a white solid at room temperature, with a density of about 2200 kg/m 3 and a melting point of 600 K (327 °C; 620 °F). It maintains high strength, toughness and self-lubrication at low temperatures down to 5 K (−268.15 °C; −450.67 °F), and good flexibility at temperatures above 194 K (−79 °C; −110 °F). PTFE gains its properties from the aggregate effect of carbon-fluorine bonds, as do all fluorocarbons. The only chemicals known to affect these carbon-fluorine bonds are highly reactive metals like the alkali metals, and at higher temperatures also such metals as aluminum and magnesium, and fluorinating agents such as xenon difluoride and cobalt (III) fluoride. At temperatures above 650–700 °C (1,200–1,290 °F) PTFE undergoes depolymerization.
When was polytetrafluoroethylene discovered?
Polytetrafluoroethylene was accidentally discovered in 1938 by Roy J. Plunkett while he was working in New Jersey for DuPont. As Plunkett attempted to make a new chlorofluorocarbon refrigerant, the tetrafluoroethylene gas in its pressure bottle stopped flowing before the bottle's weight had dropped to the point signaling "empty." Since Plunkett was measuring the amount of gas used by weighing the bottle, he became curious as to the source of the weight, and finally resorted to sawing the bottle apart. He found the bottle's interior coated with a waxy white material that was oddly slippery. Analysis showed that it was polymerized perfluoroethylene, with the iron from the inside of the container having acted as a catalyst at high pressure. Kinetic Chemicals patented the new fluorinated plastic (analogous to the already known polyethylene) in 1941, and registered the Teflon trademark in 1945.
Where is Teflon made?
By 1948, DuPont, which founded Kinetic Chemicals in partnership with General Motors, was producing over two million pounds (900 tons) of Teflon brand Polytetrafluoroethylene per year in Parkersburg, West Virginia.
When was Teflon discovered?
Teflon thermal cover showing impact craters, from NASA's Ultra Heavy Cosmic Ray Experiment (UHCRE) on the Long Duration Exposure Facility (LDEF) Polytetrafluoroethylene was accidentally discovered in 1938 by Roy J. Plunkett while he was working in New Jersey for DuPont.
What is PTFE wax used for?
Micronized PTFE wax is known to reduce friction and increase the performance of anti-slippery and lubricating. Here is what you need to know on PTFE wax. Used For Scratch Resistance. Micronized PTFE acts as an additive to powder coatings. It improves the grip, and it is scratch resistance.
Can you use PTFE wax in paint?
So if you manufacture powder coating and solvent-free paints, consider adding PTFE wax to protect the products which you coat. With the small particles of the PTFE micro powders, it can be used in any lubricant. High-speed engines, kneading machines, and gearing equipment require oil-free lubricant.
Does PTFE wax work on thin film?
The size of the PTFE wax allows its use on a thin film. Also, it has heat and scratch resistance, which ensures your printing ink retains the consistency and remains scratch-free. Also, it is an excellent solvent resistance that ensures your printing remain solid even after the printed film is exposed to liquids.
Does PTFE wax increase battery life?
PTFE wax increases battery life. Also, it reduces the production cost that would have been used during the manufacturing of the battery. Take Away Wax has a wide range of benefits, and some are yet to be discovered. However, the decrease in beekeeping means a decrease in bee wax.

Overview
Polytetrafluoroethylene (PTFE) is a synthetic fluoropolymer of tetrafluoroethylene that has numerous applications. It is one of the most well-known and widely applied PFAS, which in recent years however came under increased scrutiny by academic researchers because of adverse health effects, including cancer. The commonly known brand name of PTFE-based composition is Teflon by Chemo…
History
Polytetrafluoroethylene was accidentally discovered in 1938 by Roy J. Plunkett while he was working in New Jersey for DuPont. As Plunkett attempted to make a new chlorofluorocarbon refrigerant, the tetrafluoroethylene gas in its pressure bottle stopped flowing before the bottle's weight had dropped to the point signaling "empty". Since Plunkett was measuring the amount of gas used by w…
Production
PTFE is produced by free-radical polymerization of tetrafluoroethylene. The net equation is
n F2C=CF2 → −(F2C−CF2)n−
Because tetrafluoroethylene can explosively decompose to tetrafluoromethane (CF4) and carbon, special apparatus is required for the polymerization to prevent hot spots that might initiate this dangerous side reaction. The process is typically initiated with persulfate, which homolyzes to ge…
Properties
PTFE is a thermoplastic polymer, which is a white solid at room temperature, with a density of about 2200 kg/m and a melting point of 600 K (327 °C; 620 °F). It maintains high strength, toughness and self-lubrication at low temperatures down to 5 K (−268.15 °C; −450.67 °F), and good flexibility at temperatures above 194 K (−79 °C; −110 °F). PTFE gains its properties from the aggregate …
Processing
Processing PTFE can be difficult and expensive, because the high melting temperature, 327 °C (621 °F), is above the initial decomposition temperature, 200 °C (392 °F). Even when molten, PTFE does not flow due to its exceedingly high melt-viscosity. The viscosity and melting point can be decreased by inclusion of small amount of comonomers such as perfluoro (propylvinyl ether) and hexafluoropropylene (HFP). These cause the otherwise perfectly linear PTFE chain to beco…
Applications and uses
The major application of PTFE, consuming about 50% of production, is for the insulation of wiring in aerospace and computer applications (e.g. hookup wire, coaxial cables). This application exploits the fact that PTFE has excellent dielectric properties, specifically low group velocity dispersion, especially at high radio frequencies, making it suitable for use as an excellent insulator in connector assemblies …
Safety
While PTFE is stable and nontoxic at lower temperatures, it begins to deteriorate at temperatures of about 260 °C (500 °F), it decomposes above 350 °C (662 °F), and pyrolysis occurs at temperatures above 400 °C (752 °F). The main decomposition products are fluorocarbon gases and a sublimate, including tetrafluoroethylene (TFE) and difluorocarbene radicals (RCF2).
An animal study conducted in 1955 concluded that it is unlikely that these products would be ge…
Ecotoxicity
Sodium trifluoroacetate and the similar compound chlorodifluoroacetate can both be generated when PTFE undergoes thermolysis, as well as producing longer chain polyfluoro- and/or polychlorofluoro- (C3-C14) carboxylic acids which may be equally persistent. These products can accumulate in evaporative wetlands and have been found in the roots and seeds of wetland plant species, but has not been observed to have an adverse impact on plant health or germination s…