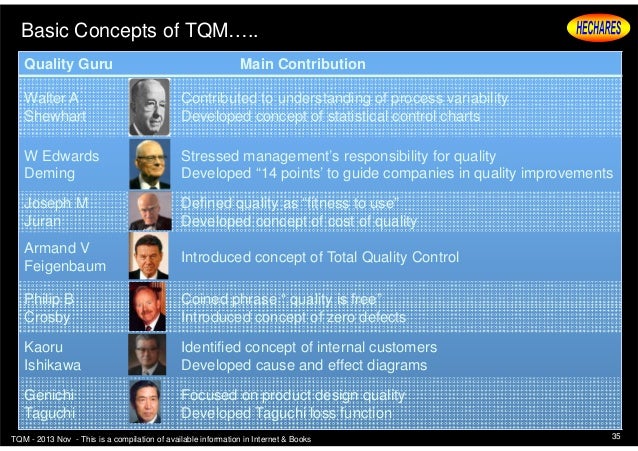
Quality Management Gurus and theories Quality Management resulted mainly from the work of the quality gurus and their theories. the American gurus featured in the 1950′s Japan: Joseph Juran
Joseph M. Juran
Joseph Moses Juran was a Romanian-born American engineer and management consultant. He was an evangelist for quality and quality management, having written several books on those subjects. He was the brother of Academy Award winner Nathan Juran.
Full Answer
What is a quality guru?
What is a quality guru? A guru, by definition, is a good person, a wise person and a teacher. A quality guru should be all of these, plus have a concept and approach to quality within business that has made a major and lasting impact.
What are the TQM guru?
Abstract: Over the past few decades, Total Quality Management (TQM) gurus have been developed certain theories in the area of business quality improvement, which caused a huge paradigm shift in improving the quality of products and services.
Who is this famous quality guru?
Dr. W. Edwards Deming: Probably the most known quality guru—for a reason. Developed a complete description and guide to quality management (14 points and 7 deadly diseases).
What is the meaning of TQM?
Total Quality ManagementTotal Quality Management (TQM) is a management approach that seeks to provide long-term success by providing unparalleled customer satisfaction through the constant delivery of quality IT services.
Who are the seven gurus of quality?
Top Quality GurusDr. Walter Shewhart. ... Dr. W. ... Dr. Joseph M. ... Armand V. Feigenbaum. ... Dr. Kaoru Ishikawa. ... Dr. Genichi Taguchi. ... Shigeo Shingo. ... Philip B.More items...
Who is not a quality guru?
1. Who among the following is not an American Quality Guru? Explanation: Crosby, Juran, and Deming are Quality Gurus from America. Ishikawa is from Japan and is famous for his development of quality initiatives.
Why are quality gurus important?
The Quality Gurus have all had a significant impact on the world through their contributions to improving not only businesses, but all organizations including state and national governments, military organizations, educational institutions, healthcare organizations, and many others.
Who is the father of quality?
Qual Saf Health Care. 2005 Aug;14(4):310-2. doi: 10.1136/qshc.
Who is the father of quality control?
William Edwards Deming (1900-1993) is widely acknowledged as the leading management thinker in the field of quality. He was a statistician and business consultant whose methods helped hasten Japan's recovery after the Second World War and beyond.
Why is TQM important?
TQM provides the quality assurance that customers will get what they expect, as well as a process for managing unsatisfied customers, make needed corrections and prevent similar reoccurrences. Explore the tools you need to achieve TQM. Check out QAD Quality Management Products.
What is TQM example?
TQM Example: One of the most famous examples of total quality management is Toyota. Toyota implemented Kanban System to make its assembly line more efficient. The company decided to keep just enough inventories to fulfill customer orders as they were generated.
What are 4 types of quality control?
What are the four types of Quality Control? The four types of quality control are process control, control charts, acceptance sampling, and product quality control.
Who is called the father of TQM?
Deming has been universally acclaimed as one of the Founding Fathers of Total Quality Management, if not the Founding Father. The revolution in Japanese manufacturing management that led to the economic miracle of the 1970s and 1980s has been attributed largely to Deming.
Who developed TQM?
W. Edwards Deming taught methods for statistical analysis and control of quality to Japanese engineers and executives. This can be considered the origin of TQM.
What is the similarities of all the gurus in quality management?
The quality Gurus all strived for the enhancement of quality of their products. Theyall wanted to achieve total quality, but had different approaches that actually in the end achieveda quality product. Deming, “Linked production of a product with the consumer needs” (Goetsch,2013, p. 11).
Where was TQM first developed?
JapanJapan began a process of implementing what came to be known as TQM.
What is TQM in business?
What is Total Quality Management (TQM)? A core definition of total quality management (TQM) describes a management approach to long-term success through customer satisfaction. In a TQM effort, all members of an organization participate in improving processes, products, services, and the culture in which they work.
What is TQM management?
TQM can be summarized as a management system for a customer-focused organization that involves all employees in continual improvement. It uses strategy, data, and effective communications to integrate the quality discipline into the culture and activities of the organization. Many of these concepts are present in modern quality management systems, ...
What is TQM history and the now?
TQM: The History and the Now (ASQTV) This episode explores total quality management’s beginnings and how it’s used to build and sustain a culture of quality today.
What is strategic management?
Strategic and systematic approach: A critical part of the management of quality is the strategic and systematic approach to achieving an organization’s vision, mission, and goals. This process, called strategic planning or strategic management, includes the formulation of a strategic plan that integrates quality as a core component.
Who is the most influential quality guru?
Dr. W. Edwards Deming (1900 – 1993) is probably the most widely-recognized and influential of the Quality Gurus. Deming was trained as a mathematical physicist, and he utilized mathematical concepts and tools (statistical process control) to reduce variation and prevent defects. However, one of his greatest contributions might have been in recognizing the importance of organizational culture and employee attitudes in creating a successful organization. In many ways, his philosophies paralleled the development of the resource-based view of organizations that emphasized that employee knowledge and skills and organizational culture are very difficult to imitate or replicate, and they can serve as a basis of sustainable competitive advantage.
What is quality management?
Quality management is the practice of managing the whole production process to produce an excellent (quality) product or service. Quality management focuses on the customer and meeting the customer's needs, and everyone in the firm is responsible for the quality of the product.
What is Deming's approach to quality?
Deming's approach requires an organization-wide cultural transformation. He advocated a statistical analysis of the manufacturing process and emphasized cooperation of workers and management to achieve high-quality products. Deming's quality methods centered on systematically tallying product defects, analyzing their causes, correcting the causes, and recording the effects of the corrections on subsequent product quality as defects were prevented. He taught that it is less costly in the long run to get things done right the first time than to fix them later.
Why is quality control important?
Quality control is used to prevent things from getting worse. Quality control is the inspection part of the Quality Trilogy where operators compare actual performance with plans and resolve the differences. Chronic waste should be considered an opportunity for quality improvement, the third element of the Trilogy. Quality improvement encompasses improvement of fitness-for-use and error reduction, seeks a new level of performance that is superior to any previous level, and is attained by applying breakthrough thinking.
Is Juran's Quality Trilogy enough?
Juran's Quality Trilogy and Quality Roadmap are not enough . An infrastructure for Quality must be developed, and teams must work on improvement projects. The infrastructure should include a quality steering team with top management leading the effort, quality should become an integral part of the strategic plan, and all people should be involved. As people identify areas with improvement potential, they should team together to improve processes and produce quality products and services.
Does Deming say that knowledge is not possible without theory?
Deming emphasized that knowledge is not possible without theory, and experience alone does not establish a theory. Experience only describes — it cannot be tested or validated — and alone is no help for management. Theory, on the other hand, shows a cause-and-effect relationship that can be used for prediction.
How to measure lack of quality?
The lack of quality should be measured as function of deviation from the nominal value of the quality characteristic. Thus, quality is best achieved by minimizing the deviation from target (minimizing variation).
How to improve the quality of a company?
Encourage education. Institute a vigorous program of education and self-improvement for everyone. Clearly define top management’s permanent commitment to ever improving quality and productivity. Put everybody in the company to work to accomplish the transformation. Support is not enough, action is required.
What is management's job?
It is management’s job to work continually on improving total system. Institute training on the job for all, including management, to make better use of every employee. New skills are required to keep up with changes in products and processes. Adopt and institute leadership aimed at helping people do a better job.
What is CWQC in manufacturing?
Established concept of Company Wide Quality Control (CWQC) – participation from the top to the bottom of an organization and from the start to the finish of the product life cycle
What is quality prevention?
Quality is conformance to requirements. Quality prevention is preferable to quality inspection. Zero defects is the quality performance standard. Quality is measured in monetary terms – the price of non-conformance.
Should quality be designed into the product and not inspected into it?
Quality should be designed into the product and not inspected into it. The product should be so designed that it is immune to causes of variation.
Why are they called quality gurus?
They are called quality gurus to those people specialized in this field who have known how to take advantage of their knowledge and observations to reform what needed improvement.
Who is the father of total quality?
1- Edwards Deming. It is considered the father of total quality, offering novel systems to measure it. His aim was to satisfy the customer to the maximum, offering products as cheap as possible. For him that forced the company to stop innovating and improving.
What are the three points of Quality Control?
To summarize its philosophy, three points can be highlighted: 1- Controlling quality is doing what needs to be done. 2- Quality control begins and ends with training at all levels. 3- The appropriate corrective actions must always be taken.
What is the definition of quality?
There is no single definition of quality, since it depends on numerous factors. It varies depending on the area of work and the time, among other elements. In the field of administration, it can be said that quality consists of perfecting the management that must be carried out, reaching the point of maximum performance.
Where was the thinker of quality born?
This thinker was born in Romania and made part of his work in Japan. It establishes several different meanings to define quality.
Why was Taguchi's loss function important?
For him it was important to observe the production process of a product as a whole: from its design until it was in the hands of a client. Through what he called the loss function, Taguchi was able to analyze the quality of any product based on the loss it would generate to society during its useful life.
What is a quality circle?
Definition of Quality Circle <ul><li>A small group of between six and twelve people who do the same or similar work, voluntarily meeting together regularly for about an hour per week in paid time , usually under the Leadership of their own supervisor , and trained to identify , analyze, and solve some of the problems in their work , presenting solutions to management , and where possible, implementing the solutions themselves .' </li></ul>
When was the Quality Circle Forum started?
In India Quality Circle Forum was started in 1980 with Headquarters at Hyderabad. </li></ul><ul><li>Quality Circles defined: </li></ul><ul><li>It's a small group comprising of 6 to 12 employees doing similar work meet together voluntarily on a regular basis for identifying improvements in their respective work areas.
What is a coordinator in a quality circle?
Roles and Responsibilities Coordinator , who also acts as a facilitator, is an individual responsible for coordinating and directing the quality circles activities within an organization and carries out such functions as would make the operations of quality circles smooth , effective and self-sustainable .
When did Toyota introduce TQC?
Toyota Motor Corporation <ul><li>Toyota Motor Corporation introduced total quality control or TQC in 1971. Fours years later, the company was awarded the Deming Application Prize for their efforts.
What is top management action?
Top management commitment and action Clearly define top management's permanent commitment to ever improving quality and productivity, and their obligation to implement all of these principles. Indeed, it is not enough that top management commit themselves for life to quality and productivity.
Who are the quality Gurus?
The Quality Gurus—Dr. W. Edwards Deming, Dr. Joseph Juran, Philip Crosby, Armand V. Feigenbaum, Dr. H. James Harrington, Dr. Kaoru Ishikawa, Dr. Walter A. Shewhart, Shigeo Shingo, Frederick Taylor, and Dr. Genichi Taguchi— have made a significant impact on the world through their contributions to improving not only businesses, but all organizations including state and national governments, military organizations, educational institutions, healthcare organizations, and many other establishments and organizations.
What percentage of quality problems are under management's control?
In emphasizing management's responsibility, Deming noted that workers are responsible for 10 to 20 percent of the quality problems in a factory, and that the remaining 80 to 90 percent is under management's control. Workers are responsible for communicating to management the information they possess regarding the system.
Why is quality control important?
Quality control is used to prevent things from getting worse. Quality control is the inspection part of the Quality Trilogy where operators compare actual performance with plans and resolve the differences. Chronic waste should be considered an opportunity for quality improvement, the third element of the Trilogy. Quality improvement encompasses improvement of fitness-for-use and error reduction, seeks a new level of performance that is superior to any previous level, and is attained by applying breakthrough thinking.
When was Juran's Quality Control Handbook published?
His third book, Juran's Quality Control Handbook, published in 1951, was translated into Japanese. Other books include Juran on Planning for Quality (1988), Juran on Leadership for Quality (1989), Juran on Quality by Design (1992), Quality Planning and Analysis (1993), and A History of Managing for Quality (1995).
Who is the founder of the International Academy for Quality?
Feigenbaum was the founding chairman of the International Academy for Quality and is a past president of the American Society for Quality Control, which presented him its Edwards Medal and Lancaster Award for his contributions to quality and productivity. His Total Quality Control concepts have had a very positive impact on quality and productivity for many organizations throughout the industrialized world.
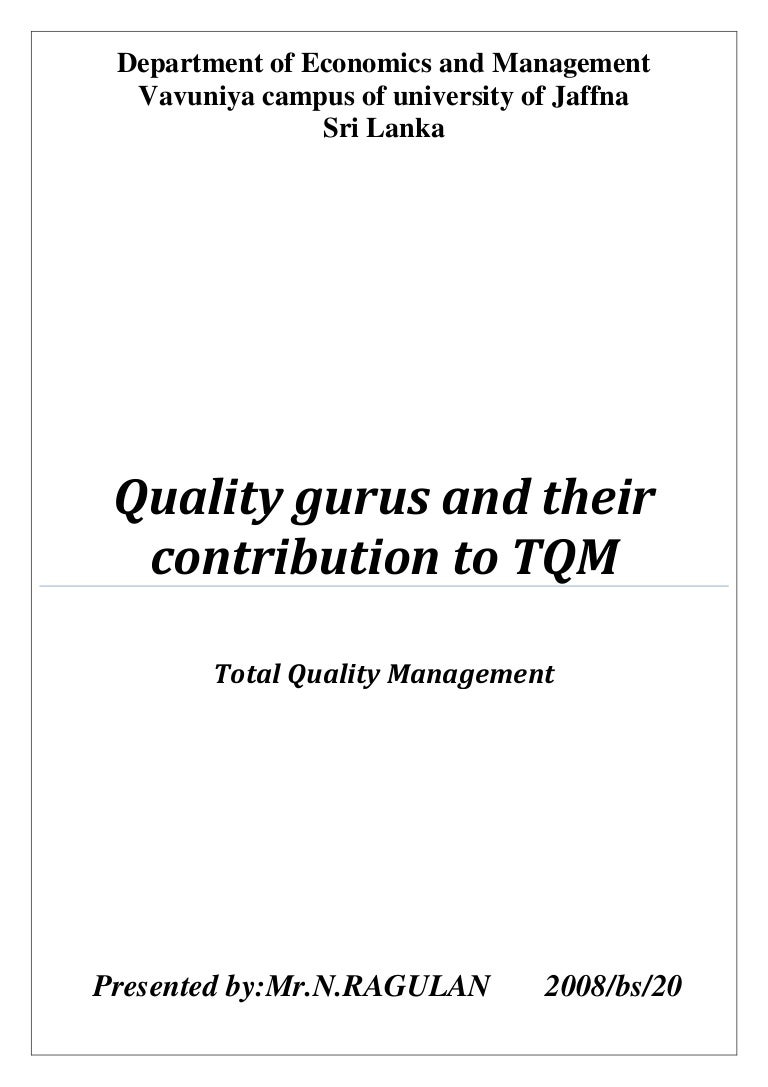