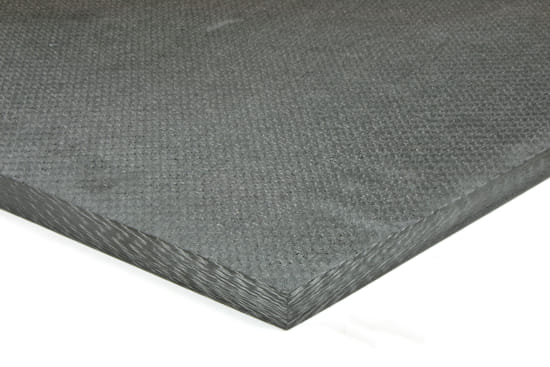
QISO carbon fiber fabric is balanced, symmetric and quasi-isotropic, all in one layer. SOURCE: A&P Technology. According to Savoie, QISO enables material savings by not having to cut and orient each individual ply to create a quasi-isotropic layup, as is typically done with conventional weaves.
What is quasi isotropic laminate?
What are the properties of carbon fiber?
What are the properties of isotropic substances?
What are the requirements for carbon fiber laminate?
How many layers of carbon fiber are there?
Is wood stronger than carbon fiber?
Is CFRP laminate anisotropic or anisotropic?
See 2 more
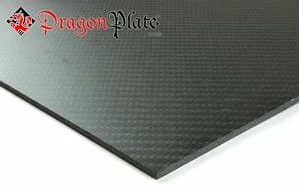
What is a quasi-isotropic lay up?
➢ Quasi-isotropic means having isotropic properties in-plane. A. quasi-isotropic part has either randomly oriented fiber in all. directions, or has fibers oriented such that equal strength is. developed all around the plane of the part.
What is quasi-isotropic laminates?
A quasi-isotropic laminate results when the individual lamina are oriented in such a manner as to produce an isotropic [A] matrix. This means that extension and shear are uncoupled (A16 = A26 = 0), the components of [A] are independent of laminate orientation, and for the quasi-isotropic laminate.
Is carbon fiber isotropic or anisotropic?
anisotropicGraphite and Carbon fibers are highly anisotropic materials which can be adequately modeled as transversely isotropic, with symmetry axis in fiber direction.
Are carbon fibers isotropic?
Carbon Fiber is Directionally Dependent – Anisotropic Unlike metals, carbon fiber, and composites in general, are called anisotropic materials. This means the properties of the material are directionally dependent.
What is the difference between isotropic and composite material?
The properties of isotropic materials, such as cubic crystals and amorphous materials (for example, glass), do not change when the substance moves. The properties of anisotropic materials, such as wood and composites, vary along with the material's directions.
Why is carbon fiber anisotropic?
Anisotropic means a material with different strength and stiffness in different directions through the material. For example, wood is stronger along the grain than across it. Carbon fiber laminates made with the fibers all oriented in one direction are extremely anisotropic.
What is difference of isotropic and anisotropic?
Isotropic refers to the properties of a material which is independent of the direction whereas anisotropic is direction-dependent. These two terms are used to explain the properties of the material in basic crystallography.
What is meant by isotropic material?
Isotropic materials are materials whose properties remain the same when tested in different directions. Isotropic materials differ from anisotropic materials, which display varying properties when tested in different directions. Common isotropic materials include glass, plastics, and metals.
What are isotropic material examples?
Common isotropic materials include glass, plastics, and metals. On the other hand, fiber-reinforced materials such as composites and natural materials such as wood tend to display anisotropic properties.
Are there different types of carbon fiber?
There are two types of Carbon Fibers: Filament and Staple. In the subsequent processing, the fibers are given varieties of the final product forms.
Are fiber-reinforced composites isotropic?
2.1. Fiber-reinforced composites can be characterized as transversely isotropic materials, with the unidirectional fibers representing the axis normal to the isotropic plane.
What is carbon Fibre reinforced plastic isotropic?
CFRP (Isotropic) Carbon fiber reinforced polymer (CFRP) composites offer greater stiffness and strength than any other type, but they are considerably more expensive than glass fiber reinforced polymer (GFRP). Continuous fibers in a polyester or epoxy matrix give the highest performance.
What are the types of laminates explain each types?
Popular Types of Decorative Laminates in IndiaMatte-Finish Laminates. As the name implies, these laminates have a matte finish. ... Gloss-finish Laminates. ... Textured Laminates. ... Metallic Laminates. ... PVC-Finish Laminates. ... Acrylic-finish Laminates. ... Exterior Laminates. ... High-Pressure Laminates.More items...•
What are the different categories of laminates available?
What are the Different Types of Laminates & Their Cost?Matte-finish laminate. ... Textured laminate. ... Gloss-finish laminate. ... Metallic laminate. ... PVC-finish laminate. ... Acrylic-finish laminate. ... Exterior laminate.
What are the types of lamination?
There are, in fact, three main types of lamination used in printing: matte, gloss, and “soft touch” lamination.
What are the types of hybrid laminates?
According to Kretsis et al. [3] types of hybrid composites include: (1) interply/multi-layer (layer-by-layer) hybrids, (2) intraply/ commingled (yarn-by-yarn) hybrids, (3) intimately/randomly (fiber-by-fiber) mixed hybrids, (4) sandwich like hybrid composite structures.
What is multidirectional laminate?
Multidirectional laminates have plies placed in multiple orientations so as to yield multidirectional stiffness properties for a wide range of applications, for example, quasi-isotropic laminates consisting of a mix of plies in 0, 45, −45, and 90 degrees orientations such that its in-plane elastic moduli are isotropic in nature. When these laminates are loaded in uniaxial tension along the longitudinal (0 degree) direction, ply cracking typically begins in 90 degree plies and proceeds in other off-axis plies at higher loads, causing damage in multiple modes. To predict evolution of ply cracking in multiple off-axis plies, Singh and Talreja52 extended the fracture mechanics-based model described in the preceding section. In this analysis, the work required to close N cracks in State 1 with crack spacing s ( Fig. 6 (a) ), and 2N cracks in State 2 with crack spacing s /2 ( Fig. 6 (b) ), can be written as
What is the maximum stress applied to the OHT coupon?
The maximum stress applied to the OHT coupon was 277.0 MPa , which was 50% of the mean OHT strength of the laminate. As mentioned previously, the load ratio was 0.1 and the frequency of load cycles was 10 Hz. The stiffness degradation results due to matrix failure with fatigue load cycles from the simulation and the validation experiments are presented in Fig. 12.12. In this figure, the boundary of stiffness degradation in the experimental coupons is marked with the “x” symbol. Beyond this point, the ultimate failure of the OHT coupon occurs driven by fiber failure, which is outside the scope of this study. Observing the figure, it can be noticed that two out of the six coupons tested in the experimental program failed at relatively low fatigue life. For the other four coupons, stiffness reduced slightly driven by matrix failure for up to 1 million load cycles. After this point, the coupons experienced significant stiffness reduction caused by fiber failure and ultimately experienced two-part failure between 1.4 and 1.8 million cycles (not shown in the figure). Two simulation cases are reported in Fig. 12.12: with and without the delamination layer. Observing the simulated stiffness degradation plots, it can be concluded that they followed the same trend as the experimental coupons that did not fail early. The simulated stiffness degradation plots are shown for up to 1.5 million cycles and upon reaching this number of cycles, the coupons retained about 95% of the initial stiffness. Another important point that can be observed from the figure is the significance of the delamination layer—adding the delamination layer clearly influences the stiffness degradation process since it acts as a load-transfer link between two composite layers. The degradation factor for the delamination layer elements was chosen to be 0.01% or 1E-4, which practically diminished any postfailure load-carrying capability. This value of the degradation factor is consistent with sudden/discrete degradation models present in the literature ( Garnich and Akula, 2009 ).
What is quasi isotropic laminate?
A quasi-isotropic laminate results when the individual lamina are oriented in such a manner as to produce an isotropic [A] matrix. This means that extension and shear are uncoupled ( A16 = A26 = 0), the components of [ A] are independent of laminate orientation, and for the quasi-isotropic laminate
What is black aluminium?
This family of laminates is typical in aircraft structures and is frequently known as “black aluminium.” The predicted final failure envelopes for this quasi-isotropic laminate are compared test data and are presented in Fig. 6. The majority of theories are in the first group and predict diamond shaped failure envelopes.
What is GIIC in physics?
and GIc and GIIc are the critical energy release rates in Mode I (opening mode) and Mode II (crack sliding mode), respectively. The multi-mode exponents M and N depend on the material system, for example, for glass/epoxy laminates, one uses M =1, N =2. Since a pure sliding action by itself will not generate a set of parallel cracks, the second term in Eq. (33) is small in comparison to the first term. For cross-ply laminates, the second term should be zero.
What is 24.9?
24.9. Tapered quasi-isotropic carbon-epoxy with two continuous and one dropped ply blocks
What does Ut and Un represent?
In above equations, un and ut represent the relative opening and sliding displacement of the cracked surfaces, respectively, and overbars show their averages. The new cracks in off-axis plies would form when the work required in going from State 1 to State 2 exceeds a critical value, i.e., if
What is Qiso weave?
QISO was introduced by A&P several years ago. Its weave pattern features 0°/±60° carbon fiber tows braided to yield a single layer of fabric that is balanced, symmetrical and quasi-isotropic. This offers real benefits for layup of complex tooling geometry. The bias yarns are two over, two under, alternating over and under the axial yarns with equal amounts of material by weight in each direction. A&P also notes that in testing, QISO has demonstrated reduced interlaminar stresses vs. more traditional laminates (e.g., 0°/±45°/90°) because all QISO plies feature the same architecture — i.e., you don’t have a large stiffness in the 0°, which then drops off in the ±45° directions.
What is QISO used for?
While the focus here is on tooling applications, QISO has and continues to be used for a variety of structural composites (see Editor’s Picks at right).
Who is Steve Savoie?
This blog comes from my discussions with Steve Savoie, a manufacturing and tooling engineer who spoke at last year’s International Boatbuilders Exhibition (IBEX). Steve has a background in both aerospace and marine composites, and specializes in process development, tooling design and equipment utilization. For example, his session at IBEX discussed temporary oven design and cheap ways to set up aerospace-quality data loggers and temperature control systems (watch for a blog on that coming soon). We were discussing a project using A&P Technology’s (Cincinnati, OH, US) QISO material, and he commented what a great material it is for tooling, but that a lot of people don’t seem aware of it for that end use. Not being an expert on tooling myself, I asked Steve to explain what QISO offers for composite tooling and why.
Is composite material still good?
Compared to legacy materials like steel, aluminum, iron and titanium, composites are still coming of age, and only just now are being better understood by design and manufacturing engineers. However, composites’ physical properties — combined with unbeatable light weight — make them undeniably attractive.
What is quasi isotropic laminate?
Quasi-isotropic laminates are made when the orientations of the plies are balanced so that the extensional stiffness of the laminate is the same in each in-plane direction. Typically, quasi-isotropic sheets are created using carbon fiber weaves with plies oriented at 0º, 90º, +45º, and -45º, with at least 12.5% of the plies in each ...
What are the properties of carbon fiber?
These properties are: isotropic, quasi-isotropic, and anisotropic.
What are the properties of isotropic substances?
These properties are: isotropic, quasi-isotropic, and anisotropic. Isotropic means a material with strength and stiffness that are the same when measured in any direction through that material. Examples of isotropic substances are glass and metals. Quasi-isotropic means a material having isotropic properties, but only in-plane.
What are the requirements for carbon fiber laminate?
In addition to orientation angles, there are other design requirements for a quality carbon fiber laminate: The layup must be symmetrical. In addition, each lamina would typically: Contain the same fiber-resin ratio; Have the same layer thickness; Contain the same fiber type and geometry. In more complex designs, these rules may not apply.
How many layers of carbon fiber are there?
In a typical quasi-isotropic carbon fiber sheets, the sheet must contain at least 4 layers, and the individual layers must contain identical stiffness and thicknesses. Furthermore, the fiber orientation must be balanced and symmetrical.
Is wood stronger than carbon fiber?
For example, wood is stronger along the grain than across it. Carbon fiber laminates made with the fibers all oriented in one direction are extremely anisotropic. Other laminate designs can have various degrees of anisotropy depending on how balanced the laminate design is.
Is CFRP laminate anisotropic or anisotropic?
In other words, the strength and stiffness are equal in all directions within the plane of the part. Many CFRP laminates fall within this category. Anisotropic means a material with different strength and stiffness in different directions through the material. For example, wood is stronger along the grain than across it.
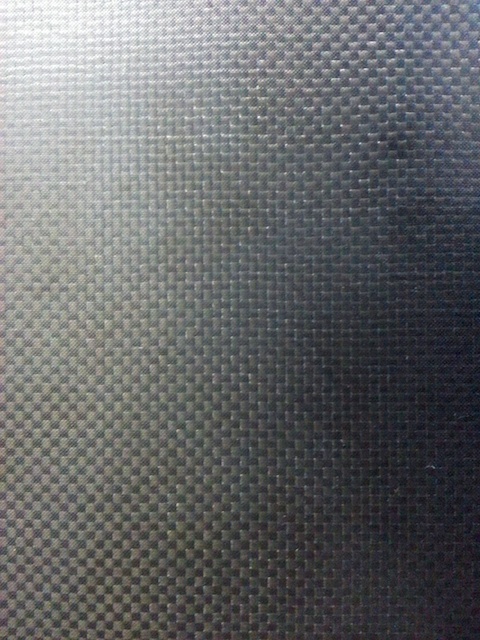