
4.1 Surface preparation methods
Method | Tool / Material | Application | Application | Application range |
1 | 2 | 3 | ||
Chiseling | Hammer and chisel | x | x | Local; for smaller areas a) |
Chiseling | Chisel (electric, pneumatic) | Local; for smaller areas a) | ||
Chiseling | Needle gun | x | x | Local; for smaller areas a) |
What is the purpose of surface preparation?
Surface preparation is the process of treating the surface of a substance in order to increase its adhesion to coatings. The single most important function that influences coating performance is the quality of surface preparation. This can be done mechanically or chemically. The surfaces most often prepared are: Steel.
What is sursurface preparation?
Surface preparation refers to the various methods that can be used to treat the surface of a material prior to coating application, the use of adhesives and other procedures. Surface preparation is essential for treating steel and other substrates before they are painted, coated or lined.
What is surface preparation for joining?
What is Surface Preparation for Joining? Surface preparation can be defined as steps and/or procedures to be followed prior to welding aimed at ensuring sound welds. Depending on the substrate material and the adhesive being used, different degrees of surface preparation are required.
What is surface preparation in corrosion protection?
Surface preparation. Surface preparation is the essential first stage treatment of a steel substrate before the application of any coating, and is generally accepted as being the most important factor affecting the total success of a corrosion protection system.
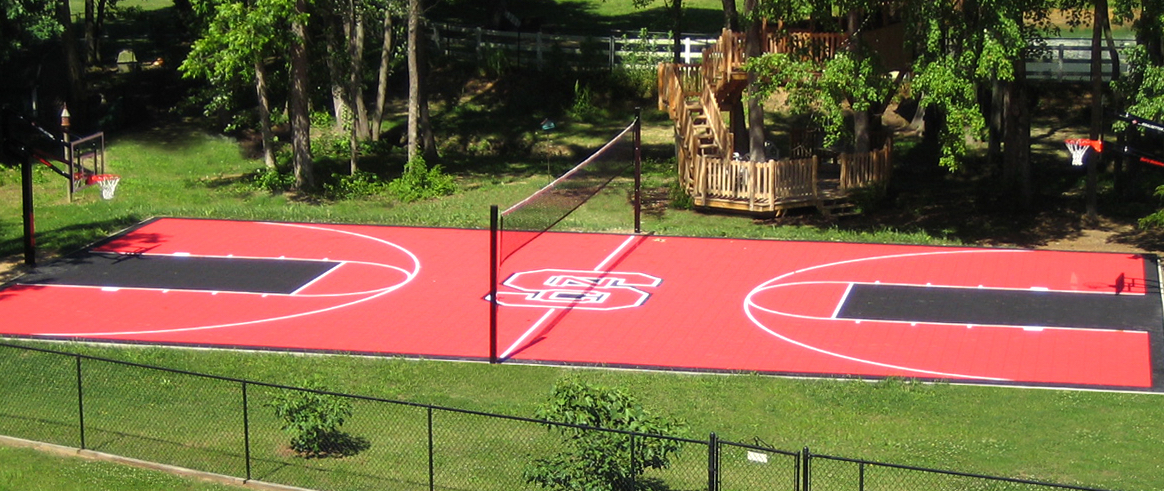
What do you mean by surface preparation?
Surface preparation refers to the various methods that can be used to treat the surface of a material prior to coating application, the use of adhesives and other procedures. Surface preparation is essential for treating steel and other substrates before they are painted, coated or lined.
What are surface preparation steps?
Surface Preparation (or Surface Prep for short) is the process of cleaning and readying surfaces for new coatings. Due to varying attributes and performance characteristics of the many coating types, surface preparation requirements can also be unique from project to project.
Why is surface preparation important before coating?
Surface preparation is the most critical aspect of a coating system's performance, in which coating performance is determined by the coating's ability to adhere to the substrate material. Surface preparation removes uncontrolled impurities like mill scale and grease to create an appropriate coating profile.
Why do we need to prepare the surface before finishing?
Section 2 – Surface preparation Surface preparation is the most important part of any finishing process, and is the foundation upon which you build the rest of your finish. When your work is presented for polishing, it must be free of all surface blemishes.
What are the methods of surface preparation?
Methods of surface preparation include: 1 Chemical cleaning (SSPC-SP1): Prior to using any method of surface preparation, it is essential to carry out chemical cleaning, which involves the removal of dirt, oil, grease and other foreign materials with organic solvents or detergents. 2 Tool cleaning: This involves two types - hand tool cleaning (SSPC-SP 2) and power tool cleaning (SSPC-SP 3). Loosely adhering mill scale, rust and old paint coatings may be removed from steel by hand wire brushing, sanding, scraping and chipping. However, these methods are incomplete, and always leave a layer of tightly adhering rust on the steel surface. Power tools include rotary wire brushes, sanding discs and needle guns. Power tool cleaning is in general more effective and less laborious than hand tool cleaning for the removal of loosely adhering mill scale, paint and rust. 3 High-low or Combinational Pressure Water Cleaning (SSPC-SP 12): Fresh water cleaning is always necessary to remove salts, fouling, any loose paint and other contaminants. 4 Abrasive Blast Cleaning (SSPC-SP5 / NACE 1 from SSPC-SP11 / NACE 5): Blast cleaning is based on the principle of an abrasive jet of particles in a compressed air stream impinging on the surface, removing impurities, mill scale, rust and old paint. Abrasive blast cleaning is the most thorough and widely used method of surface preparation in the shipbuilding and repair industry.
What is SSPC SP1?
Chemical cleaning (SSPC-SP1): Prior to using any method of surface preparation, it is essential to carry out chemical cleaning , which involves the removal of dirt, oil, grease and other foreign materials with organic solvents or detergents.
What is the most important function of coating?
The single most important function that influences coating performance is the quality of surface preparation. This can be done mechanically or chemically. The surfaces most often prepared are: Steel. Concrete. Wood. Plastic. Aluminum. Surface preparation is also known as grit blasting.
What is surface treatment?
Generally, surface treatments can be mechanical, chemical, or electrical. Newer treatments use plasma, UV light or lasers for surface modification. For nonmetal surfaces, cleaning stages consist of an initial solvent cleaning, followed by abrasion or a chemical surface alteration. Solvent cleaning is then repeated.
What is surface modification?
In general, surface modification could include one or more of a number of operations such as cleaning, removal of loose material, physical and/or chemical modification of a surface, and application of a coating to the surface.
What is abrasive blasting?
Abrasive blasting is another effective method for surface preparation and standard techniques apply to the specified surface profile. Special precautions are taken for this type of blasting in a confined space. An alternative method of abrasive blasting with environmental benefit is sponge blasting.
Why is Surface Preparation Important?
Over time, concrete commercial floors succumb to normal wear and tear. This includes dirt, oil, grease, grime, and other contaminants that can compromise your existing concrete flooring. If messy surfaces aren’t properly treated, the coating’s effectiveness is greatly impaired.
Surface Preparation Steps
There are several steps in the surface preparation process. The first step is to assess the condition of the concrete surface. Assessments determine the severity of damage. They also determine the type of cleaning needed to complete the job.
Different Methods Used in Surface Preparation
There are several types of surface preparation. As one of the most common techniques, abrasive blasting removes loose particles such as old paint, rust, and mill scale with a compressed air stream. Aerospace and healthcare facilities use abrasive blasting.
The definition of surface preparation, and what is the purpose of it?
Surface preparation refers to the many methods for treating a material’s surface before coating application, the use of adhesives, and other operations. And it is a required procedure before painting, coating, or lining steel and other materials.
Why is surface preparation needed for the performance of the coating process?
Surface preparation is the most critical aspect of a coating system’s performance, in which coating performance is determined by the coating’s ability to adhere to the substrate material. Surface preparation removes uncontrolled impurities like mill scale and grease to create an appropriate coating profile.
How many steps for surface preparation? Does each step have any special roles?
To complete the process to prepare for the surface, we do need to fulfill specific things with various purposes. In general, there are six steps below.
What is surface preparation?
Surface preparation is the essential first stage treatment of a steel substrate before the application of any coating, and is generally accepted as being the most important factor affecting the total success of a corrosion protection system. The performance of a coating is significantly influenced by its ability to adhere properly to ...
Where is water introduced in a blaster?
The water is usually introduced immediately behind the nozzle so that it is atomised and accelerated through the nozzle orifice along with the air and abrasive. Water can also be introduced in controlled amounts at the base of the blast pot and is then mixed with the air and abrasive as it passes along the blast hose.
Why is ultra high pressure water jetting used?
Ultra-high pressure water jetting over 1,700 bar (25,000psi) is gaining in popularity, partly because of its ability to remove high percentages of soluble salts from the steel surface. It has the advantage of not generating spent abrasive and not incurring the cost of abrasive disposal. Also, at the higher pressures, lower volumes of water are used, and this makes disposal costs lower than with traditional water blasting methods. Ultra-high pressure water jetting leaves a warm surface from which traces of residual water quickly dry, but does not generate sufficient heat to cause thermal stress in the steel surface.
What is BS EN ISO 8501-1?
Various methods and grades of cleanliness are presented in BS EN ISO 8501-1. This standard essentially refers to the surface appearance of the steel after hand cleaning, power tool cleaning, abrasive blast cleaning or flame cleaning and gives descriptions with pictorial references of the grades of cleanliness.
Can you clean a surface with abrasive blasting?
Where it is not possible to clean by abrasive blasting, hand and power tool methods may be the only acceptable alternative methods. Modern power tooling has been developed not only to achieve a good standard of surface cleanliness and profile but also to provide near total containment of all dust and debris generated.
Is abrasive non-metallic?
A very wide range of abrasives is available. These can be non-metallic (metal slags, aluminium oxide, etc) and metallic (steel shot or grit, etc) The particle size of the abrasive is also an important factor affecting the rate and efficiency of cleaning.
What is architect specifications?
Architects specifications are often boilerplate and transfer from one job to another- even when job conditions are different. Contractors are busy and bid many jobs- often with no time, or due to distance they are unable to examine the project specs versus the product specs and job conditions.
Can you use multiple primer coats on a non-breathable coating?
If a non-breathable coating is applied, the escaping air can create air bubbles and craters in the cured coating. In this condition- multiple primer coats should be applied prior to installing the coating. Again, check with the coating manufacturer.

What Are The stages?
- There are several general stages that are followed to successfully prepare a surface for adhesion, coating, weldingor other procedures. These include:
What Are The Names of Surface Preparation Methods?
- Surface preparation can take the form of chemical or mechanical methods, including the use of solvents, abrasive blasting materials, heat, acids and jets of water. There are also more traditional techniques using hand or power tools. Abrasive blasting, sometimes termed grit blasting, [MR1] is generally deemed to be the most efficient and versatile surface preparation method and, as suc…
Post-Cleaning Considerations
- There are a number of extra considerations to be taken account of following surface preparation, depending on the exact nature of the surface and applications.
Why Surface Preparation Is Important Before Coating
- Surface preparation is seen as being the most important factor for the success of a coating system. The performance of coatings are influenced by the ability of the coating to adhere to the substrate material. Surface preparation not only cleans away undesirable contaminants like mill scale or grease, but also introduces a suitable profile for the coating. In the majority of cases, gri…
Is Surface Preparation Important in Adhesive Bonding?
- Adhesive bonding requires a clean, dry surface and surface cleaning provides this, allowing for high bond strengths and durability. Different substrate materials require different surface preparation methods, from a simple brushing to more extensive abrasive cleaning. However, even where not much preparation is required, the smallest of activities can make a big difference to t…
Conclusion
- Surface preparation is an important step for a range of materials ahead of coating, welding, and other processes. There are a range of different techniques that range in effectiveness and cost. Generally speaking, the more complete the cleaning, the more expensive the technique. In some cases, several surface preparation techniques need to be combined, such as through the use of …
Why Is Surface Preparation Important?
- Over time, concrete commercial floors succumb to normal wear and tear. This includes dirt, oil, grease, grime, and other contaminants that can compromise your existing concrete flooring. If messy surfaces aren’t properly treated, the coating’s effectiveness is greatly impaired. Surfaces that aren’t prepared beforehand can cost you more money out of pocket to get the job done corr…
Surface Preparation Steps
- There are several steps in the surface preparation process. The first step is to assess the condition of the concrete surface. Assessments determine the severity of damage. They also determine the type of cleaning needed to complete the job. The next step is to remove the old coatings before applying the new. Failure to do this causes the coating t...
Different Methods Used in Surface Preparation
- There are several types of surface preparation. As one of the most common techniques, abrasive blasting removes loose particles such as old paint, rust, and mill scale with a compressed air stream. Aerospace and healthcare facilities use abrasive blasting.