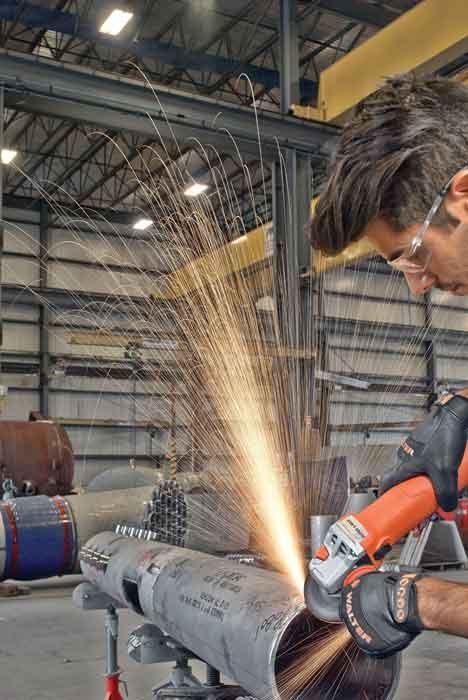
Full Answer
What type of grinding wheel is used for stainless steel?
The most important factor when grinding stainless steel is to use contaminant-free or INOX wheels. This designation means the wheels are manufactured with additives that contain less than 0.1% iron, sulfur and chlorine.
What is the best abrasive for stainless steel?
The best abrasive grains to cut and grind stainless steel alloys include aluminum oxide, zirconia, and ceramic. Zirconia will outperform aluminum oxide in stainless steel applications.
Can you use a grinder on stainless steel?
2 Cut stainless steel with a grinder. An angle grinder is a handheld tool you can also use to cut your stainless steel.
How do I choose a grinding wheel?
How to choose a Grinding WheelThe Material Being Ground.The Severity of the Operation.Required Finish and Form Accuracy.Area of Contact.Wheel Speed.Coolant Use.Machine/Spindle Horse Power.
How do you grind stainless steel?
Always start grinding with a pullback motion instead of a push to reduce the chance of gouging this expensive material. Flap discs are another popular choice for working with stainless steel, because they grind and finish the workpiece in a single step.
Will stainless steel rust if you grind it?
Any carbon steel dust particles settling onto the stainless steel during fabrication can contaminate its surface, increasing the potential for rust formation. Furthermore, cleaning and grinding tools that have been used with carbon or low alloy steel must be kept separate from stainless steels.
What tools do you use on stainless steel?
Screwdrivers.Pliers.Wrenches.Scissors & Knives.
How do you smooth out stainless steel edges?
0:321:07Stacey David's GearZ Quick Tip - Smooth Edges Of Cut MetalYouTubeStart of suggested clipEnd of suggested clipSo you put it in the hole. It's self centering. And then you just go around the perimeter of theMoreSo you put it in the hole. It's self centering. And then you just go around the perimeter of the hole. This cuts off all the sharp edges leaving.
Can you cut stainless steel with carbide blade?
These carbide tip blades offer exceptional fatigue, shock and wear resistance, even when cutting difficult to machine materials. The Haltbar 1002 can slice through steels, high-alloy metals, titanium, stainless steel, Inconel and more.
What is the hardest grinding wheel?
Diamond: The hardest mineral in the world, diamond abrasives offer an unmatched combination of durability and cutting speed. Superabrasive diamond cutting wheels use synthetic diamond crystals that are manufactured specifically for use in cutting applications.
What are diamond grinding wheels used for?
Diamond wheels are grinding wheels with industrial diamonds bonded to the periphery. They are used for grinding extremely hard materials such as carbide cutting tips, gemstones or concrete.
What are white grinding wheels used for?
White wheels are ideal for the general purpose grinding of ferrous metals but they are particularly suited for the sharpening of cutting tools such as chisels and plane irons. These wheels help keep your tools cooler to avoid overheating and weakening the cutting edge.
How do you polish stainless steel after welding?
Chemical cleaning is the most commonly used method for metal cleaning. It involves using a chemical pickling paste for cleaning after a welding job. The paste is applied to the affected areas using a brush or spray and left on the surface for some time to interact with the metal.
Can I sand stainless steel?
Stainless steel is a great look until you scratch it. Then it looks awful. But you can “sand” out the scratches with sandpaper (400 to 600 grit) and a sanding block, an abrasive pad, or with a rubbing compound. Or buy a stainless steel repair kit and get everything you need.
Which abrasive is best?
The Best Abrasive Grain Type For Metalworking For stock removal and weld blending, ceramic and zirconia do the best job on stainless steel and other ferrous metals while aluminum oxide is recommended for alloys, gray iron, and non-ferrous metals.
Can you use aluminum oxide on stainless steel?
Because of the superior strength of Aluminium Oxide, it is ideal for use on robust materials such as steel or stainless steel.
What is the best grinding wheel for stainless steel?
When grinding stainless steel, white fused alumina (WA) is generally used. White fused alumina features good cutting performance and good self-sharpening. Grinding stainless steel with cubic boron nitride grinding wheel has the best effect (recommended grain size F120, concentration 100%, resin bond). Because CBN has high hardness, grains easily wear, and good chemical stability, and it does not have a chemical affinity with iron group elements, therefore CBN grinding wheels are not blocked easily when grinding.
What is a grinding wheel good for?
It is good for reducing grinding heat and blocking of grinding wheels. When grinding austenitic stainless steel, microcrystalline fused alumina and green silicon carbide made from grinding wheel are used. The workpiece roughness can be greatly reduced, and reduce or eliminate the burn.
What impact does grain size have on stainless steel?
The grain size of abrasive grains has a direct impact on the surface roughness. Owing to the high toughness of stainless steel, abrasive debris blocks easily. If fine grit grinding wheels are used, makes the abrasives lose cutting effect, and makes the workpiece surface not finish.
What is a MA grinding wheel?
When grinding Cr17Ni7A1 precipitation hardening stainless steel, microcrystalline fused alumina (MA) grinding wheel is used. Microcrystalline fused alumina features high toughness, high cutting performance, and long service life. Self-sharpening is cracked along the crevice of microcrystalline, and it does not cause large or whole abrasive grains to fall off. It is good for reducing grinding heat and blocking of grinding wheels.
Why does my grinding wheel have scratches?
The abrasive debris falling off the grinding wheel to fall the place between the grinding wheel and the workpiece, causing the scratches on the working surface . The debris fluid is not clean, mixed with abrasive debris, and the supply of debris fluid is insufficient, scratches occur in the grinding process.
Why is stainless steel grinding wheel blocked?
Owing to high toughness of stainless steel, abrasive debris is reacted with sand grains easily under certain grinding temperature, contact pressure and relative velocity conditions. Therefore, abrasive debris adheres to the grinding wheels, filling the gap among the abrasive grains, making the grinding wheel blocked sharply. At this time, the grinding conditions deteriorate rapidly, heat serious, and the surface roughness decreases significantly.
Why are CBN grinding wheels not blocked?
Because CBN has high hardness, grains easily wear, and good chemical stability, and it does not have a chemical affinity with iron group elements, therefore CBN grinding wheels are not blocked easily when grinding. The grinding force and grinding heat of CBN grinding wheels are low, not burn the workpieces. But the price of CBN grinding wheels ...
What type of grinder is used in mold making?
More specialized grinding, such as the jig-grinder, Blanchard grinder, and tool-and-cutter grinder are commonly used, but such specialized methods are not the focus here.
What does 800 mean in grinding?
Most wheels fall between G-K, with lower letters in the alphabet indicating softer grades. 800 means that it has induced porosity.
What does 46 grit mean?
R stands for Ruby, which is a very hard grade of aluminum oxide, designed for tough tool steels. A represents Aluminum Oxide, which is by far the most common type of abrasive in typical grinding wheels. 46 stands for the grit size. Grits generally are between 32 and 220 grit.
How many grits are there in a screen?
Grits generally are between 32 and 220 grit. This number is the result of an international mesh size. Think of a screen with varying numbers of openings per square inch: the more openings, the greater the number, the smaller the grit. G represents the grinding wheel grade.
Can you get by with a wheel?
True, you can “get by” with just a few general-purpose wheels, but, to be effective you need to work smart and use the best wheel for the job. Here are some general rules for understanding the markings on the wheels.
What size wheels are best for grinding?
For this reason, finer grit sized wheels are required to grind hard materials and soft materials are best ground with medium to coarse grit size wheels. For most efficient operation, the grade must be adjusted to suit the hardness of the material.
What abrasives are available for grinding wheels?
Often referred to as just “Ceramic”, Norton Quantum’s patented ceramic form of aluminium oxide is harder and sharper than conventional abrasive grains.
What is a grinding wheel?
A grinding wheel is a precision tool with thousands of cutting points on its surface - abrasive grains that are held in place by a bond matrix (hence these are known as bonded abrasives) and separated by pores.
What grit size do I need?
When to select a coarse grit size: where the neatness of the surface finish is not essential to the project, a coarse grit can be used. Also, the coarser the grit, the more rapid the stock removal, which makes it more suitable for large areas of contact than fine gritted abrasives.
What type of abrasive is best for grinding steel?
The type of material affects the selection of abrasive, grit size and grade. Alumina type abrasives are the most suitable for grinding high tensile materials such as steel and ferritic cast irons. The more friable types of alumina are preferred on harder steels and applications having large arcs of contact.
What are the pores in a grinding mill?
These pores are hollow spaces between abrasive grains and the bond , which help with the clearance of discarded metal chips in the grinding process.
What happens when a wheel is in use?
When the wheel is in use, the abrasive grains cut into the material that is being ground, removing the unwanted surface material in small chips.
What are type 1 wheels?
Use these wheels for precision grinding on surface, cylindrical, and tool and cutter grinders. They are also known as Type 1 wheels and straight wheels.
What is the name of the wheel that doesn't corrode?
The absence of iron, sulfur, and chlorine in these wheels means they won’t corrode or discolor stainless steel. They are also known as INOX wheels, Type 27 wheels, raised-hub wheels, and grinding discs.
How long do ceramic oxide wheels last?
These high-density ceramic oxide wheels have two layers of fiberglass mesh reinforcement and last up to twice as long as long-life cutoff wheels when cutting aluminum, iron, stainless steel, and steel.
How many layers of mesh reinforcement are needed for a cut off wheel?
Two layers of fiberglass mesh reinforcement give these wheels at least three times the life of standard cutoff wheels when cutting metal such as aluminum, iron, stainless steel, and steel.
What is a cone abrasive?
Longer lasting than grinding bits, these abrasive cones remove heavy amounts of material and leave a rough surface texture. They have a threaded insert that attaches to the spindle on a straight grinder. Use in corners and inside castings.
What metals can you cut?
Make cuts in most metal, including aluminum, iron, stainless steel, and steel.
What is heat dissipating on wheels?
Heat-dissipating holes reduce material buildup and extend the life of the wheel. Wheels have a semiflexible backing that conforms to curved and rough surfaces.
What is the best material for angle grinder wheels?
Most of the best angle grinder wheels for metal cutting are made of aluminum oxide grain. This is the most popular material for wheels. The material offers a softer bond to the creation, which makes the discs easy to control and fast cutting features.
How to Choose the Best Angle Grinder Wheel for Cutting Metal?
Well, it is undeniable that you think it is easy to buy the best angle grinder discs seeing its sufficiency in the market. But when you are actually up to buy it, you realize finding the best one is the toughest task. Yes, the task is tough. Yet, we take the pleasure of covering you up with some important points while buying the best grinder wheels. Look!
What size discs are compatible with Makita?
These wheels are flat angle grinder wheel type. With a standard dimension, the discs are compatible with all angle grinders of 4.5-inch.
What is the best cut off wheel for angle grinder?
Your tempted mind might go for the cheap wheels but it is not worth it if you want to cut metal with it. 1. WORKPRO 20-pack Cut-Off Wheels, Thin Metal Cutting Disc for Angle Grinder. These excellent cut-off wheels from WORKPRO are the best metal cutting wheels for angle grinder.
Why use a dewalt cutting wheel?
They are more convenient to install and use. Moreover, the cutting wheels have a very sharp thin edge that provides a noise-free cutting.
What brands of wheels are compatible with angle grinders?
Many brands are manufacturing cut-off wheels with appropriate size diameter and thickness to install in most angle grinders. Including WORKPRO, SATC, Dewalt and many other renowned brands are offering wheel packs for angle grinders.
What speed is a 4 1/2 inch grinder?
These angle grinder wheels are perfectly compatible with your angle grinder of 4-1/2-inch with an arbor of 7/8-inch. They provide 80M/s with a speed of 13000 RPM which is a good deal. Also, the pack of grinding wheels is compatible with other angle grinders as well.
What is a resin cutting wheel?
1.Types of stainless steel cutting wheels. If the material of the cut off wheel is similar to the object being cut, a burn phenomenon will occur, so generally resin cutting wheels are used for cutting stainless steel, iron, and aluminum ( What is resin cutting wheel?)
What are cut off wheels made of?
4.Material introduction of stainless steel cut off wheel: 1 White corundum: It is made from industrial alumina powder, smelted and cooled in a high temperature above 2000 degrees in an arc, pulverized and shaped, magnetically removed iron, and sieved into a variety of particle sizes. Its texture is dense, high hardness, and granular Formed with a sharp angle, it is suitable for manufacturing ceramics, resin-consolidated abrasives, grinding, polishing, sandblasting, precision casting (corundum for precision casting), etc., and can also be used for manufacturing advanced refractory materials. 2 Brown corundum: the main raw materials are bauxite and coke (anthracite),and is smelted in an electric arc furnace at high temperature. The abrasive tools made from it are suitable for grinding higher tensile metals such as various General-purpose steel, malleable cast iron, hard bronze, etc., can also manufacture advanced refractory materials. It has the characteristics of high purity, good crystallization, strong fluidity, low linear expansion coefficient, and corrosion resistance. 3 Silicon Carbide: The raw materials are quartz sand, petroleum coke (or coal coke) and wood chips. The machine melts these materials at high temperature to make silicon carbide. Among today’s non-oxide high-tech refractory materials, such as C, N, B, silicon carbide is the most widely used and most economical one.
What is the hardest cutting disc?
There are many types of stainless steel cutting discs. The silicon carbide cutting wheel is the hardest, and the brown corundum cut off wheel is the weakest. White corundum: It is made from industrial alumina powder, smelted and cooled in a high temperature above 2000 degrees in an arc, pulverized and shaped, magnetically removed iron, ...
Why can't you cut stainless steel?
Because the hardness of aluminum is low and the hardness of stainless steel is high. If someone use an aluminum alloy cutting wheel to cut stainless steel, the cutting disc is quickly passivated and the stainless steel cannot be cut.
When cutting or grinding is stopped, the click speed should be stopped naturally?
When cutting or grinding is stopped, the click speed should be stopped naturally. It is strictly forbidden to manually apply pressure to the grinding wheel, which is considered to prevent its rotation
What is silicon carbide?
Silicon Carbide: The raw materials are quartz sand, petroleum coke (or coal coke) and wood chips. The machine melts these materials at high temperature to make silicon carbide. Among today’s non-oxide high-tech refractory materials, such as C, N, B, silicon carbide is the most widely used and most economical one.
What do you need to wear to work on a power tool?
Workers must wear eye, hand, ear protection and work clothes . The grinding wheel is correctly installed on the power tool, which is firm and stable, and at the same time, ensure that the speed of the power tool cannot be higher than the speed of the grinding wheel itself.
