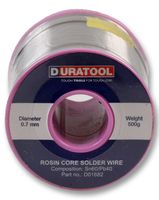
What is the difference between 50 50 and 60 solder? 60/40 melts at 374 degrees and becomes solid when it cools to 361 degrees. 50/50 melts at 421 degrees and is solid at 361 so has a working range of 60 degrees. This solder will produce a much flatter bead than 60/40.
What is the difference between 50/50 solder and 63/37 solder?
Note: 50/50 Solder cannot be sent to Pennsylvania due to that state's EPA regulations. 63/37 (63% tin - 37% lead.) 63/37 is "eutectic"; it melts and freezes at the same temperature (361.4°F). The instant freeze properties can reduce the chance of lumpy solder beads.
What is 60/40 solder made of?
A 60/40 solder is an alloy of 60 % tin and 40 % lead measured by weight. This type of solder has a melting point of around 190 °C. Another commonly used tin / lead solder alloy is 63/37, which has a melting point of 183 °C.
What temperature does 50 50 solder melt at?
50/50 (50% tin - 50% lead.) An ideal solder for copper foil seams and general purpose use. Melting temperature range: 361° - 421°F and solidifies at 361°. Note: 50/50 Solder cannot be sent to Pennsylvania due to that state's EPA regulations.
What is the difference between 50/50 tin and 60/40 tin?
Comparing solder 60/40 vs 50/50 Tin:Lead Alloy Tin% Lead% Liquidus Temp Pasty Range 40/60 40 60 247ºC 54°C 50/50 50 50 216ºC 33°C 60/40 60 40 191ºC 8°C 63:37 63 37 183ºC 0°C
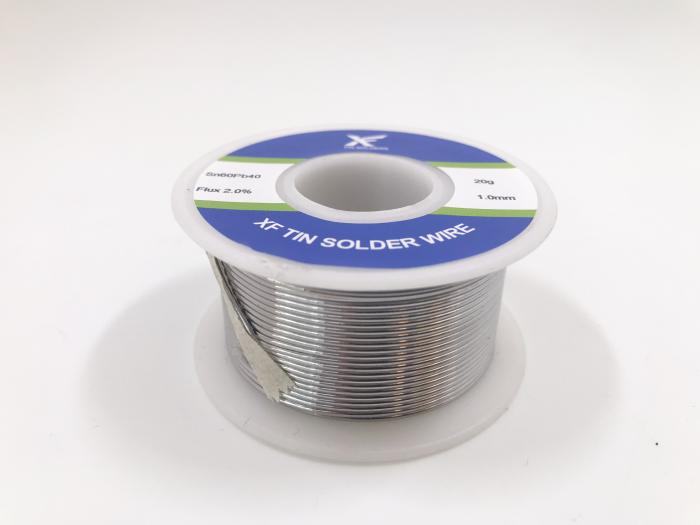
What is 50 50 solder generally used for?
50/50 is a general purpose solder used in applications involving soldering of copper and copper alloys and/or ferrous base alloys. This alloy offers satisfactory corrosion resistance properties. This alloy should not be used in soldering of potable water systems due to its high lead content.
What is so special about 60 40 solder?
This solder is composed of 60% tin and 40% lead which allows it to melt at a lower temperature.
What size solder is best?
For most electronics work, solder in the range of 0.4 - 1.0 mm in diameter will work well.
What temperature does 50/50 solder melt at?
361° - 421°F.Melting temperature: 361° - 421°F.
Which solder is stronger 60 40 or 5050?
The 60:40 solder is best suited for copper-foiled work because it stays liquid for a long time when cooling and can produce smoother and shinier beads. The 50:50 solder is a compromise if you cannot buy 40:60 solder. It is not as good as 60:40 solder for copper-foiled work because it does not stay liquid for as long.
What temp does 60 40 solder melt?
361.4°FIf using a 60/40% tin lead wire soldering, there will be a varying melting temperature range. It will begin to melt at 361.4°F and become a full liquid at 375.8°F. Tin lead wire solder is ideal for applications where there are delicate temperature requirements for soldering.
Is 60W enough for soldering?
Member. A 60W soldering iron might be a tad too much if it is not temperature regulated. For basic PCB soldering, something around 25W is more appropriate. Higher powered irons are often seen used in electronics, but most of the time these are temperature regulated.
Is thinner solder better?
The primary way of controlling how much solder you feed into a solder joint is by the length of solder you shove in. Thus if you assume a certain "length accuracy" of your hand, the overall volume accuracy of a thinner wire is higher. I personally use .
Which solder is easiest to use?
Alpha Metals 60/40 Tin-Lead Based Solder It's also simple and easy to use, allowing new DIYers to get professional results.
How hot does a 60 watt soldering iron get?
【Professional Function Design】This 60w 110v pencil-type soldering iron features adjustable temperatures(392 ℉-842 ℉/200-450 ℃) and thermostatic setting.
What solder has the lowest melting point?
Alloys commonly used for electrical soldering are 60/40 Sn-Pb, which melts at 188 °C (370 °F), and 63/37 Sn-Pb used principally in electrical/electronic work. The latter mixture is a eutectic alloy of these metals, which: has the lowest melting point (183 °C or 361 °F) of all the tin-lead alloys; and.
Does 50 50 solder contain lead?
DESCRIPTION. Black Swan's 50/50 Solder is a 50% tin and 50% lead alloy. Melting point ranges in 361° F to 421° F. Use for tin plating, sheet metal repair and copper DWV systems.
How strong is 60 40 solder?
The grade is 60/40 tin-lead. The tensile strength is 6900. The melting temperature is 375°F (190°C).
What is the difference between 60 40 and 63 37 solder?
The ratio of 63/37 gives this solder a slightly lower melting point than 60/40 solder (183C instead of 190C) which some say allows you to heat and solder the connection quicker, reducing the chance of damaging components or wiring.
Can you use 60/40 solder plumbing?
Electrical solder is commonly a 60/40 blend of lead and tin. Because of the dangers of toxic lead in drinking water, local building codes now legally require the use of lead-free plumbing solder on all potable water plumbing connections that require soldering.
What solder is best for stained glass?
The best flux for stained glass is a gel flux that has a thick enough liquid to wet and shine the solder seams when you hand-solder copper sheet metal or copper foil between the stained glass pieces. You also want to choose a flux that won't stain the copper before you have a chance to wipe it clean when soldering.
What is the difference between 60/40 and 50/50 solder?
The solder 60/40 contains 60% tin and 40% lead, while the solder 50/50 contains 50% tin and 50% of lead by weight . The solder 60/40 has higher content of tin comparing to solder 50/50 and this lead to difference in properties and cost.
What temperature is solder 50/50?
Solder 50/50 has solidus temperature 183℃ and liquidus temperature 216℃, it has bigger plastic range. So that means two things: firstly it requires more heat to work on solder 50/50; second solder 60/40 gives you a bit more than to work on the solder before it becomes pasty after solder tip is removed because cooling from 370℃ ...
Which is better, 60/40 or 50/50?
What to choose? Solder 60/40 gives you more than to flow the solder over the soldering area and helps you to get a nicer and smoother beads or solder lines; but if you prefer the solder to become solid in shorter time to prevent it to drop or penetrate through to create a mess, the solder 50/50 is a better choice as it comes pasty in shorter time. This might be more crucial problems when you work with solders for the stained glass or metal sheets joining.
What is 50/50 solder?from stortz.com
50/50 Solder – The most common solder in the roofing trade. The working temperature range of the solder is large which means that is easily workable for someone new to the task. The bead will be strong and will lay flatter meaning easier sweating of joints. The cost is reasonable and the solder is readily available in stores and online for purchase
What is solder used for?from belmontmetals.com
1. 2. Overview. Nominal Composition. Solders such as this can be used to join copper and most copper alloys, lead, nickel alloys and steel. This general purpose solder has a wide melting range used for automotive, radiator, gutter repair and electrical applications.
What is soldering in plumbing?from belmontmetals.com
Soldering is performed in a wide range of industries including plumbing, electronics, heating/AC and manufacturing processes. Selecting the right solder is based on many factors including the solder’s melting temperature range, the properties of the soldering wire for the application, bonding capabilities, and the strength and hardness of the solder. Tin lead wire is a…
Is 60/40 solder stronger than 60/40?from stortz.com
While 60/40 is going to be a stronger bond, it is more difficult to work with due to a smaller “working temperature range” of the solder. This also means that while stronger, the bead will want to be slightly rounder. 60/40 solder is recommended for use with any lead coated metals.
Do you need to be a chemist to understand solder?from stortz.com
You need not be a chemist to understand the difference in these solders. You should however, understand that the solders will start to melt at a specific temperature and will fully become liquid at a different temperature.
Is tin solder harder to work with?from stortz.com
Tin soldering will require practice for the tradesman as the lead in the 50/50 solder reduces the surface tension and makes the solder more “flowable”. Tin (lead free) solder is more expensive and harder to work with, but may be gaining popularity for good reason.
What are the different types of solder?
There are three primary types of solder that are used frequently, namely: Acid core solder. Rosin core solder. Solid core solder. Solders are also available in different form factors and solders exist for specific applications or industries. This guide will provide a summary of the various types of solder, considering core style, alloy or material, ...
What is soldering a pipe?
Solder is a material that is used to bond or fuse objects together , such as a pipe to a pipe fitting or an electrical wire to a terminal or connector. The concept of soldering makes use of a metal alloy whose melting temperature is below that of the objects being joined. To solder, heat is applied by a torch or other means, such as to the joint between a copper pipe and a pipe elbow, and once sufficiently heated, solder can be placed at the joint and will melt and flow to seal the joint and provide a strong bond between the copper pipe and the pipe elbow.
What is rosin solder made of?
Rosin core solder is also fabricated with a hollow core inside the solder wire, but the flux used is a milder variety made of rosin, which is a solid form of resin derived from conifers such as pine. The flux residue associated with rosin core solder is non-corrosive and therefore is used for making solder connections in electrical applications ...
Why use flux solder?
The use of solder flux helps remove and prevent the formation of metal oxides that would impede the formation of a strong solder connection. These solders are intended to be used for steel or other metals but require that the flux residue be cleaned after the soldering operation is completed to avoid corrosion.
What is solder form factor?
Types of Solder by Form Factor. Although the most common form factor for solder is the solder wire delivered on spools, solder may also be purchased as brazing solder bars, solder pellets, solder rings, ribbon solder, solder rods, solder ingots, solder foil, and solder strips, depending on the application.
What is indium solder?
indium solder. spelter brass solder, which is pure zinc or a zinc alloy solder. platinum solder, gold solder, and silver solder, which are higher temperature solders used as jewelers’ solder. Most solders are alloys of one or more elements.
Why do we use solder in aircraft?
Aircraft solder needs to meet the needs of environmental conditions that involve vibration and thermal cycling. In radiator repair, automotive solder is used to repair leaks that develop in the coolant heat exchangers of cars and other motor vehicles.
What size solder should I use for surface mounted devices?
For work that involves surface mounted devices, I prefer 0.5 mm diameter solder. For leaded parts and connectors, I use 0.7 mm diameter solder. For most electronics work, solder in the range of 0.4 - 1.0 mm in diameter will work well. If you perform a lot of work on surface mounted devices, aim for the lower end of this range.
How long does solder paste last?
The result is that the solder won't flow correctly and it becomes very difficult to get a good solder joint. The shelf life of solder paste is about six months.
Why is lead free solder not the best?
Lead-free solder does not have the best reputation, in part due to technical issues with the soldering process. Most lead free solder alloys melt at a higher temperature (about 220-250 ºC) than tin/lead solder (about 180-190 ºC).
Why use flux in solder joints?
The purpose of flux is to clean the solder joint as the solder is applied, thereby allowing the solder to flow, resulting in a good and void-free solder joint. The flux also changes the surface tension, which increases the solder's adhesion the metal in the solder joint.
What solder is used for copper wire?
62/36/2 (Sn/Pb/Ag). 62/36/2 "silver" solder is gaining popularity in audio circles - probably because it's more expensive and contains silver. For soldering on copper wires and circuit boards, there is no evidence that "silver" solder should be superior to regular 60/40 or 63/37 solder. However, if you are soldering to silver wire, including some mica caps and silver-on-steel RF cables, you may want to use "silver" solder. This is because regular Sn/Pb solder will dissolve the silver over time. The silver in the 62/36/2 prevents this from happening.
What is the melting point of Sn100C?
It contains 0.7 % copper, 0.05 % nickel, ≤0.01 % germanium. The remaining approx. 99.25 % is tin. The nickel and germanium work in tandem to increase the surface tension of the molten solder, thereby minimizing solder bridging and improving hole-filling. AIM Sn100C® is an eutectic alloy with a melting point of 227 ºC. As this alloy is the only game in town for lead-free wire solder, it is rather expensive at over twice the cost of 63/37 leaded solder.
What is 63/37 solder?
63/37 (Sn/Pb) . 63/37 solder is the eutectic alloy, meaning that it goes directly from solid to liquid without plasticity. 63/37 solder melts at 183 ºC. This type of solder is slightly more expensive than 60/40 but the absence of a plastic region makes it nicer to work with and more beginner-friendly.
A Quick Comparison Table
Are you in a hurry? Then, take a quick glance at both solder wires. This will help you to have a primary idea about them.
Which Options Appears More Reliable?
Since 95/5 and 50/50 solder wires are two different products, their usability will vary. If you are looking for an affordable and want to use a solder wire only for general purposes, you can go for 50/50 solder wires.
What is 60/40 solder?
A 60/40 solder is an alloy of 60 % tin and 40 % lead measured by weight. This type of solder has a melting point of around 190 °C. Another commonly used tin / lead solder alloy is 63/37, which has a melting point of 183 °C. I have compiled a Soldering Temperature Chart that might help determine the correct temperature for the type of solder used.
What is flux core solder?
Flux core solder wire means that there is flux inside the core of the solder wire. The flux prevents oxidation occurring when the oxygen in the air reacts with the hot metal. The oxide forms a covering layer over the metal and prevents the solder from sticking to it. Flux is the chemical that actively removes this oxide and prevents the build up of new oxide. Solders typically use a rosin flux, which is a naturally occurring substance in pine trees extracted in the form of tree sap. It is a very interesting chemical because at room temperature it is inert, however, when heated, it becomes acidic which helps to prevent oxidation. Linked to a number of reported worldwide cases of Asthma, rosin can trigger an attack in people who suffer from this condition. Asthma is on the increase in the general population; hence, there has been a steady shift to rosin free flux. Omega uses a new form of flux ingredient that is not only environmentally friendly, but leaves a very clear residue on your PCB that will not require cleaning.
Why is flux important in the military?
For mission critical military applications, the use of flux is a concern because flux is acidic, which can affect reliability of a circuit over a long-term period. A missile in an underground complex is required to operate reliably for many decades.
What is rosin flux?
Solders typically use a rosin flux, which is a naturally occurring substance in pine trees extracted in the form of tree sap. It is a very interesting chemical because at room temperature it is inert, however, when heated, it becomes acidic which helps to prevent oxidation.
What is the melting temperature of 60/40 solder?
60/40 (60% tin - 40% lead.) For use on copper foil and lead came seams. Offers superior flow over 50/50. Melting temperature: 361° - 376°F. Most solders melt at a higher temperature than they freeze at, the difference between these figures is called the "pasty range" The pasty range of 60/40 solder is smaller than that of 50/50, giving the user a smoother bead.
What is Amerway Ruby Lead Free Solder?
Amerway Ruby Lead Free Solder is composed of 97% tin and 3% copper/silver. This greatly improves the flow characteristics, lowers the melting point and provides greater tensile strength. You will find this alloy to be the easiest flowing lead free solder available. The extra cost for this alloy is justified by the improved workability and increased efficiency.
What is Amerway Emerald solder made of?
Amerway Emerald Lead Free Solder is composed of 97% tin and 3% copper. Like many lead free alloys, 97/3 has a higher melting point (445°F) and will require use of a hotter iron (or a hotter setting on your iron control than you would with 60/40 solder). It flows similar to 50/50solder and does a good job of spanning gaps in your work. Recommended for jewelry or any project that gets handled a lot.
Can you send 50/50 solder to Pennsylvania?
Note: 50/50 Solder cannot be sent to Pennsylvania due to that state's EPA regulations. 63/37 (63% tin - 37% lead.) 63/37 is "eutectic"; it melts and freezes at the same temperature (361.4°F). The instant freeze properties can reduce the chance of lumpy solder beads.
When you get up to 70g, are you erring on the heavier side?
When you get up toward 70g and above, you are erring on the heavier side.
What Other Shaft Weights Are There And Who Should Use Them?
There are some specialist shafts on the market and one which is currently taking the world of golf by storm.
How Does Swing Speed Effect Your Driver Shaft Weight Choice?
The easiest way to think about it is that, in general, the faster you swing it, the heavier the shaft you should use.
How Can I Measure My Swing Speed?
The best way to do it is to get onto a launch monitor, these aren’t available to everyone though.
What is the lightest shaft?
50 gram shafts are among the lightest you will see on the market. They tend to be favoured by golfers who struggle to generate clubhead speed.
Why is a heavier shaft better for golf?
Heavier shafts can feel stiffer which can be a pro for golfers with a high swing speed. This extra weight can also help control that speed.
Does a heavier shaft help with swing control?
This may not be the case, entirely, but the extra weight can help with control during faster swings. Stronger golfer may benefit from a heavier shaft.

Types of Solder by CORE Style
- Acid core solderconsists of solder that is fabricated into a wire form but with a hollow core that is filled with an acid-based flux, which is a stronger, more aggressive form of cleaning flux. The use of solder flux helps remove and prevent the formation of metal oxides that would impede the formation of a strong solder connection. These solders a...
Types of Solder by Alloy Or Material
- There are a variety of alloys or materials used to manufacture solders for different applications. Generally, the proportion of elements used in solder alloys will determine the solder’s melting temperature which then aligns to the possible applications for that solder. One primary distinction is whether the solder contains lead as an element. Lead, while valued in soldering because of it…
Types of Solder by Form Factor
- Although the most common form factor for solder is the solder wire delivered on spools, solder may also be purchased as brazing solder bars, solder pellets, solder rings, ribbon solder, solder rods, solder ingots, solder foil, and solder strips, depending on the application. There are also precoated solder washers that are used to automate the soldering operations for through-hole c…
Types of Solder by Application
- While the applications that make the most extensive use of solder are the plumbing and electronics fields, there are other uses for the material as well. Aircraft solder needs to meet the needs of environmental conditions that involve vibration and thermal cycling. In radiator repair, automotive solder is used to repair leaks that develop in the coolant heat exchangers of cars an…
Summary
- This article presented a brief summary of the common types of solder used, summarized by core style, alloy/material, form factor, and application. For information on additional topics, consult our other guides or visit the Thomas Supplier Discovery Platformto locate potential sources of supply or view details on specific products.