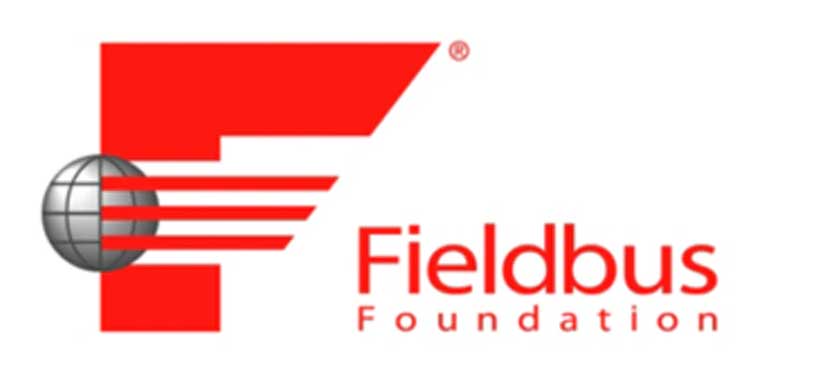
Modbus defines as a protocol of serial communications produced by Medicon. Fieldbus is a system of industrial network for real-time circulated control. … It is a method to link instruments in a plant of manufacturing.
What is Modbus?
Modbus is a granddaddy of industrial communication protocols. Modbus is Modicon plus fieldbus. Modbus, a serial communication protocol developed by Modicon in 1979. It is developed by Modicon for PLC in industrial applications, now it an open protocol. It is used over serial and Ethernet cable. It is easy to implement and also easy to use.
What is the difference between Modbus and Profibus?
As with the Modbus, there are a number of variants associated with Profibus. PROFISAFE. Profibus ( Process Fieldbus) is one of the standards for field bus communication in automation technology. PROFIBUS is also a Master/Slave protocol. But with additional token ring protocol to allow multiple masters as shown in the figure below.
What is the difference between BACnet and Modbus?
Building Automation Controls Network (BACnet): BACnet is a network protocol specifically used for multiple devices to communicate across building automation systems by system users and building system manufacturers. Modbus: Modbus is a network protocol best used for industrial automation systems specifically for connecting electronic equipment.
What is the difference between Modbus and LonWorks?
Modbus: Modbus is a network protocol best used for industrial automation systems specifically for connecting electronic equipment. Although Modbus is best for industrial applications, its simplicity allows it to be a useful tool for building automation as well. LonWorks: LonWorks is a communication network protocol useful...
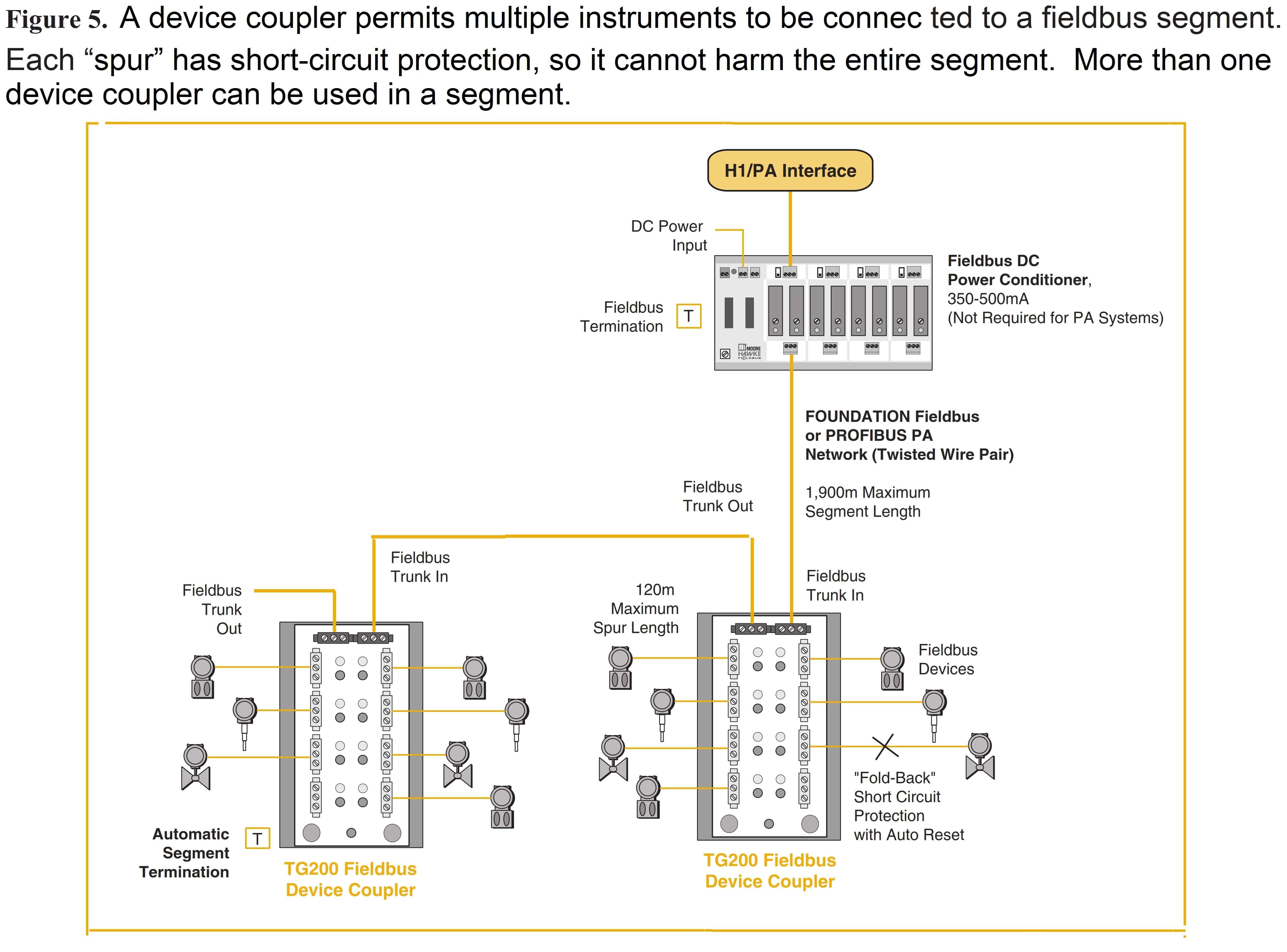
Is Modbus the same as fieldbus?
Modbus is often classified as a fieldbus protocol but with its various enhancements, particularly Modbus TCP, it has an even wider range of communication applications. One of the reasons for its proliferation is that Modbus is simple and hardy.
What is the difference between Modbus fieldbus and PROFIBUS?
PROFIBUS can operate on multiple Master devices per network. PROFIBUS only operates on RS 485 which supports 32 nodes and unlike MODBUS each node has the capability of being a master or a slave. The construction of PROFIBUS protocol ties it to only RS 485 which limits its usage. PROFIBUS can not operate on Ethernet.
What are the two types of fieldbus?
Foundation Fieldbus H1 and PROFIBUS-PA are the two fieldbus technologies used in process control. In this two-way communication, it is possible to read data from the smart sensor and also write data into it.
What is the purpose of a fieldbus?
A fieldbus is a serial bus system used in machines and systems to connect sensors and actuators (motors) to each other and to one or multiple masters (industrial PCs, PLCs). Fieldbuses make it possible to exchange data between different system components over long distances and under high external load.
What are the different types of fieldbus?
The different types of field bus are generally not compatible with each other. Network and field bus technologies types include brands such as: EtherNet/IP; DeviceNet; ControlNet; CompoNet; EtherCAT; PROFIBUS; PROFINET; Ethernet POWERLINK; CANopen; Interbus; CC-Link; Modbus TPC; AS-Interface; and IO-Link.
What is difference between Modbus and 4 20ma?
Wiring 485 modbus devices is nothing more than 2 wires (same as 4-20ma). Difference is that units can be daisy chained. This means that one can wire to node 1, and Node 1 can be connected to node 2. This does not require individual pair of wires for each node.
How many wires are in a fieldbus?
Fieldbus also uses two wires to carry power to the devices. A number of devices share the same Fieldbus wires. Fieldbus devices vary the voltage on the two wires to send signals.
Is fieldbus analog or digital?
Fieldbus is an all-digital, serial, two-way communications system that interconnects measurement and control equipment such as sensors, actuators and controllers.
What are the disadvantages of fieldbus?
Foundation Fieldbus is not utilized for applications requiring extremely fast control system response (200mS or below), such as Anti-Surge control, or for applications requiring high signal bandwidth, such as Machine Condition Monitoring systems.
What is a fieldbus signal?
Fieldbus is a bidirectional communication protocol that provides real-time, closed-loop control between intelligent field instruments and host systems. A host can be any software application: from a technician's handheld device or laptop, to a plant's process control, asset management, or safety system.
Is PROFIBUS same as fieldbus?
The short answer is: although both “buses” are very similar, they are not the same! Here is what's different: PROFIBUS is the overall name for a process fieldbus solution that includes the application and industry-specific PROFIBUS DP, PROFIBUS PA, PROFINET, and PROFIsafe.
Is fieldbus a PROFIBUS?
PROFIBUS (Process Field Bus) is a fieldbus which is being used for high speed cyclic data communication in the world of automation. PROFIBUS has two different applications: Factory automation. Process automation.
Is PROFIBUS and Modbus the same?
Profibus is also a master-slave type protocol like Modbus but with an additional token ring protocol to allow for multiple masters. Also, unlike Modbus, all devices go through a startup sequence during which they “join” the network. Each slave maintains a failsafe timer.
What is difference between RS485 and PROFIBUS?
Difference between Profibus and RS485 Profibus is a very flexible and reliable communication technology where issues can be caused by small and simple errors. On the other hand, RS485 is a more balanced technology that makes use of a two-wire transmission system.
What is the difference between PROFIBUS and CAN bus?
Re: can-bus vs proffi-bus Profibus DP is a sensor level network similar to CAN, DeviceNet or ASi. Profibus PA is a higher level network more like ControlNet and connects instrumentation like flow meters and such. Then there is Profinet which is Ethernet based like Modbus TCP or Ethernet/IP.
What are the different types of Modbus?
There are two types of Modbus serial protocols, RS-232 and RS-485. Modbus RS-232 allows concurrent, full-duplex flow of data. Modbus RS-485 is half-duplex, and indicates values using differences in voltage. Modbus messages can also be sent over Ethernet or TCP/IP.
How does Modbus work?
As already noted, Modbus is a simple master-slave protocol. The master has full control of communication on the bus, whereas a slave will only respond when spoken to. The master will record outputs and read in inputs from each of its slaves, during every cycle, as shown in Figure 2.
What physical layer does Modbus use?
Modbus ASCII and RTU both typically use either the RS-232 or RS-485 physical layer, but can also use other physical layers such as phone lines or wireless. Recommended Standards (RS) 232 and 485 were established physical layers when Modbus was first developed. RS-232 is for point-to-point, while RS-485 is for multi-drop applications. In both cases, Modbus did not add any new requirements to these physical layers. This worked, but it has caused a few problems in the case of RS-485. The problem is that the physical layer has a number of variations: 2-wire, 4-wire, use of common and variations in drivers and grounding methods. Anyone who has worked with Modbus on RS-485 from multiple vendors will already know how to manage all the variations when connecting two types in a point-to-point configuration. The difficulty comes when the site is multi-vendor and several variations have to be combined on one cable. There are a number of standards for both phone lines and for wireless. Modbus has excelled in these applications because of the small number of timing constraints in the protocol. Phone lines as well as wireless modems introduce delays in messages. Sometimes these delays are non-linear throughout the message, which can cause real problems for many protocols. However, Modbus either does not have a problem with this, or it can be adapted so that it will work in these applications.
What is the difference between RTU and ASCII?
The only difference is in the encoding of the data. ASCII encodes the message in ASCII characters, while RTU uses bytes, thus increasing the protocol’s throughput. In general, RTU is more popular, particularly in new installations.
What is Modbus protocol?
Modbus is the “granddaddy” of industrial communication protocols. It was originally designed in the mid-1970s by Modicon as a way to link intelligent devices with PLCs using a simple master/slave concept. “Simple” is a key descriptor for Modbus – and also its biggest strength. It is easy to implement and easy to use.
How long is a Profibus specification?
In comparison, Profibus’ specification document is thousands of pages long. The term “Modbus” typically refers to one of three related protocols: Modbus ASCII, Modbus RTU, or Modbus TCP/IP: 1. Modbus ASCII was the first Modbus and is a serial protocol, typically running on either the RS-232 or RS-485 physical layer.
What is a Profibus?
Profibus was designed to automate an entire plant, regardless of its size or whether the plant is factory automation (com posed of discrete input/output) or process automation (made up of analog input/output). It also does not matter if all the sections are local or remote: Profibus can handle it all well.
What is the profile standard of a Profibus?
For instrumentation, there is a part of the Profibus standard called the profile standard, which is a standardization of an instrument from the point of view of the bus.
What is fieldbus in automation?
Fieldbus is a digital two-way multidrop communication link between intelligent field devices. It is a local area network dedicated to industrial automation. It replaces centralized control networks with distributed control networks and links the isolated field devices such as smart sensors/ transducers/actuators/controllers.
What are the different types of fieldbuses?
Different types of fieldbuses include: Foundation Fieldbus, PROFIBUS, DeviceNet, ControlNet, InterBus, HART, AS-i, MODBUS, CAN Bus, Ethernet, LonWorks, and WorldFIP.
Why can't fieldbus and profibus communicate?
Devices embracing these two technologies cannot communicate with each other because of protocol mismatch and thus seamless interoperability is yet to be achieved.
What would happen if the latter option was given rise to an integrability problem?
The latter option would give rise to an integrability problem and lead to isolated islands of automation and consequent inter operability difficulty with devices from different manufacturers.
What is a foundation fieldbus?
Foundation Fieldbus H1 and PROFIBUS-PA are the two fieldbus technologies used in process control. In this two-way communication, it is possible to read data from the smart sensor and also write data into it. The multidrop communication facility in fieldbus results in enormous cable savings and resultant cost reduction.
How many devices are in a fieldbus?
Compared with this, a fieldbus system has two wires running for many devices that belong to the same segment. A segment may consist of 32 devices.
What were the problems with fieldbus?
First, a particular vendor could not provide all the parts/components needed for a plant and that a particular manufacturer cannot make all the devices better than others.
What is a modbus?
The profibus and Modbus are enhancement to previous interface standards. These protocols defines real time communication between masters of bus, distributed sensors and actors. They are used for low transmission volumes and low latency applications. Note that Modbus is a protocol which defines frame structure for the messages to be transported ...
What is a robust protocol?
It is very robust protocol which can be used to automate entire plants. It is used where there are more points and multiple vendor equipments are to be automated. It is very simple protocol which can be used to interface single controller in point-to-point mode of configuration. It is used for small plant automation.
How does a MODBUS work?
The devices which use MODBUS would communicate in a master/slave arrangement. In this type of communication, the master would communicate with one or multiple slaves. Mostly the master would be a PLC, PC, DCS, PAC, or RTU. The slaves are mostly the field devices, so in this configuration, the master would request to read or write a value. These values could be analog or digital, the slaves would respond to this request by giving the data to the master or by taking the action which is required. In case the slaves or Fieldbus wasn’t able to perform the requested action then the slave would create an error message and it would be transmitted to the master.
Why Modbus is combined with Ethernet?
The TCP/IP suite of the Ethernet act as a foundation for accessing the world wide web. So many devices support ethernet and it provides fast communication and because of this, it is used in many industrial applications.
What are the major types of MODBUS which is used for industrial communication?
This is a type of MODBUS communication protocol that uses ASCII characters to do serial communication. This type of communication protocol is the slowest but it can be used when telephone modem or radio links are used. The major advantage of this protocol is that it utilizes characters to delimit the message. So due to this if there is any delay in the transmitting medium then there won’t be any misconceiving of the message by the receiving device.
What are the MODBUS TCP/IP devices and MODBUS RTU devices?
It is designed to be used with a serial device that supports the RS 232, RS 485, and RS 422 protocols. It is used with the PLC and SCADA
What is RS 232, RS 422, and RS 485 and what is their difference?
These are the standards that are used to do serial communications. All these standards would define the wiring, signal levels, transmission baud rates, and parity checking.
Which is better, Modbus or LonWorks?
Although Modbus is best for industrial applications, its simplicity allows it to be a useful tool for building automation as well. LonWorks: LonWorks is a communication network protocol useful for building automation applications designed on a low bandwidth, for networking devices through power lines, fiber optics, and other media.
What is the purpose of transmissions must be contiguous?
Transmissions must be contiguous which limits the types of remote communications devices to those that can buffer data to avoid gaps in the transmission. Great amount of configuration and programming required. Protocol is not common in the SIMATIC family. Outdated.
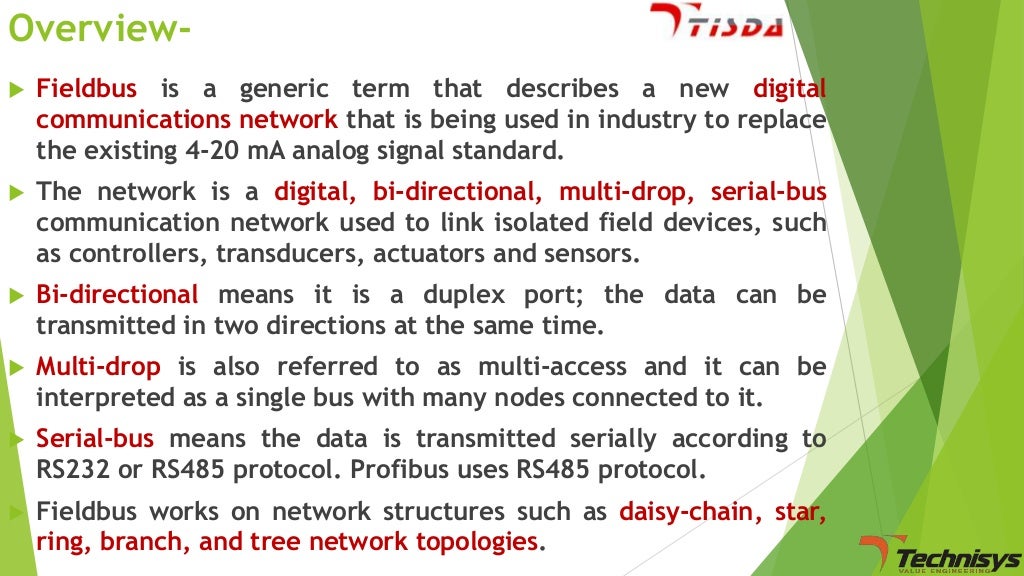