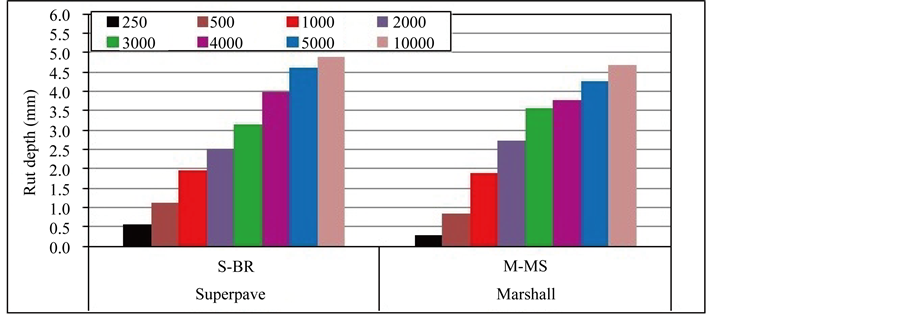
What is the difference between Superpave and Marshall? Marshall mix design primarily address the determination of asphalt binder content, while Superpave addresses all element of mix design. The Marshall design/construction method requires in most cases compaction 95% or greater of the maximum lab value.
What is the difference between Superpave and Marshall mix design?
Marshall mix design primarily address the determination of asphalt binder content, while Superpave addresses all element of mix design. The Marshall design/construction method requires in most cases compaction 95% or greater of the maximum lab value.
Is the Marshall method still relevant for asphalt mix design?
Consequently there has been a growing feeling among asphalt technologists that the Marshall method has outlived its usefulness for modern asphalt mixture design. Marshall mix design primarily address the determination of asphalt binder content, while Superpave addresses all element of mix design.
What is the Superpave System?
The Superpave system ties asphalt binder and aggregate selection into the mix design process and consider traffic and climate as well. The compaction devices from the Hveem and Marshall procedures have been replaced by a gyratory compactor and the compaction effort in mix design is tied to expected traffic.
What is Superpave mix design method?
Superpave Mix Method. One of the principal results from the Strategic Highway Research Program (SHRP) was the Superpave (Superior Performing Asphalt Pavements) mix design method. The Superpave mix design method was designed to replace the Hveem and Marshall methods.

Is Superpave better than Marshall?
The Superpave mix showed better results of the studied properties compared to Marshall mix. This result proved the superiority of Superpave mixes over Marshall mixes. Therefore, adopting the Superpave design procedure in Sudan might help in enhancing the performance of the asphalt surface roads.
What is the Superpave method?
The Superpave system ties asphalt binder and aggregate selection into the mix design process, and considers traffic and climate as well. The compaction devices from the Hveem and Marshall procedures have been replaced by a gyratory compactor and the compaction effort in mix design is tied to expected traffic.
What is Marshall in asphalt?
The Marshall method is a holistic approach to asphalt pavement mix design. Through a series of steps, it is able to establish the ideal asphalt content for a mix that will provide maximum strength and stability for its load. Through Marshall testing, engineers are able to: Select mineral aggregate and binder materials.
What does a Superpave Gyratory Compactor do?
The Superpave mix design procedure features the Superpave gyratory compactor (SGC) for compacting specimens of hot mix asphalt.
What are Superpave tests?
The Superpave (SUperior PERforming Asphalt PAVEments) system was developed to give highway engineers and contractors the tools they need to design asphalt pavements that will perform better under extremes of temperature and heavy traffic loads.
What is Marshall mix design?
The Marshall Mix Design method was originally developed by Bruce Marshall of the Mississippi Highway Department in 1939. The main idea of the Marshall Mix Design method involves the selection of the asphalt binder content with a suitable density which satisfies minimum stability and range of flow values.
What is the Marshall test used for?
The Marshall Test is a popular and proven method to measure the load and flow rate of asphalt specimens, beginning with compaction into molds using manual or automated Marshall Compactors, and conditioned in a Water Bath at the specified temperature.
Why Marshall test is done?
The Marshall test method is widely used for the design and control of asphaltic concrete and hot rolled asphalt materials, it cannot be applied to open textured materials such as bitumen macadam. Materials containing aggregate sizes larger than 20 mm, are liable to give erratic results.
Are there different grades of asphalt?
The Asphalt Institute specifies four penetration grades: 60-70, 85-100, 120-150, and 200-300. The 60-70 grade is usually used only in pavements where traffic is very heavy such as principle city streets and very heavily trafficked rural highways.
What are the benefits of gyratory compaction?
Results indicate that samples compacted with the gyratory compactor show higher precision in the strength test than the impact hammer. Data show that gyratory compaction results in different engineering properties than those obtained from the impact hammer compaction.
What does a gyratory compactor simulate?
The specimens produced with the gyratory compactor simulated the density, aggregate orientation and structural characteristics of the mixture in the pavement.
What is PG in pavement?
The Performance Grade (PG) system is the method of categorizing an asphalt cement binder. used in asphalt pavement relative to its rated performance at different temperatures. It was. originally developed during the Strategic Highway Research Program (SHRP) in the early.
What are the sequence of steps for Superpave mix design?
The Superpave mix design consists of seven stages: (i) aggregate selection, (ii) asphalt binder selection, (iii) sample preparation, including compaction, (iv) performance tests, (v) density and voids calculations, (vi) optimum asphalt binder content selection, and (vii) moisture susceptibility evaluation.
How is HMA made?
HMA is manufactured in a central mixing facility (typically called a hot mix plant) and consists of high quality aggregate and asphalt cement. The two are heated and mixed while hot to completely coat the aggregate with asphalt cement.
What do the basic tests on asphalt materials measure?
Many tests are used to evaluate the properties of mix designs such as voids (air content), asphalt cement content, gradation, voids in mineral aggregate (VMA), stiffness, and others to insure the quality of the mix design. There are three major methods for determining asphalt content: solvent extraction.
How do you find the maximum theoretical specific gravity?
Theoretical maximum specific gravity is determined by taking a sample of loose HMA (i.e., not compacted), weighing it and then determining its volume by calculating the volume of water it displaces (Figure 1). Theoretical maximum specific gravity is then the sample weight divided by its volume.
How are superpave binders selected?
Asphalt Binder Selection: Superpave PG asphalt binders are selected based on the expected pavement temperature extremes in the area of their intended use. The extremes can be calculated using software (such as LTPPBind).
What is superpave asphalt?
Superpave was created to make the best use of asphalt paving technology and to present a system that would optimize asphalt mixture resistance to permanent deformation, fatigue cracking and low temperature cracking.
What is the difference between Marshall and Superpave?
Marshall mix design primarily address the determination of asphalt binder content, while Superpave addresses all element of mix design.
How does SGC provide information about the compactability of a mixture?
The SGC can provide information about the compactability of the particular mixture by capturing data during compaction.
What would happen if HMA was compacted?
It would mean the air voids had been completely removed from the material during construction. This would result in a significantly reduced life of the HMA since the Engineers accounted for 6% air in the HMA mixture during design.
How is aggregate selected?
First, restrictions on aggregate gradation are specified by using gradation specifications. Second, there are physical property requirements on aggregate angularity, flat and elongated particles, and clay content. Third, aggregate criteria, which the Asphalt Institute calls ‘source properties’ (because they are considered to be source specific), such as durability and soundness are specified .
What percentage of air void is asphalt?
Select the optimum asphalt binder content. The asphalt binder content corresponding to 4 percent air void is selected as long as this binder content passes stability and flow requirements.
What is Superpave?
The term "Superpave" is an acronym for Superior Performing Asphalt Pavements, which evolved from partnerships created among Federal Highway Administration (FHWA), American Association of State Highway and Transportation Officials (AASHTO), TRB, and others in the SHRP community.
What is superpave gyratory compactor?
Instead of the impact of weighted hammer blows, the Superpave gyratory compactor (SGC) uses a hydraulically powered kneading system with an action much closer to actual field densification of the mix. The applied force is constant, the number of gyrations can be controlled, and the device produces feedback on the compactibility of the asphalt material. Optimum densities developed with the SGC often require less asphalt binder than Marshall methods.
How many cycles are in a trial mix compactor?
Each trial mix sample is compacted in the Superpave gyratory compactor using three different gyration cycles based on 20-year traffic loading estimates in millions of ESALs from AASHTO R 35:
What is superpave pavement?
Rather than a specific process or procedure, Superpave is a performance-based specification for asphalt binder and volumetric mixture design. The idea was to allow asphalt pavement designs that could handle the unique weather and traffic conditions of a given site in any geographic area of the U.S. The system consisted of three components:
What percentage of asphalt is aggregate?
Aggregates make up about 95% of an asphalt mixture, and their function in the overall performance of a pavement is critical. Superpave has unique criteria for aggregate acceptability that are detailed in section 6 of AASHTO M 323. Because aggregates from a single source rarely meet all the requirements, materials from different stockpiles are frequently blended to produce an acceptable mix design.
What is a PG 64-16?
A PG 64-16 binder is for use at a project site where the average seven-day maximum pavement temperature is 64°C, and the expected minimum pavement temperature is -16°C.
What is the first step in the design process?
The first step in the design process is a collection of the environmental and usage information for the project. In other words, maximum/minimum temperatures for both air and pavement, along with current and anticipated traffic types and loads. Testing and selection criteria for PG binder, combined aggregate requirements, and mixture design are detailed in AASHTO M 323.
What is the purpose of the SCR?
The aim of the present thesis was the optimization of bituminous sub-ballast in railways infrastructure under sustainability criteria through the reuse of SCR (scrap tire rubber), as well as the reduction of the energy consumption. So, for that and other reasons, the purpose was to develop new mixtures environmentally competitive and with an adequate mechanical behavior, in replacement of conventional materials. In that case, the primary objective has been achieved focused on the capacity of using ground rubber from discarded tires as elastic aggregate substituted in volumetric proportion inside a bituminous mixture by dry-process in the sub-ballast layer. Mechanical performance of CRM mixtures survey has enhanced the benefits of the track, obtaining a higher capacity of dissipated energy from train passage. At first, the mechanical behavior of bituminous sub-ballast was studied, to establish a reference performance. Also, to assess the impact of the sub-ballast layer in the global behavior of the railway track, discarded tire rubber, one of the generic types of asphalt additives, has been promoted and used to reduce the problems of damage to the rail sub-ballast during the life cycle. In this context, the use of HMA to replace granular sub-ballast is a solution that has great potential for bearing capacity and impermeability. Simultaneously the thickness of the layer is reduced to 12-15 cm, compared to the 22-25 cm used in the conventional granular design. In general, it can be stated that the evaluation of the behavior of hot asphalt (HMA) with recycled rubber as an additive has been optimal due to the laboratory performance of conventional mixtures (standard hot mix asphalt) and mixtures modified with rubber added by the dry process (DRY). This work aimed to fundamentally identify the advantages of the addition of crumb rubber (susceptibility to temperature, elastic behavior, binder viscosity reaction, the optimal amount of rubber substituted, and a satisfactory protocol of mix-design by dry technology). The results obtained in the laboratory with the design of different bituminous mixtures (HMA_DRY) and the use of varying compaction techniques (Volumetric mix-design, Marshall, and Asphalt Slab Roller Compactor), allowed considering their proper use for the conventional sub-ballast. The optimization of the conventional bituminous mixture, HMA, using the gyratory compactor (SGC), Marshall hammer (indirect tensile tests and resistance to water sensitivity), and the subsequent adaptation to mixtures with the roller compactor (ASRC), simulating the real conditions on site, have demonstrated that the use of asphalt inside the sub-ballast is efficient. Subsequently, three types of rubberized mixtures have been studied and mechanically characterized to fatigue-cracking (dissipated energy approach), and determination of the elastic-dynamic modulus by various techniques analyzed in the methodology chapter. Finally, suitable values are obtained regarding the internal composition of the material and its mechanical performance, so that the mixtures by the dry process allow their use by favoring the damping of vibrations and noise generated in the railway section. For this reason, rubberized asphalt presents a high potential for their application as bituminous sub-ballast in railway tracks.
How long does asphalt last in Jordan?
Highways in Jordan are typically designed and constructed to last at least 20 years. However, it is not uncommon to see flushing, rutting, and cracking in asphalt pavements well before that period, especially in areas exposed to harsh environmental conditions and heavy traffic loadings. The Superpave (Superior Performance Pavements) system was developed to give highway engineers the tools they need to design asphalt pavements that will perform better under temperature extremes and heavy traffic loads. This research was established to study the possibility of adopting the Superpave mix design procedure in Jordan using prevailing traffic and environmental conditions. In this study, a map showing the different temperature zones available in Jordan was developed. A comparison study was carried out utilizing local materials to design asphalt mixes using both Marshall and Superpave mix design procedures. It was found that the Superpave mix design procedure recommended, for the local environmental and loading conditions, lower asphalt content than that predicted by Marshall mix design procedure. In addition, it was found that using the presently recommended local aggregate gradation for heavy traffic in the Superpave design method gave dust proportion higher than the maximum specified limit by the Superpave procedure. High dust proportion will usually lead to brittleness of the mixes. Therefore, shifting to the Superpave design procedure might help in solving the bleeding problem and some of the distresses common in the local asphalt structures.
How does air void affect asphalt pavement?
Air voids in an asphalt concrete pavement highly influence its performance. Careful consideration of void requirements in compacted bituminous mixtures is more important than stability consideration, since the latter is always higher than necessary. Lack of attention to void requirements may be a direct cause of instability of asphalt concrete pavements. The present work studied the influence of aggregate type and its gradation on the voids in mineral aggregate and air voids of asphalt concrete paving mixtures as compacted according to the Marshall method. Three types of aggregates and five different gradations were employed. Aggregate gradation may be used to control the void requirements in a specific asphalt concrete mixture, influencing and/or affecting other important engineering properties such as water permeability of that specific mixture. On the other hand, aggregate type can provide the necessary voids requirements for an aggregate-asphalt mixture without sacrificing other important engineering properties. Two of the aggregates easily satisfied the void requirements. The third aggregate could not satisfy the same void requirements unless a porous gradation was used. Porous mixtures have more air voids, resulting in an increased permeability to water. This increase in permeability is not the same for different aggregate gradations. The coarser the mix, the higher the rate of increase in the water permeability for the same type of aggregate.
What is WMA asphalt?
Warm mix asphalt (WMA) from different warm mix technologies (WMT’s) can be prepared and compacted at reduced temperatures in comparison to hot mix asphalt (HMA). WMT’s offers unique environmental and economic benefits by reducing the energy consumption, fuel cost, and hauling distance. Numerous laboratory and field investigations have been done to assess the mechanical performance of WMA. The main objective of this state of the art review is to assimilate information on various aspects of WMA mixtures. Data on available WMT’s, mix design of WMA, workability requirements, and performance obtained in the laboratory and field are extensively reviewed and summarized. Effect of various WMT’s on the mechanical performance of asphalt mixtures prepared using polymer modified binder, crumb rubber modified binder, and reclaimed asphalt pavement material is also presented. Additionally, previous works on life cycle cost assessment, greenhouse gas emissions, and economic benefits related to various WMT’s are surveyed.
What is the role of asphalt concrete in flexible pavements?
Abstract —The quality of asphalt concrete in flexible pavements plays a major role in the performance and durability of these pavements .
Which mix showed better results of the studied properties c ompared to Marshall m ix?
The Superpave mix showed better results of the studied properties c ompared to Marshall m ix. This result p roved the superiority of
What is specime deformation?
deformation that occurs when the specime n fails. If a sample
What is AASHTO TP4?
AASHTO TP4: Preparing and Determining the Density of Hot-Mix Asphalt (HMA) Specimens by Means of the Superpave Gyratory Compactor
What is superpave gyratory compactor?
The Superpave gyratory compactor establishes three different gyration numbers: Ninitial. The number of gyrations used as a measure of mixture compactability during construction. Mixes that compact too quickly (air voids at N initial are too low) may be tender during construction and unstable when subjected to traffic.
What is the Superpave Mix Design Method?
The Superpave mix design method was designed to replace the Hveem and Marshall methods. The volumetric analysis common to the Hveem and Marshall methods provides the basis for the Superpave mix design method. The Superpave system ties asphalt binder and aggregate selection into the mix design process, and considers traffic and climate as well. The compaction devices from the Hveem and Marshall procedures have been replaced by a gyratory compactor and the compaction effort in mix design is tied to expected traffic.
What is superpave mix?
Superpave mix design specifies aggregate gradation control points, through which aggregate gradations must pass. These control points are very general and are a starting point for a job mix formula.
What is the optimum asphalt binder content?
The optimum asphalt binder content is selected as that asphalt binder content that results in 4 percent air voids at N design . This asphalt content then must meet several other requirements:
What is superpave aggregate?
Second, it places “consensus requirements” on coarse and fine aggregate angularity, flat and elongated particles, and clay content. Other aggregate criteria, which the Asphalt Institute (2001 [2]) calls “source properties” (because they are considered to be source specific) such as L.A. abrasion, soundness and water absorption are used in Superpave but since they were not modified by Superpave they are not discussed here.
How many aggregate stockpiles are there in a superpave mix?
It is quite common to find a Superpave mix design that uses 3 or 4 different aggregate stockpiles (Figure 1).
