
Understanding the Importance of Sheet Metal Fabrication in Various Industries!
- · Sheet metals are known to provide a wide range of benefits to every other industry today.
- · Since this material has a low weight to thickness ratio, it is quite easy to transport and work with.
- · Sheet metal is also known for its durability and unmatched strength, making it the perfect choice for different applications.
What is the job description of a sheet metal worker?
- Measure, cut and bend various types of sheet metal into appropriate sizes and shapes
- Connect ducts and joints by welding, bolting, riveting or soldering
- Read and analyze blueprints and operate computerized fabricating equipment such as shears, saws and presses
- Drill, anchor and install sheet metal parts according to product specifications
What are some common uses for sheet metal?
- Metal mugs
- Water pots
- Corrugated steel sheets for house and factory roofings
- Shutters
- Car casing
- Actually, casings of any vehicle possible fron rickshaw to aircrafts.
- Laptop casings
- Metallic boxes
- Chocolate tins
- Aluminiun cooking pots
What products are made of sheet metal?
Sheet metal is used in various products like machinery, building roofs, car bodies, airplanes and much more. Sheet Matel Material Used in the Process The common materials used in manufacturing sheet metal are aluminum and stainless steel .
What does a sheet metal fabrication worker do?
What does sheet metal fabrication workers do specifically?
- Sheet metal fabrication workers are often used in construction sites, metal workshops or manufacturing plants. ...
- In order to make sheet metal, fabrication workers must first create or study a given plan, blueprint and specifications. ...
- At construction sites, sheet metal fabrication workers install products produced in factories or sheet metal workshops. ...
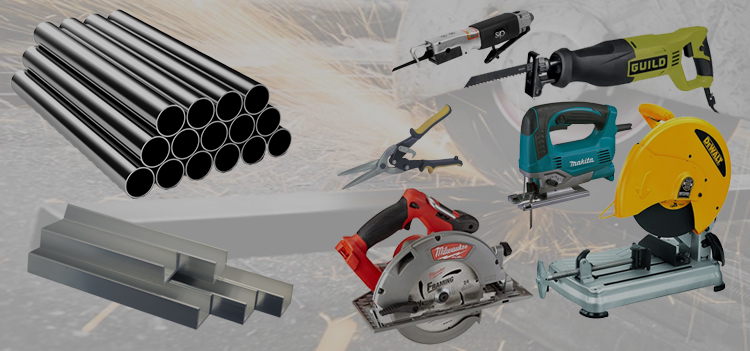
What is importance of sheet metal engineering?
Sheet metal Applications It is used to build bodies for aeroplanes, cars, boats, and ships. Iron sheet metals are also used in the energy industry in the making of transformers and other electric machines. This is due to the sheet's magnetic permeability, also referred to as laminated steel cores.
What do you mean by sheet metal work?
Basically, the word sheet metal working refers to the manufacture of products, components and parts made of metal. In addition to welding, cutting and bending, the processes of sheet metal processing also include punching, forming, rolling and joining.
What are the advantages and disadvantages of sheet metal working?
The pros are its high production rates. The cons are its high tooling and equipment costs. Stamping process actually includes a variety of operations, such as punching, blanking, embossing, bending, flanging, and coining. Drawing can be used to produce simple or complex shapes.
What are the benefits of a metal?
Heat resistance: Metals typically have a higher melting-point and are less likely to degrade under elevated temperatures. Improved strength: Metal grades tend to be stronger, harder, and more durable than their plastic counterparts.
What is sheet metal used for in construction?
Sheet metals can be used for primary structural elements, lighting, wall finishes, millwork assemblies and to create functional staircases.
What is called sheet metal?
The term “sheet metal” refers to any metal that can be formed into flat pieces of varying thicknesses. Thick metals are called plate. Metals used in the sheet metal industry include cold rolled steel, mild steel, stainless steel, tin, nickel, titanium, aluminum, brass, and copper.
What are commonly used material in sheet metal work?
Steel. The most common type of metal used for part fabrication is steel, which is an alloy of iron and carbon and may have some other elements like limestone or coal as well. Steel is popular because it's cheap and easy to weld, although it's less ductile and harder to cut than some other metals.
What are the advantages and disadvantages of using metals in construction?
Advantages and Disadvantages of metals commonly used in ManufacturingAdvantages: The most abundant metal in the Earth's crust, Aluminium is relatively soft, durable, lightweight, ductile and malleable metal. ... Disadvantages: It's not particularly strong and is expensive compared to steel of the same strength.More items...
What are the advantages of using steel?
Steel offers a number of significant advantages relative to other building materials, including:speed of construction.safety.value for money.robustness and ductility.prefabrication.reduced weight.architectural expression.configuration adaptability.More items...
What industries use sheet metal?
Some industries that are heavily reliant on sheet metal fabrication are the farming, railroad, aerospace, automobile, pharmaceutical, oil and gas, electronics, food service, heating and cooling, plumbing, medical, telecommunications, computer, military, storage, and construction industries, to name just a few.
What is the advantage and disadvantages?
As nouns, the difference between disadvantage and advantage is that disadvantage is a weakness or undesirable characteristic; a con while the advantage is any condition, circumstance, opportunity, or means, particularly favorable to success, or any desired end.
What are the advantages and disadvantages of steel?
Advantages & Disadvantages of Steel ConstructionReliability.Industrial Behavior.Lesser Construction Time / Greater Erection Speed.High Maintenance Costs And More Corrosion.Fireproofing Costs.Susceptibility To Buckling.Higher Initial Cost / Less Availability.Aesthetics.
What is sheet metal and its types?
There are many different metals that can be made into sheet metal, such as aluminium, brass, copper, steel, tin, nickel and titanium. For decorative uses, some important sheet metals include silver, gold, and platinum (platinum sheet metal is also utilized as a catalyst).
Who works with sheets of metal?
Sheet Metal Workers In construction, they use sheet metal to construct structures such as roofs, gutters and ducts used for heating and air conditioning. Sheet metal workers commonly learn their trade through a formal apprenticeship, which typically lasts between four and five years.
How many types of sheet metal are there?
There are six major types of sheet metal material, each with its own unique advantages: Alloy steel. Stainless steel. Carbon steel.
Is sheet metal hard work?
The job can be physically demanding – you may work at considerable heights and have to lift heavy materials and equipment. As with all careers in the construction industry, safety is the top priority. Sheet metal workers are trained to work safely and wear special equipment to protect against injury.
What does a sheet metal worker do?
Sheet metal workers can specialize in a single aspect of sheet metal work, like fabrication, maintenance or installation, but usually have knowledge and experience in all three. Those who work in factories, however, typically perform a single repetitive task, lacking the knowledge and skill to move on to more complex roles.
What skills do you need to work on metal sheeting?
Mechanical skills: Most metal sheet work involves working with various tools, such as saws, shears, pressers and lasers. Operating and maintaining this kind of equipment requires strong mechanical skills.
How do sheet metal workers make sure that the heating, ventilation and air conditioning units are working properly?
Testing and balancing sheet metal workers: They make sure that the heating, ventilation and air conditioning units are working properly by measuring their airflow and adjusting the metal sheets accordingly.
What is sheet metal maintenance?
Maintenance sheet metal workers: They repair previously installed heating, ventilation and air conditioning units by repairing various leaks and breaks, as well as removing any accumulated moisture and dust
What classes do you need to be a sheet metal worker?
Most sheet metal workers have a high school diploma or an equivalent. The most important classes are usually algebra and geometry, as well as vocational-educational courses like mechanical drawing, welding and blueprint reading.
What is sheet metal fabrication?
Fabrication sheet metal workers: They are also called precision sheet metal workers and they are the ones who actually make the metal sheets, in different shapes and sizes depending on their destination. Some metal sheet factories are completely computerized and the metal sheet workers operating there need to learn how to program the software that regulates the sheet metal production and cutting.
How much does a sheet metal worker make?
According to Indeed Salaries, the average yearly wage for a sheet metal worker in the U.S. is $64,027 per year. The Bureau of Labor Statistics mentions that there are currently 137,700 active sheet metal workers in the country, but the job outlook for the next decade only indicates a 1% job number increase, which is below the national average.
Why are metal sheets used in construction?
Since metal workers can easily modify and adjust their metalworks, metal sheets are seen as a perfect construction material that allows easy expansion on different structures which might not be possible with some other materials.
Why are metal sheets so durable?
Because of the ability to withstand high amounts of pressure, metal sheets are known for their durability. In addition to that, metal sheets are resistant to water, moisture, sun, and corrosion, making them perfect for a wide range of projects as well as environments.
How is sheet metal made?
To put it simply, sheet metal fabrication starts with a piece of raw sheet metal. This is shaped into the desired object through forming and deforming, although material removal could be used as well. There are a lot of metal sheets available who vary based on among other things the thickness. This depends on the specific metal used and can be very different. Aluminum can be up to 3/16 in. for example, which 14 gauge is possible for stainless steel. The sheet metal is transformed into the desired form by cutting, burning, and stretching it. To be able to do this one needs special metal fabrication tools. Multiple processes can be employed to get the exact shape that the client wants, but also to achieve the desired specifications.
What materials are used in sheet metal fabrication?
For sheet metal fabrication you can use a wide range of metals. Examples of the materials that can be used are stainless steel, aluminum, titanium, and much more. Press brakes will be used to shape the parts. Usually, these can accommodate pieces up to 10 feet long, weighing up to 125 tons.
Why is sheet metal fabrication so common?
This mostly is the case because this process is a cost-effective way to get any amount of desired shapes and sizes, while you will only need a short amount of time to produce the exact piece. It could be a small part of the semiconductor sector, but also a big part of a car. Whatever it is, sheet metal fabrication will meet the precise needs. On top of that, this method will create parts that are long-lasting and strong. Plus, they will certainly meet the standards.
What is the process of coating a layer of another metal over your metal sheet?
2. Plating . The process of coating a layer of another metal over your metal sheet in order to make it look more pleasing as well as making the metal sheet corrosion resistance is known as plating. 3. Polishing. Polishing the metal sheet is how you get rid of a the outer layer of the metal sheet.
Why powder coat metal?
In order to increase the durability and aesthetics of the metal sheet, powder coating is seen as a perfect choice as it creates a hard finish on the surface of the metal sheet.
What is sheet metal used for?
Sheet metal is used in a variety of industries namely car manufacturing, aircraft parts, tools, agriculture, mining, catering, shipping, medical, electronic parts, and construction to name a few.
Why is sheet metal used in construction?
Sheet metal is used in the construction industry because of the many benefits it offers, namely; Light – due to sheet metal being relatively lightweight it is easy to transport and deliver. Adaptable – sheet metal fabrication can handle both low and high-volume production.
What are the most important factors when choosing sheet metal fabrication services?
By asking the above questions, one should be able to get a better understanding of the level of competence and expertise offered which should make the buying decision easier. Specialization and experience in sheet metal fabrication are the most important factors when choosing sheet metal fabrication services.
Why is sheet metal fabrication important?
As technology evolves and constantly improves, new fabrication processes are identified and applied to offer merchants greater opportunities to design and make metal products or components. In the construction industry, sheet metal fabrication is especially vital.
What are the processes used to bend metal?
Different procedures, processes, and techniques are used to bend and shape metal, designed for a plethora of applications. Sheet metal fabrication processes can include but are not limited to water jet, laser cutting, plasma cutting, hydraulic brakes, magnetic brakes, stamping, punching, and welding. As technology evolves and constantly improves, ...
What is sheet metal fabrication?
Sheet metal fabrication exists to customize designs and manufacture specific components or materials required for a range of industries.
Why is it important to use reliable suppliers?
Using reliable and trusted suppliers in the construction industry is para mount to proper design, installation, safety, and regulation adherence. Sheet metal fabricators are no exception, their ethos and reliability in producing excellent products and solutions are crucial in construction circles. Fast turnaround times are the third most important factor after experience and customization to consider when choosing a supplier when selecting a supplier. Building a long-lasting and trusted relationship with a supplier who ticks the above boxes is paramount to delivering on excellent and successful projects in the future.
How much does a sheet metal worker make?
Salary. Sheet Metal Workers with little to no experience tend to make between $27780 and $35390 while the more experienced ones can earn over $64970 per year. One of the easiest ways to increase your salary as a Sheet Metal Worker is to move to a higher paying state like HI.
What degree do sheet metal workers have?
We asked other Sheet Metal Workers what degree they had when they got the job and most of them said they had a High School Diploma followed by less than a High School Diploma.
What is fastening joints?
Fasten seams or joints together with welds, bolts, cement, rivets, solder, caulks, metal drive clips, or bonds to assemble components into products or to repair sheet metal items.
What is sheet metal?
Sheet metal fabrication is metal that has been formed into thin and flat sheets which is then cut and bent into various shapes. Different metals, brass, steel, copper, tin, titanium, aluminium, etc., can be made into sheet metal. Platinum, gold, and silver are useful for decorative purposes among other uses. Sheet metal is used to construct numerous objects with varying thicknesses, from extremely thin sheets, also known as foil or leaf, to thicker sheets i.e. >6mm, also known as plate. The metal sheet thickness is referred to as gauge and generally ranges from 30 gauge to 8 gauge. The sheet metal gauge is inversely proportional to the metal thickness.
What is sheet metal fabrication?
In essence, sheet metal fabrication entails turning or processing sheet metal into functional parts by cutting, bending, or stretching into almost any shape. The processing of the metal sheets can create holes and 2D geometric cut-out shapes while deformation processes bend sheets into different angles or yield complex contours from stretching.
What are the different types of sheet metal fabrication?
Sheet metal fabrication techniques can be categorized into cutting, forming, and assembly .
Why are castings used in fabrication?
Castings are used to add visual interest to the fabrication and can speed the fabrication process.
What is the difference between shearing and cutting?
Shearing uses upper and lower blades to cut in straight lines, similarly to scissors. However, in the case of shearing, both blades do not move as with scissors; instead, one blade lowers while the other remains stationary. Its advantages include the clean cuts and smooth edges it creates, its ability to be used on a wide variety of gauges, the fact that it does not create chips in the metal, (hence the low waste), cost-effectiveness in mass production, and ability to be used at room temperature, which removes any need to preheat the sheet metal.
What is the process of forming metal?
Forming processes include bending, stamping, roll forming, stretching, and spinning.
Why is hot rolled steel not accurate?
However, hot rolled steel does not have accurate dimensions because the metal cools down and shrinks after rolling. This yields intermittent stress concentrations that can warp the material, and this changes the configuration of the steel.
The Automotive Industry
The bodies of many cars and other vehicles are constructed from sheet metal.
Airplanes
Airplanes large and small have their wings and fuselages covered in sheet metal.
A Building Material
Sheet metal can be used as a roofing material, to make flashing for roofs and to make rain gutters. Inside a building, duct work and furnaces can be made from sheet metal.
Equestrian Purposes
Sheet metal has long been used to make decorative horse tack such as breastplates.
Historical Uses
Centuries ago, sheet metal was used to make body armor for men in a cavalry.
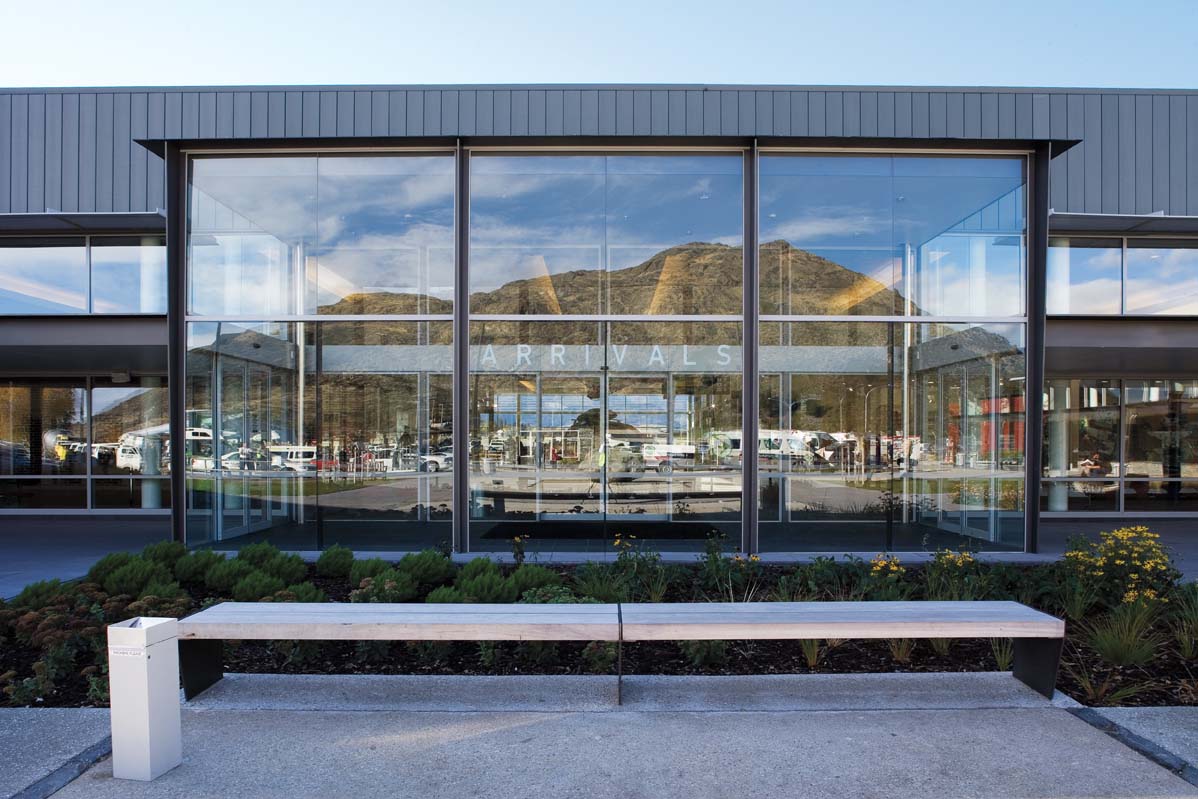
Process
Advantages
- Sheet metal fabrication is very common nowadays, which of course has a reason. This mostly is the case because this process is a cost-effective way to get any amount of desired shapes and sizes, while you will only need a short amount of time to produce the exact piece. It could be a small part of the semiconductor sector, but also a big part of a ...
Materials & Specifications
- For sheet metal fabrication you can use a wide range of metals. Examples of the materials that can be used are stainless steel, aluminum, titanium, and much more. Press brakes will be used to shape the parts. Usually, these can accommodate pieces up to 10 feet long, weighing up to 125 tons. Tight tolerances can still be achieved, however, up to circa 0.005 in. can be possible.
Finishing Sheet Metal Fabrication
- There are multiple finishing techniques that you can choose according to your requirements. With the help of these finishing techniques, you can protect the material from dust, corrosion, and other weather factors affecting the metal. Moreover, some of the standard finishing techniques that are there are:
Conclusion
- These are the basic aspects and benefits that any business or buyer gets as they opt for metal sheet fabrication services. Considering this, it is important that you choose the metal for your project carefully so that you get the best results in the end.