
Full Answer
What are the advantages of make or buy decision?
Make or Buy Decision Meaning. A Make or Buy Decision is a decision made to either manufacture a product/ service in house or buy it from outside suppliers (outsourcing) based on cost-benefit analysis. A complete or accept decision can be made using quantitative or qualitative research and most of the time, the results of quantitative analysis (cost-benefit analysis) are enough to …
Do make or buy decisions matter?
Jan 24, 2019 · The Make or Buy Decision Jan 24, 2019 By Robert Barner, Ph.D. The Talent Focus Decision, otherwise known as the Make/Buy decision, deals with the question of whether you should rely primarily on the use of internal development (Make) or external replacement (Buy) to strengthen your leadership bench.
How do you make buying decisions?
Sep 19, 2019 · The make-or-buy decision is the action of deciding between manufacturing an item internally (or in-house) or buying it from an external supplier (also known as outsourcing). Such decisions are typically taken when a firm that has manufactured
How to make better purchase decisions?
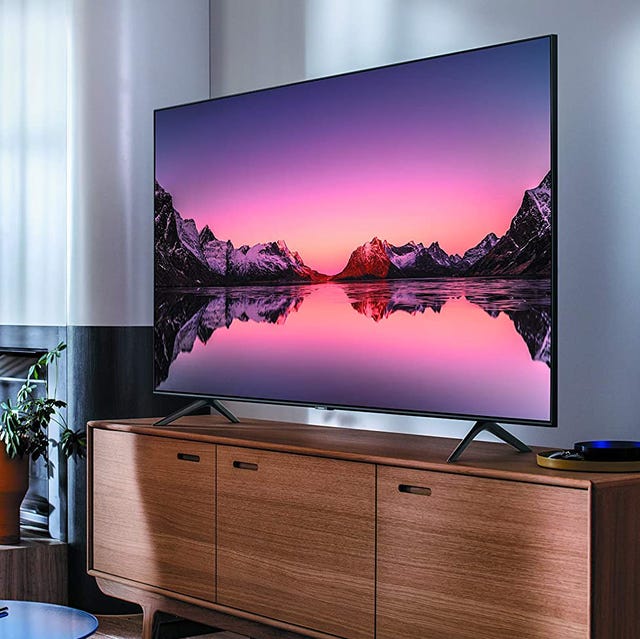
What is a make-or-buy decision?
A make-or-buy decision is an act of choosing between manufacturing a product in-house or purchasing it from an external supplier. Make-or-buy decisions, like outsourcing decisions, speak to a comparison of the costs and advantages of producing in-house versus buying it elsewhere.
What is an example of a make-or-buy decision?
Make-or-Buy decision (also called the outsourcing decision) is a judgment made by management whether to make a component internally or buy it from the market....Example.Per UnitTotalDirect Labor848,000Applied Variable Factory Overhead954,000Applied Fixed Factory Overhead1272,000$1.5 per direct labor dollar2 more rows•May 10, 2013
What is a make-or-buy decision quizlet?
Make vs. Buy Decision. the act of deciding whether to produce an item internally or buy the item from an outside supplier. make. Producing (i.e., manufacturing) materials or products internally (i.e., in operations owned by the company).
What factor will you consider at the time of make-or-buy decision?
The make-or-buy decision requires thorough analysis from all angles. Quantitative factors to consider may include things such as the availability of production facilities, production capacity, and required resources. They may also include fixed and variable costs that can be determined with certainty or estimated.
Why make-or-buy decision is important?
Enabling or Improving Product Production In other cases, the make-or-buy decision can help companies with product designs and manufacturing efforts that they would not otherwise be capable of. For example, say that a scooter company is designing a new scooter for mass production.
What are the key considerations in making a make vs buy decision with regard to a software?
Let's take a look at the major factors and considerations you will face while making your decision.Technology & Compatibility. Square Pegs & Round Holes. ... Features. The Must Have's, Should Have's, Could Have's, & Won't Have's. ... Performance. The Need for Speed. ... Design. ... Documentation, Training & Support. ... Speed to Market. ... Cost & ROI.
Which of the following is one of reasons for buy decision?
In the make-or-buy decision, one of the reasons for making is: to assure adequate supply in terms of quantity.
Which of the following factors are not qualitative factors in a make-or-buy decision?
Question: Which of the following is not a qualitative factor to be considered in a make-or-buy decision? Possible lost jobs from buying outside supplier's ability to satisfy quality standards Direct materials and direct labor costs from making Outside supplier's ability to meet production schedule.
Why is the make-or-buy decision strategy important for a business?
The make or buy decision involves whether to manufacture a product in-house or to purchase it from a third party. The outcome of this analysis should be a decision that maximizes the long-term financial outcome for a company.Mar 11, 2021
What is a make or buy decision?
A make-or-buy decision is an act of choosing between manufacturing a product in-house or purchasing it from an external supplier. Make-or-buy decisions, like outsourcing decisions, speak to a comparison of the costs and advantages of producing in-house versus buying it elsewhere. There are many factors at play that may tilt a company ...
What are the factors to consider in making a buy decision?
In a make-or-buy decision, the most important factors to consider are part of quantitative analysis, such as the associated costs of production and whether the business can produce at required levels.
What factors can tilt a company from making an item in-house or outsourcing it?
There are many factors at play that may tilt a company from making an item in-house or outsourcing it, such as labor costs, lack of expertise, storage costs, supplier contracts, and lack of sufficient volume. Companies use quantitative analysis to determine whether making or buying is the most cost-efficient method.
What factors can a firm use to make an item in-house?
Similarly, factors that may tilt a firm toward making an item in-house include existing idle production capacity, better quality control, or proprietary technology that needs to be protected.
What factors influence a firm's decision to buy a part rather than produce it internally?
Factors that may influence a firm's decision to buy a part rather than produce it internally include a lack of in-house expertise, small volume requirements, a desire for multiple sourcing, and the fact that the item may not be critical to the firm's strategy.
What should a company consider when considering a supplier?
The firm should also consider whether the supplier can offer the desired long-term arrangement if that is what it requires.
What is included in in-house production?
Regarding in-house production, a business must include expenses related to the purchase and maintenance of any production equipment and the cost of production materials. Costs to make the product can include the additional labor required to produce the items, which takes the form of wages and benefits, storage requirements within the facility, holding costs overall, and the proper disposal of any remnants or byproducts from the production process.
What is a make or buy decision?
A Make or Buy Decision is a decision made to either manufacture a product/ service in house or buy it from outside suppliers (outsourcing) based on cost-benefit analysis. A complete or accept decision can be made using quantitative or qualitative research and most of the time, the results of quantitative analysis (cost-benefit analysis) ...
What are the advantages of making a buy decision?
Some of the advantages of making or buy decisions are as follows: The finding helps choose the most efficient option to go about in-house production of outsourcing. The decision helps in the strategic maneuver of the business. The decision helps save the cost for many businesses.
What are the factors considered when deciding to buy the good or service from the outside supplier?
Environmental reasons. Political reasons. The following are the major factors considered while deciding to buy the good or service from the outside supplier. Lack of expertise. Research and specialized know-how of the supplier better than the buyer.
Why does Apple outsource its manufacturing to China?
The smartphone giant Apple Inc. outsources the manufacturing of all its devices to China because manufacturing is not its core competency. It is also significantly cheaper to assemble the tools in China due to substantially lower costs.
What are the benefits of outsourcing production?
The benefits include higher margins from in-house production. The cost associated with outsourced production includes the product and service, transportation, warehousing, and storage and labor costs for managing the logistics. The decision becomes a little straightforward if the company does not have an idle capacity to produce ...
Should you make or buy?
The make or buy decision should be taken with utmost care keeping the long-term and short-term benefits into consideration. There are pros and cons to both make and purchase; however, generally, businesses tend to outsource function where they do not have a core competency or when the cost of procuring the components or services from outside suppliers is significantly cheaper.
What are the four numbers you need to know to make a decision?
Four Numbers You Should Know. When you are supposed to make a make-or-buy decision, there are four numbers you need to be aware of. Your decision will be based on the values of these four numbers. Let's have a look at the numbers now. They are quite self-explanatory. The volume. The fixed cost of making.
Why is outsourcing important?
Outsourcing was viewed as one of the best ways of getting things done for a fraction of the original cost. Outsourcing is closely related to make or buy decision. The corporations made decisions on what to make internally and what to buy from outside in order to maximize the profit margins.
Can an organization make a decision on make or buy?
By following the above structured process, the organization can make an informed decision on make-or-buy. Although this is a standard process for making the make-or-buy decision, the organizations can have their own varieties.
Is "make or buy" a valid concept?
Make or buy decision is always a valid concept in business. No organization should attempt to make something by their own, when they stand the opportunity to buy the same for much less price.
What are the drawbacks of the Make Strategy?
Another drawback that you need to consider is that, over time, companies that become heavily reliant on the Make Strategy can fall into the trap of becoming excessively insular. When this happens, they tend to gauge the strength of their leadership talent solely by historical standards.
What do managers learn on the job?
Much of what managers learn on the job is not anything that can be neatly summarized in a policy statement or procedural manual, but rather consists of that vast body of tacit knowledge that managers learn through close-quarter observation and personal experimentation.
Who is Robert Barner?
Robert Barner, Ph.D., is Vice President of Management Development for Belo Corporation, a media company that encompasses newspapers, broadcast stations, cable networks and Internet services in major U.S. cities. He is also a professor in the Department of Dispute Resolution and Conflict Management at Southern Methodist University. Dr. Barner has more than 20 years of experience in organizational and management development and has worked on OD assignments throughout North America, Europe, Asia and Australia.
Is the buy strategy expensive?
Pitfalls Associated with the Buy Strategy. Unfortunately , the Buy Strategy can prove incredibly costly, since the current market value for top-notch leaders may be quite high when compared to the compensation currently being paid to those incumbents who have slowly worked their way up the internal salary escalator.
What are some examples of factors that affect the decision making process?
Examples of such factors include control over component quality, the reliability and reputation of the suppliers, the possibility of modifying the decision in the future, the long-term viewpoint concerning manufacture or purchase of the product, and the impact of the decision on customers and suppliers.
What are relevant costs for manufacturing the good?
Relevant costs for manufacturing the good are all the expenses that could be avoided by not manufacturing the product in addition to the opportunity cost resulting from utilizing production facilities to manufacture the good as against the next best alternative utilization of the manufacturing facilities.
What is the difference between qualitative and quantitative?
Quantitative aspects can be calculated and compared whereas qualitative aspects call for subjective judgment and, frequently require multiple opinions. In addition, some of the associated factors can be quantified with sureness while it is necessary to estimate other factors. The make-or-buy decision calls for a thorough assessment from all angles.
What are qualitative factors? What are some examples?
An example for this is that it may be possible that the business has zero experience in manufacturing a specific good and its previous experience in manufacturing other goods cannot be applied.
What is relevant cost?
Relevant costs for buying the product are all the expenses relating to purchasing a product from suppliers. Irrelevant costs are the expenses involved irrespective of whether the good is produced internally or bought externally.
What is value chain?
A value chain is the complete range of tasks – such as design, manufacture, marketing and distribution of a product / service that businesses must get done to take a service or product from conception to their customers.
Why is design secrecy important?
Quantity too little to interest a supplier. Design secrecy is necessary to protect proprietary technology. Control of transportation, lead time, and warehousing expenses. Political, environmental, or social reasons.
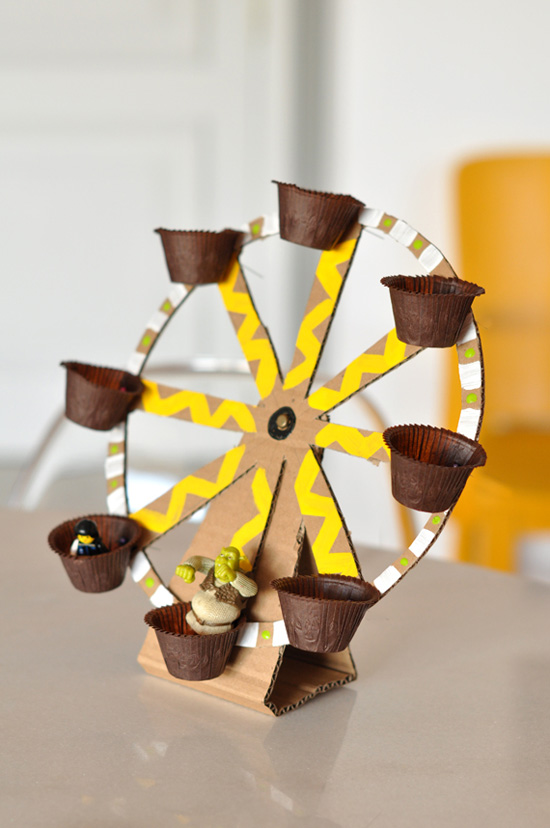
Make-Or-Buy Decision Triggers
- A company’s decision on whether to make or buy is based on its core competence. The production cost and quality problems are the major triggers of a make-or-buy decision. Other factors are managerial decisions and a company’s long-term business strategy that dictate the c…
Make-Or-Buy Decision Criteria
- Setting up a standard make-or-buy process that applies to all companies is a complicated process. It is partly due to companies’ distinct behavior patterns and the fact that businesses operate in different business environments that are unique to each business. However, cost accounting remains the primary dimension of the make-or-buy decision. Companies evaluate ou…
Benefits of A Make-Or-Buy Decision
- A make-or-buy decision framework relates to autonomy, and a company selects from the many advanced options to account for various factors associated with outsourcing.
Additional Resources
- Thank you for reading CFI’s guide to Make-or-Buy Decision. To keep advancing your career, the additional CFI resources below will be useful: 1. Cost AllocationCost AllocationCost allocation is the process of identifying, accumulating, and assigning costs to costs objects such as departments, products, programs, or 2. Competitive AdvantageCompetitive AdvantageA compet…
What Is A Make-Or-Buy Decision?
Understanding A Make-Or-Buy Decision
- Regarding in-house production, a business must include expenses related to the purchase and maintenance of any production equipment and the cost of production materials. Costs to make the product can include the additional labor required to produce the items, which takes the form of wages and benefits, storage requirements within the facility, holding costsoverall, and the pro…
Choosing Make Or Buy
- The results of the quantitative analysis may be sufficient to make a determination based on the approach that is more cost-effective. At times, the qualitative analysis addresses any concerns a company cannot measure specifically. Factors that may influence a firm's decision to buy a part rather than produce it internally include a lack of in-house expertise, small volume requirements, …
Why Choose?
- If a company is already in business there may be a point when certain situations arise that will cause a company to pause and consider which direction it should proceed in; whether it should buy or make the parts or products it needs. Some of these events could be a trusted supplier shutting down, an increase or decrease in demand for the product, or a possible path for new op…
Introduction
Four Numbers You Should Know
- When you are supposed to make a make-or-buy decision, there are four numbers you need to be aware of. Your decision will be based on the values of these four numbers. Let's have a look at the numbers now. They are quite self-explanatory. 1. The volume 2. The fixed cost of making 3. Per-unit direct cost when making 4. Per-unit cost when buying Now, there are two formulas that use …
Reasons For Making
- There are number of reasons a company would consider when it comes to making in-house. Following are a few: 1. Cost concerns 2. Desire to expand the manufacturing focus 3. Need of direct control over the product 4. Intellectual property concerns 5. Quality control concerns 6. Supplier unreliability 7. Lack of competent suppliers 8. Volume too small to get a supplier attract…
Reasons For Buying
- Following are some of the reasons companies may consider when it comes to buying from a supplier: 1. Lack of technical experience 2. Supplier's expertise on the technical areas and the domain 3. Cost considerations 4. Need of small volume 5. Insufficient capacity to produce in-house 6. Brand preferences 7. Strategic partnerships
The Process
- The make or buy decision can be in many scales. If the decision is small in nature and has less impact on the business, then even one person can make the decision. The person can consider the pros and cons between making and buying and finally arrive at a decision. When it comes to larger and high impact decisions, usually organizations follow a standard method to arrive at a d…
Conclusion
- Make-or-buy decision is one of the key techniques for management practice. Due to the global outsourcing, make-or-buy decision making has become popular and frequent. Since the manufacturing and services industries have been diversified across the globe, there are a number of suppliers offering products and services for a fraction of the original price. This has enhance…