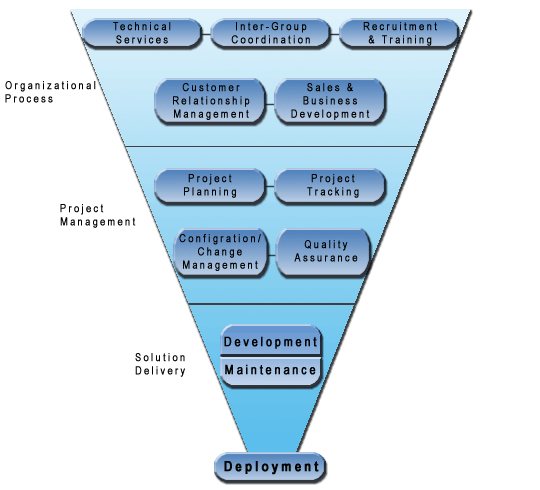
Quality management consists of four key components, which include the following:
- Quality Planning – The process of identifying the quality standards relevant to the project and deciding how to meet them.
- Quality Improvement – The purposeful change of a process to improve the confidence or reliability of the outcome.
- Quality Control – The continuing effort to uphold a process’s integrity and reliability in achieving an outcome.
What are the best practices of quality management?
Practice Makes Perfect…or Very Close. So, when we at InfinityQS talk about best practices for quality management systems, we’re talking about five things: Taking a step back. Knowing your goals. Starting small. Thinking “standardization”. Treating it like it’s a process. These five mainstays of what I consider to be best practices for ...
What companies have implemented Total Quality Management?
With fear of closing down, Xerox fought back using TQM to regain their market share. They implemented TQM by opening the Palo Alto Research Center (PARC), which focused on ways to emerge as a leader in the printer/copy/fax market. Their main goal: “Innovation is everywhere; the problem is learning from it.”
What is the concept of quality management?
• Quality Management — The planning, scoping, implementing, and monitoring of quality into all phases of the project from concept through the delivery aspects of the work. Quality Management involves the skill of forming and managing a team of people to achieve a qualitative goal within an effective cost and time frame, which will result in the production of a quality product or service.
Why implement a quality management system?
- Required by your Customers, especially internationally-focused businesses
- Required by overseas regulatory bodies for suppliers of quality-sensitive products, e.g. medical devices
- Necessary to maintain market presence and a competitive advantage
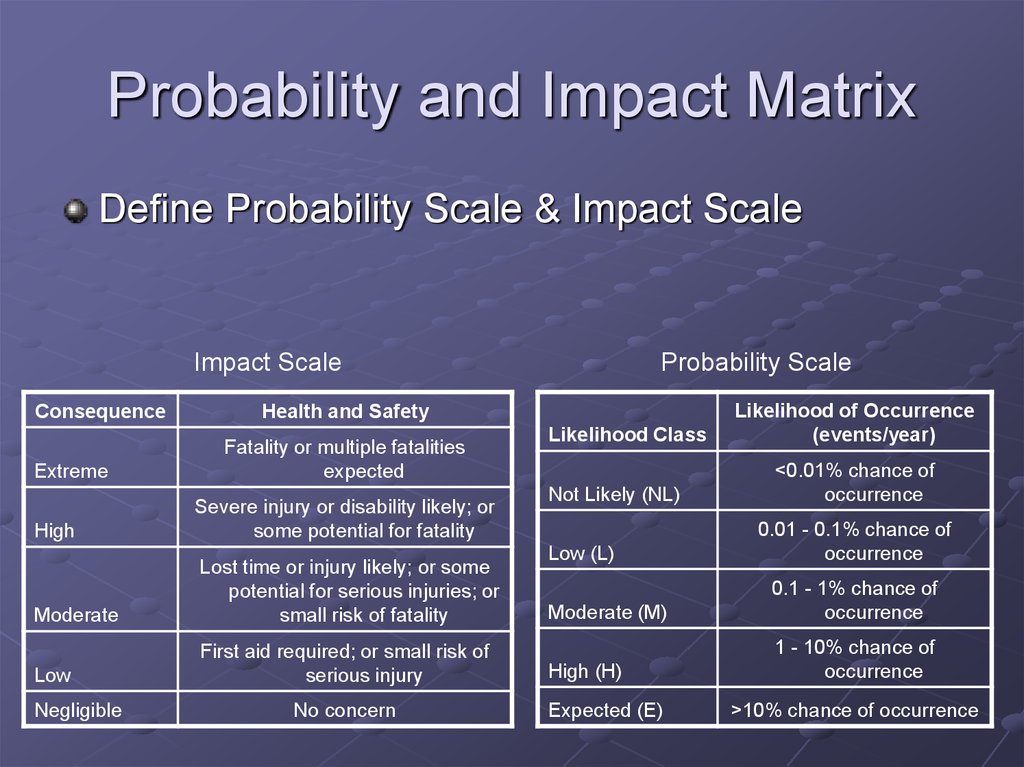
What are the processes in quality?
Components of Quality Management Process Afterwards, three key processes, namely, a "Quality Assurance Process", "Quality Control Process", and "Continuous Improvement Process", are set forth to measure, report and improve the deliverables' actual quality.
What are the three processes of quality management?
Project quality management is broken down into three main processes: Quality Planning, Quality Assurance, and Quality Control.
How many processes are there in quality management?
Project quality management happens with these three processes: Quality planning. Quality assurance. Quality control.
Why quality is a process?
Quality Process means the quality assurance procedures, methods and mechanisms that assure consistency and control in producing a product or service.
What are the four stages of quality management?
Total quality management (TQM) has evolved over four stages: quality inspection, quality control, quality assurance, and TQM (Dahl- gaard, Kristensen, and Kanji, 2002).
What are the 4 components of a process?
These four critical items are: (1) Process Definition, (2) Process and Activity Roles, (3) Available Tools and (4) Training. Plain and simple reality- these elements are inseparably linked.
What is Process Management in TQM?
Process Management refers to aligning processes with an organization's strategic goals, designing and implementing process architectures, establishing process measurement systems that align with organizational goals, and educating and organizing managers so that they will manage processes effectively.
What is quality management?
Quality management is the act of overseeing different activities and tasks within an organization. Corporate Structure Corporate structure refers to the organization of different departments or business units within a company. Depending on a company’s goals and the industry.
What are the principles of quality management?
These principles are used by top management to guide an organization’s processes towards improved performance. They include: 1. Customer Focus.
How does consistency help an organization?
It helps an organization achieve greater consistency in tasks and activities that are involved in the production of products and services. It increases efficiency in processes, reduces wastage, and improves the use of time and other resources. It helps improve customer satisfaction.
What is relationship management?
Relationship management is about creating mutually beneficial relations with suppliers and retailers. Different interested parties can impact a company’s performance. The organization should manage the supply chain process well and promote the relationship between the organization and its suppliers to optimize their impact on the company’s performance. When an organization manages its relationship with interested parties well, it is more likely to achieve sustained business collaboration and success.
What is evidence based decision making?
Evidence-based Decision Making. Businesses should adopt a factual approach to decision-making. Businesses that make decisions based on verified and analyzed data have an improved understanding of the marketplace. They are able to perform tasks that produce desired results and justify their past decisions.
What is quality planning?
Quality Planning – The process of identifying the quality standards relevant to the project and deciding how to meet them. Quality Improvement – The purposeful change of a process to improve the confidence or reliability of the outcome. Quality Control – The continuing effort to uphold a process’s integrity and reliability in achieving an outcome.
How does management engage employees?
The management engages staff in creating and delivering value whether they are full-time, part-time, outsourced, or in-house. An organization should encourage the employees to constantly improve their skills and maintain consistency. This principle also involves empowering the employees, involving them in decision making and recognizing their achievements. When people are valued, they work to their best potential because it boosts their confidence and motivation. When employees are wholly involved, it makes them feel empowered and accountable for their actions.
What are the objectives of quality management?
The objectives of the quality management process are: 1 To set the quality targets to be met by the project team 2 To define how the set quality targets are to be measured 3 To take all necessary actions to measure the project quality 4 To report on the overall level of quality achieved on the project
What is the role of a project manager in quality management?
The project manager is tasked with the planning of the quality management process. This planning process touches on all the aspects of the scope of the project as they all determine the quality of the final results of the project. 2. Test and Inspection Planning.
What is quality assurance?
The quality assurance team plans on what should be considered and how the test and inspection will be carried out to measure the quality targets set out for the project. This is done to ensure that the final results and product of the project complies with the standards and regulations put in place.
What is a test plan?
The Test Plan is the output document for the test and inspection planning activity. It details how the tests and inspection will be conducted on the project to measure its level of quality.
Why is the process important in a project?
Thus, the process helps to monitor the final results of a project on both the management level and the product to determine if they correspond to the set standards and establish what could be done to improve the results to meets the standards. This process is critical as it helps in ensuring that the deliverables acquired can meet ...
What is a project manager?
The project manager develop s the quality management plan while putting into consideration all the quality standards that were set for the project. To develop the quality management plan, it will require all the documents detailing the quality standards and regulations to be used.
Is quality management an independent process?
Quality management is not an independent and separate process that occurs at the end of the project lifecycle. Rather, it is a continuous process that should begin and end with the project. Thus, these activities must be implemented effectively to ensure the expected product quality is realized.
What is project quality management?
Project quality management is the process of continually measuring the quality of all activities and taking corrective action until the desired quality is achieved. Quality management processes help to control the cost of a project, establish standards, and determine the steps to achieving and confirming those standards.
What is quality control?
Quality control involves operational techniques meant to ensure quality standards. This includes identifying, analyzing, and correcting problems. While quality assurance occurs before a problem is identified, quality control is reactionary and occurs after a problem has been identified, and suggests methods of improvement. Quality control monitors specific project outputs and determines compliance with applicable standards. It also identifies project risk factors, their mitigation, and looks for ways to prevent and eliminate unsatisfactory performance.
What is matrix diagram?
Matrix diagrams. A matrix diagram is used to analyze data within an organization's structure. The matrix diagram shows the relationships between objectives, factors, and causes that exist between rows and columns that make up the entire matrix.
What is quality assurance?
Quality assurance is a process that provides evidence to the stakeholders that all quality-related activities are being done as defined and promised. It ensures that safeguards are in place to guarantee that all expectations will be met with regard to quality outputs. Quality assurance is done to the products and services delivered by a project, ...
Why use prioritization matrices?
Use prioritization matrices during brainstorming sessions to evaluate different issues based on set criteria to create a prioritized list of items. It helps to identify what issues may arise and determine what problems to solve first to meet certain objectives.
How does a quality management system affect an organization?
Benefits of a documented quality management system include: Meeting the customer’s requirements, which helps to instill confidence in the organization, in turn leading to more customers, more sales, and more repeat business.
What are the elements of a quality management system?
Each element of a quality management system helps achieve the overall goals of meeting the customers’ and organization’s requirements. Quality management systems should address an organization’s unique needs; however, the elements all systems have in common include: 1 The organization’s quality policy and quality objectives 2 Quality manual 3 Procedures, instructions, and records 4 Data management 5 Internal processes 6 Customer satisfaction from product quality 7 Improvement opportunities 8 Quality analysis
What is QMS self assessment?
Healthcare QMS Self-Assessment Based On A Maturity Model ( Journal for Quality and Participation) Details on how the self-assessment process should be modified as the organization advances through the six maturity stages. Process maps and worksheets and worksheets are included for each stage.
What is the hospital-based QMS model?
This model is directed to the CEO and CMO who are seeking to improve patient outcomes, safety, and satisfaction, as well as cost savings, risk management, and regulatory compliance.
What is QMS design?
The QMS design should be influenced by the organization’s varying objectives, needs, and products and services provided. This structure is based largely on the plan-do-check-act (PDCA) cycle and allows for continuous improvement to both the product and the QMS.
What is control and measurement?
Control and measurement are two areas of establishing a QMS that are largely accomplished through routine, systematic audits of the quality management system. The specifics vary greatly from organization to organization depending on size, potential risk, and environmental impact.
Why is QMS important?
Because of the multitude of unique systems that can be applied, the term “Quality Management System” or “QMS” is preferred. At the start of the 21st century, QMS had begun to merge with the ideas of sustainability and transparency, as these themes became increasingly important to consumer satisfaction.
What is quality management?
Quality management is when a company ensures it completed all of its tasks and production in a specific way to ensure a certain level of excellence. Quality management is often discussed in terms of the actual product production process. However, this strategy is important in any area in which the company directly impacts or affects its consumers.
Why is quality management important?
There are several reasons why quality management is an important component of any successful business. The primary reasons why it's important include that it:
Components of quality management
When it comes to effective quality management, there are a few primary components that must be accounted for. These components include:
Quality management principles
The International Standard for Quality Management has set forth several principles to guide organizations when implementing quality management procedures. These principles include:

Quality Improvement Methods
Quality Management – Example
- A model example of great quality management is the implementation of the Kanban system by Toyota Corporation. Kanban is an inventory control system that was developed by Taiichi Ohno to create visibility for both the suppliers and buyers to help limit the upsurge of excess inventoryon the production line at any given point in time. Toyota used the concept to execute its Just-in-Tim…
Principles of Quality Management
- There are several principles of quality management that the International Standard for Quality Management adopts. These principles are used by top management to guide an organization’s processes towards improved performance. They include:
Benefits of Quality Management
- It helps an organization achieve greater consistency in tasks and activities that are involved in the production of products and services.
- It increases efficiency in processes, reduces wastage, and improves the use of time and other resources.
- It helps improve customer satisfaction.
- It helps an organization achieve greater consistency in tasks and activities that are involved in the production of products and services.
- It increases efficiency in processes, reduces wastage, and improves the use of time and other resources.
- It helps improve customer satisfaction.
- It enables businesses to market their business effectively and exploit new markets.
Bottom Line
- Quality management in businesses is vital to ensure consistency in its processes, as well as in its products and services. In business, customer satisfaction is key. As a customer’s main concern is the quality of the products or services they purchase, the supplier’s main goal should always be to ensure that what they produce is of consistent and fine quality.
Related Readings
- Thank you for reading CFI’s guide to Quality Management. To learn more and expand your career, check out the additional CFI resources below: 1. Free Fundamentals of Credit Course 2. 5 P’s of Marketing 3. Brand Equity 4. Homogenous Cost Pool 5. Walmart Marketing Mix