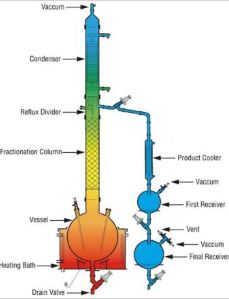
The packing in a distillation column creates a surface for the liquid to spread on. This provides a high surface area for mass transfer between the liquid and the vapor.
What is a packed distillation column?
Packed distillation columns are filled or "packed" with a material that allows rising vapors to contact descending condensate. The more vapor liquid contact the better the separation. Packing material of construction should be compatible with the material being distilled.
What type of packaging is best for fractional distillation equipment?
This packing is ideal for cases where packing must be made of glass or Teflon. This packing is great for rugged industrial type fractional distillation equipment. It is normally made of stainless steel. There are other types of high-tech structured packing that are very efficient.
What is random packing in distillation?
Random packing in the form of proprietary shapes, saddles and rings. Random packing is arbitrarily unloaded into the distillation column and takes up a random order within the column. Packing with a consistent layout, for example, grids have an advantage in that they provide a much larger surface area for substances to flow through.
Is a packed column more cost effective than a plate column?
However, with smaller diameter columns, it can be more cost-effective to use packing and replace it once it becomes fouled. When considering corrosive substances, a packed column tends to be always more cost-effective than a column with trays. The liquid holdup in a packed column is significantly less than in a plate column.

Why packing is used in distillation column?
Packing material can be used instead of trays to improve separation in distillation columns. Packing offers the advantage of a lower pressure drop across the column (when compared to plates or trays), which is beneficial while operating under vacuum.
What does column packing do?
Packed columns are used in a range of industries to allow intimate contact between two immiscible/partly immiscible fluids, which can be liquid/gas or liquid/liquid. The fluids are passed through a column in a counter current flow.
What is the use of packing in the column or tower?
Within the column, tower packing provides a surface for capturing moisture and/or particulates that then fall to a collection point at the bottom of the tower while the hot gases rise to an exit.
What is packing in distillation?
The small pieces of random packing in a distillation column are designed to form a large surface area where the reactants can interact while minimizing complexity within the column. Random packing is designed to maximize the surface-to-volume ratio and minimize pressure drop.
Which packing is commonly used in column?
There exists two methods to fill columns: • dry packing, • slurry packing (filtration technique). The dry filling method is easy to perform, but the slurry method gives, especially for smaller particles, more efficient and more reproducible columns.
What are the types of packing in distillation column?
The types of packing that exist include Raschig rings, Pall rings, Berl saddle ceramic rings, Intalox saddle ceramic rings, metal hypac and super Intalox ceramic rings. Three different types of plates exist: sieve plate (perforated plate), bubble-cup plates and valve plates (floating cap plates).
Why packed column might be chosen rather than tray column for application of absorption?
Packings provide extra interfacial area for liquid-vapor contact, so the efficiency of the separation is increased for the same column height. Packed columns can be shorter and more cost-efficient than trayed columns. Random packings are easier to install than trays and structured packing.
What is packing in absorption column?
Packing section in the absorption process plays important role providing surface area for the gas and liquid phases to contact upon. Mainly, two different types of packing materials are available for gas absorption; Random packing (Pall ring, IMTP, Raschig rings) and Structured packing (Flexipac, Mellapak, Gempak, BX).
Why do we pack column chromatography?
Good column packing is essential for any chromatographic process and plays a key role in bioprocessing of biopharmaceuticals. A bed packed too densely might crack, which can lead to channeling and early breakthrough. A bed packed too loosely can further compress causing a liquid gap where mixing can occur.
What is column packing in chromatography?
In chromatography: Column chromatography. A packed column contains particles that either constitute or support the stationary phase, and the mobile phase flows through the channels of the interstitial spaces.
What is column packing material?
Packing Material HPLC columns are usually packed with pellicular, or porous particles. Pellicular particles are made from polymer, or glass beads. Pellicular particles are surrounded by a thin uniform layer of silica, polystyrene-divinyl-benzene synthetic resin, alumina, or other type of ion-exchange resin.
What is packing material of distillation column?
The standard distillation column packing offered is Pro-Pak® random packing. Customer specified packings can be used including materials of stainless steel, metal alloys, ceramic and plastics.
Why are distillation columns important?
As a result, they must be designed correctly and in the most cost-effective way possible. The interior of the distillation columns is arguably the most important part of the column as they are difficult to access after start-up.
What is distillation column design?
Distillation column design is a complex and intricate process that requires a good comprehension of various concerns. Each design choice has an impact on the operational range, pressure drop, cost, capacity and efficiency of the overall processes. Observing the suggestions outlined here will allow for more knowledgeable decisions.
What factors are considered when deciding on the internals of a distillation column?
Various factors need to be considered when deciding on the internals of the distillation column such as the flowrates of the vapour and liquid phases, the reason for separation, the desired product characteristics and the physical properties of the vapour and liquid phases.
What is the downcomer area of a cross flow plate?
The deck in a typical cross-flow plate contains an inlet region where the liquid is supplied as depicted above. The downcomer is the outlet. Plates need to have holes for vapour to flow through. The perforations make up approximately 5 % to 15 % of the tray area. The spacing between the trays is outlined below. The downcomer area consists of approximately 5 % to 30 % of the cross-sectional area of the column. This is dependant on the liquid load.
What are the two types of packing options?
When considering the choice between plates and packing, two types of packing options exist: random packing and structured packing. Packed columns tend to be used for distillation, gas absorption and liquid-liquid flow. The flow can be counter-current; however, in some gas-absorption columns, co-current flow is used.
Why is structured packing better than plate?
However, it is important to weigh the design choice between structured packing and plates because plates are preferable when the liquid flow rate is high, and the pressure drop is high.
What is a distillation plate?
Distillations plates, also called trays, allow for an amount of liquid holdup. This is to allow the vapour flow to encounter the liquid and allows for vapour-liquid mass transfer which is necessary for separation to occur.
