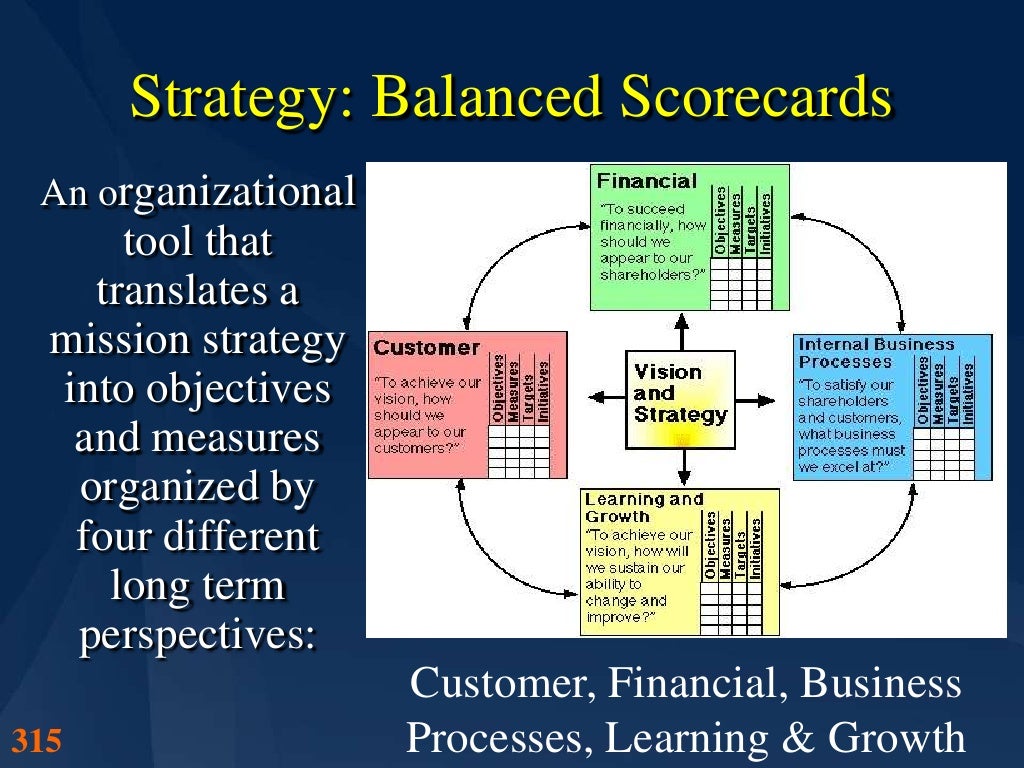
What are the different quality management approaches?
In this chapter the main quality management approaches are discussed, and the quality management principles are presented. In the development of their quality management systems, organisations have used three main approaches: the consultancy approach, the standardisation approach and the quality awards approach.
What is a quality approach in manufacturing?
The implementation of a quality approach in the industry aims to control, ensure and plan quality. It necessarily involves the constant improvement of products and services. This is naturally linked to manufacturing processes.
What are the main objectives of the quality approach?
The main objectives of the quality approach are to increase customer satisfaction and, more generally, to enable the company to gain in efficiency and performance. However, the customer is not the only side to be satisfied when developing and applying a quality approach.
What are the principles of quality management?
There are several principles of quality management that the International Standard for Quality Management adopts. These principles are used by top management to guide an organization’s processes towards improved performance. They include: 1. Customer Focus
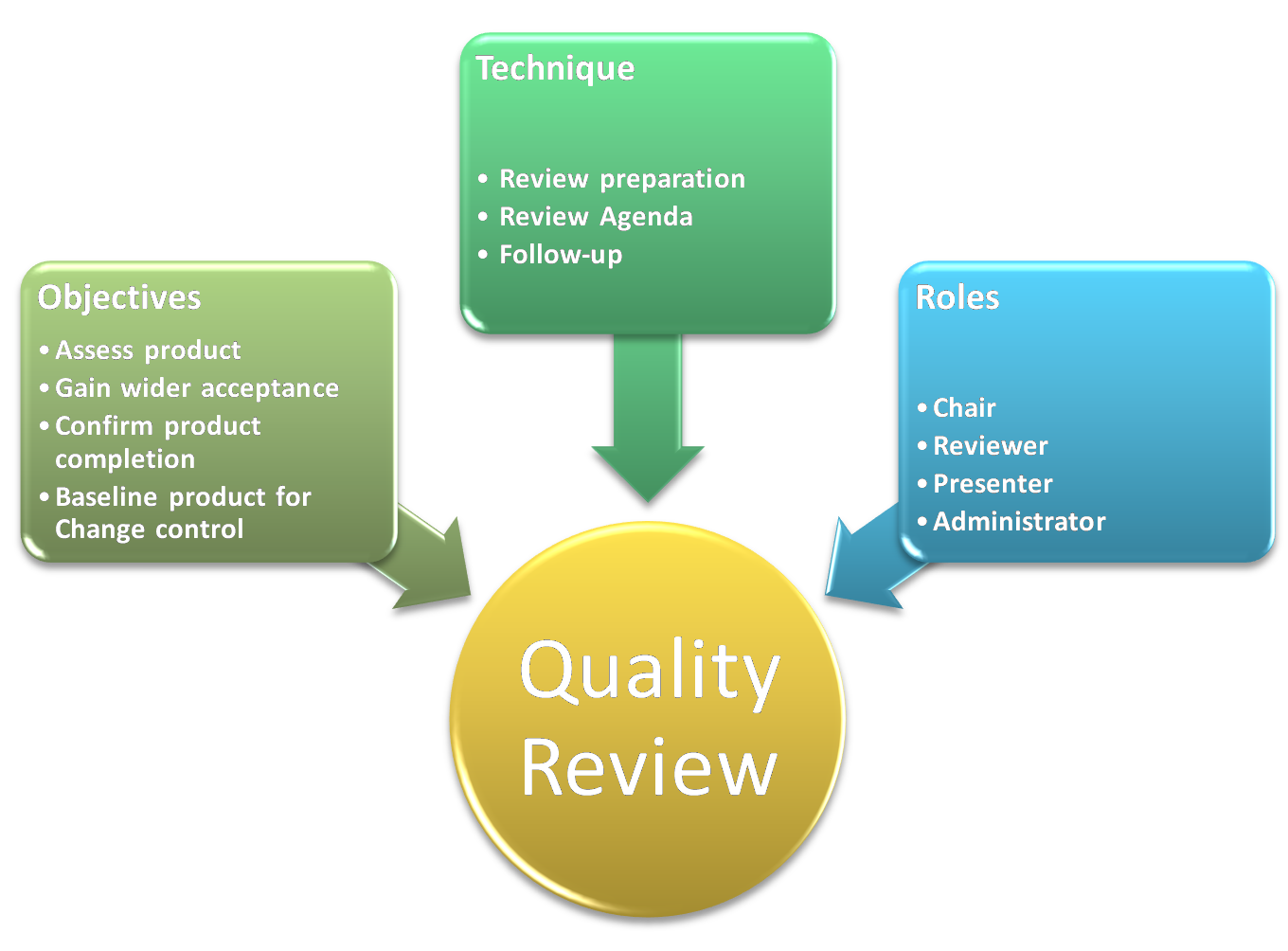
What is quality approach in quality management?
A Quality Management Approach describes how quality will be managed during the project. This includes the specific processes, procedures, techniques, standards, and responsibilities to be applied.
What is process approach in quality?
' An ISO 9001 process approach is a management strategy which incorporates the plan-do-check-act cycle and risk-based thinking. It means that processes are managed and controlled. It also means that we not only understand what the core processes are, but we also consider how they fit together.
What is difference between quality and total quality approach?
The difference between it and product quality is its scope. TQM deals with the entire process of production. The main thesis of the approach is that all elements of a firm are connected. To make a quality product, all aspects of a firm must be constantly striving for improvement.
What is the total quality management approach?
Total Quality Management (TQM) is a management framework based on the belief that an organization can build long-term success by having all its members, from low-level workers to its highest ranking executives, focus on improving quality and, thus, delivering customer satisfaction.
What is the approach process?
The process approach is a method of thinking applying to understand and plan the sequence and interactions of processes in the system. Saying that again, it's a method to plan the processes and the interactions of these processes as part of the management system.
What is process Approach example?
Examples include measurement, monitoring, reviews, audits and performance analysis. processes to ensure that they continue to deliver the intended outputs Act on the findings to ensure improvement of process effectiveness.
What are the two basic approaches to quality define them?
Five major approaches to the definition of quality can be identified: (1) the transcendent approach of philosophy; (2) the product-based approach of economics; (3) the user-based approach of economics, marketing, and operations management; and (4) the manufacturing-based and (5) value-based approaches of operations ...
What is total quality approach essay?
TQM is a continuous quest for excellence that aims to improve the efficiency as well as the flexibility of any organization by integrating the different processes within the organization. This system makes the prevention of defects in the early stages and is highly customer oriented.
What are the 7 principles of quality management?
The seven principles of quality management are:Engagement of people.Customer focus.Leadership.Process approach.Improvement.Evidence-based decision making.Relationship management.
What is modern quality approach?
Modern quality management entails customer satisfaction, it prefers prevention against inspection and it recognizes the managerial team's responsibility for quality. Several remarkable persons in the management field, like W. Edwards Deming, Joseph M.
What approaches of quality is implemented?
These approaches to TQM include: Just in time, Statistical process control, Total preventive maintenance, statistical and Management Tools, Automation Development, Quality function development, Quality circles, Total Quality control, Robust design, High Technology Circles, New Technology Development, Policy deployment, ...
What are 4 types of quality control?
What Are the 4 Types of Quality Control? There are several methods of quality control. These include an x-bar chart, Six Sigma, 100% inspection mode, and the Taguchi Method.
What is the importance of process approach?
The process approach is important to ISO 9001 as it places an overall focus on all processes in the QMS. This approach aims to iron out any inefficiencies, making it easier for your organisation to work on continual improvement.
What is primary goal of process approach?
The purpose of the process approach is to improve an organizational effectiveness and efficiency in achieving its defined objectives. Process effectiveness and efficiency are normally assessed through internal or external review processes.
What is a process management approach?
Process management is an approach to management that views the activities of an organization as a set of processes undertaken to advance organizational goals. A manager using this technique attempts to design organizational processes - activities - that emphasize quality and performance.
What are the advantages of the process approach?
What Benefits Does a Process Approach Provide?It focuses on integrating, aligning and linking processes and organizational functions effectively to achieve planned goals and objectives.It allows an organization to focus on improving its effectiveness and efficiency by focusing on end-products and customers.More items...•
Timeline Quality Management Approach
A Quality Management Approach describes how quality will be managed during the project. This includes the specific processes, procedures, techniques, standards, and responsibilities to be applied. A template is usually provided by the organization and only needs minor changes.
Timeline Quality Management Approach
The Quality Management Approach is created in the Initiating a Project process by the Project Manager
Why is building a quality management system easier than it seems?
Building a quality management system is easier than it seems. It is to improve your quality processes, which is more delicate and requires the implication of all . This is the principle of continuous improvement. Therefore, this new is much richer because it derives directly from the concept of this organization and quality as a measure ...
What is a procurement process?
Each process is a collection of activities you should define. For example, a procurement process that includes vendor selection, ordering, receiving and reassessment activities. You should identify and describe each of these activities with the formalism appropriate to the complexity of these activities and the competence of the staff.
Is quality approach new?
The reference to “quality approach” is not new. But today it expresses itself in specific meaning, even technical , on many occasions and in many fields. International standards are devoted to it, models, simple or less simple, are proposed about it. The shelves of bookstores are cluttered with general works, introductory books, specialized books, … that claim to teach you, in a hundred pages or a thousand, what’s what quality.
What is the purpose of quality approach?
The main objectives of the quality approach are to increase customer satisfaction and, more generally, to enable the company to gain in efficiency and performance. However, the customer is not the only side to be satisfied when developing and applying a quality approach.
What is quality system?
As a key element of the approach, the quality system covers the entire organization, procedures, processes and means for implementing quality management. It is based in particular on the improvement objectives mentioned in the quality manual, on a quality standard (operational procedures, quality plans, work instructions) and on ...
Why is it important for a company to ensure that the quality of the production is controlled?
It is therefore a matter for the company to ensure that the quality of the production is controlled, to have the capacity to meet customer requirements, to reduce malfunctions and anomalies that may affect quality and support its competitiveness.
How to be competitive in the market?
In order to be competitive, to position oneself favorably over the competition and to increase consumer interest in the products and services it offers, the company must make sure to control and ensure quality. What the company sell needs to be continually improved to meet the demands of the market. But it also needs to meet the expectations of the customer. It implements a quality approach that brings together and organizes all aspects of the company’s operation to achieve quality objectives.
What is anomaly sheet?
When an anomaly is found, it is reported in a formalized document that will subsequently analyze it and take the necessary measures to eliminate it in a sustainable way: this is the anomaly sheet. It usually shows the identifying elements of the anomaly (identifier, gravity, date …), its description and the response.
What is total quality management?
Total quality management has evolved from the quality assurance methods that were first developed around the time of World War I. The war effort led to large-scale manufacturing efforts that often produced poor quality products. To help correct this, quality inspectors were introduced on the production line to ensure that the level of failures due to quality was minimized.
What are the key principles of TQM?
A number of key principles can be identified in defining TQM, including: Executive Management: Top management should act as the main driver for TQM and create an environment that ensures its success . Training: Employees should receive regular training on the methods and concepts of quality.
What is TQM in business?
TQM looks at the overall quality measures used by a company including managing quality design and development, quality control and maintenance, quality improvement, and quality assurance. TQM takes into account all quality measures taken at all levels and involving all company employees.
What was the role of quality control in Japan after World War II?
Post World War II. After World War II, the industrial manufacturers in Japan produced poor quality items. In a response to this, the Japanese Union of Scientists and Engineers invited Dr. Deming to train engineers in quality processes. By the 1950s quality control was an integral part of Japanese manufacturing and was adopted by all levels ...
What is the theory of SQC?
The theory of SQC was based on the notion that a variation in the production process leads to variation in the end product. If the variation in the process could be removed this would lead to a higher level of quality in the end product.
What is a product requirement?
They are planned and incurred before actual operation, and can include: Product Requirements: The setting specifications for incoming materials, processes, and finished products/services. Quality Planning: Creation of plans for quality, reliability, operational, production, and inspections.
Is TQM costing more than benefits?
Many companies believe that the costs of the introduction of TQM are far greater than the benefits it will produce. However research across a number of industries has costs involved in doing nothing, i.e., the direct and indirect costs of quality problems are far greater than the costs of implementing TQM.
What is quality management?
Quality management is the act of overseeing different activities and tasks within an organization. Corporate Structure Corporate structure refers to the organization of different departments or business units within a company. Depending on a company’s goals and the industry.
What are the principles of quality management?
These principles are used by top management to guide an organization’s processes towards improved performance. They include: 1. Customer Focus.
How does consistency help an organization?
It helps an organization achieve greater consistency in tasks and activities that are involved in the production of products and services. It increases efficiency in processes, reduces wastage, and improves the use of time and other resources. It helps improve customer satisfaction.
What is the primary focus of an organization?
1. Customer Focus. The primary focus of any organization should be to meet and exceed the customers’ expectations and needs. When an organization can understand the customers’ current and future needs and cater to them, that results in customer loyalty, which in turn increases revenue.
What is relationship management?
Relationship management is about creating mutually beneficial relations with suppliers and retailers. Different interested parties can impact a company’s performance. The organization should manage the supply chain process well and promote the relationship between the organization and its suppliers to optimize their impact on the company’s performance. When an organization manages its relationship with interested parties well, it is more likely to achieve sustained business collaboration and success.
What is evidence based decision making?
Evidence-based Decision Making. Businesses should adopt a factual approach to decision-making. Businesses that make decisions based on verified and analyzed data have an improved understanding of the marketplace. They are able to perform tasks that produce desired results and justify their past decisions.
What is quality planning?
Quality Planning – The process of identifying the quality standards relevant to the project and deciding how to meet them. Quality Improvement – The purposeful change of a process to improve the confidence or reliability of the outcome. Quality Control – The continuing effort to uphold a process’s integrity and reliability in achieving an outcome.
What is Agile testing?
Agile Testing Process and Approach. Agile is undoubtedly the preferred software development methodology for today’s developers. Agile testing uses the same principles to encompass all elements of software testing from unit to system testing.
Why is automation important in QA?
Automation is also key to reducing costs and improving the efficiency of your team, which is one of the main reasons why QA managers must educate themselves and be willing to implement automation practices.
Is agile development the future?
Most would admit that agile development is the future; however, in order to exceed client expectations and improve the user experience, regardless of what method you choose, extensive QA isn’t a “nice to have,” it’s imperative. As the development landscape grows denser, our approach with its focus on automation, continuous integration, and the other best practices mentioned earlier will help you to maintain and surpass quality, ensure the highest satisfaction upon delivery, and provide the greatest experience for the user, as well as your development team, as possible.

Timeline Quality Management Approach
- A Quality Management Approach describes how quality will be managed during the project. This includes the specific processes, procedures, techniques, standards, and responsibilities to be applied. A template is usually provided by the organization and only needs minor changes. This document is created at the initiation stage with the other approach...
Source Data For The Quality Management Approach
- Quality Management Approach template which should already include most of the following information
- Project management team structure (forRolesand responsibilities),
- Project Product Description(for the customer’s quality expectations and acceptance criteria)
- Supplier and customer quality management systems
Format of The Quality Management Approach
- This document can take a number of formats
- However, it will normally be a stand-alone document (Word / PDF)
Quality Criteria For The Quality Management Approach
- Clearly define how the customer’s quality expectations will be met
- Responsibilities for quality are defined up to a level that is independent of the project and Project Manager
- The strategy conforms to the supplier’s and customer’s quality management systems
- The strategy conforms to the corporate or programme quality policy
Tips from Frank
- Decide which approach to use for quality: Customer or Supplier
- Get an up to date Quality Management Approach template from the programme or customer
- Review theProject Product Descriptionbefore you review the Quality Management Approach template