
The thickness of the coating is in microns or micrometers (μm). Zinc plating requires a minimum thickness of 5μm (.005mm) and a maximum thickness of 25μm (.025mm). Coating steel of any thickness will become too technical and expensive. The minimum thickness of hot-dip galvanized is 45μm (.045mm), more than 100μm (.1mm)
See more

How thick is a galvanized coating?
3-8 milsTypical galvanized coatings range from 3-8 mils (75-200 mi- crons) thick. When designing and detailing tapped holes, the increased thickness is important. Best practice suggests that the hole be tapped after galvanizing, removing the coating on the interior mating surface.
How thick should zinc plating be?
The zinc coating thickness of mechanically plated parts ranges from 0.2 to 4.3 mils (5 to 109 µm), but the common thickness on commercial fasteners is 2 mils (50 µm). The thickness is regulated by the amount of zinc in the barrel and the duration of the tumbling time.
How much does galvanizing add to thickness?
4% to 8%The weight of the zinc on any article after galvanizing depends on the thickness of the article being galvanized. Normally, galvanizing will add 4% to 8% to the nominal weight of a steel article. Heavier items normally pick up a lower percentage of weight (4%-5%) than thinner material.
How much zinc is used for galvanized steel?
Regular galvanized is approximately 99.7% zinc coated. Galvannealed offers a surface with more of a matte finish and more porosity. Its paint adhesion properties are excellent. The coating is composed of approximately 90% zinc and 10% iron.
How do you calculate the thickness of zinc coating?
The density of the zinc is 7.14. Therefore, a thickness of 1 micron of zinc is equivalent to 7.14 g/m2. Example: zinc coating thickness measured on one side of the CGI sheet is 20 µm. Then, the zinc coating mass is equal to: 20 x 7.14 = 135.66 g/m2 of zinc on one side.
How is zinc coating thickness measured?
There are two methods for measuring the zinc coating thickness of hot-dip galvanized steel; a magnetic thickness gauge and optical microscopy. The simplest and non-destructive way is to utilize a magnetic thickness gauge, as optical microscopy is a destructive test only used to resolve measurement disputes.
What is the galvanizing standard?
Galvanizing standards. Hot dip galvanizing is a relatively simple process to specify and is covered by a single standard EN ISO 1461. Galvanizers Association can provide detailed advice on compiling your specifications, as well as reviewing design details to maximise the benefits of galvanizing your steel.
How is galvanization thickness measured?
There are four ways to measure the galvanization thickness:Magnetic principle coating thickness gages.Stripping and weighing.Weighing the part before and after galvanizing.Optical microscopy (ASTM B487)
How is coating thickness calculated?
film thickness needs to be using some simple mathematical formulae:Wet Film Thickness.=Dry Film Thickness x 100.% Volume Solids.Spreading Rate (m2/litre) =% Volume Solids x 10.DFT Required.
How do you calculate the thickness of zinc coating in a galvanized sheet?
Weight = Surface Area X Thickness X Density. Because there are 10,000 cm2 per m2 of Surface Area, and 1/10,000 of a cm in a micron, the numbers work out nicely, with 1 micron thickness over a square meter being equal to 1 cm3 of metal.
What lasts longer zinc or galvanized?
The big difference is thickness: zinc plating is normally 0.2 mils thick. Hot dip galvanizing might be 1.0 mil thick – you get over 5 times the protection with galvanizing. All true galvanizing is hot dip galvanizing. Parts to be galvanized are submerged in molten, liquid zinc; hence the name “hot dip”.
Which is better zinc coated or galvanized?
A product that is hot dip galvanised will have a thicker coating, meaning it will last far longer. Hot dip galvanised coatings give superior protection against corrosion. The images below show that zinc plated gate hardware will rust over time.
How thick should plating be?
Choice of thickness when replating It might not sound like a lot, but plating from 1 micron and up is deemed good quality – under 1 micron is mostly referred to as flash plating and is not part of our offering, as the quality is too low.
What is the thickness of plating?
There are differences of plating layer thickness by the kind as chrome plating is possible to yield 0.1~0.2mm, and as nickel plating and copper plating are possible to yield above 1mm.
How do you calculate electroplating thickness?
We are using this formula: thickness in microns =. 22 * current density * plating time.
What is the typical thickness of an electroplated coating?
Electroplating for Increased Durability The plating thickness was tested at both 0.005 inch (0.127 mm) as well as 0.010 inch (0.254 mm). The thickness of plating typically ranges from 0.0001 inch to 0.020 inch (0.0025 mm 0.508 mm).
How thick is zinc coating?
The coating densities, in terms of thickness required to equal 1 oz of zinc per square foot of surface, are: Coating. Thickness to reach 1 oz/ft 2.
How much zinc is in a galvanized sheet?
For example, an ASTM A653 Class G90 sheet contains 0.90 oz/ft 2 of zinc or about 0.45 oz/ft 2 per side.
Why is zinc coating important?
Each zinc coating covered in this section provides varying degrees of corrosion protection and it is important to identify the corrosiveness of the exposure environment to determine if the coating selected will provide adequate service life.
When was zinc first used?
Zinc Coatings. Zinc, a natural, healthy, and abundant element was first used in construction in 79 AD. Zinc metal has a number of characteristics that make it a well-suited corrosion protective coating for iron and steel products.
Is zinc good for corrosion?
Zincsexcellent corrosion resistance in most environments accounts for its successful use as a protective coating on a variety of products and in many exposure conditions. This proven corrosion resistance is a result of zincs ability to form dense, adherent corrosion byproducts, which leads to a rate of corrosion considerably lower ...
Is zinc corrosion reactive?
While a fresh zinc surface is quite reactive when exposed to the atmosphere, zinc corrosion products develop rapidly on the surface as the coating is exposed to natural wet and dry cycles in the atmosphere. These corrosion products, collectively known as the zinc patina, act as an additional barrier between the steel and the environment.
Can zinc be used as a protective coating?
Some zinc coatings will be eliminated by the nature alone, (zinc coating processes limited to small parts or sheet steels cannot be considered for the protective coating of structural steel members); others may be ruled out based on cost, appearance, availability, etc.
How thick is hot dip galvanized zinc?
It varies. A typical thickness for hot dip galvanization is 10 μm. [ 1] For electrodeposited zinc, ASTM B633 specifies thicknesses ranging from 5 μm, for mild service conditions, to 25 μm, for very severe conditions. Other galvanization processes can produce thicker zinc coatings, as I’ll describe shortly for some real components.
How much zinc is in a G60 coating?
The density of zinc is 0.258 lb/in^3, so a G60 coating would be 0.30oz / 16 = 0.01875 lb per square foot on each side, which is 1.302x10^-4 lb/in^2.This is 1.302x10^-4 / 0.258 = 5.047x10^-4 inches (0.0128mm) thick
Why is zinc a sacrificial material?
Zinc is a sacrificial material to prevent rusting of iron since zinc is more reactive than iron. Once the zinc coating is penetrated in any way the zinc corrodes preferentially to iron, that is, it is “sacrificed” in order to protect the iron.
What is the G60 on a galvanized sheet?
Those numbers refer to the total amount of zinc deposited on both sides of the sheet. G60 means a total of 0.60 oz of zinc per square foot (0.30 oz on each side). G140 means 1.40 oz per square foot, and so on.
How long does zinc galvanize last?
As an aside, in the above SEM micrograph, the 85 μm zinc thickness gives about a 60 year service life (time to 5% surface rusting) in an industrial environment. [ 2]
What is a barrier coating?
In contrast to this are coatings that are called “barrier” coatings that protect by preventing the oxygen from getting to the iron. This is typically a chrome plating. But if you notice, if the chrome plating gets scratched or a pit, then that it will corrode because the oxygen can reach the iron.
What does "adjust" mean on a dry film thickness gauge?
For a dry film thickness gauge, this would mean an adjustment to zero on the uncoated surface or to known thicknesses such as shims.
How is galvanized steel made?
Galvanized steel is produced by hot dipping steel into molten zinc at 455 C. The steel reacts with the molten zinc to form an outer coating that is approximately 95% zinc and 5% steel. This galvanized coating is very strong, and can withstand the stress of transport and handling quite well.
What happens when you put zinc in acid?
After being placed in the acid, the metal was much less shiny and weighed less. While the acid ate away at the zinc coating on the surface of the metal, the solution bubbled vigorously, indicating that a gas (hydrogen) was being released.
Does zinc prevent rusting?
Rusting is an electrochemical process, and the presence of the zinc coating prevents the iron from rusting as long as any zinc coating is left at all. Unless properly coated, one problem that can occur with galvanized steel is delamination (blisters or flaking from the surface).
What is the weight of zinc on both sides of a galvanized steel sheet?
According to ASTM A 653, a G90 coating designation means the weight of zinc on both sides of a steel sheet is 0.90 oz/ft². However, a magnetic thickness gage measures only one side.
How to measure galvanizing thickness?
There are four ways to measure the thickness of galvanizing: magnetic principle thickness gages. stripping and weighing. weighing the part before and after galvanizing.
Why is magnetic thickness measurement used?
Because it is non-destructive, magnetic thickness measurement is the most common method of evaluating galvanizing coating thickness.
What does coating thickness gage reading mean?
Measure the galvanized part. The coating thickness gage reading indicates the thickness of the applied galvanizing.
How thick should a sandpaper be?
Thickness should be between 1.4 and 3.9 mils (35 and 100 µm) depending on the coating grade.
What is galvanizing steel?
Galvanizing is the process by which a sacrificial anode layer of zinc is applied to the surface of a fabricated steel part to provide corrosion protection . The final step in this process is the inspection of:
How thick should a specimen coating be?
The specimen coating thickness shall be the average of a minimum of 5 readings at widely dispersed points.
What does galvanized mean?
Galvanization is when a protective zinc coating is applied to steel or iron to prevent rust. The most common method is hot-dip galvanizing. This is when the metal parts are completely immersed in the molten zinc bath. Galvanizing (also known as electro galvanizing) is the process of applying zinc by using an electrical current. Although it does provide some protection against rust, its thinner coating is not as rust resistant as hot-dip galvanized. Its main advantages are cheaper and easier to weld.
What is hot dip galvanized?
Hot-dip galvanized or galvanized can be used in any building from small nuts and bolts to the girder. The steel is placed in a large bath, where it is coated. If it is galvanized, it will be dull gray and a bit rough. Galvanized products will have gloss and smoothness. Even if it is a bit ugly, hot-dip galvanized products still have the best rust protection.
Is electro galvanized hot dip?
Electro galvanizing is another term for galvanizing. Therefore, when you see "galvanized", use the newly acquired knowledge to ensure that it is hot-dip galvanized rather than electro-galvanized.
What is the most common method of achieving thicker galvanised coatings?
This is the most common method of achieving thicker galvanised coatings. Grit b lasting to Sa 2½ (ISO 7079) the steel surface prior to immersion, using chilled angular iron grit of size G24, roughens and increases the surface area of steel in contact with the molten zinc.
How is coating thickness determined?
Coating thicknesses are normally determined by the steel thickness and are set out in EN ISO 1461. There are three exceptions to this rule, the first produces a slightly thinner coating, the other two increase it.
What happens when you remove reactive steel from a zinc bath?
However, the reaction rate in these steels can be so high that this pure zinc layer is transformed completely to zinc-iron alloy before the article has had time to cool.
When the reaction between iron and zinc has virtually ceased and the article is taken out of the galvanizing bath answer?
In reality there is no demarcation between steel and zinc but a gradual transition through the series of alloy layers which provide the metallurgical bond.
Why is it important to ensure careful preparation of steel components?
For best results it is just as important for the customer to ensure careful preparation of the steel components as it is to ensure that the construction and design are suitable for galvanizing.
Is there a delimitation between steel and zinc?
In reality there is no demarcation between steel and zinc, but a gradual transition through the series of alloy layers which provide the metallurgical bond.
Does silicon slow down the growth of zinc?
Silicon changes the composition of the zinc-iron alloy layers so that they continue to grow with time and the rate of growth does not slow down as the layer becomes thicker. To a lesser degree, phosphorus exerts a similar influence on the formation of the coating.
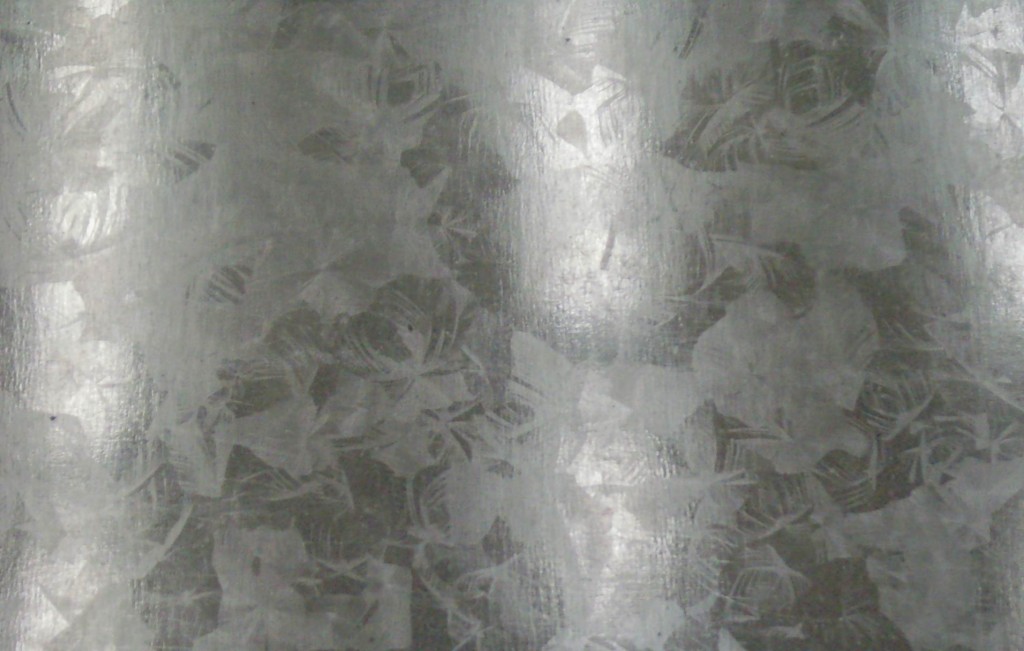