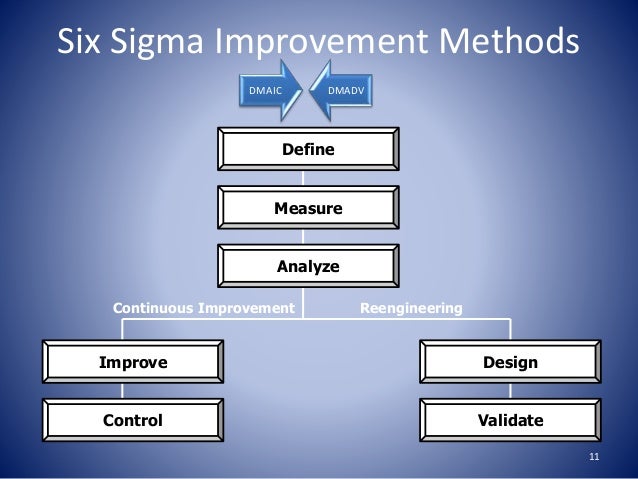
Here are the 8 principles of total quality management:
- Customer-focused: The customer ultimately determines the level of quality. ...
- Total employee involvement: All employees participate in working toward common goals. ...
- Process-centered: A fundamental part of TQM is a focus on process thinking. ...
What are the pros and cons of Total Quality Management?
The seven principles which form the base of ISO 9000 are:
- Customer focus: Companies should focus on meeting customer expectations and it should be the only first and foremost motive.
- Process-centric: Management of all activities and resources should be done as a system-wide process.
- Leadership: To drive companies toward their objectives and maintain the right internal environment, good leaders are required.
What are the objectives of Total Quality Management?
What are the principles of TQM?
- Customer focus. Central to all successful TQM systems is an understanding that quality is determined by the customer. …
- Employee involvement. …
- Centred on process. …
- Integrated system. …
- Strategic & systematic approach. …
- Decision-making based on facts. …
- Communication. …
- Continuous improvement.
What is Total Quality Management and why is it important?
Your answer should explain the chosen principle and why/how it relates to what is being discussed.
- An ice cream shop owner notices that over the past few months, the number of people who order the rocky road ice cream has been declining. ...
- Your boss decides to put together a team to try to come up with ways to make better use of new technology to make your product faster.
- You work for a firm that sells pharmaceuticals. ...
What companies have implemented Total Quality Management?
With fear of closing down, Xerox fought back using TQM to regain their market share. They implemented TQM by opening the Palo Alto Research Center (PARC), which focused on ways to emerge as a leader in the printer/copy/fax market. Their main goal: “Innovation is everywhere; the problem is learning from it.”
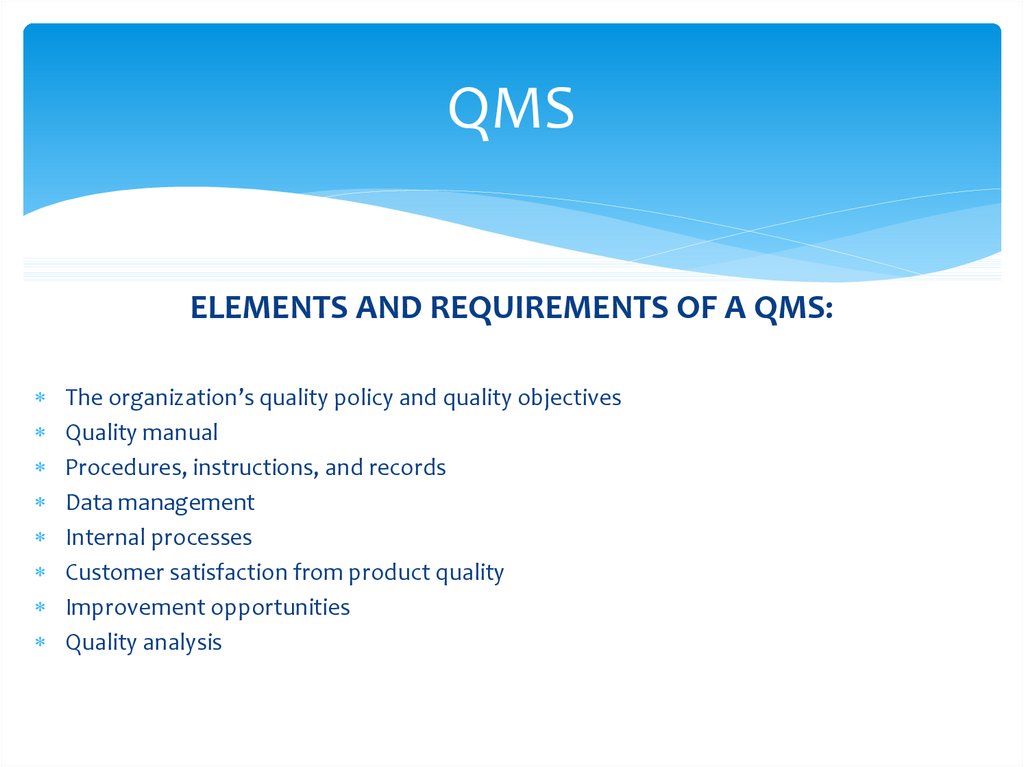
What are the approaches to quality management?
4 Approaches to Quality ManagementI. Cost-effect approach.II. Product-based approaches.III. User-based approach.IV. Fail fast, Fix fast, Recover Fast.
What is total quality approach give example?
Total Quality Management Example: TQM Example: One of the most famous examples of total quality management is Toyota. Toyota implemented Kanban System to make its assembly line more efficient. The company decided to keep just enough inventories to fulfill customer orders as they were generated.
What are the key elements of the TQM approach?
To successfully implemented TQM organization should focus on 6 key elements: Confidence, Training, Teamwork, Leadership, Recognition and Communication (Bhat et. al., 2009). It is a result of integrity and ethics of the organization without trust cannot be built within the work of TQM.
What is the Deming approach to total quality management?
Deming promoted the Plan-Do-Check-Act approach to process analysis and improvement. Emphasize training and education so everyone can do their jobs better. Use kaizen as a model to reduce waste and to improve productivity, effectiveness, and safety.
What is quality approach?
Quality Approach is a marketing research company that improves customer service and increases sales through mystery evaluations and customized training programs. QA has the skills and resources to help you look at your business as your customers do.
What is total quality approach essay?
TQM is a continuous quest for excellence that aims to improve the efficiency as well as the flexibility of any organization by integrating the different processes within the organization. This system makes the prevention of defects in the early stages and is highly customer oriented.
What is the main goal of TQM?
TQM is considered a customer-focused process that focuses on consistently improving business operations. It strives to ensure all associated employees work toward the common goals of improving product or service quality, as well as improving the procedures that are in place for production.
What are the 4 principles of TQM?
Key Principles of TQMCustomer focus. Central to all successful TQM systems is an understanding that quality is determined by the customer. ... Employee involvement. ... Centred on process. ... Integrated system. ... Strategic & systematic approach. ... Decision-making based on facts. ... Communication. ... Continuous improvement.
What are the five 5 major elements of TQM?
There are five major steps to TQM, and each are essential to successful implementation.Commitment and Understanding from Employees. ... Quality Improvement Culture. ... Continuous Improvement in Process. ... Focus on Customer Requirements. ... Effective Control.
What is the Deming Cycle approach?
The Deming cycle is a continuous quality improvement model which consists of a logical sequence of four key stages: Plan, Do, Study, and Act.
What is Deming's quality theory?
Edward Deming's Belief. W. Edwards Deming is considered by many to be the father of the total quality management movement. All of W. Edwards Deming's theories are based on the simple concept that continual improvement can help increase quality while decreasing costs, or what we can call total quality management.
What is Crosby approach?
Crosby's approach revolves around Zero Defects. Doing things right the first time is always cheaper than trying to fix defects. after they have been created. Thus, quality is free. According to Crosby, costs of poor quality are higher than organizations realize.
What is TQM management?
TQM can be summarized as a management system for a customer-focused organization that involves all employees in continual improvement. It uses strategy, data, and effective communications to integrate the quality discipline into the culture and activities of the organization. Many of these concepts are present in modern quality management systems, ...
What is TQM in business?
What is Total Quality Management (TQM)? A core definition of total quality management (TQM) describes a management approach to long-term success through customer satisfaction. In a TQM effort, all members of an organization participate in improving processes, products, services, and the culture in which they work.
What is strategic management?
Strategic and systematic approach: A critical part of the management of quality is the strategic and systematic approach to achieving an organization’s vision, mission, and goals. This process, called strategic planning or strategic management, includes the formulation of a strategic plan that integrates quality as a core component.
What is self managed work teams?
Self-managed work teams are one form of empowerment. Process-centered: A fundamental part of TQM is a focus on process thinking. A process is a series of steps that take inputs from suppliers (internal or external) and transforms them into outputs that are delivered to customers (internal or external).
What is the primary principle of total quality management?
Primary Principles of Total Quality Management. TQM is considered a customer-focused process and aims for continual improvement of business operations. It strives to ensure all associated employees work toward the common goals of improving product or service quality, as well as improving the procedures that are in place for production.
What is TQM approach?
The standards set as part of the TQM approach can reflect both internal priorities and any industry standards currently in place. Industry standards can be defined at multiple levels and may include adherence to various laws and regulations governing the operation of the particular business.
What is TQM in management?
Total quality management (TQM) is a structured approach to overall organizational management. The focus of the process is to improve the quality of an organization's outputs, including goods and services, through continual improvement of internal practices. The standards set as part of the TQM approach can reflect both internal priorities and any industry standards currently in place.
What is TQM used for?
With this in mind, TQM is used in many industries, including, but not limited to, manufacturing, banking and finance, and medicine. These techniques can be applied to all departments within an individual organization as well.
What is TQM in manufacturing?
While TQM originated in the manufacturing sector, its principles can be applied to a variety of industries. With a focus on long-term change over short-term goals, it is designed to provide a cohesive vision for systemic change. With this in mind, TQM is used in many industries, including, but not limited to, manufacturing, banking and finance, and medicine.
Who developed TQM?
TQM was developed by William Deming, a management consultant whose work had a great impact on Japanese manufacturing. 1 While TQM shares much in common with the Six Sigma improvement process, it is not the same as Six Sigma. TQM focuses on ensuring that internal guidelines and process standards reduce errors, ...
What is TQM in Toyota?
Perhaps the most famous example of TQM is Toyota's implementation of the Kanban system. A kanban is a physical signal that creates a chain reaction, resulting in a specific action. Toyota used this idea to implement its just-in-time ( JIT) inventory process.
What is the primary focus of quality management?
Customer Focus: The primary focus of quality management is to meet customer requirements and to strive to exceed customer expectations. Leadership: Leaders at all levels establish unity of purpose and direction and create conditions in which people are engaged in achieving the organization’s quality objectives.
What is TQM in business?
As a quality management technique, TQM involves all workers to maintain high standards of work across the entire company. Implementing TQM can help improve employee productivity, increase customer satisfaction, and achieve competitive advantage. Total Quality Management (TQM) Diagram.
Why is ISO 9001 important?
Total Quality Management is important because it provides an agile framework to implement effective quality and productivity initiatives in every aspect of business operations.
What is TQM certification?
TQM certification is a business course usually offered by educational institutions to equip people with Total Quality Management principles for practical application in the workplace. Since TQM is an approach to quality management, organizations cannot be TQM-certified, nor is it currently administered by any certifying body.
What is CWQC in TQM?
In Total Quality Control, Feigenbaum introduced the concept of Company-wide Quality Control (CWQC) which is agreed upon by some experts as the most direct inspiration for TQM. When searching for 3 total quality management principles, his 3-step approach to improving quality might be one of the first ideas that come to mind:
When was TQM first developed?
While there has yet to be a single authoritative resource, it is widely accepted that TQM first manifested as early as the mid-1920s, when Walter Shewhart formulated a statistical sampling technique for quality control which was eventually known as Statistical Process Control (SPC).
What is organizational commitment?
Organizational Commitment: All members of the organization, including office staff, engineers, and shop-floor workers have significant roles in improving business quality. Motivating and continuously training the entire workforce shows commitment toward the improvement of product or service quality.
What is total quality management?
Total quality management meaning refers to an approach wherein each employee at every level in a business is accountable for evaluating products and services per quality standards and customer needs.
What is the first principle of total quality management?
Hence, the first among the total quality management principles is customer focus. It means the end product must meet the demands and needs of the customers.
What is TQM in business?
TQM is a business management approach that entails every employee at every level of the organization feeling accountable for removing the production errors and ensuring the quality of the products and services per customer needs. The error-free production process reduces product and service costs.
What is TQM in manufacturing?
It is a successful management approach commonly employed in industries, such as manufacturing. As part of the quality improvement planning process, the executives train the workforce from different departments about the process standards and define business goals. Not only does TQM help an organization meet customer expectations, ...
What are the benefits of TQM?
Let us have a quick look at the benefits of the TQM: 1 Error prevention and elimination 2 Guaranteed customer retention 3 Reduced service costs and increased profits 4 Feedback from all stakeholders 5 Involvement and empowerment of employees at every production level 6 Improved market image 7 Customers becoming the main focus 8 Meeting consumer expectations leads to increased customer satisfaction 9 Improved organizational culture 10 Enhanced stakeholder relationships 11 Boost in employee morale 12 Continuous efforts to meet the quality standards 13 Increased stakeholder value 14 Innovative strategies and creative ideas
What is TQM in organizations?
When implementing TQM, organizations need to create an environment where their employees will feel empowered. They, along with management, become responsible for assessing the quality of the products and services at their levels. Here, organizational communication plays a vital role in boosting employee morale.
Who proposed sampling based quality inspection?
American statistician Dr. W. Edwards Deming, who proposed sampling-based quality inspection through his Statistical Quality Control theory, first conceptualized the TQM strategy. He also contributed toward introducing quality control in the quality management measures of the Japanese manufacturers in the 1950s post-World War Second.
Total Quality Management Defined
The key to be successful in any marketplace is to never get complacent. To that end, total quality management is an organization-wide effort to create a constant thrust towards improvement.
History of Total Quality Management
The roots of total quality management can be traced back to the economic instability of the late 1970s and into the early 1980s. It was at this time that the dominance of North America and Western Europe was challenged by competition from the East, specifically Japan’s skill at making high-quality inexpensive products.
Key Concepts in Total Quality Management
The key concepts of total quality management developed by the U.S. Navy include:
Elements of Total Quality Management
As the methodology of total quality management moved from the military to the private sector, the key elements that make it up were further codified.
How to Implement Total Quality Management
Getting started with total quality management requires that the top management learn about the methodology, and then commit to it as one of the organization’s strategies. The organization writ large must then assess its customer satisfaction and quality management systems.
What is the goal of TQM?
Quality is from the overall goal of TQM: an increase in product quality and the value it can provide to customers. This managerial process can provide a variety of benefits to businesses that choose to employ the strategy:
What is strategic approach in TQM?
Strategic Approach. Just as TQM is process-based, it also heavily relies on strategic management of the many processes you’ve developed. By doing this, you can ensure that all teams are accurately sticking to their processes and producing products or services that will provide the most value to your customers.
How does TQM increase customer satisfaction?
TQM increases customer satisfaction as business changes and processes are enacted specifically to provide higher quality goods and increased value to customers. Higher quality products, in turn, increase sales as customers take notice of its worth.
What is TQM quality award?
This strategy focuses on using the criteria of a reputable TQM quality award to identify areas of improvement. It’s essentially using the rubric for awarding the prize as a guide to discovering and implementing changes within a business because the award criteria define success.
What is TQM process?
Firstly, Total describes the process as it involves all organization members, from order fulfillment to marketing to sales. Everyone is working towards the same goal, and all teams are accountable for results. Management stems from managers and executives overseeing the process, ...
What is the Guru approach?
The guru approach uses the knowledge and understanding of key thinkers of the quality management industry as a business’ North Star, so to speak, towards understanding any shortfalls. Since each person likely has their own interpretation, this method is valuable for organizations in a variety of industries as they can choose a leader that relates most to their needs.
Is TQM a new strategy?
If TQM is an entirely new strategy for you, it’s also new to your employees. Effective and consistent communication plays a large role in maintaining employee morale, especially for a new approach that may make your employees nervous. If everyone knows what’s going on, and how your processes are going, employees will feel more confident in their job processes rather than floundering in confusion.
What is TQM management?
TQM relies heavily on a strategic and systematic approach to accomplish the goals of an organization while achieving the established vision and mission. The management of this approach requires a strategic plan to be formulated with quality as the core component.
What is process in quality management?
Processes are a central focus of total quality management. Transforming inputs (both internal and external) into outputs to be delivered to customers is a process. The definition of each step of the process and continuously monitored performance measures detect the unplanned variation.
What is TQM in business?
Making large-scale changes in an established business can create difficulties with employees, customers and stakeholders. The TQM approach has an outline that, when followed closely, can create a happier, more empowered environment. Here are six steps to take to implement TQM:
How to implement TQM?
Making large-scale changes in an established business can create difficulties with employees, customers and stakeholders. The TQM approach has an outline that, when followed closely, can create a happier, more empowered environment. Here are six steps to take to implement TQM: 1 Once top management has decided to adopt the total quality management approach, they can evaluate their current quality management systems, customer satisfaction and culture. 2 After identifying and prioritizing customer demands, the company will adjust the products and services in response. 3 Management will outline the critical processes currently in use to meet customer needs and establish teams to focus on process improvement. 4 A steering committee will manage the momentum of the total quality management approach while managers contribute through coaching, training, planning and other methods. 5 Process standardization and management will continue daily while evaluation and revision will be conducted as needed. 6 Communication and feedback for employees and stakeholders will be continual and a recognition and reward process will be set up for a total commitment on all levels.
What determines the level of quality of a company?
The level of quality provided by a company is determined by the customer. A company can retrain the employees, focus on a top-quality design and embrace all forms of technology, but the customer will always determine whether the adjustments are worthwhile.
What is TQM in team?
Communication. TQM requires every team member to be at their best and to function as a value-adding member of that team. This means communication and transparency is a core tenet of successful TQM practices. Data-driven. TQM doesn’t employ guesswork.
Why doesn't TQM focus on a single department?
TQM doesn’t focus on a single department because the goal is to provide customers with a great experience from every level of the organization. Process-based. TQM focuses on the creation and implementation of processes that provide organizations with the ability to find success and repeat it.
What is the magic quadrant of ITSM?
The Gartner Magic Quadrant for ITSM is the gold-standard resource helping you understand the strengths of major ITSM software vendors, insights into platform capabilities, integration opportunities, and many other factors to determine which solution best fits your needs.
What is an error in quality management?
An error is an opportunity to assess a problem, but it’s also a chance to discover what is working. Total quality management practitioners should take advantage of errors as a chance to learn from their mistakes and find ways to avoid them in the future.
What is the most important aspect of delivering quality?
One of the most important aspects of delivering quality is managing errors. No matter how focused everyone is on driving quality, IT organizations will always run into one issue or another.
Is TQM a one and done process?
Constant improvement. TQM isn’t a one and done process. Perfection is impossible, so it must always be pursued to get the organization as close as possible to it.
