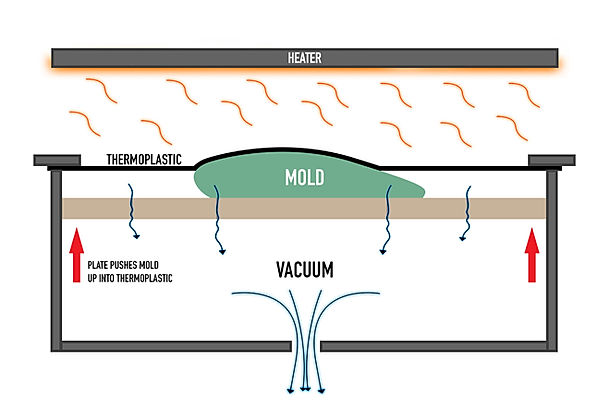
Conclusion
- Vacuum forming is an ancient technique that is used for manufacturing plastic products.
- It is the simplest form of thermoforming process which uses vacuum suction pumps for work.
- It has two types of molds: male mold and female mold.
- The vacuum forming process has the following steps for manufacturing
What are the advantages and disadvantages of vacuum forming?
What Are the Advantages and Disadvantages of Vacuum Forming? Advantages Disadvantages Excess plastic can be recycled into more sheets for future production needs Excess moisture can cause unwanted bubbles to form Supports rapid prototyping processes Clear or light-colored parts can show debris from the mold.
What products are made using vacuum forming?
Vacuum formed products & applications
- Agriculture. The agricultural industry use vacuum formed plastics for a variety of different uses – from components for vehicles used solely for transportation, to large parts for heavy duty agricultural ...
- Automotive and transport. ...
- Construction Machinery. ...
How much does vacuum forming cost?
How expensive is vacuum forming? A typical mold used in thermoforming costs $4,000-$7,000 for 0.015-inch tolerance (3 x 4 foot mold) or about $8,000 for 0.005-inch tolerance on cut tolerances compared with $50,000 to $100,000 for injection molds.
How does vacuum forming machine work?
What Are The Stages Of Vacuum Forming?
- First, a wooden mould is made. This is made in the shape to which the plastic will form around. ...
- The mould is then placed into the vacuum former oven. A plastic sheet is then clamped above, but not on the mould.
- In the oven, the heater is positioned above the plastic. ...
- After a few minutes, the plastic should be at a temperature to allow moulding.

How does vacuum forming work step by step?
The Six Stages of Vacuum FormingMake the mould. Firstly, a mould is constructed in the shape that the plastic will form around. ... Place the mould into the vacuum former. ... Position the heater above the plastic. ... Move the shelf towards the plastic. ... Switch the vacuum former on. ... Remove the sheet from the vacuum former.
Why do we use vacuum forming?
This is a clean way of removing vacuum formed parts from the material sheet. It doesn't require a special cutting tool to be made for an individual product and is therefore suitable for low volumes of parts where straight lines are no problem.
What type of process is vacuum forming?
thermoforming processVacuum forming is a thermoforming process in which a plastic sheet is heated to the desired temperature, and then moulded to a three-dimensional shape using vacuum technology and compressed air.
What is the process of vacuum molding?
Vacuum molding is a copying technique used to create a small series of functional plastic parts. The process involves using two-component polyurethanes and silicone molds for fast production of high-quality prototypes or end-use products.
What material is used for vacuum forming?
Materials for Vacuum Forming Acrylic (PMMA) Acrylonitrile butadiene styrene (ABS) Polycarbonate (PC) Polyethylene (PE)
What products are made by vacuum forming?
Numerous household items are made from vacuum forming plastic. Think about your own home; the plastic bathtub in your bathroom, the plastic utensils, and appliances that can be found in your kitchen, the garden equipment that is stored in the shed.
How thick can you vacuum form?
Vacuum forming sheet thickness may range from 0.0005 to 0.50 inch (0.0127 to 12.7 mm). However, for prototype applications, the Formech machines are limited to sheet thicknesses between 0.0005 to 0.25 inch (0.0127 to 6.35 mm). After a prototype is vacuum formed, it will shrink and grip the tool.
What temperature is needed for vacuum forming?
high-density polyethylene (HDPE), which requires a core temperature of approximately 280°F for optimal forming.
Can you vacuum form PVC?
Vacuum Forming This method is best for larger products where high levels of detail or sharply defined corners aren't necessary. In fact, polyvinyl chloride vacuum forming is used for things like bathtubs and shower trays.
Why is HIPs used for vacuum forming?
HIPs is ideal for vacuum forming plastic space saving nested packaging and containers. HIPs thermoplastic is widely used in the food packaging industry because of its unique qualities of strength, hygiene, visual appearance, and ability to retain heat, while also not deforming because of general warm water application.
What is the difference between vacuum forming and thermoforming?
Thermoforming is a process where thermoplastic sheets are heated to a pliable temperature, formed to a specific shape using a mold, and trimmed to create a finished product. Vacuum Forming takes it one step further. When the part is formed to the mold, vacuum pressure is added to assist with the molding of the part.
What is vacuum processing?
The “Good” Vacuum (Low Pressure) Processing Environment The vacuum processing system consists of a processing chamber, vacuum pumps with associated plumbing, an exhaust system, and a gas manifold system. Linear and rotational motion can be introduced into the chamber using mechanical or magnetic feedthroughs.
What temperature is needed for vacuum forming?
high-density polyethylene (HDPE), which requires a core temperature of approximately 280°F for optimal forming.
What Is Vacuum Forming?
Vacuum forming is a manufacturing method used to shape plastic materials. During the vacuum forming process, a sheet of plastic is heated and then pulled around a single mold using suction.
Why do manufacturers use vacuum forming?
Manufacturers often use vacuum forming to produce food-grade containers and parts for the medical industry because it is compatible with plastics that can be sterilized or kept free of contaminants. For example, high-density polyethylene (HDPE) is frequently used to vacuum form food storage containers.
How to vacuum form plastic?
The step-by-step vacuum forming process works as follows: 1 Clamp: A sheet of plastic is placed in an open frame and clamped into place. 2 Heat: The plastic sheet is softened using a heat source until it reaches the appropriate forming temperature and becomes pliable. 3 Vacuum: The framework containing the heated, pliable sheet of plastic is lowered over a mold and pulled into place via a vacuum on the other side of the mold. Female (or convex) molds need to have tiny holes drilled into crevices so that the vacuum can effectively pull the thermoplastic sheet into the appropriate form. 4 Cool: Once the plastic has been formed around/into the mold, it needs to cool. For larger pieces, fans and/or cool mist are sometimes used to speed up this step in the production cycle. 5 Release: After the plastic has cooled, it can be removed from the mold and released from the framework. 6 Trim: The completed part will need to be cut out of the excess material, and edges may need to be trimmed, sanded, or smoothed.
What is the difference between pressure forming and vacuum forming?
The main difference between pressure forming and vacuum forming is the number of molds that are used. Vacuum forming is the simplest type of plastic thermoforming, that uses one mold and vacuum pressure to obtain the desired part geometry.
What is thermoforming in manufacturing?
Thermoforming is a manufacturing process where a sheet of plastic is heated to become pliable, then shaped or contoured using a mold, and trimmed to create a final part or product. Vacuum forming and pressure forming are both different types of thermoforming processes.
Why is vacuum forming used in packaging?
Vacuum forming is often used for food packaging because it is compatible with food-grade plastic and can produce parts that are easy to sanitize. These ornate chocolates were produced in vacuum formed molds and are resting in a clear vacuum formed tray.
How long does it take to make aluminum molds?
Aluminum molds are more expensive and take longer to produce (turnaround time may be anywhere from two weeks to two months) than other tooling options. Because of this, cast or machined aluminum molds aren’t used as often for short runs or prototypes, but they are frequently used for large-scale production. Industrial vacuum forming machines often incorporate aluminum tooling because these molds are considered to have one of the longest lifespans of the tooling options available for vacuum forming.
How does vacuum forming work?
How vacuum forming works. Vacuum forming heats a plastic sheet until it becomes pliable, stretches the material onto a mold, and then uses vacuum pressure to obtain the desired part geometry. The simplest type of plastic thermoforming, vacuum forming uses wooden patterns and epoxy tools in addition to temperature-controlled aluminum tooling.
What is the difference between male and female vacuum molds?
With female molds, the thermoplastic sheet is placed inside the mold. Male molds are used when the inside dimensions of the plastic part are a priority. Female molds are used when outer dimensions are more important than inner dimensions.
What happens to the bottom of a mold after cooling?
The bottom of the sagging portion contacts the mold first and tends to retain its thickness. Material in the corners and at the top edges stretches the most and, therefore, thins the most. After cooling, the plastic part is removed from the frame and excess material is trimmed away.
What is billow forming?
With billow forming, the softened sheet is blown into a bubble with approximately the same surface area as the finished part. The pre-stretched sheet is then pulled against the mold walls by vacuum pressure to produce a part with less pronounced variation in wall thickness. If the depth of draw is especially deep, a plug assist may be used to facilitate an even distribution of material.
Can you use plug assist in straight vacuum forming?
Billow forming and plug assists are designed to yield more uniform wall thicknesses in the finished part. Plug assists can be used with billow forming, or with straight vacuum forming.
What is vacuum forming?
Vacuum forming is a simplified version of thermoforming, where a sheet of plastic is heated to a forming temperature, stretched onto a single-surface mold, and forced against the mold by a vacuum. This process can be used to form plastic into permanent objects such as turnpike signs and protective covers. Normally draft angles are present in the ...
When was vacuum forming invented?
Modern vacuum-forming equipment is based on a series of US patents awarded in 1950, 1964, and 1974.
What material is used for vacuum forming?
Suitable materials for use in vacuum forming are conventionally thermoplastics. The most common and easiest to use thermoplastic is high impact polystyrene sheeting (HIPS). This is molded around a wood, structural foam or cast or machined aluminium mold, and can form to almost any shape. This high impact material is hygienic and capable ...
What is composite mold?
Composite molds are a lower cost alternative to cast or machined aluminium molds. Composite molds are typically made from filled resins that start as a liquid and harden with time. Depending on the application, composite molds can last a very long time and produce high quality parts.
What is a machined aluminum mold?
Machined aluminium molds are like cast aluminium , but are cut out of a solid block of aluminium using a CNC machine and a CAD program. Typically, machined aluminium is used for shallow draw parts out of thin gauge material. Applications may include packaging and trays.
What causes webbing in mold?
Webbing can also occur when a mold is too large or parts of the mold are too close together. Finally, objects that are formed often stick to the mold, which is remedied by using a draft angle of three degrees or more in the mold.
Can you vacuum form wood?
Wood patterns are a common material to vacuum form as it is relatively inexpensive and allows the customer to make changes to the design easily. The number of samples that one is able to get from any pattern depends on the size of the part and the thickness of the material. Once the specifications of the part have been met, the pattern is then used to create a ceramic composite mold, or cast aluminum mold for regular production. Potentially, there are ways to create holes in plaster with a vacuum form if the replicated forms made from the vacuum form are deep enough and gaps are left between them for the plastic to form into. Then, once the plastic is used to cast a plaster mold, the deep plastic areas will leave holes if the mold is not completely filled.
What are the Advantages of Vacuum Forming?
When it comes to vacuum thermoforming, the possibilities are endless, and this has to be one of the great vacuum forming advantages. The process of heating up a sheet of thermoplastic and vacuuming it over a 3D shape allows the production of countless items – including a large variety of different shapes and sizes. It doesn’t matter if you’re looking to run a regular production line or if you’d like to create a custom one-off design, vacuum forming could be the answer.
What is vacuum formed?
Vacuum forming is one of those things that you’ve probably heard of, but you’re not really sure what it is or how it works. Yet look around in your daily life, and we guarantee, you will see vacuum formed products everywhere. From the traffic light housing you see on your way to work to the plastic bottle you drink from at lunch, these products are all made using a simple vacuum forming process. It is one of the most diverse and versatile plastic fabrication techniques on the market – transforming a single sheet of plastic into just about anything you could possibly want or need.
What is the bed size of a Talbot vacuum forming machine?
Our range of computer-controlled vacuum forming machines has a bed size of up to 70” x 46” and a draw depth of 14”+, which means we can manufacture a high quantity of products and successfully cope with different shaped and sized mouldings. We also employ a range of modern trimming band saws, ensuring that each item is finished to perfection. Here at Talbot Designs, we combine all the best available thermoplastic materials with the latest advances in vacuum thermoforming technology. Thanks to our in-house tooling and assembly department, we can monitor quality throughout the full vacuum forming process. Rest assured, items are produced to the best possible quality and they always meet our client’s exacting standards.
What is the second step of vacuum thermoforming?
The second step of the vacuum thermoforming process involves cooling and trimming . Once the plastic has set into the shape of its mould, it is taken out of the machine and any excess materials are removed. Numerous trimming methods can be employed and the type of equipment necessary depends on a variety of factors, including the type of cut, the thickness of the plastic and the production quantity. Holes, slots and cut-outs can also be drilled into the product at this stage and any other post- vacuum forming processes – such as decoration or assembly – can take place.
How to make a plastic sheet soft?
The first step involves heating up a plastic sheet. The sheet is heated uniformly over its entire surface area and throughout its thickness until it reaches its forming temperature; that is, the temperature at which the sheet becomes soft and pliable. It is then draped and stretched over a surface or a mould and a low-pressure vacuum is applied.
What materials are used to make thermoplastics?
Virtually all thermoplastics can be used in this process, but the more commonly used materials include acrylic, polyethylene, polycarbonate and polystyrene. We use them to make acrylic domes and polycarbonate domes.
Is vacuum thermoforming more economical than other plastic fabrication techniques?
The mould fabrication time is also reasonably short and therefore, overall, vacuum thermoforming is much more economical than other plastic fabrication techniques .
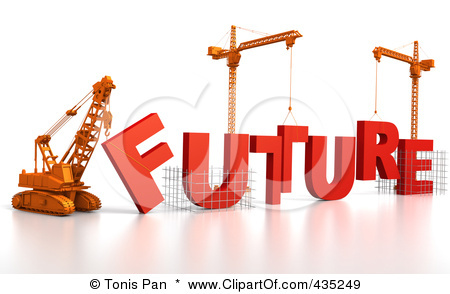
Overview
Vacuum forming is a simplified version of thermoforming, where a sheet of plastic (in various forms HIPS (High impact polystyrene) for low impact products, or for Bathroom shower trays ABS, and exterior vehicle parts HDPE, plus various other types of vacuum formable materials) is heated to a forming temperature, stretched onto a single-surface mould, and forced against the mo…
Typical applications
Original equipment manufacturers (OEMs) utilize heavy gauge vacuum formed components for production quantities in the range of 250–3000 units per year. Vacuum-formed components can be used in place of complex fabricated sheet metal, fiberglass, or plastic injection molding. Typical industry examples besides product packaging include: fascias for outdoor kiosks and automated teller ma…
Common problems
There are some problems encountered in the vacuum forming process. Absorbed moisture can expand, forming bubbles within the plastic's inner layers. This significantly weakens the plastic. However, this can be solved by drying the plastic for an extended period at high but sub-melting temperature. Webs can form around the mold, which is due to overheating the plastic and so must be carefully monitored. Webbing can also occur when a mold is too large or parts of the mold ar…
Types of molds
There are numerous patterns one can make with vacuum forming. The most inventive way to use vacuum forming is to take any small item, replicate it many times and then vacuum form the new pattern to create a more cohesive form. The vacuum forming helps tie the individual pieces together and make one mold out of many pieces that can easily be replicated. From there plaster, concrete, …
Finishing methods
Once a vacuum forming has been created out of a sheet of plastic, a finishing operation will be needed in most cases to turn it into a usable product. Common vacuum forming finishing methods include:
• Guillotining: The product is cut out of the sheet by pressing a blade through the product into a die underneath. This is a clean way of removing vacuum formed …
Further reading
• Soroka, W. Fundamentals of Packaging Technology, IoPP, 2002, ISBN 1-930268-25-4
• Walsh, D. E. Do It Yourself Vacuum Forming for the Hobbyist (rev. ed.), Workshop Publishing, Lake Orion, MI, 2002, OCLC 46798883
• Yam, K. L. Encyclopedia of Packaging Technology, John Wiley & Sons, 2009, ISBN 978-0-470-08704-6