
Thus, the speed of a DC motor can control in three ways:
- By varying the flux, and by varying the current through field winding.
- By varying the armature voltage, and the armature resistance.
- Through the supply voltage.
What is the speed control of a motor?
Introduction. When focusing attention on the speed control segment of the motor market, servo and stepper motors control their speed with a pulse train, while the induction motor and the brushless DC motor control speed with an external resistor and/or DC voltage. This article explains the structure, the speed control principle,...
What are the different types of AC speed control motor?
The "AC speed control motor unit" that uses the most popular single-phase capacitor-run induction motor, the small and highly efficient "Brushless DC motor unit", and the "Inverter unit" that combines a three-phase induction motor with a small inverter.
What are the speed control motor packages?
Our speed control motor packages include the motor, the driver (controller), and a potentiometer which allows for easy speed control adjustment. There are three speed control motor product groups.
How do you increase the speed of a DC motor?
Conversely, we may increase a DC motor’s speed (and reduce its torque output) by increasing the field control resistor’s resistance, weakening the stationary magnetic field through which the armature spins. Regulating field current may alter the balance between speed and torque, but it does little to control total motor power.
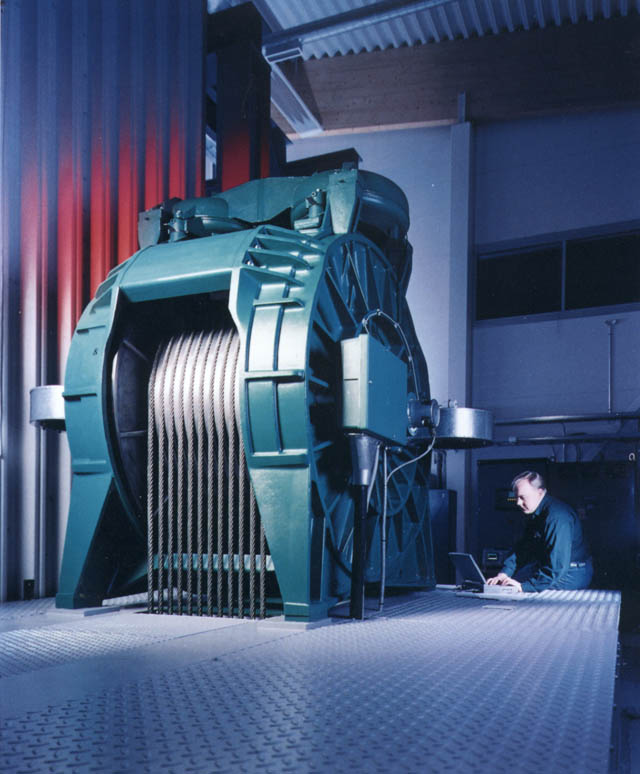
What kind of motors can be speed controlled?
There are three speed control motor product groups. The "AC speed control motor unit" that uses the most popular single-phase capacitor-run induction motor, the small and highly efficient "Brushless DC motor unit", and the "Inverter unit" that combines a three-phase induction motor with a small inverter.
Can any motor be speed controlled?
Depends on the type of motor. Brushed DC or universal can be controlled with a potentiometer. AC and brushless DC motors can't be controlled that way. They require a change in frequency, not a change in voltage.
Can all DC motors be speed controlled?
Accordingly, by adjusting the voltage applied to a DC motor, it can be made to run at any speed regardless of load torque. Linear or PWM control can be used to vary the motor drive voltage.
Can you put a variable speed control on any motor?
Variable frequency drives also control the speed of a motor, but they do so by changing the voltage and frequency and can thus only be used with AC motors.
What motor is best for speed control?
For applications where variable speeds are necessary, typically an AC motor with an Inverter or brush motors are used. Brushless DC motors are an advanced option due to their wide speed range, low heat and maintenance-free operation. Stepper Motors offer high torque and smooth low speed operation.
Can you put a speed control on a single-phase motor?
Speed control of single-phase induction motors is desirable in most motor control applications since it not only provides variable speed but also reduces energy consumption and audible noise. Most single-phase induction motors are unidirectional, which means they are designed to rotate in one direction.
Can any DC motor be variable speed?
A: In general if you don't do anything special to it, a DC motor will have variable speed. The main factors are the DC voltage applied to the armature coil and the amount of torque load you are trying to drive. In order to make it into a constant speed DC motor you have to have some sort of electronic feedback.
What DC motor is best for speed regulation?
DC Differential Compound MotorThe speed regulation of the DC differential compound motor is the best among all types of DC motors.The percentage speed regulation of the DC differential compound motor is in the range of 2-5 %.
Can you change RPM of electric motor?
Although they are constant speed devices, AC motor speeds can vary if the frequency, input voltage, or the windings that make the motor rotate are changed. A common and efficient means of changing a motor's speed is to vary the frequency by use of an inverter as the power source.
Can you put a speed control on a split phase motor?
Single phase split phase motors such as you make reference to have their speed controlled via the number of poles in the windings and cannot be speed controlled via other external means.
Can a VFD be used on any 3 phase motor?
Yes, a VFD can power a three-phase motor with a single-phase input power supply, but phase conversion introduces many considerations that normally don't factor in to buying a VFD.
How do you convert an electric motor to variable speed?
Alternating current electric motor speeds can be changed by the use of a frequency converter. This device changes the frequency of the alternating current to the motor. This then changes the rotating speed of the motor's internal magnetic field.
Can you adjust motor speed?
Although they are constant speed devices, AC motor speeds can vary if the frequency, input voltage, or the windings that make the motor rotate are changed. A common and efficient means of changing a motor's speed is to vary the frequency by use of an inverter as the power source.
Can you change the speed of a motor?
You increase the speed by increasing the frequency. If a motor base speed is 60 Hz, raising the frequency to 120 Hz will double the speed of the motor. However, if you do not keep the volt to hertz ratio constant, you will cause the motor windings to heat up.
Can any DC motor be variable speed?
A: In general if you don't do anything special to it, a DC motor will have variable speed. The main factors are the DC voltage applied to the armature coil and the amount of torque load you are trying to drive. In order to make it into a constant speed DC motor you have to have some sort of electronic feedback.
How do you control the speed of a universal motor?
Unlike an induction motor, a universal motor is easily speed controlled by varying its voltage. The RMS voltage of an AC line can be easily, albeit somewhat crudely, varied by chopping out pieces of the sinusoidal waveform. Modern semiconductor power devices quite easily enable such chopping.
What is a VSI?
Voltage Source Inverter (VSI) conversion functions similarly to that of the CSI – converting incoming AC to DC voltage. The difference is that the VSI uses a diode bridge rectifier to achieve the conversion. The bridge uses capacitors to maintain consistent DC voltage, as well as storing energy for the drive system.
How is the speed of a DC shunt motor controlled?
In a DC shunt motor where the field is in parallel with the armature, the speed is controlled by increasing or decreasing the applied voltage to the armature utilizing a rheostat.
How does speed affect armature resistance?
The speed of a DC motor is directly proportional to the back EMF. That means, when supply voltage and the armature resistance are kept constant, then the speed is directly proportional to armature current. Thus, if we add resistance in series with the armature, the current decreases, and therefore the speed will also decrease. Greater is the resistance in series with the armature, the greater the decrease in speed. In Armature Control Method a large amount of power is wasted and it is useful for small motors.
What is a shunt field?
The shunt field is given a fixed exciting voltage but varying voltages are applied to the armature. This voltage across the armature is controlled by suitable switchgear and the speed of the motor is generally proportional to the voltage across the armature.
What is pulse width modulation?
Pulse Width Modulation (PWM) employs a diode bridge rectifier, like a VSI, converting incoming AC voltage to DC. Ripples generated by the rectifier are smoothed out using the DC Link’s large capacitors. This ensures a stable DC bus voltage.
How to control speed of DC motor?
The speed of a DC motor can be controlled by changing the flux applied to it as the speed of the motor is inversely proportional to the flux per pole. To control the flux, a variable resistor or a rheostat is added in series with the field winding. Increasing the resistance will increase the speed as it will decrease the flux. In shunt motors, the field current is quite very small, so this method works quite efficiently. Flux control is an easy and convenient method for speed control as the power loss is small due to small because of the shunt field current.
What is Ward Leonard system?
Ward-Leonard system speed control of DC motors is used where very accurate speed control of the motor is required. In this method, the output from the generator is fed to the armature of the motor whose speed is to be controlled. The output voltage of the generator can be varied employing the field regulator from zero to its maximum value, thereby varying the armature voltage smoothly, which results in very smooth control of the speed of the DC motor.
How does reducing the resistance value of the diverter affect the armature current?
If so, then flux per pole must increase ( T α φIa) to maintain a constant torque.
How is the field winding excited?
In this method, the field winding is excited by a constant voltage but the armature winding is supplied with different voltages through switching devices. The speed of the motor will be proportional to the armature voltage.
How is resistance added in series?
In this method, additional resistance is added in series with the armature winding by using a rheostat. The current through armature is controlled with the rheostat and thus called an armature control method.
What happens to the armature voltage when switching devices?
Using the switching devices, the armature voltage is increased or decreased. With respect to the change in voltage, the speed varies. This method of controlling the speed is not much adopted in real applications.
What is a variable resistance called?
A variable resistance (Rheostat) called field diverter is connected across the series field winding. A portion of the current flowing through the series field winding is diverted into the field diverter by varying its resistance.
Why is diverter resistance not economical?
By using this method, the speed over a wide range can be obtained but below the normal speed. It is not economical due to considerable power losses in the diverter resistance. It is used in applications where slow speeds are essential at light loads.
What is armature control?
The armature control method is used where speed below the no-load speed is required. It also has poor speed regulation and low efficiency.
How is speed limited?
Speed is limited by the counter-EMF generated by the armature as it spins through the stationary magnetic field. This counter-EMF is directly proportional to armature speed, and also directly proportional to stationary pole magnetic field strength (which is directly proportional to field winding current in a motor that is not permanent-magnet) ...
Why is tachogenerator feedback important?
If the tachogenerator becomes disconnected – whether mechanically or electrically (it doesn’t matter) – from the drive, the drive will “think” the motor is not turning. In its capacity as a speed controller, the drive will then send full power to the DC motor in an attempt to get it up to speed. Thus, loss of tachogenerator feedback causes the motor to immediately “run away” to full speed. This is undesirable at best, and likely dangerous in the case of motors as large as the one powering this ship.
How does a field control resistor affect motor speed?
Decreasing the field control resistor’s resistance allows more current through the field winding, strengthening its magnetic field. This will have two effects on the motor’s operation: first, the motor will generate more torque than it did before (for the same amount of armature current) because there is now a stronger magnetic field for the armature to react against; second, the motor’s speed will decrease because more counter-EMF will be generated by the spinning armature for the same rotational speed, and this counter-EMF naturally attempts to equalize with the applied DC source voltage. Conversely, we may increase a DC motor’s speed (and reduce its torque output) by increasing the field control resistor’s resistance, weakening the stationary magnetic field through which the armature spins.
Why do DC motors lack windings?
Some DC motors lack field windings, substituting large permanent magnets in their place so that the stationary magnetic field is constant for all operating conditions. In any case, the operating principle of a DC electric motor is that current passed through the armature creates a magnetic field that tries to align with ...
What is a commutator?
However, a set of segmented copper strips called a commutator breaks electrical contact with the now-aligned coil and energizes another coil (or in the simple example shown above, it re-energizes the same loop of wire in the opposite direction) to create another out-of-alignment magnetic field that continues to rotate the armature. Electrical contact between the rotating commutator segments and the stationary power source is made through carbon brushes. These brushes wear over time (as does the commutator itself), and must be periodically replaced.
What is a variable speed drive?
What is ideally desired from a variable-speed drive is precise command over the motor’s speed. For this reason, most VSDs are designed to receive feedback from a tachometer mechanically connected to the motor shaft, so the VSD “knows” how fast the motor is turning. The tachometer is typically a small DC generator, producing a DC voltage directly proportional to its shaft speed (0 to 10 volts is a common scale). With this information, the VSD may throttle electrical power to the motor as necessary to achieve whatever speed is being commanded by the control signal. Having a speed-control feedback loop built into the drive makes the VSD a “slave controller” in a cascade control system, the drive receiving a speed setpoint signal from whatever process controller is sending an output signal to it:
How to control DC motor power?
In order to control the power output of a DC motor, we must also regulate armature voltage and current. Variable resistors may also be used for this task, but this is generally frowned upon in modern times because of the wasted power.
What is a DC motor?
First to begin with, an electric motor is a machine that uses electricity to turn a shaft, thereby converting electrical energy into mechanical energy. Electric motors are broadly divided into the following three types.
What is a brushed DC motor?
DC motors are further divided into brushed DC motors and brushless DC motors. Brushed DC motors have coils in their rotor, and alters the way current flows through the coils based on a mechanism using commutators and brushes. Brushed DC motors generate electrical and acoustic noise, and require frequent maintenance because their brushes and commutator are both consumable parts. But, they also feature a simple design and can operate without an electronic drive circuit if speed control is not needed.
Why does the speed of a motor change with load?
This is because the motor’s load torque varies due to the load itself, as well as other factors such as temperature, humidity, and changes over time. Simply driving the motor with a constant voltage will result in its speed fluctuating with changes in load.
What happens to the torque-speed curve when the voltage used to drive the DC motor is changed?
In other words, increasing the voltage shifts the torque-speed curve upward, parallelly. The torque-speed curve for a DC motor can be adjusted at will, by changing the voltage applied to the motor.
Why do DC motors make noise?
Brushed DC motors generate electrical and acoustic noise, and require frequent maintenance because their brushes and commutator are both consumable parts. But, they also feature a simple design and can operate without an electronic drive circuit if speed control is not needed.
How to change the voltage of a motor?
An alternative technique is the PWM control. The voltage applied to the motor can be varied by turning a semiconductor switch (such as a transistor or an FET) on and off at high speed, with the voltage being determined by the on and off pulse widths. The high efficiency of this technique makes it most commonly used nowadays.
How does increasing the voltage affect torque?
In other words, increasing the voltage shifts the torque-speed curve upward, parallelly. The torque-speed curve for a DC motor can be adjusted at will, by changing the voltage applied to the motor. Motor drive voltage and torque curve.
How does speed affect stepper motors?
Similarly, the speed of a stepper motor is proportional to the rate of input pulses. A higher pulse rate (higher pulse frequency) causes the speed of stepper motor rotation to increase proportionally. This motor speed (revolutions per minute, r/min, rpm) can be calculated as follows.
Why do stepper motors lose synchronization?
On the other hand, loss of synchronization between input pulses and motor rotation can occur due to overloading or sudden changes in speed.
What is a stepper motor?
Stepper motors are motors that rotate in fixed intermittent steps. The movement of the second hand of an analog clock is a familiar example of this feature in practice. The angle and speed of rotation of stepper motors can be controlled simply and accurately by means of input pulses. This capability is put to use in a wide range ...
What are the advantages of a stepper motor?
The main features of stepper motors are as follows. Advantages. Accurate positioning can be achieved using open-loop control. Angle of rotation is determined by the number of pulses (digital input), therefore position control is simple. Can rotate at low speeds .
How are stepper motors controlled?
Stepper motors are controlled by electrical pulses. The shaft of these motors rotate in a fixed angle, intermittently. Now, how is their speed controlled? This page provides a simple explanation of how to control the speed of stepper motors.
Why are stepper motors so good?
Their ability to provide simple and accurate positioning without the need for a sensor to detect shaft position, is one of the major advantages of stepper motors. Prone to loss of synchronization when the load changes unexpectedly, such as when operating at high speed or with sudden changes in speed.
What is the operation mode of a stepper motor?
There are two different operation modes for stepper motors, called the constant velocity motion profile , and the acceleration/deceleration motion profile. The former instantly changes speed of motor rotation. Also called the rectangular motion profile, this mode is restricted to the operating range within which the motor is able to self-start (get up to speed immediately). If sufficient torque is available for this acceleration, this mode is very simple with a constant rate of pulses.
