
Is concrete construction better than wood frame?
Wood frame buildings also don’t insulate noise as well as concrete buildings. Concrete is considered to be the premium when it comes to new developments as the overall maintenance over time is generally less and can better withstand the natural elements Vancouver weather throws at us.
How to install a wood subfloor over concrete?
- Lay the first layers of plywood with edges side by side to the wall without securing. ...
- Plywood panels should be placed with a 1/8″ gap amid sheets.
- Place the next layer at a 45-degree angle or straight to the first.
- Sections of plywood should be laid with 3/4” minimum extension space at all wall lines and vertical obstructions.
Which is best, a concrete or wooden gravel board?
- For example, if you have a stretch of ground 48 ft (15 m) long, you could use 8 posts spaced 6 ft (1.8 m) apart. ...
- Concrete gravel boards are easiest to install along metal posts with slots in the side. ...
- You could also fill the holes with gravel instead of concrete. It’s a possibility for wood posts. ...
What is the best floor covering for concrete?
What Type of Floor Is Good to Put Over Concrete?
- Engineered Wood. Engineered wood is real wood. ...
- Cork Flooring. Install cork flooring over concrete as long as the floor is level and clean. ...
- Laminate Flooring. Consisting of a wood-fiber center, a laminate floor plank is topped with a paper coating and the combinations are then sealed.
- Carpeting. ...
- Tiles. ...
- Decorative Concrete. ...

What wood should I use for concrete forms?
Plywood is the best material for building concrete forms because it retains its shape and integrity following prolonged exposure to wet concrete. Cut OSB panels tend to swell on exposure to water. Plyform panels are the best choice since they're specially engineered for concrete forming.
Can I use 2x4 for concrete forms?
Prior to placing concrete forms: Construct the form with 2x4 or 2x6 lumber and secure in place by wood stakes and deck screws. Excavate the slab area to a depth of about 7 inches, allowing 3 inches for a gravel base and 4 inches for concrete.
What materials can be used for concrete formwork?
In addition to timber, concrete formwork can be made out of steel, plywood, and fiberglass. These materials can be used separately or together. The most common type of concrete formwork used in heavy civil construction is steel!
Can you use plywood for concrete forms?
Nearly all types of plywood panels can be used in concrete-forming, from common roof and wall sheathing to sanded panels.
Does concrete stick to wood forms?
A variety of common household products will help keep concrete from sticking to wood. In most cases, you can prevent concrete from sticking to a mold by applying carnauba wax to the wood, but only if temperatures are above 50 degrees Fahrenheit.
Do you need rebar for 4 inch slab?
Rebar is not necessary for every concrete project. The general rule of thumb is that if you are pouring concrete that is more than 5 inches in depth, you are probably going to want to add in some rebar to help reinforce the entire structure.
Which material is most commonly used to make formwork?
TimberTimber as Formwork Material Timber is the most commonly used material for formwork.
Which material is used for formwork?
The original material used for formwork was timber, and it is still in use today. Other unfabricated materials such as steel are also used.
What are 2 types of formwork?
TypesTraditional timber formwork. The formwork is built on site out of timber and plywood or moisture-resistant particleboard. ... Engineered Formwork System. ... Re-usable plastic formwork. ... Permanent Insulated Formwork. ... Stay-In-Place structural formwork systems. ... Flexible formwork.
How thick should plywood be for concrete forms?
3/4-inchIt is normally 1-inch (3/4-inch dressed) tongue- and-groove lumber or 3/4-inch plywood. Concrete is plastic when placed in the form, so sheathing should be watertight. tongue-and-groove lumber or plywood gives a watertight surface. Reinforce sheathing to prevent bulging from the weight of the concrete.
How do you keep concrete from sticking to wood forms?
Fill a hand-pump sprayer with oil. Any type of oil will prevent concrete from sticking to wood. Spray the surfaces that will face the wet concrete with a heavy saturation of oil. Allow the oil to penetrate the wood for 15 to 20 minutes.
Can you use MDF for concrete forms?
Product Details. This MDF Bender Board product has a wide variety of applications. It can be used for curving concrete sidewalk forms as well as temporary landscape applications. It is made of 1/4 in.
Can you pour concrete 2 inches thick?
The minimum thickness for pouring concrete over concrete is 1.5 inches. In most cases, I don't like to pouring the new concrete less than 2 inches thick. Two inches of concrete (or more) that's bonded, gives you adequate strength for a wear surface, especially if you're driving over it.
Can you pour concrete directly on dirt?
Long story short, yes you can pour concrete over dirt.
How long should concrete cure before removing forms?
The forms or “molding” that holds the concrete in place until it dries should be left alone for at least two days to ensure that the concrete is completely dry. If the forms are removed too soon, the concrete can begin to sag, crack and collapse, especially if conditions like temperature affected its strength.
How do you keep concrete from sticking to forms?
In some instances, concrete will naturally bond to other materials. To prevent concrete from sticking to these materials, you need to treat them with a release agent to keep the concrete from sticking by forming a thin lubricant film over the material. When the concrete is dry, it's easy to separate.
What is plywood form?
Member manufacturers of APA−The Engineered Wood Association produce a variety of plywood form panel products—Plyform—designed for most general concrete-forming applications. Usually pretreated with a release agent to facilitate stripping, these panels are available in many grades from basic B-B to products with overlays ( i.e. Medium-density Overlay [MDO]) and High-density Overlay [HDO]) that add stability, resist abrasions, and provide a smoother and more durable forming surface.
What is class I plywood?
These panels are rated as Class I, which means they are manufactured with the strongest and stiffest veneers.
How many reuses can a B-B grade concrete forming panel withstand?
In fact, with proper care, some proprietary concrete-forming panels can achieve more than 100 reuses.
Why is it important to fasten form panels to framing?
For example, because panels absorb water, and the increase in moisture content usually causes the panels to expand and move , it is important to adequately fasten the form panels to the framing and to leave space between the panels that allows for their flatwise movement within ...
What factors affect the number of pours anticipated from concrete-forming plywood?
Many factors can affect the number of pours anticipated from concrete-forming plywood, including: desired finish on the concrete; durability of the panel’s surface, including overlays; types of concrete formulation; and. which release agents are used. The most critical factor is the handling and care of the form panels.
What to use to remove concrete from a panel?
only use non-ferrous wedges and tools ( e.g. wood or softer plastics) to remove excess concrete from the faces and edges of the panels; keep the panels stored face to face to protect cleaned surfaces; protect vulnerable corners and edges of panels during removal and handling;
Can plywood be used for concrete?
Nearly all types of plywood panels can be used in concrete-forming, from common roof and wall sheathing to sanded panels. APA Plyform panels, however, are specifically designed to withstand the wear-and-tear of repeated concrete pours, as well as to provide a smoother and more consistent finish to the concrete’s surface.
What is formwork in concrete?
Formwork can be classified in many ways: Type of material used. By the concrete element supported. Removable or permanent. Formwork has a fundamental role in concrete construction. It must have enough strength to bear all the loads present during casting operations, and must then hold its shape while concrete hardens.
What is timber formwork?
Timber Formwork. Timber formwork was one the first types used in construction industry. It is assembled on site and is the most flexible type, bringing the following advantages: However, before using timber its condition must be checked carefully, making sure it is free of termites.
What is concrete used for?
Concrete is one of the most widely used construction materials, thanks to its exceptional properties. However, to create building elements with concrete, it must be poured into a specially designed mold. This is known as formwork or shuttering. Formwork can use temporary or permanent molds, which hold the poured concrete in shape ...
What is ICF in construction?
Insulating concrete forms (ICF) are the most common type of permanent insulated formwork, where concrete structures are insulated with polystyrene boards that stay in place after concrete has cured. Permanent insulated formwork offers energy efficiency and sustainability, contributing to a lower environmental impact from the building sector.
Why is it important to consider the type of concrete and the pouring temperature?
When selecting formwork it is important to consider the type of concrete and the pouring temperature, since both affect the pressure exerted. Also, formwork must be capable of resisting the loads of wet and dry concrete.
What is another formwork called?
Another type of stay in place formwork is called coffor, which can be used in any type of building:
What is formwork made of?
This type of formwork is assembled from interlocking panels or modular systems, made of lightweight and robust plastic. Plastic formwork works best in small projects consisting on repetitive tasks, such as low-cost housing estates.
Why is timber used in concrete?
This is because timber is cost-effective, lightweight, durable, and flexible, allowing the concrete to shift while it sets without pieces breaking off or putting strain on the formwork. For the best results, invest in timber formwork that is easy to work with, lightweight, and dried thoroughly.
What is formwork made of?
Another type of material used to make formwork is resin-bonded plywood. These sheets of plywood will typically be attached to timber frames to create large, inexpensive concrete forms. However, plywood is less durable and rarely reusable.
What is insulating concrete?
Insulating concrete forms are essentially concrete walls that are poured between two layers of insulating material to create a strong and insulated foundation.
How long does it take for concrete to set?
Photo: istockphoto.com. Poured concrete is a viscous solution that can take up to 48 hours to properly set. During the setting time, the concrete needs to be contained in a concrete form. Concrete forms or formwork are the supporting materials or molds that are used when working with concrete. They also determine the final shape ...
What is concrete form?
A concrete form or formwork is a support or mold that the concrete is poured into. Temporary or permanent, the formwork is built into the shape that the user wants the concrete to take when the liquid concrete begins to dry. Photo: istockphoto.com. 2. Timber is the most commonly used material for formwork.
Why is concrete form important?
1. Concrete forms are necessary to ensure that the concrete sets properly during a construction project. Concrete is used regularly in construction projects. For example, it can be poured to create supports for a fence or gate or as a foundation for a new shed. However, when concrete is initially mixed, it isn’t a stiff compound ...
Can you use concrete slabs without formwork?
Many people either don’t know about concrete form s or they don’t want to have to pay for timber or plywood to set up formwork because the extra cost is too high. Unfortunately, without the use of formwork, it’s all too easy for construction projects to go awry, leaving the concrete slab for the new shed or workshop uneven and difficult to use as support. So, while it’s a bad idea to go without concrete forms, there are ways that can help save on the cost of these materials.
What is a good formwork?
Requirement for Good formwork ( Shuttering) A good formwork should satisfy the followings requirements: The material of the formwork should be cheap and it should be suitable for reuse several times. The form should be practically waterproof so that it does not leak and absorb water from concrete.
What are the advantages of steel formwork?
Advantages of steel formwork is given below: It can be used for many numbers of times, Stripping process is easy in steel formwork, A uniform charming and smooth surface finish by using steel formwork, The rigidity is high in steel formwork, Shrinkage or distortion is less in concrete by using it.
What is Formwork (Shuttering)?
Formwork (Shuttering) is temporary support as a mould for fresh concrete, in which concrete is poured and cast in the desired shape and gain initial strength, hardened and matured. Formwork is used in different shapes and sizes according to our construction elements in the form of PCC, RCC works in Building, Bridge, Tunnel Lining, Hydropower Dam, Irrigation Headwork, Sanitary Pipeline work, etc.
Why is it necessary to remove formwork?
In order to reduce the cost of form, it is necessary to design economical types of formwork and to mechanize its construction. We should have to remove the form work when concrete has reached a suitable strength. That process of removal of formwork is also called stripping.
How many times can you use a formwork?
These formworks can be re-used for 10 to 12 times .
What load can a concrete mixer carry?
It should easily carry the load of concrete and live load of pouring, vibration, compaction, and curing.
Is timber a formwork?
Plain concrete form. Above this, timber is normally used as formwork and it is also cheap. But there is the possibility of warping, swelling, and shrinkage of the timber is a drawback of timber.
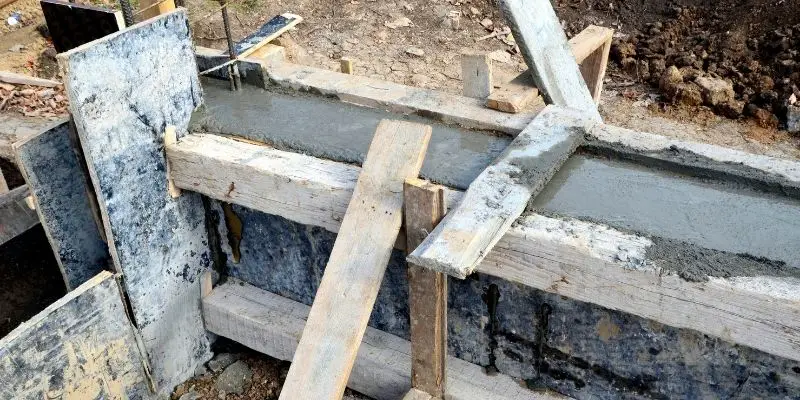