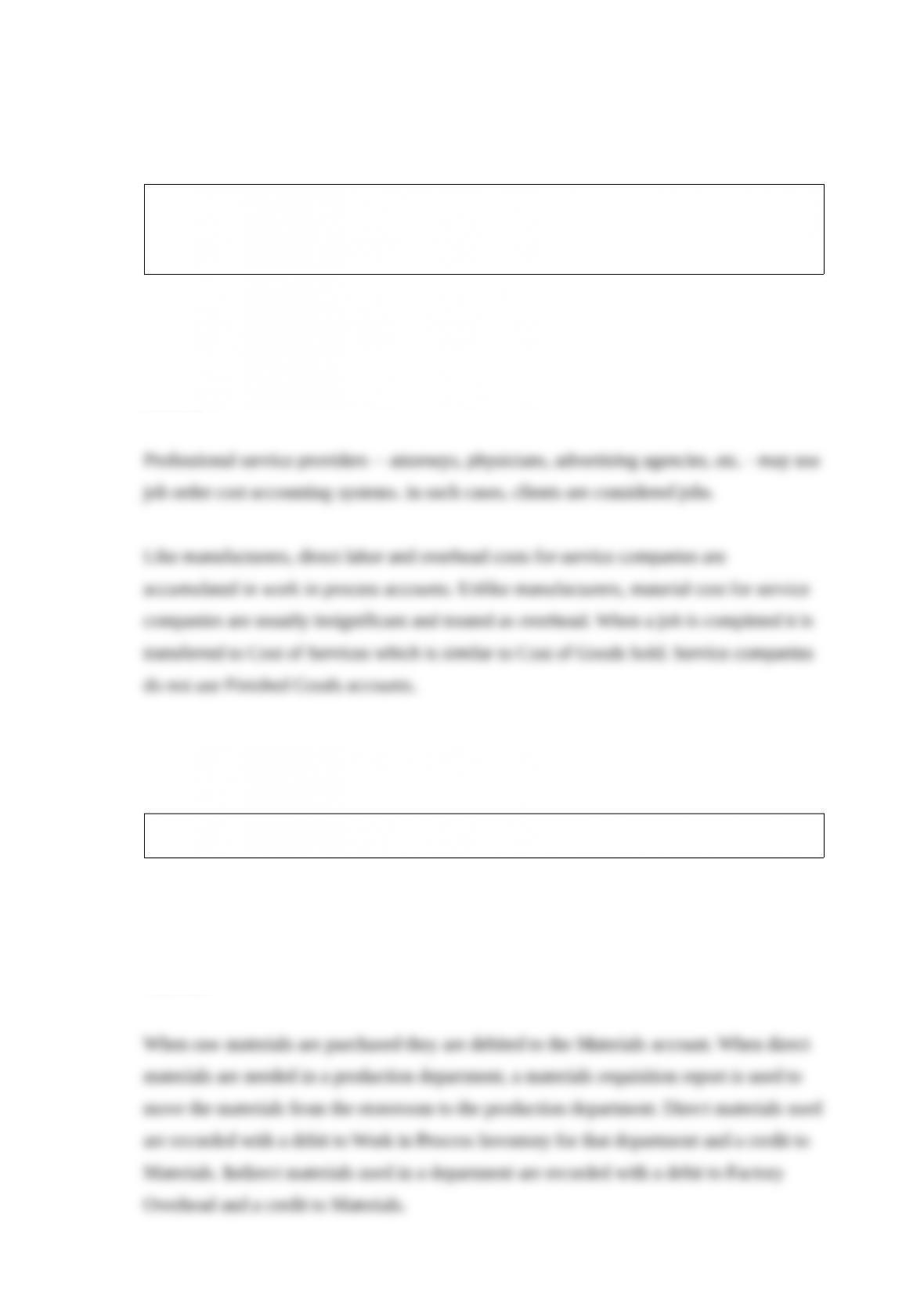
Similarities Between Job-Order and Process Costing •Both systems assign material, labor, and overhead costs to products and they provide a mechanism for computing unit product costs. •Both systems use the same manufacturing accounts, including Manufacturing Overhead, Raw Materials, Work in Process, and Finished Goods.
Full Answer
What is the formula for job order costing?
Job costing, also known as project-based accounting, is calculated by adding together costs for all the individual items categorized under three major areas of a project: labor, materials and overhead. The overall formula for calculating the cost of a job is: Total job cost = Materials + labor + overhead.
What are the main features of job order costing?
There are many similarities between job costing and contract costing, which are:
- (1) Both job costing and contract costing are specific order costing.
- (2) In the case of both job costing and contract costing, each job or contract constitutes a cost unit.
- (3) Both methods have the same object to find out cost and profit.
- (4) Under both the methods a separate account is opened. ...
How do you calculate job costing?
To calculate their job cost, they'll need to run the following calculation:
- 6 x 30 x $30 to determine the labor cost
- $4,000 for the material cost
- $8 x 6 x 30 for the overhead cost
Which would cost systems companies use, job order or process?
Key Takeaway. A process costing system is used by companies that produce similar or identical units of product in batches employing a consistent process. A job costing system is used by companies that produce unique products or jobs. Process costing systems track costs by processing department, whereas job costing systems track costs by job.
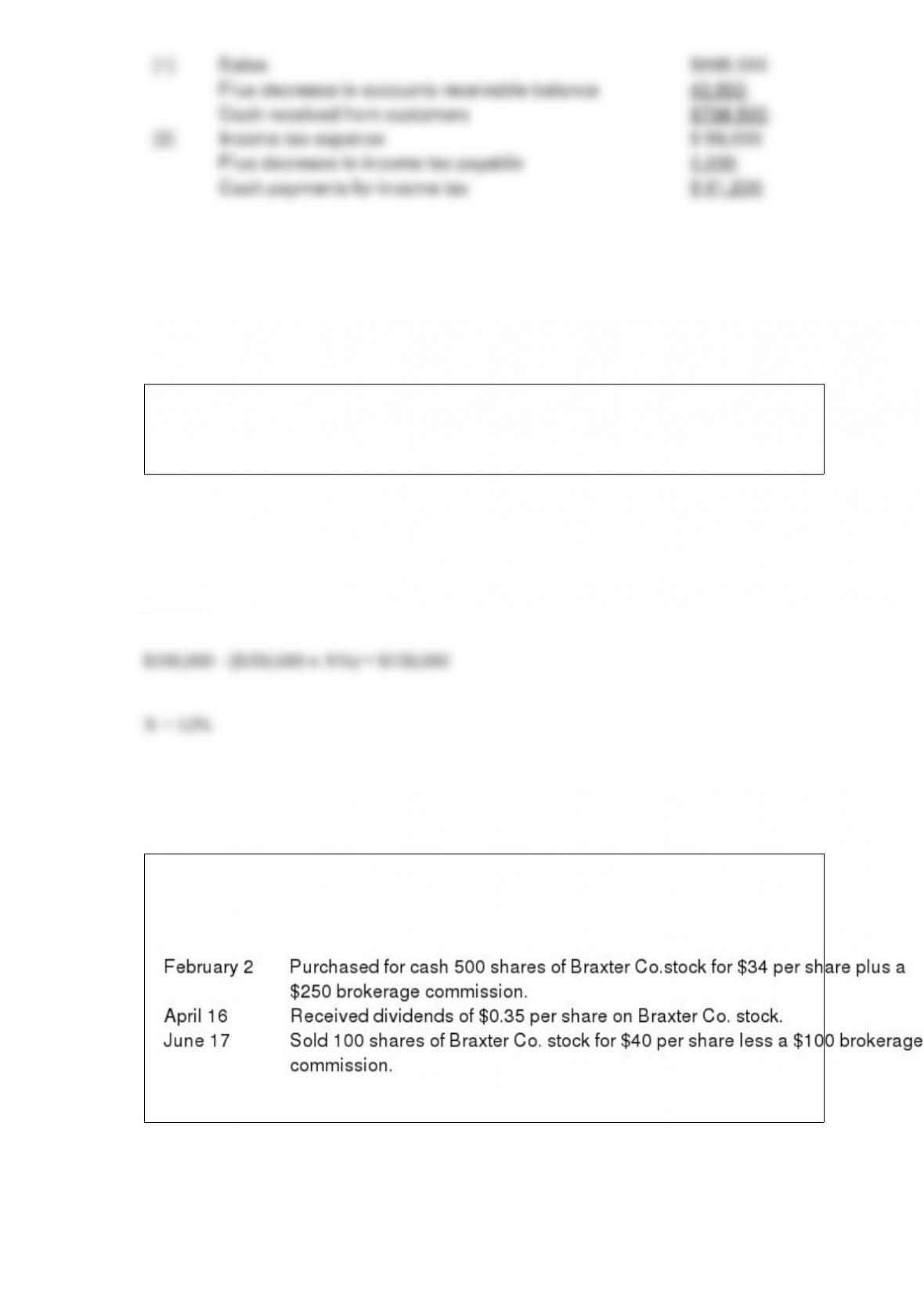
What are the similarities between job order and process costing?
Both process costing and job order costing maintain the costs of direct material, direct labor, and manufacturing overhead. The process of production does not change because of the costing method. The costing method is chosen based on the production process.
What are the similarities and differences between job order costing and process costing?
The job order costing is used for the costing of products that are more unique and customizable. This is usually applied to small production orders. The process costing is used for the costing of more standardized products that are usually produced in large volumes.
Which of the following are similarities between job order costing and process costing quizlet?
Which of the following are similarities between job-order costing and process costing? The flow of costs through the manufacturing accounts is basically the same for both costing systems. The same basic manufacturing accounts are used for both costing systems.
Which one of the following is considered a basic similarity between job order cost and process cost systems?
Terms in this set (8) Which one of the following is considered a basic similarity between job order cost and process cost systems? Unit cost computations.
What is the difference between job and process?
Question: What is the difference between Job and Process? Answer: A process refers to a program under execution. This program may be an application or system program. Job means an application program and it is not a system program.
Which of the following is a key difference between process and job order costing?
Which of the following is a key difference between process and job-order costing? Under process costing, it makes no sense to try to identify materials, labor and overhead costs with a particular customer order.
In what ways are job order and process costing similar quizlet?
Similarities between Process Costing and Job-Order Costing: 1.) Both systems assign material, labor, and overhead costs to products and they provide a mechanism for computing unit product costs.
How does the unit cost computation differ between job order cost systems and process cost systems quizlet?
In a job order cost system, the unit cost is the total cost per job divided by the units produced. In a process cost system, the unit cost is total manufacturing costs for the period divided by the equivalent units produced during the period.
Which of the following is a characteristic of process costing?
Which of the following is characteristic of a process costing system? Characteristics of a process costing system include repetitive operations, homogenous products and services, high production volume, low product flexibility, and high standardization.
Which of these best reflects a distinguishing factor between a job order cost system and a process cost system quizlet?
Which of these best reflects a distinguishing factor between a job order cost system and a process cost system? denominator of units produced during the period.
Can a company use both job order costing and process costing?
Your business can use job order costing and process costing to track production costs and allocate expenses, such as time, materials and labor, to your products, and both use about the same information to calculate unit cost.
What is the main factor for a company in choosing between the job order costing and process costing systems give two possible applications of each system?
The main deciding factor in choosing between a job order costing system or a process costing system is the type of product or service. Examples where a process costing system is likely appropriate include chemicals, cleaning fluids, mail processing, and oil refinement.
What is job order costing?
As you’ve learned, job order costing is the optimal accounting method when costs and production specifications are not identical for each product or customer but the direct material and direct labor costs can easily be traced to the final product . Job order costing is often a more complex system and is appropriate when the level of detail is necessary, as discussed in Job Order Costing. Examples of products manufactured using the job order costing method include tax returns or audits conducted by a public accounting firm, custom furniture, or, in a comprehensive example, semitrucks. At the Peterbilt factory in Denton, Texas, the company can build over 100,000 unique versions of their semitrucks without making the same truck twice.
When to use a job order cost system?
Thus, a job order cost system is used for custom jobs when it is easy to determine the cost of materials and labor used for each job. A process cost system is often less expensive to maintain and works best when items are identical and it is difficult to trace the exact cost of materials and labor to the final product.
Why does the process of production not change?
The process of production does not change because of the costing method. The costing method is chosen based on the production process. In job order cost production, the costs can be directly traced to the job, and the job cost sheet contains the total expenses for that job. Process costing is optimal when the costs cannot be traced directly to ...
Why does Nabisco use process costing?
In order to understand how much each product costs—for example, Oreo cookies— Nabisco uses process costing to track the direct materials, direct labor, and manufacturing overhead used in the manufacturing of its products.
What is the expense recognition principle?
The expense recognition principle is the primary reason to separate the costs of production from the other expenses of the company.
What is conversion cost?
Conversion costs are the costs necessary to convert direct materials into a finished product: direct labor and manufacturing overhead, which includes other costs that are not classified as direct materials or direct labor, such as plant insurance, utilities, or property taxes.
When is process costing used?
Process costing is used most often when manufacturing a product in batches. Each department or production process or batch process tracks its direct material and direct labor costs as well as the number of units in production.
What is the difference between job order and process costing?
The first is that the flow of units in a process costing system is more or less continuous, and the second is that these units are indistinguishable from one another. Under process costing it makes no sense to try to identify materials, labor, and overhead costs with a particular order from a customer ( as we do with job order costing ), since each order is just one of many that are filled from a continuous flow of virtually identical units from the production line. Under process costing, we accumulate costs by department rather than by order, assign these costs uniformly to all units that pass through the department during a period.
What is the key document controlling the accumulation of costs by a job?
Many different jobs are worked on during each period, with each job having different production requirements. Costs are accumulated by individual job. Job cost sheet is the key document controlling the accumulation of costs by a job. Unit costs are computed by job on the job cost sheet.
How are unit costs computed?
Unit costs are computed by job on the job cost sheet. A single product is produced either on continuous basis or for long periods. All units of product are identical. Costs are accumulated by departments. The department production report is the key document showing the accumulation and disposition of costs.
What are the basic functions of both manufacturing accounting systems?
Both systems have the same basic purposes-to assign material, labor, and overhead costs to products and to provide mechanism for computing unit product cost. Both systems use the same basic manufacturing accountants, including manufacturing overhead, Raw materials, Work in process, and Finished Good. The flow of costs through the manufacturing ...
What is the difference between job order costing and process costing?
One main difference between job order costing and process costing is the product type and the uniqueness of the product evaluated. Businesses use job order costing for small batches of customizable or unique products and individual job orders, while businesses use process costing for mass-produced or standardized products.
Why is job order costing important?
Job order costing is a way to track the production of small and unique batches of products ordered by customers. In a job order costing system, you can track the price of each individual project and ensure ...
What is cost accumulation?
The method of cost accumulation is also different for job order costing and process costing. In job order costing, costs accumulate by individual jobs. Typically, job costing includes customer billing to outline the exact cost of each step in the process of a particular job or order. In process costing, costs accumulate by each process or processing department and may not focus on the exact cost of each item in the process.
How many inventory accounts are there in a job order costing system?
In job order costing systems, there is usually one inventory account for each individual job. Job order costing typically requires more record keeping than process costing because businesses that use job order costing record materials and other resources for each item of a job. However, in process costing systems, ...
Why do companies use process costing?
Many large companies use process costing to account for factors such as the number of completed products they have .
What is process costing?
Process costing can also be useful for industries such as fuel , processed food, pharmaceuticals, paint, plastic or any other industry that produces large volumes of single or similar products.
Can you use work in progress in job order costing?
Typically, businesses are unlikely to use work in progress with job order costing. However, in process costing, businesses might record work in progress when products transfer between departments.
What is job costing?
Job costing is the cost of each job carried during an assignment or project. Whereas, process costing is the total cost of the processes carried out in the entire project.
When is job costing used?
Job costing is used in cases where products produced are unique, and process costing is used for the standardized products produced. In a job, casting losses can be segregated, but in the case of later losses are bifurcated on the bases of processes. Transfer cost is not considered in job costing when the job is shifted from one assignment ...
When is WIP present in costing?
In job costing, WIP may or may not be present, but for process costing, WIP may be present at the beginning and end of the period. Special treatment is required for each job in job costing, whereas in process costing, there is no need for special treatment for each process. Job costing each job is different from another, so it has individuality.
Does job costing have individuality?
But, later, products are produced in large volume, and consequently, therefore, it does not have individuality. In job costing, the time and materials are considered while calculating the cost of the job, so recordkeeping of all these things is an important and tedious task.
Is transfer cost considered in job costing?
Transfer cost is not considered in job costing when the job is shifted from one assignment to another. In the case of process costing, the cost of the previous processing stage is transferred to the next processing stage. There is less scope of reduction of cost in job costing, whereas for the process costing, there is a higher scope ...
Is each job considered an isolated project?
Each job is considered as an isolated project and a distinct entity for. Based on the client’s requirement. No job is the same and is heterogeneous, and each job will have to be done in a manner required to satisfy each job. The difference in work in progress exists in each period.
Can cost be transferred?
The cost cannot be transferred. The cost can be transferred from one process to another. Individuality. Since each job is different from another, all the products have their individuality. Products are produced in large volume, and consequently, therefore, they do not have any individuality.
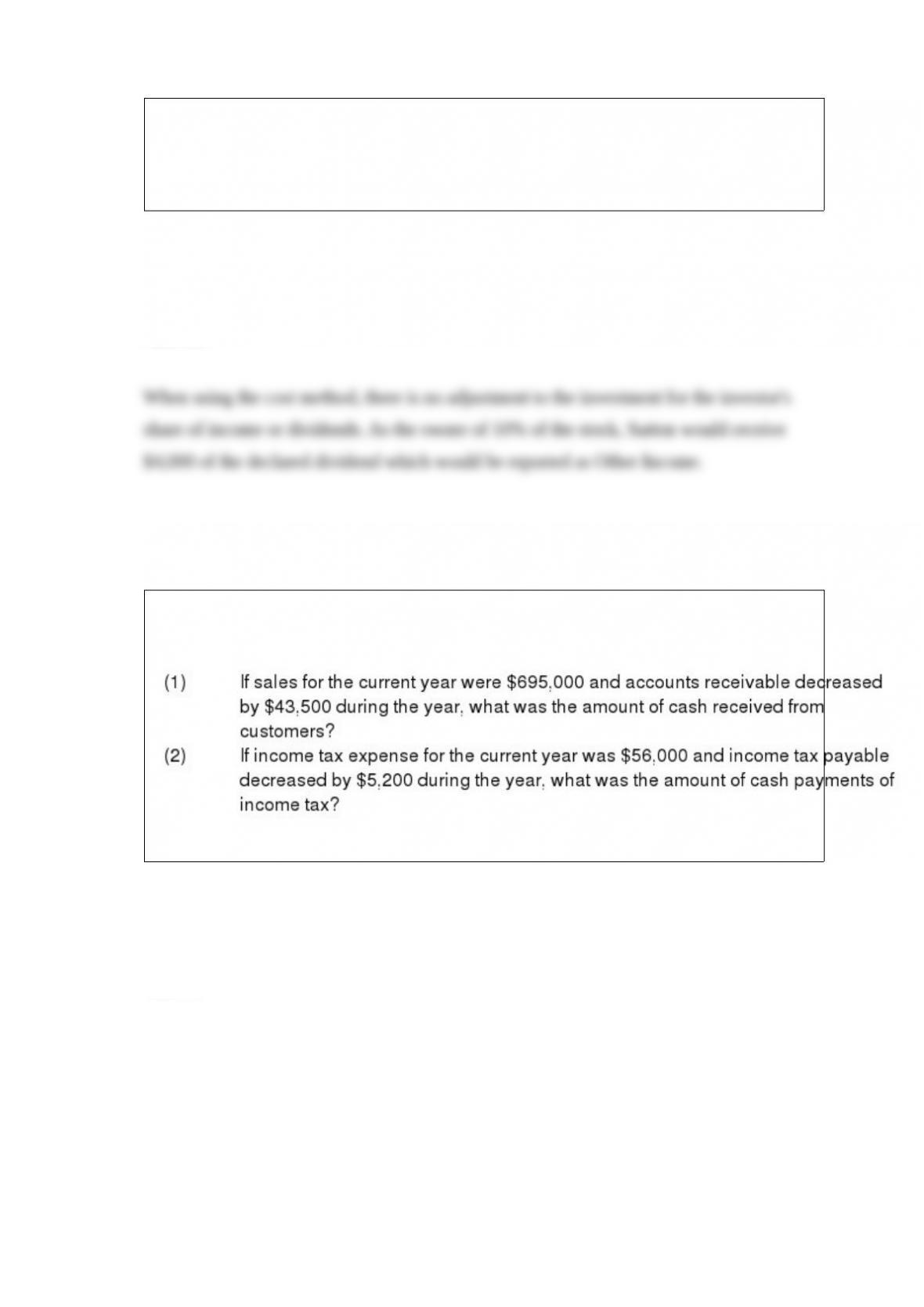