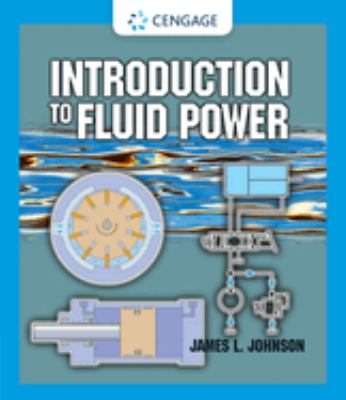
- Mobile: Fluid power is used to transport, excavate and lift materials as well as control or power mobile equipment. ...
- Industrial: Fluid power is used to provide power transmission and motion control for industrial machinery. ...
- Aerospace: Fluid power is used for both commercial and military aircraft, spacecraft and related support equipment. ...
What are the advantages of fluid power?
However, fluid power offers important advantages over the other technologies. Fluid power systems easily produce linear motion using hydraulic or pneumatic cylinders, whereas electrical and mechanical methods usually must use a mechanical device to convert rotational motion to linear.
Why is fluid power contamination control important?
Thus, keeping contaminants in check helps ensure components and systems perform as intended and last a long time, with minimal unscheduled downtime. Heed the following advice for proper fluid power contamination control.
What do you learn in fluid power?
Once they understand how the system operates and put it together, they use it to try to move specific pieces of material. Students learn about the fundamental concepts important to fluid power, which includes both pneumatic (gas) and hydraulic (liquid) systems.
Where can fluid power be used?
Safe in hazardous environments: Fluid power can be used in mines, chemical plants, near explosives and in paint applications because it is inherently spark-free and can tolerate high temperatures.
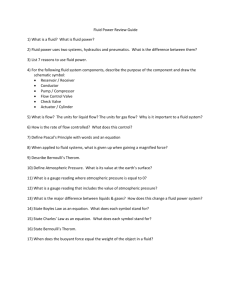
What are 3 benefits of fluid power systems?
Simple, Safe, Economical and Reliable –Hydraulic systems use fewer moving parts in comparison with mechanical & electrical systems. This makes them easier to maintain. Cost effective – As compared to pneumatic systems, hydraulic systems are less expensive.
What impact does fluid power have on our everyday lives?
Fluid power is in our ever day life. We see the use of fluid power in Cooling systems in most vehicles as it also is the heating system. Power steering systems in vehicles, Hydro electric generation, Lift tilt system on forklift and brake systems in cars. Fluid power helps us achieve everyday activities.
Which is an advantage of a fluid power system?
Another major advantage of fluid power is that pressure can remain constant without having to apply significant amounts of additional energy to the system. Hydraulic or pneumatic pumps are easier and more cost effective for tasks that require both pressure and position control.
What are the advantages and disadvantages of fluid power?
Advantages of hydraulic systems include power, accuracy, efficiency and ease of maintenance. But they disadvantages too: they can leak, which makes them messy, and the fluids inside them are often caustic to paint and some seals.
What uses fluid power?
Fluid power systems Are used in a variety of applications from braking systems on cars to robotics to heavy machinery. These systems produce linear motion using either hydraulic or pneumatic cylinders.
Why is hydraulic fluid important?
The major function of a hydraulic fluid is to provide energy transmission through the system which enables work and motion to be accomplished. Hydraulic fluids are also responsible for lubrication, heat transfer and contamination control.
Why hydraulic system is it important in the industry?
Hydraulic systems are capable of moving heavier loads as well as providing greater force than mechanical, electrical or pneumatic systems. The fluid power system means it can easily cope with a large weight range without having to use gears, pulleys or heavy leavers.
What are 5 Advantages of hydraulics?
Hydraulic System AdvantagesHydraulic systems are easy to control and accurate. ... Hydraulic systems are simpler and easier to maintain because these systems use less moving parts.Only hydraulic systems can deliver constant torque or force regardless of speed changes.Easy to spot leakages of a hydraulic system.More items...•
What is fluid power system?
Fluid Power is the technology that deals with the generation, control, and transmission of power, using pressurized fluids. Fluid power is called hydraulics when the fluid is a liquid and is called pneumatics when the fluid is a gas. Hydraulic systems use liquids such as petroleum oils, synthetic oils, and water.
Why choose fluid power systems over electrical or mechanical systems?
Fluid power systems generally can transmit equivalent power within a much smaller space than mechanical or electrical drives can, especially when extremely high force or torque is required. Fluid power systems also offer simple and effective control of direction, speed, force, and torque using simple control valves.
Why is hydraulic power especially useful with heavy work?
The favourable difference in power required to compress the liquid and the quantum of force delivered at the work end make hydraulic systems preferred over pneumatic system for heavy work.
What are the limitations of fluid power?
Limitations of Fluid Power Even though fluid power actuators themselves have a much higher power density than electromechanical actuators, hydraulic and pneumatic systems require a central power unit to convert electrical or mechanical power into pressure and flow.
What is fluid power?
Fluid power is energy transmitted and controlled by means of a pressurized fluid, either liquid or gas. The term fluid power applies to both hydraulics and pneumatics. Hydraulics uses pressurized liquid, for example, oil or water; pneumatics uses compressed air or other neutral gases.
Why is fluid power used in hazardous environments?
Fluid power can be used in mines, chemical plants, near explosives and in paint applications because it is inherently spark-free and can tolerate high temperatures.
How can fluid power be combined with other technologies?
Fluid power can be effectively combined with other technologies through the use of sensors, transducers and microprocessors. Read more : Difference Between Power System | Mechanical , Hydraulic , Electrical , Pneumatic. How fluid power works.
What are the components of a fluid power system?
A typical fluid power system includes the following components: Hydraulic pump or air compressor, which converts mechanical power to fluid power. Cylinder or motor, which converts fluid power to linear or rotary mechanical power. Valves, which control the direction, pressure and rate of flow.
What are the devices used to store fluid?
Sealing devices, which help contain the fluid. Accumulators and reservoirs, which store the fluid. Instruments such as pressure switches, gauges, flow meters, sensors and transducers, which are used to help monitor the performance of a fluid power system.
What is hydraulics used for?
The high levels of power that can be achieved through relatively simple means in hydraulics makes the technology ideal for certain types of heavy equipment, such as cranes, lifts, bulldozers, and diggers.
Which is more cost effective, hydraulic or pneumatic?
Hydraulic or pneumatic pumps are easier and more cost effective for tasks that require both pressure and position control. Compare this to an electric motor, which requires constant torque to drive and can lead to overheating if it is not limited by the control system.
Is fluid power a good energy source?
Even though it is not as popular as electromechanical energy, fluid power has many distinct advantages that make it ideal for different services. Additionally, there are many unique qualities to fluid power based machines, so it is essential to maintain the proper guidelines while creating them.
Is fluid power a hazardous material?
While fluid power lacks some of the hazards that are common with electrical machinery, it still maintains many of the same machinery-related opportunities for workers to come under harm and has some unique associated hazards.
What is fluid power?
Fluid power systems consist of multiple components that work together or in sequence to perform some action or work. People well versed in fluid power circuit and system design may purchase individual components and assemble them into a fluid power systems themselves. However, many fluid power systems are designed by distributors, consultants, ...
What are the components of a fluid power system?
The major components of any fluid power system include: 1 a pumping device — a hydraulic pump or air compressor to provide fluid power to the system 2 fluid conductors — tubing, hoses, fittings, manifolds and other components that distribute pressurized fluid throughout the system 3 valves — devices that control fluid flow, pressure, starting, stopping and direction 4 actuators — cylinders, motors, rotary actuators, grippers, vacuum cups and other components that perform the end function of the fluid power system. 5 support components — filters, heat exchangers, manifolds, hydraulic reservoirs, pneumatic mufflers, and other components that enable the fluid power system to operate more effectively.
Why is compressed air used in pneumatics?
Because compressed air can have a cushioning effect, it is often called on to provide a gentler touch than what hydraulics or electromechanical drives can usually provide. In many applications, pneumatics is used more for its ability to provide controlled pressing or squeezing as it is for fast and repetitive motion.
What is pneumatics used for?
And although pneumatics is capable of transmitting high force and torque, it is more widely used for fast-moving, repetitive applications, such as pick-and-place operations, gripping, and repetitive gripping or stamping. In both cases, electronic controls and sensors have been implemented into fluid power systems for the last few decades.
What is hydraulic system?
Hydraulic and pneumatic systems are both widely used in stationary (industrial) and off-highway (mobile) equipment. Hydraulic systems are widely used when heavy force or torque is involved, such as lifting loads weighing several tons, crushing or pressing strong materials like rock and solid metal, and digging, lifting, ...
What is a pumping device?
a pumping device — a hydraulic pump or air compressor to provide fluid power to the system. fluid conductors — tubing, hoses, fittings, manifolds and other components that distribute pressurized fluid throughout the system. valves — devices that control fluid flow, pressure, starting, stopping and direction.
How can pressurized fluids be transmitted?
pressurized fluids can be transmitted over long distances and through complex machine configurations with only a small loss in power. multi-functional control — a single hydraulic pump or air compressor can provide power to many cylinders, motors, or other actuators. elimination of complicated mechanical trains of gears, chains, belts, cams, ...
What is hydraulics?
To visualize a basic hydraulic system, think of two identical syringes connected together with tubing and filled with water (see Figure 1). Syringe A represents a pump, and Syringe B represents an actuator, in this case a cylinder. Pushing the plunger of Syringe A pressurizes the liquid inside.
What is pneumatics?
The principles of pneumatics are the same as those for hydraulics, but pneumatics transmits power using a gas instead of a liquid. Compressed air is usually used, but nitrogen or other inert gases can be used for special applications. With pneumatics, air is usually pumped into a receiver using a compressor.
Why is fluid power used?
In these cases, fluid power – whether hydraulic or pneumatics – is used because it can deliver linear and rotary motion with high force and torque within a smaller, lighter package than is possible with other forms of power transmission. A cement mixer, for example, illustrates how different methods of power transmission may be used.
What is fluid power?
Fluid power is a term describing hydraulics and pneumatics technologies. Both technologies use a fluid (liquid or gas) to transmit power from one location to another. With hydraulics the fluid is a liquid (usually oil but can be water) whereas pneumatics uses a gas (usually compressed air).
Why are pneumatics better than hydraulics?
Pneumatic systems are generally simpler because air can be exhausted to the atmosphere whereas hydraulic fluid usually is routed back to a fluid reservoir. Pneumatics also holds advantages over electro-mechanical power transmission methods. Electric motors are often limited by heat generation.
How does fluid power work?
Fluid power systems easily produce linear motion using hydraulic or pneumatic cylinders, whereas electrical and mechanical methods usually must use a mechanical device to convert rotational motion to linear .
What is pneumatics power?
The principles of pneumatics are the same as those for hydraulics, but pneumatics transmits power using a gas instead of a liquid. Compressed air is usually used but nitrogen, or other inert gases, can be used for special applications. With pneumatics air is usually pumped into a receiver using a compressor.
How much force can a hydraulic cylinder push?
For example, a hydraulic cylinder with a 25 cm diameter piston (19.34 square centimetres) and fluid pressure of 50 bar (5 MPa) can push with 9.815N of force.
What are the components of a fluid power system?
The major components of any fluid power system include: > A pumping device: a hydraulic pump or air compressor to provide fluid power to the system. > Fluid conductors: tubing, hoses, fittings, manifolds and other components that distribute pressurised fluid throughout the system.
Why is filtration important?
Filtration is essential to prevent damage from solid particles like dust and dirt. Solid particles traveling through a system can score and abrade surfaces, enlarge critical clearances, promote internal leakage and, in hydraulics, even act as a catalyst to chemically break down the fluid. Particulates come from several sources, including built-in debris left over after manufacturing components; by-products of normal internal wear and tear during operation; and dirt ingested from the outside environment. Filters trap such contaminants, but the necessary level of filtration varies with the application and system.
Why are filters installed in pneumatic systems?
In pneumatic systems, a number of filters are usually mounted throughout a circuit to protect individual machines and processes. They’re often installed in conjunction with regulators and sometimes lubricators, comprising an FRL. Keep in mind that contamination that is damaging in one system may be harmless in another.
Does running a system cleaner than necessary hurt the system?
Running systems cleaner than necessary does no harm to a system, but it wastes money. Also specify the right filter size. Select a filter for minimal pressure drop at the highest flow. Most manufacturers supply pressure and flow curves to rate pressure drop and dirt-holding capacity.
Is water a contaminant in a fluid power system?
Dry systems work best. Water is also a damaging contaminant in fluid power systems. Water vapor in the air is routinely drawn into compressors that raise the air’s pressure, temperature and dew point increase. Any subsequent cooling downstream can cause the water vapor to condense and liquefy.
Why do engineers use fluid power?
Engineers use fluid power to impact such areas as lowering fuel consumption in the transportation industries to improving patient care in the medical industries. Fluid power can improve our quality of life when engineers and researchers investigate how to use this technology to become more efficient, compact and cost effective.
What is fluid power?
Fluid power is all about moving energy from one location to another. Energy is the ability to do work. Energy transfer is the energy moving from the prime mover, or input source, to an actuator, an output device. Work is defined as force multiplied by distance.
What are the components of fluid power?
Both systems contain four basic components: reservoir/receiver, pump/compressor, valve, cylinder. Students learn background information about fluid power—both pneumatic and hydraulic systems—including everyday applications in our world (bulldozers, front-end loaders, excavators, chair height lever adjustors, door closer dampers, dental drills, vehicle brakes) and related natural laws. After a few simple teacher demos, they learn about the four components in all fluid power systems, watch two 26-minute online videos about fluid power, complete a crossword puzzle of fluid power terms, and conduct a task card exercise. This prepares them to conduct the associated hands-on activity, using the Portable Fluid Power Demonstrator (teacher-prepared kits) to learn more about the properties of gases and liquids in addition to how forces are transmitted and multiplied within these systems.
What is pneumatics in electrical?
pneumatics: The use of gas flowing under pressure to transmit power from one location to another. pressure: The force per unit area exerted by a fluid against a surface. pressure regulator: A type of pneumatic pressure control valve that controls the maximum pressure in a branch of a circuit.
