
MIG Welder Has Stopped Working
- Power Input: If your welder is not arcing, you may have an issue with the power input. ...
- Clogging/Contamination: A lack of arc in your welder can be caused by its consumable parts. ...
- Hot Electrode Holder: If your electrode holder heats up, there may be a connection issue. ...
Why won’t my MIG welder feed wire?
Over time, the liner will accumulate dust and grime, which can create wire feed problems. With the MIG welder not feeding wire, you should consider cleaning your feed liner. This can be done via pumping compressed air in short bursts to get rid of any clogged regions within the liner.
Why did my welder stop working?
Your welder may have stopped working because of insufficient power, or an inability for power to reach your machine. Clogging/Contamination: A lack of arc in your welder can be caused by its consumable parts.
What are the most common MIG welding issues?
This article will help you to identify and troubleshoot some of the most common MIG welding issues. Whether you are having issues with wire feed, splatter, or penetration, this will cover it all. Sometimes, small pockets of gas can get trapped in the weld metal. This is called porosity.
Why does my MIG welder spatter?
A voltage that is too high or too low can also cause spattering. Make sure that your amperage and voltage are finely tuned to your machine and project, and do not be afraid to do test welds. Make sure that you are using the shortest wire stick-out allowed for MIG welding.
What is one of the most common problems with MIG welds?
Porosity, one of the most common MIG welding defects, is the result of gas becoming trapped in the weld metal. Inadequate shielding gas coverage is among the biggest culprits, and this can be addressed in several ways.
How do you reset a MIG welder?
0:411:26Millermatic® 252 MIG welder system reset - YouTubeYouTubeStart of suggested clipEnd of suggested clipTurn the right knob clockwise until on is displayed depress the gun trigger. And the machine willMoreTurn the right knob clockwise until on is displayed depress the gun trigger. And the machine will reset to the factory default settings and return to the home.
Why does my MIG welder keep stopping?
Check your ground lead for worn or broken wires, dirty or contaminates clamps, and good tight spring tension. Make sure you are feeding the wire through your welder at the proper speed for your welding technique.
How do you troubleshoot a welder?
0:093:57How to Troubleshoot MIG Welding Problems - YouTubeYouTubeStart of suggested clipEnd of suggested clipBetween the gun and the drive rolls can also result in bird nesting. Other causes of bird nestingMoreBetween the gun and the drive rolls can also result in bird nesting. Other causes of bird nesting include too much Drive rule tension and the gun not inserted into the drive housing properly.
How do you set up a MIG Miller welder?
7:239:45Setting up your Millermatic 141, 190 or 211 MIG welder - YouTubeYouTubeStart of suggested clipEnd of suggested clipFirst select your material type and gas. Then select wire diameter. And choose your materialMoreFirst select your material type and gas. Then select wire diameter. And choose your material thickness. For all machines you can still use manual mode if you want to fine-tune your setting.
Can you do TIG with a MIG welder?
3:406:58TFS: HOW to convert your MIG into a TIG Welder - YouTubeYouTubeStart of suggested clipEnd of suggested clipMake sure you switch it over that way otherwise your fryin tungsten. Now you have essentially aMoreMake sure you switch it over that way otherwise your fryin tungsten. Now you have essentially a scratch start TIG with a MIG gun. This is pretty much what it looks. Like.
Why does my welder keep cutting out?
The simple answer is that if the welder is causing the breaker to trip, then it's trying to pull more power than the breaker can supply. This may be because the breaker doesn't support a high enough amperage for what the welder is pulling, or it could be that there's a defect in either the breaker or the welder.
Why does my welder keep sputtering?
When the power source senses the reduced current at the arc, it sends a surge of voltage in order to overcome the restricted current flow. This increased voltage causes the popping and sputtering that leads to poor and inconsistent weld quality.
How do you service a MIG welder?
0:311:35MIG Welder Maintenance Tips - YouTubeYouTubeStart of suggested clipEnd of suggested clipCheck gas hoses and fittings. Clean and tighten weld. Terminals. Compressed air through lines toMoreCheck gas hoses and fittings. Clean and tighten weld. Terminals. Compressed air through lines to remove any debris. Every six months clean the welder by blowing it off with compressed. Air remove.
Why is my MIG welder not sparking?
These are the 5 most common reasons why your welder won't spark: Metal connections areas are not clear or clean. The work lead clamp is not properly connected. Wire is faulty or rusted.
How do I know if my MIG liner is bad?
Poor or erratic wire feeding, a loss of amperage or frequent contact tip burnback are all signs of liner problems. Unfortunately, because of the time it takes to replace the liner, this is often one of the last components checked during a troubleshooting effort.
What causes MIG Burnback?
Burn back is a very common problem. It results when a weld forms in the contact tip. It usually occurs when the wire is fed too slowly or the MIG gun is held too close to the base metal.
Why is my MIG welder not feeding wire?
If your MIG welder wire feed motor not working, then it is impossible that you can create a continuous arc after your first spark. A welder that will not feed wire usually has one of the two things causing the issue. First, the tension of wire feed system is too loose. And the second one is that the welding tip is blocked by slag or you have burned the wire into it. For the ladder, just changing the contact tip will do the trick to get the machine up and running again.
Why doesn't my MIG welder make an arc?
The first and most common problem why usually MIG welder doesn’t make an arc is that the ground clamp is not attached to the base metal properly. Even experienced welders forget to attach the ground clamp to the workpiece, and if you think that’s the issue in your case, all you need to do is check the ground clamp whether it is connected properly ...
How many volts do you need for a MIG welder?
When using a small MIG welder you must have around 110-volt s to 120-volts, (you can check it using a multi-meter). A great idea would be to make sure that you have not blown the fuses.
Why is my welding tip stuck on the ladder?
First, the tension of wire feed system is too loose. And the second one is that the welding tip is blocked by slag or you have burned the wire into it. For the ladder, just changing the contact tip will do the trick to get the machine up and running again.
Why do drive rolls wear down?
Drive rolls are specially made to smoothly feed the electrode wire from the wire spool trough the gun cable, but if the tension of the drive roll is set too tight, the drive rolls will wear down quicker and it can cause rough wire feeding as well that can result in arc instability.
Can a MIG welder start an arc?
Bear in mind that a MIG welder requires clean base metals thus if you are trying to weld on a surface that has oil, zinc, old paint, rust, and other coatings your MIG welder may not start an arc, and even if it does, more than likely you will not get good penetration.
Is it okay to run fuses on an extension cord?
If your wire feed is working, then your fuses are okay! Another common problem is that you’re running to is small or too long of an extension cord. With this in mind, if you’re using an extension cord make sure that it is not too long to prevent any voltage drop.
MIG Welder Wire Feed Motor Not Working
Below, we have put together a guide to help you figure out the possible reasons why the wire feed motor in your MIG welder is not working.
2. Tension in the Spool and Drive Roller
Most Miller MIG welder wire feed problems arise at the point of your spool brake and drive rolls.
3. Gun Liner Maintenance
The gun liner needs to be squeaky clean if you want to avoid MIG welder wire feed problems.
Tools you need to fix this problem
Here are some of the things you may need before you start to check the possible causes and how to fix the wire feed motor of the MIG welder, which has stopped working.
1. wire quality
Does the quality of your wire matter when it comes to the issues of MIG welders? Some people may tend to overlook the fact that wire quality affects your wire feed motor and make it not work efficiently. Indeed, many MIG welder wire feed issues often arise at this point.
2. Tension in your spool and drive roller
Some of the MIG welder wire feed issues come at the point of the spool and drive rolls. When the tension is too much on your wire spool, it will automatically cause a short tear and wear; however on the other side of the tension is very little in your spool, you will encounter a bird’s nest mess for you to deal with.
3. Gun liner maintenance
The only way to avoid MIG welder wire feed issues is to ensure that the gun liner is squeaky clean. Again it must have an adequate matching size of the wire you are using.
4. Contact tip maintenance
One of the essential features of your MIG welder is contact tips. They are in direct contact with your welding puddle; hence they can be distorted over a certain period.
Why is there no fusion in MIG welding?
Cause: Cold lapping in the short arc transfer process is the most common cause for lack of fusion. This MIG welding defect occurs when the weld pool melts but since there’s not enough energy, it doesn’t fuse to the base plate. So the weld can look good, but the metal won’t actually be joined together.
Why does a MIG weld spatter?
This affects the weld appearance and the strength of the fusion. Cause: It can be caused by high wire feed speed and voltage settings. Other causes include the insufficient use of gas and dirty base material.
Why is my welding bead convex?
Cause: A convex bead indicates that the heat input settings are too low, meaning there’s not enough heat for the weld to penetrate the base metal. Solution: Check that you’re using a proper amperage setting for the metal you’re welding.
What is porosity in welding?
Porosity is small pockets of gas that get caught in the weld metal. It can occur internally, as well as on the surface on the weld bead. In both cases, it weakens the strength of the weld. Here are a few instances of what causes porosity in MIG welding.
Why does my GMAW gun get hot?
Cause: The copper strands that are located inside the gun tend to break and wear out with time. This results in faulty wire delivery. Solution: If during use you notice that a particular area of the gun gets very hot, it’s an indication of internal damage. So prevent GMAW welding defects, immediately replace the gun.
Why is my welding surface porosity?
Cause: One of the most common causes is improper surface conditions. For example, if you haven’t clean ed the surface and there was oil, rust or dirt left on it, it will prevent proper weld penetration, leading to porosity. Other welding processes, such as SMAW and FCAW have better tolerance to surface contaminants.
How to get a tangled wire out of a gun?
Solution: Flip up the drive roll and pull the wire out of the gun. Trim the tangled wire and re-thread it back to the gun. Also, check the tension and make sure that it’s not too high. Other solutions can include using a larger diameter wire and using a shorter distance between the wired feeds.
What causes a MIG welding defect?
Porosity , one of the most common MIG welding defects, is the result of gas becoming trapped in the weld metal. Inadequate shielding gas coverage is among the biggest culprits, and this can be addressed in several ways. First, check the regulator or flow meter for adequate gas flow, increasing it as necessary. Check the gas hoses and welding gun for possible leaks, and block off the welding area if drafts are present.
How to minimize MIG welding defects?
To minimize the time and money spent addressing MIG weld defects, take a systematic approach for troubleshooting each one should they appear. Look for any variables that have changed during the course of welding — such as parameters or welder technique — then consider these tips as potential remedies.
Why do weld beads have concave beads?
Concave weld beads are particularly prevalent when welding in vertical-down applications and are simply the result of working against gravity. Adjust the parameters to a lower setting so the weld pool is less fluid and more able to fill in the joint.
What is a convex weld?
Convex weld beads are high, rope-like welds that generally happen in flat and horizontal welding, but can also occur in fillet welds, when the parameters are too cold for the material. Convex weld beads normally have poor fusion of the toes. Increase the voltage to prevent convex beads.
Why does my welding arc not work?
It’s caused primarily by improper welding gun angle or incorrect travel speed . Avoid this problem by maintaining a 0- to 15-degree gun angle during welding and keeping the arc on the leading edge of the weld pool. It’s sometimes necessary to increase travel speed to maintain correct arc position. Insufficient heat in the weld can also cause lack ...
Why is welding a defect?
As with most things, welding is subject to human error from time to time. Weld defects are often caused by improper technique, parameters or equipment settings. When a weld defect appears, it's important for welders to have the knowledge to fix the situation as quickly as possible.
What causes burn through welding?
Burn-through, which happens when the weld metal penetrates completely through the base material, is especially common when welding thin materials less than 1/8 inch or about 12 gauge. Excessive heat is the main cause of burn-through, and this can be fixed by reducing voltage or wire feed speed.
Why is my MIG welder not feeding wire?
If you find your MIG welder not feeding wire, here are some of the places to look for commonly occurring issues: 1. The Spool Hub. The spool hub is the source of your wire feed. The spring system incorporated into the hub ensures a braking mechanism to prevent over spooling.
What happens if a MIG welder is not feeding?
If the wire in your MIG welder is not feeding properly, you may experience frustration and burnout , which can negatively affect the progress of your work.
What is a MIG wire feed problem?
MIG welder wire feed problems are a direct reflection of how well you maintain and look after your MIG wire feed welding machine. The proper and timely maintenance of the machine, as well as choosing the best consumables, can go a long way in determining the quality of weld it is capable of undertaking. In the end, wire feed problems are manageable.
Why is my welder wire rusty?
If you have not been using your welder for a while now, chances are, the wire feed has experienced weathering and may be rusty. This can cause the liner to clog up, creating wire feed problems. If you are sure there is rust on your spool, try unspooling the wire until you get to the point where there is no more rust.
What happens if the contact tip gets clogged?
Therefore, if the contact tip gets clogged or distorted, the welding pool and the formed bead will be affected.
How to check tension on a spool?
The best way to check the level of tension on your spool is to pinch it forward so that it reverts back into the feed with a snap. This pressure that the feed experiences will help you determine whether the spool requires any additional tension or not. 2. Drive Rolls Should Match the Wire.
Do drive rolls match wire?
Drive Rolls Should Match the Wire. It is important to understand that you are using the correct drive rolls according to the diameter of the welding wire. Most of the models tend to have provisions for running two different kinds of wire sizes. Make sure each of these is adequately aligned with the wire you are using.
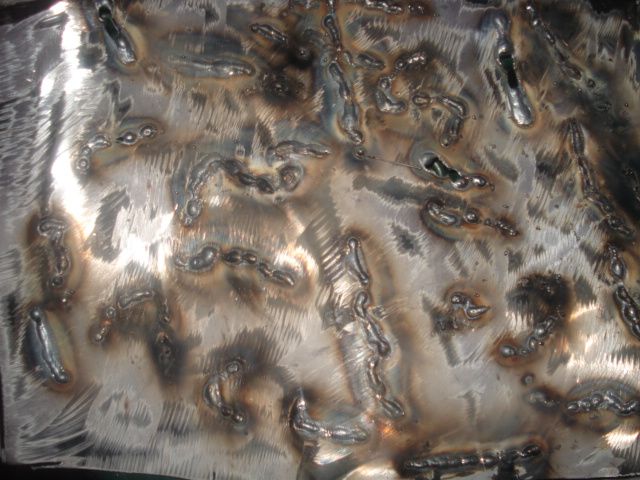