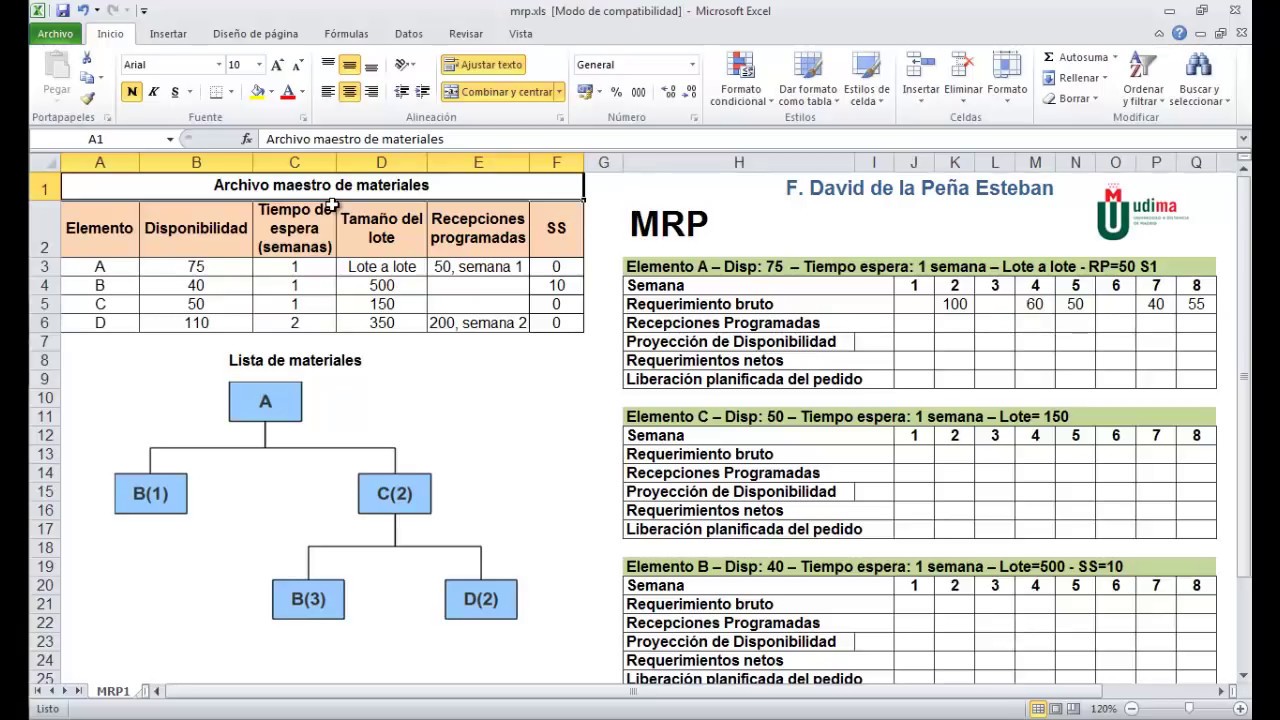
5 Reasons Why Manufacturing Businesses Should Use an MRP System
- 1. Inventory control from raw materials to finished goods Inventory management plays a significant role in achieving manufacturing efficiency. ...
- 2. Master production planning MRP systems identify bottlenecks in the production line caused by lack of material. ...
- 3. Resource management Raw materials are essential in any manufacturing process. ...
- 4. Data management ...
- 5. Time-saving ...
What are the benefits of Materials Requirements Planning (MRP)?
The benefits of materials requirements planning include the following: Inventory Levels - MRP enables inventory managers to be able to reduce the level of component parts and raw materials inventory. MRP systems work backward from production scheduling, in which it determines the amount of inventory needed to meet overall production demand.
What is MRP in manufacturing?
Material requirements planning (MRP) is a system that helps manufacturers plan, schedule, and manage their inventory during the manufacturing process. It is primarily a software-based system.
What is MRP II and why is it important?
To help companies make better decisions in these areas material requirements planning (MRP I) has been introduced in the 1960-s. While today it has evolved to manufacturing resource planning (MRP II), its core benefits are relevant more than ever.
What data must be considered in an MRP scheme?
The data that must be considered in an MRP scheme include: The final product being created. How much is required at a time. When the quantities are required to meet demand. Shelf life of stored materials. Inventory status records: Records of net materials available for use already in stock (on hand) and materials on order from suppliers.

Why do we need MRP?
Why is MRP important? MRP, which is done primarily through specialized software, helps ensure that the right inventory is available for the production process exactly when it is needed and at the lowest possible cost. As such, MRP improves the efficiency, flexibility and profitability of manufacturing operations.
What is the main purpose of material planning processes?
Main objective is to balance the demand for materials with the supply of materials.
What is the key of MRP?
There are three processing keys to choose from are net change planning (NETCH), net change planning in the planning horizon (NETPL), and online regenerative planning (NEUPL).
What is the most important output of the MRP?
- Planned order releases (MOST IMPORTANT OUTPUT OF THE MRP SYSTEM).
What is the main objective of the material planning process in an ERP system what are the basic questions addressed by material requirements planning?
What are the basic questions addressed by material planning? The main objective of material planning is to balance the demand for materials with the supply of materials so that an appropriate quantity of materials is available when they are needed.
What do you mean by material planning?
Materials Planning has been defined as the scientific way of determining the requirements of raw materials, components and other items needed for production within the economic investment policies. It is rather a sub system in the overall planning activity.
What is MRP in manufacturing?
To help companies make better decisions in these areas material requirements planning (MRP I) has been introduced in the 1960-s. While today it has evolved to manufacturing resource planning (MRP II), ...
What is MRPeasy software?
MRPeasy offers one of such readymade solutions. Our MRP software includes not only material requirements planning (MRP I) features, like inventory and supply chain management, but also cost control, equipment capacity planning, workforce control, payroll accounting, extensive statistics and more (MRP II). This makes it a single piece of software any small or medium manufacturer would need for their manufacturing resource planning.
How does material requirements planning work?
One of the simplest yet effective ways to ensure that there is enough material available for production is to use a “saw tooth” inventory management logic. Below is the descriptive image of how this logic works.
What are the biggest risks of not using any system for material requirements planning?
What are the biggest risks of not using any system for material requirements planning? The biggest would be of course not being able to meet contract obligations to supply product to the client at the agreed time. Customer is not interested to know the reason why the product that has been ordered long time ago has not arrived as promised. Most probably such a client will change to a new supplier entirely or will ask for substantial discounts in the future shipment. In both cases, this will have a highly negative impact on manufacturer’s business.
How does material management affect shipping?
In material management everything is interconnected, the amount of finished goods planned for shipping depend heavily on the amount of material being purchased for the future product batch. Knowing how much finished goods there will be available in the future, manufacturer can better plan its sales.
Why is knowing the quantity of finished goods important?
This is especially critical for businesses with several operational facilities in different countries. Knowing exact quantities and time when the products is being shipped helps manufacturers to save both on shipping and storage costs.
Why do companies need MRP?
MRP helps companies maintain low inventory levels.
Why is MRP important?
MRP helps companies maintain low inventory levels. Making a bad decision in any area of the production cycle will cause the company to lose money. By maintaining appropriate levels of inventory, manufacturers can better align their production with rising and falling demand.
What is the MRP step?
Check demand against inventory and allocate resources. This step involves checking demand against what you already have in inventory. The MRP then distributes resources accordingly. In other words, the MRP allocates inventory into the exact areas it is needed.
How does MRP work?
MRP works backward from a production plan for finished goods, which is converted into a list of requirements for the subassemblies, component parts, and raw materials needed to produce the final product within the established schedule.
What are the steps of MRP?
Steps of Material Requirements Planning (MRP) The MRP process can be broken down into four basic steps: Estimating demand and the materials required to meet it. The initial step of the MRP process is determining customer demand and the requirements to meet it. Utilizing the bill of materials—which is simply a list of raw materials, assemblies, ...
What is MRP in manufacturing?
Material requirements planning (MRP) is a system that helps manufacturers plan, schedule, and manage their inventory during the manufacturing process. It is primarily a software-based system. MRP's objective is threefold: Make sure raw materials are available for production when required.
What are the advantages of MRP?
Advantages of the MRP process include the assurance that materials and components will be available when needed, minimized inventory levels, reduced customer lead times, optimized inventory management, and improved overall customer satisfaction.
Common Problems
As a business grows, fragmented processes often develop with it. For example, those involved in production/manufacturing planning may use an Excel spreadsheet to track orders through the various stages of manufacture, but this will not talk to sales, warehouse or shipping—each of which may have their own system.
How and Why MRP Should Work
MRP or manufacturing resource planning takes ownership of the data from the quotation stage, through the sale, the raising of the works order, through all stages of production including the warehouse (goods in/out) and subcontracting, through to shipping and invoicing.
Summary
In short, businesses that will be successful are those that make the decision, stick with it and implement a MRP system in a swift but structured approach. A well implemented system does not have to cost a fortune and will be able to deliver quantifiable return on investment in a very short amount of time.
1. Inventory control from raw materials to finished goods
Inventory management plays a significant role in achieving manufacturing efficiency. MRP systems help you understand exactly how much inventory you need to meet your customers’ demand, reducing the inventory carrying costs. You keep track of inventory from raw materials to finished goods, create reorder points, and avoid stock-outs.
2. Master production planning
MRP systems identify bottlenecks in the production line caused by lack of material. The system automatically reroutes production or recommends production of a different product where materials are available. This means that manufacturers can plan their production lines, despite material availability constraints.
3. Resource management
Raw materials are essential in any manufacturing process. An MRP system offers information on raw materials’ availability and expected yield and helps manufacturers clearly understand what resources to engage in the process.
4. Data management
Analysing, understanding, and presenting data in visually appealing formats is necessary to improve the decision making processes. MRP systems handle this information, through processing and documenting purchasing, inventory, deliveries, and cash flow data into receipts, invoices, lists, reports, or documents.
5. Time-saving
The automation offered by MRP systems means that little human intervention is necessary to manage inventory, purchases, and production. The accuracy these systems provide outruns any error-prone human method. They also manage and store production data, which eliminates the need for specific human resources attributed to these functions.
Concluding thoughts
An MRP system helps to effectively manage inventory, schedule production, and purchase raw materials. It helps to avoid overstocking or stock-outs and ensure high quality standards through traceability. You cut costs, mitigate waste, and improve your overall processes.
What is MRP in manufacturing?
Material requirements planning or MRP is a computerized system that allows manufacturers to plan, manage, and control their inventories more efficiently. It, thus, helps them schedule the manufacturing per bills of materials and deliver the right product at the right time and the best possible price.
What is MRP software?
Material requirements planning or MRP is sales forecast-based software that helps manufacturers plan, manage, and control their inventory based on the demand forecasts.
How Does Material Requirement Planning Work?
Material requirements planning software forms an essential part of inventory management Inventory Management Inventory management in business refers to managing order processing , manufacturing, storage, and selling raw materials and finished goods. It ensures the right type of goods reach the right place in the right quantity at the right time and at the right price. Thus, it maintains the product availability at warehouses, retailers, and distributors. read more. As long as raw materials are available, these could help develop finished goods. If they are more than required, other producers in the same niche or industry can use them.
What system did Sharon use to prepare a bill of materials?
Her friend Lisa, who was more into using technology to solve business challenges, suggested using the material requirements planning system. Sharon did so and prepared a bill of materials to understand the type, quantity, and delivery time. The computerized system did all computations and let her know how to maintain the demand and supply chain.
What is MRP in manufacturing?
Material Requirement Planning (MRP) is a system used for planning, production & inventory control. It integrates data of production schedules with inventory and BOM to calculate purchasing and shipping schedules for the materials that are required to build the final product. The three basic steps of MRP are:-
How many outputs does MRP have?
After MRP receives the input, it generates the output. There are four main outputs. These include:
Why is MRP overflowing?
Additionally, MRP frameworks can be overflowing with blunder when organizations with offices in various nations don’t set up by individual locations. For instance, the MRP framework could show that there is a lot of raw material accessible for production when, actually, that crude material is on the opposite side of the world. Staff power is additionally not generally represented in MRP. In these cases, the MRP makes a limit issue.
What is insufficient raw materials available?
Insufficient raw materials available prevents planned production and client delivery due dates to be missed, making contracts to be canceled.
What is a material plan?
Material Plan:This details the raw materials, assemble items, and parts needed to make the finished product with amounts and dates.
How to keep production plan running?
Make sure that raw materials and segment parts are always close by for production, to keep the production plan running easily.
What is an auxiliary report?
Auxiliary reports are those that detail things, for example, performance control, exception data (e.g., errors or late orders), deviations, and predictors of future inventories and contracts.
Why is MRP important?
This is why Material Requirements Planning (MRP) was developed. It allows manufacturers to manage their orders and materials by having an efficient materials planning strategy that allows them to keep up with growing demands.
How does MRP work?
MRP systems work backward from production scheduling, in which it determines the amount of inventory needed to meet overall production demand. As inventory-associated costs are one of the highest incurred in manufacturing, MRP allows manufacturing operations to effectively manage their inventory levels and reduce costs.
What is MRP?
MRP (Material Requirements Planning) is an automated process that compares the demand for materials and finished goods to the on-hand and planned supply to generate jobs and/or purchase orders to satisfy unmet demands.
How does MRP save time?
Saves Times - Having an integrated production planning and scheduling system that can perform MRP will save time. MRP systems are automated which means that the system will generate production orders or purchase orders based on the inventory levels to supply demand. In addition, all team members have access to the latest data in real-time which eliminates time wasted updating each other on changes made to the production.
What is MRPII in manufacturing?
In more recent years, MRPII (Manufacturing Resource Planning) was developed as an extension of traditional MRP (now MRPI). MRPII goes a step further by ensuring that materials arrive on time based on the available capacity required for production.
What is the importance of planning for production?
One important aspect that comes with planning your production is ensuring that you have enough material to make the products. Without raw materials being transported through the supply chain adequately, you will encounter complications within your production, be unable to fulfill customer orders, or have potential inventory issues.
What is purchasing planning?
Purchasing Planning - This portion of the software pertains to what inventory is needed in order to meet demand. Any information pertaining to how much material is needed in order to meet product demand will help managers plan for any future facilities expansion. By planning your materials and inventory based on your actual demand, you will know exactly the amount of materials you need to store.
Why isn't material requirement considered in MRP?
Below are the some of the reason behind it: 1. Check the Planning file entry for Material. If not exist, maintain in MD20 by manually.
How to check MRP in MD20?
1. Check the Planning file entry for Material. If not exist, maintain in MD20 by manually. 2. Check Plant level Setting, MRP is activated or not in OMDU. 3. MRP type should not be ‘ND’. It should be ‘PD’.
Is material under reorder planning?
5. Material should not be under Reorder planning.Materials will be considered for planning only if stock falls below reorder point.

What Is Material Requirements Planning (MRP)?
How Material Requirements Planning (MRP) Works
- MRP is designed to answer three questions: 1. Whatis needed? 2. How muchis needed? 3. Whenis it needed? MRP works backward from a production plan for finished goods, which is converted into a list of requirements for the subassemblies, component parts, and raw materials needed to produce the final product within the established schedule. In other words, it's basically a system …
Steps in The MRP Process
- The MRP process can be broken down into four basic steps: 1. Estimating demand and the materials required to meet it.The initial step of the MRP process is determining customer demand and the requirements to meet it. Utilizing the bill of materials—which is simply a list of raw materials, assemblies, and components needed to manufacture an end product—MRP breaks do…
MRP in Manufacturing
- A critical input for material requirements planning is a bill of materials(BOM)—an extensive list of raw materials, components, and assemblies required to construct, manufacture or repair a product or service. BOM specifies the relationship between the end product (independent demand) and the components (dependent demand). Independent demand originates outside th…
Types of Data Considered by MRP
- The data that must be considered in an MRP scheme include: 1. Name of the final product that's being created: This is sometimes called independent demand or Level "0" on BOM. 2. What and when info: How much quantity is required to meet demand? When is it needed? 3. The shelf life of stored materials. 4. Inventory status records: Records of net materials available for use that are …
Advantages and Disadvantages of MRP
- There are several advantages to the MRP process: 1. Assurance that materials and components will be available when needed 2. Minimized inventory levels and costs associated 3. Optimized inventory management 4. Reduced customer lead times 5. Increased manufacturing efficiency 6. Increased labor productivity 7. Increased overall customer satisfaction Of course, there are also …
MRP Systems: Background
- Material requirements planning was the earliest of the integrated information technology (IT) systems that aimed to improve productivity for businesses by using computers and software technology. The first MRP systems of inventory management evolved in the 1940s and 1950s. They used mainframe computers to extrapolate information from a bill of materials for a specifi…
Common Problems
- As a business grows, fragmented processes often develop with it. For example, those involved in production/manufacturing planning may use an Excel spreadsheet to track orders through the various stages of manufacture, but this will not talk to sales, warehouse or shipping—each of which may have their own system. Companies have even been known to plan schedules using P…
How and Why MRP Should Work
- MRP or manufacturing resource planning takes ownership of the data from the quotation stage, through the sale, the raising of the works order, through all stages of production including the warehouse (goods in/out) and subcontracting, through to shipping and invoicing. By holding a single source of data all departments should have visibility of rel...
Why It Often Doesn’T Work
- If the IT or production manager is trying to implement a system that the CEO/CFO or other department heads do not agree with, then there is little or no hope of getting others on board, or indeed getting budget allocated to acquire a suitable system. Directors need to drive the system through the company and, rather than forcing it on an unwilling team of managers they should c…
Summary
- In short, businesses that will be successful are those that make the decision, stick with it and implement a MRP system in a swift but structured approach. A well implemented system does not have to cost a fortune and will be able to deliver quantifiable return on investment in a very short amount of time.