
Can I use plumbing flux on electronics? The strong acid in plumbing solder is very corrosive in order to strip the layer of oxidation off the surface of pipes as the solder melts, allowing it to adhere and form a waterproof joint. However, that corrosive acid flux will rapidly degrade wiring if plumbing solder is mistakenly used for electronics.
What is flux in plumbing?
What is Flux Used for in Plumbing?
- Water Soluble Flux. Water soluble flux is great for heaps of jobs. ...
- Petroleum-based Flux. Petroleum-based (also known as Petrolatum) Flux is a general-purpose flux that’s petroleum-based (as the name suggests!)
- ASTM B-813 Compliant Flux. This specific type of flux is both water-soluble and less corrosive. ...
- Speciality Flux. ...
Can soldering flux go bad?
When the soldering has been completed its a good idea to wipe the joined pipework down with an old damp cloth to remove the residue and boiled flux, By removing any old flux you can stop any discoloration or staining of the copper metal as the flux will degrade and go black or green with time.
What is the best solder for electrical work?
Top 12 Solder for Electronic Reviews
- Kester 32117 60/40 Wire Solder. The Kester Solder brand is one of the top-rated solder brands for wire solder. ...
- Maiyum 63/37 Tin-Lead Based Core Solder. This product is perfect for small soldering field-based jobs. ...
- WYCTIN 60/40 Tin-Lead Based Rosin Core. ...
- Icespring 63/37 Solder Wire. ...
- Alpha Metals 60/40 Tin-Lead Based Solder. ...
Do you need flux to solder copper?
Yes, flux is a vital proponent in joining pipe and fitting via the process of soldering. Flux is acidic in nature and not only acts to clean the copper pipe, but attracts the flame towards it, which brings the melted alloy with it, creating a water tight seal.
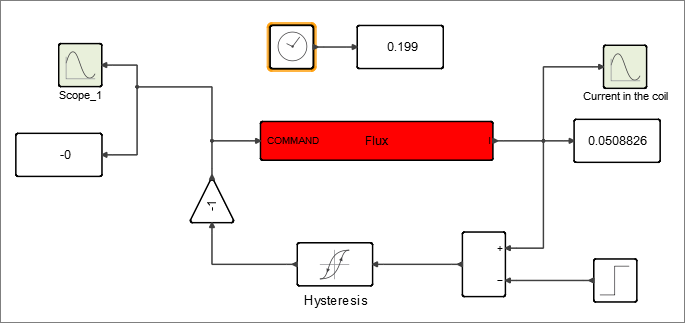
Can plumbers flux be used on electronics?
The strong acid in plumbing solder is very corrosive in order to strip the layer of oxidation off the surface of pipes as the solder melts, allowing it to adhere and form a waterproof joint. However, that corrosive acid flux will rapidly degrade wiring if plumbing solder is mistakenly used for electronics.
What kind of flux do you use for electronics?
Rosin fluxRosin flux is the oldest and still one of the most common fluxes used for electrical components. It is only active when heated, and generally safe for unheated electrical circuits. Rosin flux can be cleaned using an isopropyl alcohol solution. Organic acid flux is also commonly used for soldering electrical circuits.
Can you use oatey flux for electronics?
The Oately's fluxes are is recommend for use with the plumbing lead free solders but it works well with electronics solders too.
Is water soluble flux OK for electronics?
Water soluble flux Water Soluble fluxes are excellent for soldering, and provide the best soldering possible. They have a great amount of activity that readily cleans the metals to be soldered, and virtually never burn off during the soldering process.
Can I use Vaseline as flux?
3:234:12Vaseline Instead of Rosin Flux. Is it Possible? - YouTubeYouTubeStart of suggested clipEnd of suggested clipAs a soldering flux the answer is yes however the only trouble that uh exists with vaseline comparedMoreAs a soldering flux the answer is yes however the only trouble that uh exists with vaseline compared to uh conventional rosin flux is that it does not clean.
Is soldering fluid the same as flux?
What is Flux and What is the Difference Between Flux and Solder? While solder is used to assemble components onto your circuit board, the flux is used prior to assembly to prepare and help your board through the soldering process.
Do you use flux when soldering electronics?
Flux is a chemical cleaning agent used before and during the soldering process of electronic components onto circuit boards. Flux is used in both manual hand soldering as well as the different automated processes used by PCB contract manufacturers.
Do you need flux to solder electronics?
When soldering an electronic connector to a contact point (often called a “pad”), you generally need the following: A soldering iron capable of reaching the melting point of the solder. Wire solder, with or without a flux core. Flux, if the wire solder does not include a flux core or if additional flux is needed.
Can lead free tinning flux for electronics?
95 Tinning Flux is a petrolatum-based flux containing tinning powder to help pre-tin the pipe. It cleans, tins and fluxes most commonly soldered metals. 100% lead free, No. 95 Tinning Flux is NSF listed for potable water applications....Oatey® No. 95 Tinning Flux.Brand:OateyLead:NoProduct Type:Tinning FluxColor:Gray
What do you use water soluble flux for?
Water Soluble fluxes are excellent for soldering, and provide the best soldering possible. They have a great amount of activity that readily cleans the metals to be soldered, and virtually never burn off during the soldering process.
Why no-clean flux is used?
The primary reason to remove no-clean flux and its residue is to prevent malfunctions in circuits and to prevent interference with signal transmission. For instance, if too much no-clean flux builds up on a circuit board, or if white residue is left behind, it creates noise on the board.
What is water soluble flux made of?
glycol basesWater soluble flux, also called organic acid flux, is typically made from glycol bases. The downside to using water soluble flux is it often bonds with the circuit board itself or other metal surfaces, and as a result will require thorough cleaning.
What type of flux should I use?
Rosin activated flux cleans best, but will leave a significant amount of residue behind — because of this, rosin activated flux is rarely used. Water soluble flux, also called organic acid flux, is typically made from glycol bases.
Do you use flux when soldering electronics?
Flux is a chemical cleaning agent used before and during the soldering process of electronic components onto circuit boards. Flux is used in both manual hand soldering as well as the different automated processes used by PCB contract manufacturers.
Do I need flux to solder electronics?
When soldering an electronic connector to a contact point (often called a “pad”), you generally need the following: A soldering iron capable of reaching the melting point of the solder. Wire solder, with or without a flux core. Flux, if the wire solder does not include a flux core or if additional flux is needed.
What solder is best for electronics?
6 Best Solder for Electronics ReviewsKester Solder. First on our list is the Kester Solder, a 0.031 inches diameter steel-based solder with very high conductivity. ... Maiyum Solder Wire. ... SONEAK 60/40 Tin Lead Solder. ... Austor Solder Wire. ... Canfield Solder. ... Mandala Crafts Store Rosin Core Solder Wire.
What is soldering in electronics?
In electronics you are cleaning, and soldering in one step. The soldering is usually a surface bond of components. With plumbing the flux cleans the fittings, and gets the solder to flow into the cup of the fitting. -1.
Is flux corrosive?
Sort of all of the above. Electronic flux is non-corrosive, which is why it is used in electrical work. To say that the corrosion from plumbing flux adversely affects electrical components is a wild understatement. "Destroys" might be somewhat closer to the mark. But plumbing flux does a much better job of cleaning off oxidation -- which is the objective of the exercise, after all -- and at least in my experience is a good deal less sensitive to being overheated.
Just buy the good stuff!
With the in flux (get it?) of large international marketplaces it can be difficult to know for sure what you are buying. Translation errors, different brands in different regions, different regulations on what has to be printed on the label, the possibility of the sender to stock or ship the wrong thing, counterfeit products, etc.
But how do you know?
Sometimes they tell you straight up on the package: "Not applicable to PC boards", but you're not always that lucky. The user in the question that prompted me to ask here thought that his flux was corrosive because it had warning labels, but here is a quality U.S.
What is Plumbing Flux?
Flux is an acidic paste that is widely used in plumbing applications to link two joints that are soldered together. This is referred to as “sweating” the pipes. Flux, when combined with solder, is an important component of the sweating (or soldering) process.
What is Plumbing Flux Made From?
Flux is a chemical agent (trisodium phosphate) that is used to clean and combine metals. It comes in liquid and paste forms and is created from organic or inorganic ingredients. Which you use depends on the qualities you’re looking for in your project.
What is Flux Melting?
Flux is acidic in nature, and it not only cleans the copper pipe, but it also draws the flame to it. This brings the melted alloy with it and forms a watertight seal. It is critical to have a proper connection during soldering in order to avoid future leaks and water damage.
How to Apply Plumbing Flux
For plumbing purposes, you want to use an acid flux or lead-free tinning flux for soldering copper pipes as these are the two best options. Larger areas of oxidation can be removed with acid flux, resulting in much stronger soldering work.
Final Thoughts
That’s all there is to it. You’ve used the flux to clean and connect. You’re now ready to begin soldering. We have some great instructions on how to solder (or sweat) a copper pipe correctly. That article is below in our Related Resources.
Call 1-Tom-Plumber
Don’t hesitate to contact us here or call us at 1-Tom-Plumber (1-866-758-6237) if you need help soldering your plumbing pipes.
What is liquid flux used for?
Liquid fluxes are generally used for small, intricate parts. Paste fluxes are generally used for plumbing and piping and other situations that call for larger quantities of flux to be applied to a part before soldering. Paste fluxes are generally applied with a brush.
How does flux work in soldering?
Oxides and dirt are removed by the flux at elevated temperatures exposing a fresh, clean surface for the solder to bond with. Then the flux functions to protect this newly created surface from becoming re-contaminated. Finally, the flux controls the surface tension of the metal surface and the molten solder to draw the solder along. Without a flux performing these three critical tasks during a soldering operation, molten solder would simply drip off the surface of the material without any bonding. Try soldering with no flux and prove to yourself what a difference it makes.
What is flux solder?
The word flux literally means to flow or flowing, and describes one of the chief aims of a quality flux, to help the solder "flow" around the fitting as it is sweated to the pipe or tube. The flux is able to do this by governing three events that take place during the soldering process.
How to solder copper?
Here are some tips for making sure you are using flux effectively to make the best possible solder joints: 1 Select the proper flux for the application, the solder, and the surface metal. 2 Pre-clean surfaces as much as possible. Remove any burrs, heavy oxide films, or ink stamps by rubbing with an abrasive pad. Dirty copper is more difficult to solder and will give inconsistent results. 3 Apply small amounts of flux to both surfaces to be joined. Too much flux wastes material and can cause excessive spattering. Flux on only one surface can cause weak joints. 4 Gently and evenly heat both surfaces to be joined. Uneven or inadequate heating will cause poor solder flow. Overheating can also cause poor solder flow by decomposing the flux. Ideally the surfaces to be joined are heated to just above the activation temperature of the flux and the melt/flow point of the solder. 5 Work as quickly as possible without using excessive heat. Try to heat and solder the part in less than 15 seconds to avoid decomposing flux.
What is B-813 flux?
An ASTM B-813 compliant flux is designed to be less corrosive and water-soluble. ASTM B-813 is a standard that specifies the functionality of the flux and is meant specifically for copper plumbing. To maintain low corrosion potential, these fluxes have lower levels of active ingredients. This can potentially reduce the cleaning ability and solder flow of these fluxes. They are also prone to charring. Being water-soluble means that any residue is naturally rinsed away. This flux should be used if the ASTM B-813 standard is enforced in your area.
What is the best flux for soldering?
1) Water Soluble (non-ASTM B-813) Flux. A general-purpose type of flux that is good for many types of metals and solders. They can have a higher content of active ingredients, making them very good at metal cleaning and surface tension control for superior solder flow.
Can flux be applied to only one surface?
Apply small amounts of flux to both surfaces to be joined. Too much flux wastes material and can cause excessive spattering. Flux on only one surface can cause weak joints.
